Giáo trình Thi công đường ô tô (Phần 2)
CHƯƠNG 7: CÔNG TÁC KIỂM TRA VÀ NGHIỆN THU NỀN
ĐƯỜNG
7.1. MỤC ĐÍCH
Mục đích chung của công tác kiểm tra và nghiệm thu nền đường nhằm đảm bảo quá trình
thi công xây dựng nền đường đạt được chất lượng tốt, phù hợp với hồ sơ thiết kế cũng như các
yêu cầu của bản vẽ thi công. Công tác kiểm tra và nghiệm thu giúp phát hiện những sai sót về
mặt kỹ thuật, nhằm kịp thời đưa ra các yêu cầu và biện pháp để nâng cao chất lượng thi công
nền đường, có thể bao gồm cả biện pháp để nâng cao năng suất, hạ giá thành của công tác xây
dựng. Đồng thời, qua công tác kiểm tra và nghiệm thu sẽ giúp xác nhận khối lượng công tác đã
hoàn thành của đơn vị thi công để làm cơ sở thanh quyết toán khối lượng.
Bạn đang xem 20 trang mẫu của tài liệu "Giáo trình Thi công đường ô tô (Phần 2)", để tải tài liệu gốc về máy hãy click vào nút Download ở trên
Tóm tắt nội dung tài liệu: Giáo trình Thi công đường ô tô (Phần 2)
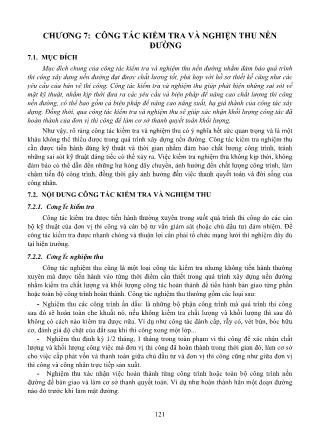
121 CHƯƠNG 7: CÔNG TÁC KIỂM TRA VÀ NGHIỆN THU NỀN ĐƯỜNG 7.1. MỤC ĐÍCH Mục đích chung của công tác kiểm tra và nghiệm thu nền đường nhằm đảm bảo quá trình thi công xây dựng nền đường đạt được chất lượng tốt, phù hợp với hồ sơ thiết kế cũng như các yêu cầu của bản vẽ thi công. Công tác kiểm tra và nghiệm thu giúp phát hiện những sai sót về mặt kỹ thuật, nhằm kịp thời đưa ra các yêu cầu và biện pháp để nâng cao chất lượng thi công nền đường, có thể bao gồm cả biện pháp để nâng cao năng suất, hạ giá thành của công tác xây dựng. Đồng thời, qua công tác kiểm tra và nghiệm thu sẽ giúp xác nhận khối lượng công tác đã hoàn thành của đơn vị thi công để làm cơ sở thanh quyết toán khối lượng. Như vậy, rõ ràng công tác kiểm tra và nghiệm thu có ý nghĩa hết sức quan trọng và là một khâu không thể thiếu được trong quá trình xây dựng nền đường. Công tác kiểm tra nghiệm thu cần được tiến hành đúng kỹ thuật và thời gian nhằm đảm bảo chất lượng công trình, tránh những sai sót kỹ thuật đáng tiếc có thể xảy ra. Việc kiểm tra nghiệm thu không kịp thời, không đảm bảo có thể dẫn đến những hư hỏng dây chuyền, ảnh hưởng đến chất lượng công trình, làm chậm tiến độ công trình, đồng thời gây ảnh hưởng đến việc thanh quyết toán và đời sống của công nhân. 7.2. NỘI DUNG CÔNG TÁC KIỂM TRA VÀ NGHIỆM THU 7.2.1. Công tác kiểm tra Công tác kiểm tra được tiến hành thường xuyên trong suốt quá trình thi công do các cán bộ kỹ thuật của đơn vị thi công và cán bộ tư vấn giám sát (hoặc chủ đầu tư) đảm nhiệm. Để công tác kiểm tra được nhanh chóng và thuận lợi cần phải tổ chức mạng lưới thí nghiệm đầy đủ tại hiện trường. 7.2.2. Công tác nghiệm thu Công tác nghiệm thu cũng là một loại công tác kiểm tra nhưng không tiến hành thường xuyên mà được tiến hành vào từng thời điểm cần thiết trong quá trình xây dựng nền đường nhằm kiểm tra chất lượng và khối lượng công tác hoàn thành để tiến hành bàn giao từng phần hoặc toàn bộ công trình hoàn thành. Công tác nghiệm thu thường gồm các loại sau: - Nghiệm thu các công trình ẩn dấu: là những bộ phận công trình mà quá trình thi công sau đó sẽ hoàn toàn che khuất nó, nếu không kiểm tra chất lượng và khối lượng thì sau đó không có cách nào kiểm tra được nữa. Ví dụ như công tác đánh cấp, rẫy cỏ, vét bùn, bóc hữu cơ, đánh giá độ chặt của đất sau khi thi công xong một lớp... - Nghiệm thu định kỳ 1/2 tháng, 1 tháng trong toàn phạm vi thi công để xác nhận chất lượng và khối lượng công việc mà đơn vị thi công đã hoàn thành trong thời gian đó, làm cơ sở cho việc cấp phát vốn và thanh toán giữa chủ đầu tư và đơn vị thi công cũng như giữa đơn vị thi công và công nhân trực tiếp sản xuất. - Nghiệm thu xác nhận việc hoàn thành từng công trình hoặc toàn bộ công trình nền đường để bàn giao và làm cơ sở thanh quyết toán. Ví dụ như hoàn thành hẳn một đoạn đường nào đó trước khi làm mặt đường. 122 7.3. THÀNH PHẦN NGHIỆM THU Để tiến hành công tác nghiệm thu nền đường thường thành lập đoàn nghiệm thu gồm: - Chủ đầu tư (hoặc tư vấn giám sát); - Phòng kỹ thuật thi công; - Phòng lao động tiền lương của công ty; - Đại diện các đơn vị trực tiếp thi công đoạn nền đường cần nghiệm thu. Tuỳ theo mục đích nghiệm thu, và giai đoạn nghiệm thu, mà thành phần nghiệm thu có thể thay đổi. Có thể mời thêm đại diện các đơn vị quản lý, khai thác tuyến đường sau này, cũng có thể chỉ tổ chức nghiệm thu trong nội bộ của đơn vị thi công mà không cần đại diện của chủ đầu tư. 7.4. CÔNG VIỆC CẦN NGHIỆM THU 7.4.1. Nghiệm thu vị trí tuyến và kích thước hình học của nền đường - Sau khi thi công xong nền đường, không được bố trí thêm đường cong, không được tạo độ dốc dọc và làm thay đổi độ dốc quá 5% độ dốc thiết kế; - Bề rộng nền cho phép sai số ±10cm; - Tim đường được phép lệch 10cm so với tim thiết kế; - Cao độ tim đường cho phép sai số ±10cm; - Độ dốc siêu cao nền đường không được vượt quá 5% độ dốc siêu cao thiết kế; - Độ dốc mái ta luy: Đoạn sai về độ dốc mái ta luy không được kéo dài liên tục quá 30m và tổng cộng chiều dài các đoạn sai không được chiếm quá 10% chiều dài đoạn thi công: Không được dốc quá 7% của độ dốc mái ta luy thiết kế khi chiều cao mái ta luy H ≤ 2m; Sai số không quá 4% khi chiều cao mái ta luy 2m ≤ H ≤6m; Sai số không quá 2% khi chiều cao mái ta luy H > 6m. 7.4.2. Nghiệm thu hệ thống rãnh thoát nước - Bề rộng đáy và mặt trên của rãnh không được nhỏ hơn kích thước thiết kế quá 5cm; - Độ dốc dọc của đáy rãnh không được sai số quá 5% độ dốc rãnh thiết kế; - Độ dốc ta luy rãnh biên như quy định với nền đường; - Độ dốc ta luy rãnh đỉnh, rãnh ngang thì không được sai quá 7% so với độ dốc ta luy thiết kế. 7.4.3. Nghiệm thu chất lượng đầm nén và độ bằng phẳng - Mỗi km đường phải kiểm tra chất lượng đầm nén ở ba mặt cắt, mỗi mặt cắt phải thí nghiệm ở ba vị trí và mẫu đất phải lấy sâu dưới mặt nền 15cm. Độ chặt đạt được không nhỏ hơn độ chặt quy định 2%. Phải kiểm tra thường xuyên độ chặt trong quá trình đắp; - Mặt nền phải nhẵn, cho phép nứt nẻ nhỏ nhưng không liên tục, không bị bóc từng mảng. Độ bằng phẳng đo bằng thước 3m khe hở không được quá 3cm. 7.4.4. Nghiệm thu việc khôi phục cọc lại sau khi thi công xong nền đường - Phải có đủ cọc đỉnh, cọc đường cong (20m phải có một cọc) và cọc đường thẳng (50m 123 phải có một cọc). 7.4.5. Một số lưu ý khi kiểm tra và nghiệm thu nền đường - Khi tiến hành công tác kiểm tra và nghiệm thu, đơn vị thi công cần phải chuẩn bị sẵn và trình bày các tài liệu sau: Bản vẽ thi công trong đó có vẽ lại và ghi chú đầy đủ các chỗ thay đổi đã được duyệt so với đồ án thiết kế; Nhật ký thi công của đơn vị (có ghi cả những ý kiến chỉ đạo thi công của cán bộ cấp trên); Biên bản nghiệm thu các công trình ẩn dấu từ trước; Biên bản thí nghiệm thử đất và đầm nén từ trước; Các sổ sách ghi các mốc cao độ và các tài liệu có liên quan đến công tác đo đạc để kiểm tra; - Sau khi tiến hành kiểm tra và nghiệm thu, cần phải lập biên bản có chữ ký của tất cả các đại diện tham gia công việc nghiệm thu trong đó nêu rõ các văn bản dùng làm cơ sở cho việc kiểm tra và các kết luận về chất lượng cũng như khối lượng thi công. 124 PHẦN 2: XÂY DỰNG MẶT ĐƯỜNG CHƯƠNG 8: CÁC VẤN ĐỀ CHUNG TRONG XÂY DỰNG MẶT ĐƯỜNG 8.1. MỘT SỐ ĐỊNH NGHĨA VÀ THUẬT NGỮ 8.1.1. Khái niệm Mặt đường là một kết cấu gồm một hoặc nhiều tầng, lớp vật liệu khác nhau được rải trên nền đường nhằm đảm bảo các yêu cầu chạy xe về cường độ, độ bằng phẳng và độ nhám. Cấu tạo hoàn chỉnh áo đường gồm có tầng mặt và tầng móng, mỗi tầng lại có thể gồm nhiều lớp vật liệu khác nhau. Hình 8.1 – Kết cấu mặt đường Mặt đường là một bộ phận rất quan trọng của đường. Nó cũng là bộ phân đắt tiền nhất. Mặt đường tốt hay xấu sẽ ảnh hưởng trực tiếp tới chất lượng chạy xe: an toàn, êm thuận, kinh tế. Do vậy ngoài việc tính toán thiết kế nhằm tìm ra một kết cấu mặt đường có đủ bề dày, đủ cường độ thì công nghệ thi công và chất lượng thi công nhằm tạo ra các tầng lớp vật liệu như trong tính toán là vấn đề hết sức quan trọng. 8.1.2. Yêu cầu đối với mặt đường Mặt đường chịu tác dụng trực tiếp của tải trọng xe chạy, của các nhân tố tự nhiên như mưa, nắng, sự thay đổi nhiệt độ... Nên để bảo đảm đạt được các chỉ tiêu khai thác – vận doanh có hiệu quả nhất thì việc thiết kế và xây dựng kết cấu mặt đường phải đạt được các yêu cầu sau: - Đủ cường độ: kết cấu mặt đường phải có đủ cường độ chung và tại mỗi điểm riêng trong từng tầng, lớp vật liệu. Nó biểu thị bằng khả năng chống lại biến dạng thẳng đứng, biến dạng trượt, biến dạng co dãn khi chịu kéo – uốn hoặc do nhiệt độ; - Ổn định với cường độ: cường độ phải ít thay đổi theo điều kiện thời tiết, khí hậu; - Độ bằng phẳng: mặt đường phải đạt được độ bằng phẳng nhất định để giảm sức cản lăn, 125 giảm sốc khi xe chạy. Do đó nâng cao được chất lượng chạy xe, tốc độ xe chạy, giảm tiêu hao nhiên liệu, kéo dài tuổi thọ của xe... Yêu cầu này được đảm bảo bằng việc chọn vật liệu thích hợp, biện pháp và chất lượng thi công; - Đủ độ nhám: mặt đường phải có đủ độ nhám để nâng cao hệ số bám giữa bánh xe và mặt đường, tạo điều kiện tốt cho xe chạy an toàn với tốc độ cao và trong những trường hợp cần thiết có thể dừng xe nhanh chóng. Yêu cầu này chủ yếu phụ thuộc vào việc chọn vật liệu làm lớp trên mặt đường và hoàn toàn không mâu thuẫn gì với yêu cầu về độ bằng phẳng; - Ít bụi: bụi là do xe cộ phá hoại, bào mòn vật liệu làm mặt đường. Bụi gây ô nhiễm môi trường, giảm tầm nhìn 8.2. CẤU TẠO KẾT CẤU ÁO ĐƯỜNG 8.2.1. Tầng mặt Tầng mặt chịu tác dụng trực tiếp của tải trọng bánh xe (gồm lực thẳng đứng và lực ngang) và các nhân tố thiên nhiên (như mưa, nắng, nhiệt độ...). Yêu cầu tầng mặt phải đủ bền trong suốt thời kỳ sử dụng của kết cấu áo đường, phải bằng phẳng, có đủ độ nhám, chống thấm nước, chống được biến dạng dẻo ở nhiệt độ cao, chống được nứt, chống được bong bật, phải có khả năng chịu bào mòn tốt và không sinh bụi. Vật liệu để làm các lớp của kết cấu mặt đường gồm có cốt liệu và các chất liên kết. Áo đường mềm: Để đạt được yêu cầu trên, tầng mặt áo đường mềm thường cấu tạo gồm có 3 lớp: - Lớp 3: lớp chịu lực chủ yếu - Lớp 2: lớp hao mòn - Lớp 1: lớp bảo vệ Hình 8.2 – Cấu tạo áo đường mềm Lớp chịu lực chủ yếu có thể được cấu tạo từ một hoặc nhiều lớp vật liệu. Do tính chất chịu lực (chịu nén, chịu uốn và chịu cắt) nên lớp chịu lực chủ yếu phải cấu tạo từ vật liệu có cường độ cao, có khả năng chống trượt nhất định. Thông thường là hỗn hợp đá – nhựa (bê tông nhựa (BTN), đá trộn nhựa,...), đá dăm gia cố xi măng, cấp phối đá dăm hay đá dăm nước được chêm chèn và lu lèn chặt. 126 Lớp bảo vệ và lớp hao mòn được bố trí trên lớp chịu lực chủ yếu cũng có tác dụng làm giảm tác động của lực ngang, tăng cường sức chống bào mòn cho tầng mặt. Nhưng tác dụng chủ yếu là để giảm bớt tác động của lực xung kích, chống lại sự mài mòn trực tiếp của bánh xe và thiên nhiên (ví dụ như: lớp láng nhựa có tác dụng chống nước thấm vào lớp chịu lực chủ yếu, giữ cho lớp này ổn định cường độ...). Ngoài ra, chúng còn tăng cường độ bằng phẳng, tăng độ nhám cho mặt đường. Lớp hao mòn thường là một lớp mỏng dày từ 1 – 3cm, ở ngay trên lớp mặt chủ yếu và thường làm bằng vật liệu có tính dính: lớp láng nhựa, BTN chặt, hạt mịn hay BTN cát... Lớp bảo vệ cũng là một lớp mỏng 0.5 – 1cm, để bảo vệ cho lớp dưới khi chưa hình thành cường độ (lớp cát trong mặt đường đá dăm nước... ). Đối với mặt đường BTN và có xử lý nhựa thì không có lớp này. Lớp hao mòn, lớp bảo vệ là các lớp định kì phải khôi phục trong quá trình khai thác. Lớp liên kết: giữa lớp mặt và lớp móng có thể có hoặc không có lớp liên kết. Áo đường cứng: Hình 8.3 – Cấu tạo áo đường cứng Tầng mặt áo đường cứng gồm lớp chịu lực chủ yếu là tấm bê tông xi măng (BTXM). Cũng có thể có thêm lớp hao mòn bằng BTN hạt nhỏ (BTN mịn, BTN cát). Lớp BTN này còn có tác dụng rất lớn là giảm sốc cho mặt đường do các khe nối gây ra. Tấm BTXM phải có cường độ chịu uốn cao, đủ cường độ dự trữ để chống lại hiện tường mỏi, hiện tượng phá hoại cục bộ ở góc tấm do tác dụng của tải trọng trùng phục, lực xung kích. Khi cho xe chạy trực tiếp trên tấm BTXM, nó còn phải có khả năng chịu được mài mòn. 8.2.2. Tầng móng Áo đường mềm: Khác với tầng mặt, tầng móng chỉ chịu tác dụng của lực thẳng đứng. Nhiệm vụ của nó là phải phân bố làm giảm nhỏ ứng suất thẳng đứng truyền xuống nền đường tới một giá trị để đất nền có thể chịu đựng được mà không tạo nên biến dạng quá lớn. Do lực thẳng đứng truyền xuống ngày càng bé đi nên để tiết kiệm, tầng móng có cấu tạo gồm nhiều lớp vật liệu có cường độ giảm dần từ trên xuống. Thông thường có 2 lớp: lớp móng trên và lớp móng dưới. Do không chịu tác dụng bào mòn trực tiếp, tác dụng lực ngang mà chỉ chịu lực thẳng đứng nên vật liệu làm tầng móng không yêu cầu cao như tầng mặt và có thể dùng các vật liệu rời rạc, chịu bào mòn kém nhưng chủ yếu lại đòi hỏi có độ cứng nhất định, ít biến dạng. Tầng móng thường làm bằng các loại vật liệu như: cấp phối đá dăm loại 1, cấp phối đá gia cố xi măng, đá dăm láng nhựa, đá dăm tiêu chuẩn... (lớp móng trên) và cấp phối đá dăm loại 2, đất, cát gia cố 127 xi măng, đất gia cố nhựa, cấp phối sỏi suối, cấp phối sỏi ong, cấp phối sỏi đồi... (lớp móng dưới). Không phải bao giờ một kết cấu mặt đường mềm cũng bao gồm đầy đủ các tầng, lớp như trên mà tuỳ theo yêu cầu xe chạy, tuỳ theo điều kiện cụ thể nó có thể chỉ gồm một số tầng lớp nào đó. Ví dụ: như với đường cấp thấp, áo đường chỉ có thể chỉ gồm tầng mặt. Khi này tầng mặt kiêm luôn chức năng của tầng móng. Với đường cấp cao thì kết cấu áo đường thường có nhiều tầng lớp như trên. Hiểu rõ chức năng của mỗi tầng lớp trong kết cấu áo đường mới có thể chọn được cấu tạo, chọn vật liệu sử dụng trong mỗi tầng lớp được hợp lý và mới đề xuất đúng đắn các yêu cầu thi công cụ thể đối với mỗi tầng lớp đó. Áo đường cứng: Khác với kết cấu áo đường mềm, trong mặt đường cứng thì bản thân tấm BTXM chịu lực là chủ yếu, mặt khác áp lực do tải trọng bánh xe truyền xuống lớp móng rất nhỏ vì diện phân bố áp lực dưới tấm BTXM rất rộng. Do vậy tầng móng cũng như nền đất tham gia chịu lực không đáng kể nên cấu tạo tầng móng mặt đường cứng sẽ ít lớp vật liệu hơn. Tầng móng của mặt đường cứng tuy không tham gia chịu lực lớn như trong mặt đường mềm nhưng nó có tác dụng quan trọng đối với sự bền vững lâu dài của tấm BTXM ở trên. Nếu tầng móng không bằng phẳng hoặc đầm nén không tốt, không đều, không đủ cường độ sẽ xảy ra tích luỹ biến dạng dư, lún không đều. Lúc này tấm BTXM sẽ bị cập kênh, điều kiện làm việc bình thường của tấm không còn nên tấm BTXM sẽ bị phá hoại. Chính vì thế yêu cầu quan trọng nhất của lớp móng mặt đường cứng là phải đảm bảo điều kiện tiếp xúc tốt nhất giữa tấm bê tông và lớp móng trong suốt quá trình chịu tải. Đáp ứng yêu cầu này, lớp móng mặt đường cứng thường là lớp móng cát, cát gia cố xi măng, cấp phối đá gia cố xi măng,... có nghĩa là vật liệu có độ cứng lớn, rất ít biến dạng dư và dễ tạo phẳng. 8.2.3. Lớp đáy móng (lớp trên nền đường) Lớp đáy móng là lớp chuyển tiếp giữa nền đất và tầng móng của mặt đường, có các chức năng sau: - Tạo một lòng đường chịu lực đồng nhất (đồng đều theo bề rộng), có sức chịu tải tốt; - Ngăn chặn ẩm thấm từ trên xuống nền đất và từ dưới lên tầng móng áo đường; - Tạo “hiệu ứng đe” để bảo đảm chất lượng đầm nén các lớp móng phía trên; - Tạo điều kiện cho xe máy đi lại trong quá trình thi công áo đường không gây hư hại nền đất phía dưới (nhất là khi thời tiết xấu). Trường hợp nền đất làm bằng vật liệu có cường độ cao, ổn định với nước tốt thì không cần làm lớp này. 8.3. CÁC NGUYÊN LÝ SỬ DỤNG VẬT LIỆU LÀM MẶT ĐƯỜNG Mỗi phương pháp xây dựng mặt đường phải dựa trên một nguyên lý sử dụng vật liệu nhất định và trình tự thi công nhất định. Mỗi nguyên lý sử dụng vật liệu khác nhau sẽ quyết định yêu cầu đối với mỗi thành phần vật liệu về số lượng và chất lượng, đồng thời cũng quyết định các biện pháp và kỹ thu ... ợt quá quy định trong Bảng 13.8. Nếu trạm trộn sử dụng hệ thống điều khiển tự động thì phải sử dụng hệ thống tự động cấp liệu, đồng thời dựa vào thành phần mẻ trộn in ra hằng ngày để thống kê số liệu tỷ lệ phối trộn và sai số tương ứng với mỗi lý trình đã rải trên thực tế. Bảng 13.8: Sai số cho phép khi trộn vật liệu so với thiết kế, % Loại và cấp hạng đường làm mặt đường BTXM Xi măng Phụ gia khoáng Cát Cốt liệu thô Nước Phụ gia Đường cao tốc cấp I, cấp II, cấp III 1 1 2 2 1 1 Các loại đường khác 2 2 3 2 2 2 Cần phải dựa vào độ dính kết, độ đồng đều và độ ổn định của hỗn hợp bê tông trộn thử để xác định thời gian trộn tối ưu. Thông thường với thiết bị trộn một trục thẳng đứng thì tổng thời gian trộn trong khoảng 80-120 giây, trong đó thời gian trút vật liệu vào máy không nên ít hơn 40 giây và thời gian thực trộn không được ngắn hơn 40 giây. Nếu bê tông có dùng phụ gia khoáng thì thời gian thực trộn nên dài hơn bê tông thông thường từ 10 - 15 giây. Phải kiểm tra và khống chế chất lượng hỗn hợp bê tông thi qui định tại bảng Nội dung kiểm tra Tần suất kiểm tra Mặt đường BTXM đường cao tốc, cấp I, cấp II, cấp III Mặt đường BTXM các đường cấp hạng khác Tỷ lệ Nước/Xi măng và độ ổn định Mỗi 5000m3 kiểm tra 1 lần hoặc khi có thay đổi Mỗi 5000m3 kiểm tra 1 lần hoặc khi có thay đổi Độ sụt và độ đồng nhất Mỗi ca làm việc đo 3 lần hoặc khi có thay đổi Mỗi ca làm việc đo 3 lần hoặc khi có thay đổi Tổn thất độ sụt Kiểm tra trước khi thi công, khi nhiệt độ cao hoặc khi có thay đổi Kiểm tra trước khi thi công, khi nhiệt độ cao hoặc khi có thay đổi Độ tách nước Kiểm tra khi cần thiết Kiểm tra khi cần thiết Khối lượng thể tích Mỗi ca làm việc đo 1 lần Mỗi ca làm việc đo 1 lần Nhiệt độ, thời gian đông kết cuối cùng, nhiệt lượng thuỷ hoá Kiểm tra 1-2 lần trong mỗi ca làm việc khi thi công vào mùa đông và mùa hè; khi nhiệt độ lúc Kiểm tra 1 lần trong mỗi ca làm việc khi thi công vào mùa đông và mùa hè; khi nhiệt độ lúc cao nhất, 233 cao nhất, thấp nhất thấp nhất Phân tầng Quan sát thường xuyên Quan sát thường xuyên Hình 13.5: Trạm trộn bê tông thẳng đứng 13.2.5.3. Vận chuyển bê tông Bê tông từ các trạm trộn thường được vận chuyển đến nơi thi công bằng ô tô tự đổ hoặc ô tô chuyên dụng. Số lượng xe vận chuyển tương ứng với hệ thống rải máy được xác định theo công thức sau: 𝑁 = 2𝑛 (1 + 𝑆 𝛾𝑐𝑚 𝑉𝑞𝐺𝑞 ) Trong đó N – số lượng xe vận chuyển (xe); n – số trạm trộn có cùng công suất; S – khoảng cách vận chuyển một chiều (Km); c – khối lượng thể tích của bê tôn (T/m3); m – công suất trộn của một trạm trong một giờ (m3/h); Vq – vận tốc chuyển trung bình của xe (km/h); Gq – tải trọng của xe (T/xe) 234 Hình 13.6: Xe vận chuyển bê tông 13.2.5.4. Yêu cầu kỹ thuật vận chuyển Phải căn cứ vào tiến độ thi công, khối lượng vận chuyển, khoảng cách vận chuyển và tình trạng của tuyến đường vận chuyển để lựa chọn loại xe và số lượng xe đảm bảo bê tông được vận chuyển đến công trường theo đúng thời gian qui định. Hỗn hợp bê tông khi vận chuyển đến công trường phải có các đặc tính phù hợp với yêu cầu thi công. Thời gian dài nhất cho phép từ khi bê tông ra khỏi buồng trộn đến khi rải xong đối với mỗi loại công nghệ phải thoả mãn qui định trongBảng 13.9. Khi không thoả mãn phải thông qua thí nghiệm để tăng phụ gia làm chậm đông kết. Bảng 13.9: Thời gian dài nhất cho phép từ khi bê tông ra khỏi buồng trộn đến khi rải xong Nhiệt độ khi thi công, oC Thời gian vận chuyển dài nhất cho phép, h Thời gian dài nhất cho phép đến khi rải xong, h Công nghệ ván khuôn trượt, ván khuôn ray hoặc các công nghệ liên hợp khác Rải bằng công nghệ đơn giản Công nghệ ván khuôn trượt, ván khuôn ray hoặc các công nghệ liên hợp khác Rải bằng công nghệ đơn giản 5-9 2,0 1,5 2,5 2,0 10-19 1,5 1,0 2,0 1,5 20-29 1,0 0,75 1,5 1,25 30-35 0,75 0,5 1,25 1,0 Ghi chú: Nhiệt độ khi thi công là nhiệt độ không khí trung bình trong thời gian thi công, khi sử dụng phụ gia làm chậm đông kết thì giá trị trong Bảng có thể tăng thêm 0,25-0,5h. Ngoài ra việc vận chuyển cần tuân thủ các yêu cầu sau: Thùng xe phải sạch. Độ cao trút bê tông từ máy trộn vào thùng xe không được lớn hơn 2m để tránh hiện tượng phân tầng cốt liệu. 235 Không để rơi vãi vật liệu trên đường trong quá trình vận chuyển. Xe vận chuyển phải có bộ phận giảm xóc để tránh hỗn hợp phân tầng. Nếu vận chuyển bằng ô tô tự đổ thì phải có tấm che cho hỗn hợp bê tông và bán kính vận chuyển không được quá 20km. Không được để xe vận chuyển va vào ván khuôn hoặc các cọc tiêu đánh dấu cơ tuyến thi công. Nếu va vào thì phải báo cáo để tiến hành sửa chữa kịp thời. Khi xe quay đầu hoặc xả bê tông phải có người chỉ huy. 13.2.6. Rải và đầm nén hỗn hợp BTXM Nên dùng các loại máy rải chuyên dụng để thi công, nếu không có máy rải chuyên dụng có thể rải và đầm nén bẳng thủ công. Chiều dày rải BTXM: h1=K.h với hệ số rải K=1.15 - 1.3 (hệ số này xác định chính xác theo kết quả rải thử nghiệm) Một số loại máy rải chuyên dụng còn có khả năng tự động hoá toàn bộ công việc từ bước rải vật liệu, đầm lèn hỗn hợp, tự động bố trí cốt thép truyền lực khi bê tông chưa đông cứng và hoàn thiện bề mặt. Hình 13.7: Rải mặt đường bằng máy rải ván khuôn trượt Hình 13.8: Rải mặt đường bằng máy rải trốn lăn và 3 trục lăn 236 Hình 13.9: Rải mặt đường bằng thủ công Sau khi rải hỗn hợp thì tiến hành san bằng và đầm nén hỗn hợp. Công tác đầm nén được thực hiện tự động bằng máy rải chuyên dụng hoặc có thể đầm nén bán thủ công bằng một số loại đầm như sau: + Đầm dùi: ở một vị trí đầm khoảng 45s, sau đó chuyển sang vị trí khác. + Đầm bàn: một vị trí đầm khoảng 45-60s, chồng lên nhau 10cm. + Đầm ngựa (đầm thanh): đầm sau cùng để tạo phẳng hoàn thiện sơ bộ bề mặt, tốc độ khoảng 0,5-1,0m/phút. Hình 13.10: Đầm dùi 237 Hình 13.11: Đầm bàn Hình 13.12: Đầm ngựa bán thủ công 13.2.7. Hoàn thiện bề mặt Mục đích của công tác hoàn thiện bề mặt là làm cho bề mặt bằng phẳng và nhám. Việc làm bằng phẳng có thể tiến hành bằng máy hoặc thủ công. Khi hoàn thiện bằng thủ công thì dùng bàn xoa để xoa bằng cho đến khi bề mặt không đọng nước thì thôi. Sau khi làm phẳng bề mặt thì dủng bàn chải chất dẻo hoặc bàn chải sắt quét ngang mặt đường tạo thành các rãnh ngang nhỏ. Cũng có thể tạo nhám bằng rãnh dọc tại các đoạn đường vòng hoặc có yêu cầu giảm tiếng ồn. chiều sâu tạo rãnh bằng 2-4mm, rộng 3-5mm, khoảng cách giữa các rãnh khoảng 15-25mm. 238 Hình 13.13: Hoàn thiện bề mặt bằng thủ công Hình 13.14: Hoàn thiện bề mặt bằng máy Hình 13.15: Tạo nhám bằng thủ công 239 Hình 13.16: Tạo nhám bằng máy chuyên dụng 13.2.8. Làm khe Các loại khe nối gồm: + Khe dọc + Khe co ngang + Khe dãn + Khe thi công Công tác thi công khe nối bao gồm việc bố trí thanh truyền lực, thanh chịu kéo (thanh thép chống trôi) và xẻ khe chèn matic. Việc đặt thanh truyền lực và thanh chống trôi trong các khe ngang thường dùng máy chấn động để ấn các thanh thép truyền lực đó vào trong bê tông sau khi đã đầm và hoàn thiện sơ bộ. Thép chống trôi trong khe thi công dọc thì có thể bẻ gập 900 một đầu, sau khi bê tông động cứng và tháo ván khuôn thì uốn thẳng lại phần bẻ gập đó. Các thanh thép truyền lực của khe dãn thì đặt trên giá đỡ bằng thép và xuyên qua tấm gỗ đệm đã cố định trên lớp móng. Giá đỡ phải chịu được tác dụng của đầm chấn động không làm nghiêng lệch các thanh truyền lực. Có thể đổ trước tại vị trí khe dãn một ít bê tông và dùng đầm dùi đầm xung quanh vị trí khe dãn, sau khi đảm bảo vị trí chính xác của thanh truyền lực thì mới cho máy rải đi qua. Việc làm khe đổ matic có thể dùng phương pháp xẻ khe trong bê tông mới cứng và phương pháp nén (xẻ khe trong bê tông ướt). Phương pháp xẻ khe không chấn động lại bê tông và có thể tạp thành các khe rất bằng phẳng, nhưng phải xác định đúng thời gian xẻ khe. Nếu xẻ quá sớm cường độ bê tông chưa đủ thì mép khe có thể bị sức mẻ hoặc sụt, còn xẻ khe quá muộn thì ứng suất co ngót có thể tạo thành các đường nứt ngang trong bê tông. Thời gian thích hợp tuỳ theo điều kiện khí hậu từng địa phương, thường là sau công tác hoàn thiện 8- 18 giờ. 240 Hình 13.17: Máy rải rải tự động có bộ phận cắm thanh truyền lực Hình 13.18: Xẻ khe trong bê tông mới cứng Hình 13.19: Đổ matic chèn khe 13.2.9. Bảo dưỡng bê tông Bảo dưỡng bê tông là một khâu quan trọng để đảm bảo chất lượng của mặt đường bêtông xi măng. Trong quá trình bêtông xi măng đông cứng cần bảo đảm các vấn đề sau: Không cho xe cộ và người đi lại làm hư hỏng mặt đường. Không cho bê tông co rút đột ngột dưới tác dụng của nắng và gió. Không cho mưa xói hỏng bê tông. Không cho nước trong hỗn hợp bê tông bóc hơi làm thiếu mất lượng nước cần thiết để tạo thành đá xi măng. 241 Công tác bảo dưỡng phải bắt đầu ngay sau khi rải BTXM hoặc tạo nhám xong. Một số biện pháp bảo dưỡng bêtông: Tưới nước hàng ngày, có thể tưới bằng thủ công hoặc dùng xe phun. Phủ cát hoặc rải màng giữ ẩm, vải địa kỹ thuật, bao tải để giữ ẩm và tưới nước. Làm nhà, lều di động. Hiện nay, người ta còn dùng một phương pháp khác để bảo dưỡng là phun một lớp màng mỏng vật liệu không thấm nước lên bề mặt tấm bê tông để giữ ẩm. (Lớp này có thể là nhũ tương, nhựa lỏng hoặc sơn rẻ tiền). Thời gian bảo dưỡng phải được xác định tuỳ theo thời gian cường độ kéo khi uốn của hỗn hợp BTXM vừa rải đạt được tối thiểu 80% theo thiết kế. Cần đặc biệt chú trọng việc bảo dưỡng trong 7 ngày đầu. Hình 13.20: Bảo dưỡng bê tông bằng tấm phủ Hình 13.21: Phun màng vật liệu không thấm để bảo dưỡng bê tông 13.2.10. Kiểm tra, nghiệm thu Việc kiểm tra chất lượng thi công cần thực hiện trong suốt quá trình từ giai đoạn chuẩn bị thi công, giai đoạn thi công cho đến khi hoàn thành mặt đường BTXM. Kiểm tra vật liệu trong giai đoạn chuẩn bị thi công Kiểm tra máy móc, thiết bị và dụng cụ thi công 242 Kiểm tra nền móng trước khi thi công mặt đường BTXM Kiểm tra trong quá trình thi công + Phải thường xuyên giám sát, kiểm tra chất lượng vật liệu trong khi trộn, rải, đầm nèn + Kiểm tra kích thước hình học: bề rộng, chiều dầy tấm, độ lệch tim, cao độ, độ dốc + Kiểm tra độ bằng phẳng + Kiểm tra chất lượng khe nối. + Kiểm tra cường độ bê tông: khoan lấy mẫu đem về thí nghiệm + Kiểm tra thành phần cấp phối, hàm lượng xi măng: lấy mẫu đem về phân tích. 13.3. XÂY DỰNG MẶT ĐƯỜNG BÊ TÔNG CỐT THÉP LẮP GHÉP Thường dùng các tấm bê tông kích thước nhỏ để xây dựng mặt đường trên các đường thứ cấp, quảng trường, chỗ đỗ xe, trong các sân hoặc trên các đoạn đường mà nền đường có khả năng lún không đều. Về cấu tạo các tấm bê tông xi măng thường có hình dạng lục giác, vuông hoặc chữ nhật Thường dùng bê tông mác 300-400 để đúc các tấm bê tông kích thước nhỏ. Các tấm bê tông này thường được lát trên lớp móng cát, sỏi, đá dăm hoặc xỉ lò cao. Trên lớp móng sỏi, đá dăm, xỉ lò phải có một lớp cát đệm dày 2-5cm. Các tấm bê tông kích thước nhỏ thường được lát bằng tay kết hợp với công cụ cải tiến. Các tấm kích thước lớn thì đặt bằng ô tô cần trục. Để tăng cường độ và độ ổn định của mặt đường, phải chèn hoặc xây mạch nối giữa các tấm. thường dùng vữa xi măng, mattic nhựa đường, hỗn hợp xi măng cát khô để xây dựng hoặc chèn mạch. Trình tự thi công: Chuẩn bị lớp móng: kiểm tra độ bằng phẳng, độ chặt, độ dốc, kích thước hình học của lớp móng. Lên khuôn mặt đường: căn cứ vào kích thước hình học mặt cắt ngang để đóng các cọc định vị khuôn cho mặt đường. Sau đó dùng dây căng nối các cọc dọc theo mép đường và thẳng góc với tim đường để kiểm tra việc lát mặt trong quá trình thi công. Chế tạo các tấm bê tông và vận chuyển các tấm bê tông đến vị trí thi công. Làm lớp đệm: khi lát trên lớp móng bằng bê tông hoặc đá dăm thì phải bố trí một lớp đệm. Thường dùng máy san tự hành để san lớp đệm cát hoặc cát trộn xi măng và hoàn thiện thêm bằng thủ công. Lát mặt đường: việc lát mặt chủ yếu làm bằng tay, nếu lát mặt bằng loại gạch bê tông tự chèn có thể dùng máy lát chuyên dụng. Khi lát trên đoạn đường dốc, phải lát từ thấp lên cao và chèn chặt các tấm vào vị trí trước khi đầm lèn mặt đường. Đầm lèn mặt đường: có thể dùng đầm rơi tự do để đầm lèn mặt đường lát. Nếu lớp móng là bê tông hoặc đá dăm có thể dùng đầm hơi ép hoặc đầm cơ giới. Kiểm tra bề mặt: kiểm tra độ bằng phẳng trước khi rải vật liệu chèn 243 Rải vật liệu chèn hoặc xây mạch nối: vật liệu chèn phải được rải đều và phủ kín toàn bộ các khe chèn + Nếu dùng vữa xi măng – cát để gắn mạch thì phải tưới nước trên mặt đường sau đó mới rải vữa trên mặt đường còn ướt. Dùng chổi cứng hoặc bàn trang để rải đều vữa trên mặt đường rồi dùng bàn là để là bằng vữa ở vị trí các mạch. Phải dùng đầm tay đầm nhẹ mặt đường cho vữa thấm đều và sâu xuống các mạch. Sau khi gắn mạch xong phải phủ lên mặt một lớp bao tải hoặc cát ẩm và tưới nước bảo dưỡng. + Nếu dùng hỗn hợp xi măng cát khô để chèn mạch thì rải đều hỗn hợp này lên mặt đường, dùng chổi quét vào các mạch rồi đầm nhẹ cho xuống đều các mạch. Kiểm tra, hoàn thiện và nghiệm thu. (a) (b) Hình 13.22: Thi công lớp đệm cát bằng máy rải bê tông nhựa (a) Thi công lớp đệm; (b) Lớp đệm đã được san phẳng Hình 13.23: Thi công lát mặt bằng máy lát 244 (a) (b) Hình 13.24: Công tác đầm nén mặt đường (a): đầm bằng đầm chấn động; (b): đầm bằng lu bánh lốp (a) (b) Hình 13.25: Rải vật liệu chèn và đầm nén hoàn thiện (a): Rải vật liệu chèn; (b): đầm hoàn thiện bằng đầm chấn động Hình 13.26: Kiểm tra độ bằng phẳng mặt đường 245 Hình 13.27: Mặt đường bê tông tự chèn đã hoàn thiện 246 TÀI LIỆU THAM KHẢO [1]. Nguyễn Quang Chiêu, Lã Văn Chăm, Xây dựng nền đường ôtô, Hà Nội, NXB Giao Thông vận Tải, 2001. [2]. Nguyễn Quang Chiêu, Phạm Duy Khang, Xây dựng mặt đường ôtô, Hà Nội, NXB Giao Thông vận Tải, 2007. [3]. Nguyễn Quang Chiêu, Dương Học Hải, Tổ Chức thi công đường ôtô, Hà Nội, NXB Giao Thông vận Tải, 2007. [4]. Quyết định số 1951/QĐ-BGTVT ngày 17/08/2012 Ban hành quy định tạm thời về kỹ thuật thi công và nghiệm thu mặt đường bê tông xi măng trong xây dựng công trình giao thông. [5]. TCVN 8857:2011- Lớp kết cấu áo đường ô tô bằng cấp phối thiên nhiên –Vật liệu, thi công và nghiệm thu. [6]. TCVN 5559: 2011 – Lớp móng cấp phối đá dăm trong kết cấu áo đường ô tô Vật liệu, thi công và nghiệm thu. [7]. TCVN 8809 :2011- Mặt đường đá dăm thấm nhập nhựa nóng – Thi công và nghiệm thu. [8]. TCVN 8863:2011 – Mặt đường láng nhựa nóng – Thi công và nghiệm thu. [9]. TCVN 8819: 2011: Mặt đường bê tông nhựa nóng – Yêu cầu thi công và nghiệm thu. [10]. TCCS 06-2013/TCĐBVN- Sữa chữa kết cấu áo đường bằng hỗn hợp đá dăm đen rải nóng – Thi công và nghiệm thu. [11]. 22TCN 81-84 – Quy trình sưu dụng đất gia cố bằng chất kết dính vô cơ. [12]. 22TCN 246-98 –Quy trình thi công và nghiệm thu lớp cát gia cố xi măng trong kết cấu áo đường ô tô.
File đính kèm:
giao_trinh_thi_cong_duong_o_to_phan_2.pdf