Vật liệu ma sát luyện kim bột trong chế tạo máy
1. Đặt vấn đề
Ở ngoài nước, vật liệu ma sát luyện kim bột được sử dụng để chế tạo các chi tiết phanh
và các cụm truyền động của xe ô tô, máy nông nghiệp, máy mỏ, máy xây dựng, máy bay, máy
công cụ, máy dập, máy ép trong sản xuất cơ khí. Việc sử dụng các loại vật liệu ma sát để làm
việc có bôi trơn cưỡng bức trong các cụm thiết bị như: đĩa ly hợp, máy điều tốc, khớp nối có
môment tới hạn, hệ truyền dẫn thuỷ lực hoặc ở điều kiện làm việc không có bôi trơn (ma sát
khô) như: khớp nối, phanh hãm, khớp nối điện từ thay thế cho vật liệu thép và gang đúc hoặc
các vật liệu ma sát gắn kết với nền bằng gang hoặc thép truyền thống trước đây cho phép tăng
độ bền và độ tin cậy khi làm việc, cũng như tăng hiệu quả sử dụng của các cụm ma sát trong
máy móc thiết bị. Vật liệu ma sát luyện kim bột đồng thời tạo điều kiện tốt để thiết kế, chế tạo
các cụm ma sát có kết cấu mới với hệ số ma sát cao, khả năng làm việc ổn định, chịu mài mòn
và bền nhiệt cao của cả hai chi tiết cặp đôi [1÷4].
Tóm tắt nội dung tài liệu: Vật liệu ma sát luyện kim bột trong chế tạo máy
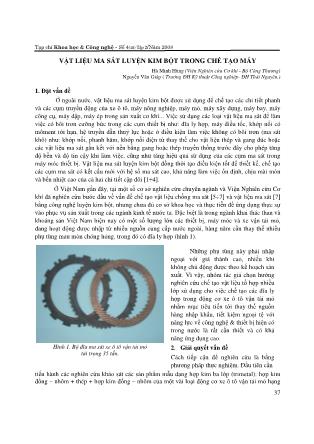
T¹p chÝ Khoa häc & C«ng nghÖ - Sè 4(48) Tập 2/N¨m 2008 37 VẬT LIỆU MA SÁT LUYỆN KIM BỘT TRONG CHẾ TẠO MÁY Hà Minh Hùng (Viện Nghiên cứu Cơ khí - Bộ Công Thương) Nguyễn Văn Giáp ( Trường ĐH Kỹ thuật Công nghiệp- ĐH Thái Nguyên.) 1. Đặt vấn đề Ở ngoài nước, vật liệu ma sát luyện kim bột được sử dụng để chế tạo các chi tiết phanh và các cụm truyền động của xe ô tô, máy nông nghiệp, máy mỏ, máy xây dựng, máy bay, máy công cụ, máy dập, máy ép trong sản xuất cơ khí... Việc sử dụng các loại vật liệu ma sát để làm việc có bôi trơn cưỡng bức trong các cụm thiết bị như: đĩa ly hợp, máy điều tốc, khớp nối có môment tới hạn, hệ truyền dẫn thuỷ lực hoặc ở điều kiện làm việc không có bôi trơn (ma sát khô) như: khớp nối, phanh hãm, khớp nối điện từ thay thế cho vật liệu thép và gang đúc hoặc các vật liệu ma sát gắn kết với nền bằng gang hoặc thép truyền thống trước đây cho phép tăng độ bền và độ tin cậy khi làm việc, cũng như tăng hiệu quả sử dụng của các cụm ma sát trong máy móc thiết bị. Vật liệu ma sát luyện kim bột đồng thời tạo điều kiện tốt để thiết kế, chế tạo các cụm ma sát có kết cấu mới với hệ số ma sát cao, khả năng làm việc ổn định, chịu mài mòn và bền nhiệt cao của cả hai chi tiết cặp đôi [1÷4]. Ở Việt Nam gần đây, tại một số cơ sở nghiên cứu chuyên ngành và Viện Nghiên cứu Cơ khí đã nghiên cứu bước đầu về vấn đề chế tạo vật liệu chống ma sát [5÷7] và vật liệu ma sát [7] bằng công nghệ luyện kim bột, nhưng chưa đủ cơ sở khoa học và thực tiễn để ứng dụng thực sự vào phục vụ sản xuất trong các ngành kinh tế nước ta. Đặc biệt là trong ngành khai thác than và khoáng sản Việt Nam hiện nay có một số lượng lớn các thiết bị, máy móc và xe vận tải mỏ, đang hoạt động được nhập từ nhiều nguồn cung cấp nước ngoài, hàng năm cần thay thế nhiều phụ tùng mau mòn chóng hỏng, trong đó có đĩa ly hợp (hình 1). Những phụ tùng này phải nhập ngoại với giá thành cao, nhiều khi không chủ động được theo kế hoạch sản xuất. Vì vậy, nhóm tác giả chọn hướng nghiên cứu chế tạo vật liệu tổ hợp nhiều lớp sử dụng cho việc chế tạo các đĩa ly hợp trong động cơ xe ô tô vận tải mỏ nhằm mục tiêu tiến tới thay thế nguồn hàng nhập khNu, tiết kiệm ngoại tệ với năng lực về công nghệ & thiết bị hiện có trong nước là rất cần thiết và có khả năng ứng dụng cao. 2. Giải quyết vấn đề Cách tiếp cận để nghiên cứu là bằng phương pháp thực nghiệm. Đầu tiên cần Hình 1. Bộ đĩa ma sát xe ô tô vận tải mỏ tải trọng 35 tấn. tiến hành các nghiên cứu khảo sát các sản phNm mẫu dạng hợp kim ba lớp (trimetal): hợp kim đồng – nhôm + thép + hợp kim đồng – nhôm của một vài loại động cơ xe ô tô vận tải mỏ hạng Héi th¶o Khoa häc toµn quèc C«ng nghÖ vËt liÖu vµ bÒ mÆt - Th¸i Nguyªn 2008 38 nặng đang làm việc tại Quảng Ninh, trong đó có xe ô tô vận tải mỏ của Nga sản xuất để lập bộ tiêu chí giám định chất lượng sản phNm. Bước tiếp theo là thực nghiệm ép + thiêu kết vật liệu ma sát hệ hợp kim đồng – nhôm hoặc hợp kim đồng – thiếc – nhôm có thành phần hoá học tương tự mẫu của Nga để tối ưu hoá các công nghệ tạo phôi vật liệu tổ hợp nhiều lớp thông qua việc giám định theo các chỉ tiêu chất lượng tương ứng với sản phNm nhập ngoại. Trong quá trình tiến hành nghiên cứu, chúng tôi gắn kết với việc hướng dẫn các học viên cao học và nghiên cứu sinh tham gia thực nghiệm khoa học. Tiếp đến là sản xuất thử loạt nhỏ một vài loại đĩa ly hợp xe ô tô vận tải mỏ bằng công nghệ ép nóng, thí nghiệm mòn nhanh trong quy mô phòng thí nghiệm và lắp ráp thử nghiệm trên hiện trường nhằm đánh giá khả năng làm việc của vật liệu [5÷7]. 3. Nội dung báo cáo Ngày nay, trong các máy móc thiết bị được lắp các bộ phận ma sát nhằm mục đích khác nhau: chuyển động, dừng và khởi động lại, thay đổi chế độ sử dụng và điều khiển chúng không thể thiếu các bộ phanh ma sát hoặc các bộ phận chuyển số mà khả năng làm việc của những cơ cấu đó phụ thuộc vào các đặc tính kỹ thuật của chúng. Vật liệu ma sát có hệ số ma sát cao (quy ước lớn hơn 0,2 ÷ 0,25 khi ở điều kiện ma sát khô của cặp ma sát gang – thép và lớn hơn 0,5 khi có bôi trơn). Công suất ngày càng lớn, tốc độ và tải trọng của các máy móc thiết bị hiện đại tạo ra điều kiện làm việc hết sức nặng của vật liệu ma sát. Ví dụ, tốc độ phanh có thể đạt 50 m/s ở áp lực đến 2,5 MPa khi làm việc không bôi trơn và 100 m/s ở áp lực 2,0 MPa khi có bôi trơn. Liên quan tới các điều kiện cứng khi làm việc của các bộ phanh hãm máy móc thiết bị hiện đại vật liệu ma sát cần có các tính chất sau: 1) Có độ bền ma sát nhiệt cao, tức là bảo đảm giá trị ổn định của hệ số ma sát và độ mòn thấp trong một khoảng nhiệt độ rộng; 2) Đủ độ bền vững chống mài mòn. Mức độ chống mài mòn yêu cầu được xác định phụ thuộc vào điều kiện sử dụng và nằm trong khoảng 0,01÷ 0,02 µm đến 0,1÷ 0,15 µm tính cho một chu kỳ làm việc; 3) Có đủ độ bền chống gỉ và khả năng không hoá gỉ với chi tiét cùng bộ đôi ma sát; 4) Các phần tử của cặp ma sát cần phải không bắt chặt (hàn dính) vào nhau cả trong quá trình và sau khi phanh hãm. Đối với vật liệu ma sát của cặp đôi ma sát điều quan trọng đáng kể là sử dụng được toàn bộ bề mặt ma sát, tức là nhận được bề mặt tiếp xúc có thể tối đa. Khi đó, diện tích ma sát thấy được cần phải không nhỏ hơn 80% giá trị trung bình, còn các bề mặt ma sát cần phải trơn phẳng, không có các vết rắn lạ ấn dính vào chúng; 5) Vật liệu ma sát còn không hµm chứa các cấu tử quý hiếm và đắt tiền, nó cần phải được gia công dễ dàng trên các máy công cụ hiện có, công nghệ chế tạo phải dễ tiếp cận và dễ thực hiện về mặt kỹ thuật trong sản xuất hàng loạt lớn; 6) Các tính chất cơ lý của vật liệu ma sát là: có độ bền cơ học cao ở nhiệt độ làm việc. Trong quá trình sử dụng không bị tách lớp hoặc biến hình tạo ra các khe nứt sâu và các hạt bị mài mòn tách ra từ nó bám dính vào bề mặt ma sát phát hủy chế độ làm việc bình thường của các cụm phanh hãm; 7) Từ những vật liệu ma sát đã được biết đến nay thì vật liệu ma sát luyện kim bột đáp ứng khá đầy đủ những yêu cầu kể trên, nó được chế tạo từ nguyên liệu đầu vào là kim loại và phi kim loại. Các cấu tử kim loại làm cho vật liệu có độ bền cao, còn các chất phi kim loại – làm tăng hệ số ma sát và giàm xu hướng bị ăn mòn vào vật liệu (bị bào mòn do ma sát khi phanh T¹p chÝ Khoa häc & C«ng nghÖ - Sè 4(48) Tập 2/N¨m 2008 39 hãm). Nhờ có các đặc tính đó mà vật liệu ma sát luyện kim bột có thể làm việc ở tải trọng và tốc độ phanh trượt cao và đặc trưng bởi độ bền mòn cao hơn so với các vật liệu ma sát khác. Sự dụng vật liệu ma sát luyện kim bột trong các bộ phanh hãm đảm bảo sự khởi động trơn đều, hệ số ma sát ổn định và tuổi thọ nâng cao. Hiện nay 75% các chi tiết ma sát được sản xuất làm việc trong môi trường có dầu bôi trơn. Sự có mặt của dầu bôi trơn cho phép sử dụng tốc độ và áp lực cao, đảm bảo hệ số ma sát ổn định hơn và tạo điều kiện thuận lợi cho việc làm mát bề mặt làm việc của chi tiết, điều đó lại góp phần nâng cao độ tin cậy làm việc và thời hạn sử dụng của bộ ma sát phanh. Các chi tiết ma sát chính làm việc ở điều kiện thủy tĩnh được chế tạo từ các hợp kim bột trên nền đồng. Trong số vật liệu đó được dùng phổ biến hơn cả là vật liệu có mác MK-5 với thành phần hóa học sau: 4% Fe; 9 % Sn; 8 % Pb; 7 % grafit; 72 % Cu. Ở các nước công nghiệp trên thế giới, trong đó có Liên Xô trước đây, người ta đã chế tạo và sử dụng ma sát kiểu như vật liệu MK-5. Độ bền chống mài mòn và độ bền chống gỉ cao, không bị bóc tách các hạt làm bNn dầu bôi trơn – đó là những ưu điểm cơ bản của các loại vật liệu này. Tuy nhiên, bên cạnh các ưu điểm đó, vật liệu ma sát luyện kim bột trên nền đồng còn có các hạt chế sau: hệ số ma sát tương đối thấp (0,04 ÷ 0,6); sử dụng các vật liệu đắt tiền (đồng, thiếc), không phù hợp với các bộ phận làm việc ở điều kiện ma sát biên và ma sát khô. Hệ số ma sát có thể được nâng cao bằng các cho thêm các hạt mài, nhưng sự có mặt của chúng trong vật liệu ma sát luyện kim bột dẫn đến hiện tượng bong tách trong quá trình làm việc và làm bNn dầu bôi trơn, dẫn đến làm giảm độ bền chống mài mòn của vật liệu ma sát. Vật liệu ma sát được chế tạo tại nhiều nước trên thế giới có sự khác biệt về thành phần các chất ma sát phụ gia và chủng loại của chúng (bảng 1). Bảng 1 Thành phần hóa học của vật liệu ma sát làm việc trong dầu bôi trơn [4]. TT Đồng, Cu Thiếc, Sn Chì, Pb Các bon, C Dioxit silíc SiO2 Sắt, Fe Phụ gia ma sát 1 73 9 4 4 - 8 Bêtônit -2, Asbet – 2, 2 72 9 7 5 - 4 Asbet – 3 3 73,5 9 8 4 - 4 Mullít – 1,5 4 Nền 5 ÷ 9 5 v 15 0,5 ÷ 10 0,5 ÷ 10 - Talk – 1 ÷ 16, Asbet 0,5 - 8 5 68 8 7 6 4 7 6 Nền 4 ÷ 8 - 25 - 5 ÷ 15 Các bít, Asbet – 5 7 72 7 6 8 3 3 Ôxit môlípđen 8 69 5,5 9 2,5 4,5 7 Ôxit môlípđen 9 60 ÷ 70 5,8 0 ÷ 10 4 ÷ 7 3 ÷ 4 7 Asbet – 3; 4 10 62 ÷ 72 6 ÷ 10 2 ÷ 6 5 ÷ 9 - 4,5 ÷ 8 Silíc 4 ÷ 6 Từ bảng 1 cho thấy: để làm việc trong dầu bôi trơn người ta sử dụng nhiều loại vật liệu ma sát luyện kim bột, trong đó đồng được coi như kim loại kết dính, được hợp kim hóa bởi thiếc là chủ yếu. Do thiếc là kim loại quý hiếm và đắt tiền nên đã có nhiều nghiên cứu nhằm giảm hàm lượng thiếc và tiến tới không sử dụng thiếc trong loại vật liệu này. Tại Viện Luyện kim bột thuộc Việc Hàn lâm Ucraina, đã chế thử và qua sản xuất thử nghiệm công nghiệp vật liệu ma sát luyện kim bột được thay thế bằng nhôm. Theo các tính chất sử dụng vật liệu này tốt hơn các vật liệu hiện có trước đó và được cho trong bảng 2. Tuy nhiên, nếu thay thế thiếc bởi các kim loại thành phần khác (nhôm) dẫn đến giảm giá thành chế tạo và nâng cao tính chất ma sát ở mức độ nhất định thì nhược điểm không khắc phục được của vật liệu mới là tính bền nhiệt kém. Héi th¶o Khoa häc toµn quèc C«ng nghÖ vËt liÖu vµ bÒ mÆt - Th¸i Nguyªn 2008 40 Bảng 2 Tính chất vật liệu ma sát có chứa nhôm so với vật liệu ma sát MK-5 [4]. Al, % Khối lượng Độ cứng, HB, MPa Độ bền uốn, σUB, MPa Độ bền cắt, τC, MPa Độ xốp Θ, % Hệ số ma sát f ở ν=20 m/s P=3 MPa Lượng mòn tuyến tính trung bình cho một chu kỳ, µm Chất lượng gia công cắt gọt 8 700 ÷ 750 280 160 3 ÷ 4 0,075 12 ÷15 Tốt 9 780 v 820 300 170 3 ÷ 4 0,081 10 ÷ 12 Tốt 10 940 ÷ 980 320 190 3 ÷ 4 0,089 6 ÷ 8 Tốt 11 1040 ÷ 1120 320 195 4 ÷ 5 0,093 6 ÷ 8 Xấu 12 1120 ÷ 1210 295 180 4 ÷ 5 0,100 30 ÷ 40 Không gia công 13 1330 ÷ 1410 230 160 4 ÷ 6 - - MK-5 450 ÷ 500 100 ÷ 120 50 - 70 4 ÷ 5 0,07÷0,08 10 ÷ 15 Tốt Nhược điểm lớn của vật liệu ma sát trên nền đồng là nhiệt độ trên bề mặt ma sát tối đa cho không cao (300 OC). Khi làm việc, ở bộ ly hợp mômen tối đa cho quá trình trượt ma sát lâu dài của cặp ma sát nên xảy ra sự tăng nhiệt độ làm việc một cách đáng kể, khi đó dầu bôi trơn một phần, và đôi khi tất cả dầu, bị bốc cháy, tức là hầu như vật liệu làm việc không có bôi trơn. Các điều kiện làm việc tương tự như vậy đối với ma sát tổ hợp trên nền đồng sẽ dẫn đến sự hư hỏng toàn bộ cụm ma sát, vì thế một trong những hướng tạo vật liệu mới ma sát là tìm kiếm các hợp kim có tính chất cơ-lý cao hơn, đảm bảo khả năng làm việc bình thường của bộ ma sát ở các yêu cầu nâng cao tính năng sử dụng trong các máy móc thiết bị hiện đại. Để làm việc được trong điều kiện tải trọng nặng khi sử dụng (không có bôi trơn), người ta sử dụng vật liệu ma sát luyện kim bột trên nền đồng. Độ bền và nhiệt độ nóng chảy của sắt cao hơn đồng đảm bảo khả năng làm việc của vật liệu trong điều kiện ma sát không có bôi trơn, khi đó nhiệt độ trên bề mặt ma sát tăng đến 900 ÷ 1.000 OC, đó là điều quan trọng khi chọn vật liệu làm việc ở điều kiện ma sát khô. Hiện nay có số lượng lớn các mác vật liệu ma sát đã biết thuộc loại này theo tiêu chuNn của Nga, nhưng trong đó số vật liệu ma sát được sử dụng nhiều nhất thuộc 4 nhóm sau [4]: a) Vật liệu mác ФMK-11 với thành phần hóa học gồm: 64% Fe; 15% Cu; 9% Grafit; 6% Ba2O4; 3% SiO2 và 3% Asbet, có độ bền cao hơn khoảng 2 lần so với vật liệu ma sát nền brônza. Ưu điểm chính của vật liệu ФMK-11 là nó có thể làm việc ở nhiệt độ cao và trong khoảng làm việc rộng của tải trọng và tốc độ phanh hãm, với độ mài mòn tương đối nhỏ khi ma sát với cặp chi tiết thép tôi hoặc gang; b) Vật liệu ФMK- 8 với thành phần hóa học: 45 % Fe; 25 % Ni; 10 % Cr; 6 % W; 7 % Grafit và 7 % Cu2S, nhờ sự có mặt của các nguyên tố hợp kim hóa trong thành phần của nó mà có độ bề chống mài mòn cao ở nhiệt độ làm việc ma sát đến 500 ÷ 6000C; c) Vật liệu MKB - 50A với thành phần hóa học: 64 Fe;10% Cu; 8% Grafit;5 % FeSO4; 5% B4C; 5% SiC và 3% Asbet có đặc tính sử dụng cao trong điều kiện phanh hãm tải trọng nặng; d) Vật liệu CMK- 80 với thành phần hóa học: 46,5% Fe; 25% Cu; 10% B4C; 3,5% SiC; 6,5% Mn và 2,5% BN, có hệ số ma sát và trị số lượng mòn ổn định trong trong phạm vi rộng của áp suất và tốc độ làm việc. Vật liệu này được các nhà nghiên cứu tại Viện Luyện kim bột thuộc Viện Hàn lâm Khoa học Ucraina, được sử dụng trong các cụm phanh hãm máy móc thiết bị làm việc trong điều kiện tải trọng nặng. T¹p chÝ Khoa häc & C«ng nghÖ - Sè 4(48) Tập 2/N¨m 2008 41 Tổng hợp tính chất các loại vật liệu ma sát nói trên trong trong bảng 3. Trong sản xuất công nghiệp, người ta còn sử dụng các thành phần khác của vật liệu bột trên nền sắt có chứa một số hạt mài tự nhiên. Tính chất của những vật liệu loại này phụ thuộc vào hàm lượng (theo tỉ lệ phần trăm) các thành phần có trong nguyên liệu đầu vào, ví dụ như: vật liệu với thành phần hoá học 73,8% Cu; 10% Fe; 9,7% SiO2; 3% B4C và 3,5% Grafit, có hệ số ma sát f = 0,17 và độ mòn 0,025 mm (tính cho 1 chu kỳ làm việc). Trong khi đó, vật liệu với thành phần hoá học: 75% Cu; 10% Fe; 12% SiO2; 3% B4C với những điều kiện thử tương tự có hệ số ma sát f = 0,16, còn độ mòn – cao hơn khoảng 1,5 lần. Tóm lại, ngay cả khi sự thay đổi nhỏ tỷ lệ phần trăm các nguyên tố, và hơn nữa khi thay thế một vài nguyên tố bởi các nguyên tố khác trong thành phần hóa học vật liệu, đều có dẫn đến sự thay đổi đáng kể các tính chất cơ bản của vật liệu ma sát luyện kim bột. Công nghệ chế tạo các chi tiết ma sát từ vật liệu ma sát luyện kim bột bao gồm các công đoạn: chuNn bị nền để gắn vật liệu ma sát, chuNn bị các chi tiết từ vật liệu ma sát luyện kim bột, gắn kết chúng với nhau và gia công cơ khí đến kích thước yêu cầu. Bảng 3. Tính chất vật liệu ma sát nền sắt [4]. Tính chất theo mác vật liệu ФMK- 8 ФMK- 11 MKB-50A CMK-80 Mật độ, ρ, g/cm3 6,0 6,0 5,0 5,7 Độ bền, σb , MPa 90 ÷ 100 57 34 - Giới hạn bền kéo, τC MPa 70 ÷ 90 80 ÷ 100 67 ÷ 85 65 ÷ 80 Độ bền nén, σCB, MPa 450 ÷ 500 300 ÷ 350 150 ÷ 210 200 ÷ 250 Độ cứng Brinen, HB, MPa 600 ÷ 900 800 ÷ 1.000 800 ÷ 1.000 800 ÷ 1.000 Hẹ số dẫn nhiệt, W/(m.K) 37,3 46,1 ÷ 19,3 27,2 ÷ 18,8 29,3 ÷ 20,9 Hệ số ma sát, f 0,21 ÷ 0,22 0,23 ÷ 0,29 0,28 ÷ 0,37 0,39 ÷ 0,40 Độ ổn định hệ số ma sát 0,50 ÷ 0,55 0,7 ÷ 0,9 0,7 ÷ 0,9 0,85 ÷ 0,87 Độ mòn tối đa của mẫu trong một lần phanh hãm, µm 5 ÷ 8 22 10 ÷ 13 7 ÷ 10 Đặc điểm đặc trưng của các chi tiết ma sát luyện kim bột là sự có mặt của nền thép mà sự cần thiết phải sử dụng nó được giải thích như sau: Vì vật liệu ma sát luyện kim bột có độ bền cơ học không cao (giới hạn chảy khi kéo vật liệu trên nền sắt thường chỉ bằng 80 ÷ 100 MPa, còn trên nền đồng là 20 ÷ 40 MPa), nên để tăng độ bền chi tiết ma sát người ta phải hàn nó vào các đĩa hoặc tấm bằng thép. Hỗn hợp bột được cho vào trong buồng trộn và trộn trong thời gian 2 ÷ 6 giờ. Để cải thiện các điều kiện trộn người ta cho thêm vào hỗn hợp bột nguyên liệu xăng hoặc dầu thực vật với hàm lượng đến 1% tính theo khối lượng phối liệu. Một trong những nguyên công chủ yếu của quá trình công nghệ là ép tạo hình chi tiết, sử dụng máy ép thuỷ lực và ép với áp lực khoảng 200 ÷ 400 MPa để đảm bảo độ xốp vật ép là 15 ÷ 20%. Việc gắn kết các lớp thép nền với lớp vật liệu ma sát xNy ra bằng tích hợp quá trình thiêu kết với dính kết dưới áp lực. Khi làm dính kết các lớp bột phối liệu trên nền thép thì độ bền liên kết phụ thuộc vào trạng thái bề mặt tấm đế thép. Mỗi một vết ôxit nhỏ cũng dẫn đến liên kết không đủ bền vững có thể xNy ra khi thiêu kết do có thoát khí và chất Nm có chứa trong các lỗ xốp của vật liệu ma sát luyện kim bột. Như vậy, cần phải có những biện pháp ngăn ngừa bề mặt lớp thép nền khỏi bị Héi th¶o Khoa häc toµn quèc C«ng nghÖ vËt liÖu vµ bÒ mÆt - Th¸i Nguyªn 2008 42 ôxy hoá không chỉ trong điều kiện bình thường, mà còn ở nhiệt độ cao khi thiêu kết. Lớp bảo vệ như vậy trên lớp nền thép có thể là một lớp niken hoặc đồng có chiều dày 10 ÷ 20 µm. Trước khi ép thiêu kết các bề mặt thép nền và vật liệu ma sát được tNy sạch dầu mỡ bằng rượu và sấy khô trong không khí. Sau khi ép bột vật liệu ma sát lên lớp nền thép, phôi được đưa vào thiêu kết. Để tránh các phôi ép này khỏi dính bám vào nhau, giữa chúng đặt các vách ngăn làm bằng thép chịu nhiệt hoặc vật liệu phân cách chống dính kết (lớp giấy bọc grafit hoặc ôxit nhôm đã được rây qua lưới sàng). Khi chế tạo các đĩa ma sát người ta sử dụng hai phương án sau: 1) vật liệu ma sát ở bột nguyên liệu được dàn phẳng trên nền đĩa thép sau khi thiêu kết xong thì gia công cơ khí bề mặt đến yêu cầu cần thiết; 2) dạng prophin với lớp vật liệu ma sát đó có hình dạng đúng như chi tiết cần chế tạo kể cả về kích thước, cũng như các rãnh chứa trên vật liệu ma sát, và như vậy sau khi thiêu kết sẽ không cần phải gia công cơ khí tiếp theo. Tuy nhiên, với định hướng có triển vọng sử dụng công nghệ tạo prophin từ vật liệu ma sát, nhưng công nghệ này khá phức tạp, nặng nhọc và cần nhiều đồ gá chuyên dụng. Số lượng các tổ hợp đĩa ma sát có thể xếp chồng lên nhau khi thiêu kết phụ thuộc vào chiều dày của các vách ngăn công nghệ giữa chúng, đĩa nền thép, kích thước và hình dạng buồng nung của lò thiêu kết. Khi xếp lớp các đĩa ma sát cần chú ý đến việc không để chúng bị xô lệch với nhau và so với các lớp vách ngăn công nghệ. Đối với vật liệu ma sát trên nền đồng việc thiêu kết các đĩa ép được thực hiện trong lò điện kiểu bàn cờ ở nhiệt độ 700 ÷ 800OC và dưới áp lực 0,7 ÷ 1,0 MPa, đối với vật liệu trên nền sắt thì thiêu kết ở nhiệt độ 900 ÷ 1.040OC và dưới áp lực 1,2 ÷ 2,0 MPa. Thời gian giữ nhiệt khi thiêu kết đối với cả hai loại vật liệu ma sát trên nền đồng và thép đều bằng 2,5 ÷ 5 giờ. Sau khi thiêu kết với các vách ngăn phẳng công nghệ, các đĩa ma sát được gia công cơ khí (cắt các rãnh và mài bề mặt ma sát). Việc cắt rãnh trên bề mặt lớp vật liệu ma sát là bắt buộc đối với điều kiện làm việc có dầu bôi trơn. Các rãnh dầu này là để chứa các hạt mài tách ra khỏi vật liệu ma sát trong quá trình làm việc và giữ ổn định hệ số ma sát tối đa mài bề mặt làm việc của đĩa ma sát nhằm mục đích tạo độ song song các bề mặt tiếp xúc khi làm việc, khuyên dùng đá mài có độ hạt 46 và tốc độ vòng 1 m/s, lượng ăn đá mài là 0,03 ÷ 0,05 mm. Lĩnh vực sử dụng chủ yếu của chi tiết từ vật liệu ma sát luyện kim bột có thể được phân loại như: 1) Cơ cấu truyền động làm việc không bôi trơn: tải trọng nhỏ (máy kéo, máy công cụ, máy tính...), tải trọng trung bình (máy chuốt, máy dập, máy vận chuyển công nghiệp), phanh hãm không có dầu bôi trơn ở tải trọng nặng (máy bay); 2) Các liên kết làm việc có bôi trơn: tải trọng trung bình (hệ truyền động lực máy tự động, máy công cụ, bộ phận điều khiển máy kéo) và tải trọng nặng (hệ truyền động lực và máy kéo). Có thể nêu một vài ví dụ về ứng dụng vật liệu ma sát luyện kim bột trong các khớp ly hợp và phanh hãm của các máy móc thiết bị như: trong các hệ truyền động lực của ô tô MAZ và các nhà máy ô tô khác: đĩa ma sát được chế tạo có nền thép và lớp ghép bằng vật liệu ma sát luyện kim bột trên nền đồng, áp lực tối đa trong các cụm ma sát đạt đến 10 MPa và tốc độ tối đa 60 m/s. Sự làm việc đảm bảo tuyệt đối tốt của hệ truyễn dẫn động chủ yếu là nhờ sử dụng các chi tiết ma sát luyện kim bột. Các loại má phanh bánh của ô tô có thời gian sử dụng tăng lên đến 10 lần khi sử dụng vật liệu ma sát luyện kim bột. Các loại vật liệu ma sát mới từ bột kim loại đã T¹p chÝ Khoa häc & C«ng nghÖ - Sè 4(48) Tập 2/N¨m 2008 43 được áp dụng tại nhà máy chế tạo máy kéo Minsk (Belarusia) trong các cụm phanh trên máy kéo MTZ -100 và khớp ly hợp bảo vệ trên máy kéo MTZ-82. Tuổi thọ sử dụng của các cụm phanh và ly hợp này tăng lên rất nhiều so với vật liệu ma sát truyền thống, đạt đến 8.000 ÷ 10.000 giờ. 5.Kết luận 1) Báo cáo trình bày về các tính chất vật liệu ma sát đáp ứng yêu cầu làm việc trong các máy móc thiết bị hiện đại mà hiện nay nước ta còn phải nhập ngoại, khái quát về thành phần hóa học của một số mác vật liệu ma sát làm việc trong điều kiện có dầu bôi trơn trên cơ sở nền đồng, cùng với cơ tính vật liệu ma sát có chứa nhôm từ nguồn tại liệu do các nước thuộc khối Liên xô chế tạo. Bên cạnh đó, tác giả còn trình bày về vật liệu ma sát trên cơ sở nền sắt, làm việc trong điều kiện ma sát khô của các bộ phanh hãm chế tạo bằng công nghệ luyện kim bột. 2) Từ những tính chất của một sô vật liệu ma sát hiện được sử dụng trong chế tạo máy, trong đó có mẫu bộ đĩa ma sát trong bộ ly hợp động cơ ô tô vận tải mỏ loại có tải trọng 35 tấn đang hoạt độ tại các mỏ khai thác than ở tỉnh Quảng Ninh, tác giả báo cáo đã chọn phương án công nghệ chế tạo là bằng phương pháp ép nóng bột kim loại lên nền thép. Công nghệ ép nóng đồng thời với việc thiêu kết bột kim loại (thiêu kết dưới áp lực) hiện nay hoàn toàn có thể thực hiện được trong điều kiện Việt Nam, vì đã có nhiều sơ sở nghiên cứu chuyên ngành và sản xuất được đầu tư thiết bị luyện kim bột. Tuy nhiên, mức đầu tư còn nhỏ Tóm tắt Bài báo của nhóm tác giả trình bày khái quát về tính chất vật liệu ma sát đang được sử dụng phổ biến trong ngành chế tạo máy được chế tạo bằng phương pháp công nghệ luyện kim bột tại một số nước công nghiệp phát triển trên thế giới. Một trong những nhóm vật liệu ma sát dùng cho việc chế tạo các đĩa ly hợp động cơ ô tô, điezen là vật liệu trên cơ sở hợp kim nhôm - đồng hoặc hợp kim nhôm - thiếc - đồng đã được nghiên cứu phân tích trên các mẫu điã ly hợp động cơ ô tô vận tải mỏ tại Quảng Ninh do nhóm nghiên cứu tại Viện nghiên cứu Cơ khí thực hiện. Friction powder materials in mechanical engineering Ha Minh Hung (National Research Institute of Mechanical Engineering) Nguyen Van Giap(Thai Nguyen University of Technology ) 1.Summary The Paper presents overview of powder metallurgy friction material used in machine manufacturing in developed industrial countries. Aluminum – copper and aluminum – Tin – copper based alloys are friction material groups used in automobile engine’s clutche disk are analyzed based on specimens in heavy trucks used in Quang Ninh’ mining regions by authors at National Research Institute of Mechanical Engineering. 2. Introduction In developed country, Powder metallurgy friction materials are applied in brake and transmission components of transportation vehicles, agricultural, mining, construction, pressing, punching machines, machine tools and aircraft. Friction materials are more durable, reliability and effective materials than and are excellent alternatives for traditional materials (steels, cast Héi th¶o Khoa häc toµn quèc C«ng nghÖ vËt liÖu vµ bÒ mÆt - Th¸i Nguyªn 2008 44 iron and iron or steel fastened friction materials) used in components working in wet conditions such as clutches disks, speed regulator, critical moment joints, and hydraulic power transmission system or in “dry” operation conditions such as couplers, brakes, electromagnetic couplers. Powder metallurgy friction materials enable to design and produce new structure friction assemblies with high friction coefficient, reliability, wear – resistance and heat resistance [1, 2]. In Vietnam, fabrication of anti-friction and friction materials [3-6, 7] have been researched by NARIME several professional research centers but the results are insufficient to meet requirements of market, particularly of coal and mineral mining vehicles. Every year, imported mining trucks, devices and equipments need replace many wearing parts, especially clutch disks. Most of these are costly imported parts and result in breaking of production plan. Because of mentioned reasons, fabrication technology of composite materials used in clutch disks of mining heavy trucks is chosen to research in order to produce alternative imported parts. 3. Solution: Research methods: empirical research method Step 1. Carry out survey and research copper - aluminum - steel or copper trimetal clutch disks of heavy trucks made in Russia and other countries used in Quang Ninh province’s mining regions to build set of quality evaluation criteria. Step 2. Carry out pressing and sintering experiments on copper – aluminum or copper – tin – aluminum powder metallurgy friction materials that equivalent to composition of Russian products to optimize fabrication technology of composite material through quality evaluation criteria. Step 3. Pilot production: Produce small batch clutch disks of heavy trucks applying hot – pressing. Install products, monitor quality and reliability of products. 4. Research results: The results are presented in the report Tài liệu tham khảo [1]. Игнатов Л. И. , Колпаков Я. Б., Крысин Б. Т. , Лебедева Л. П., Михайловский В. А., (1968), “Производство фрикционных материалов на основе железной основе”, Москва, Металлургия, 176 стр.; [2]. Федорченко И. М., Крячек В. М., Патайоти И. И., (1975),”Современнные фрикционнные материалы”, Киев, Наумкова думка,336 стр.; [3]. И. М. Федоренко и другие, (1978), “Свойства порошков металлов, тугоплавких соединений и спеченных материалов”, Киев, “Наукова Думка”, 183 стр.; [4]. Под редакцией док. техн. наук Б. С. Митина, (1987), “Порошковая металлургия и напыленные покрытия”, Москва, “Металлургия”, 792 стр.; [5]. Hà Minh Hùng, (2000), “Nghiên cứu thử nghiệm công nghệ ép nóng kim loại bột để chế tạo chi tiết máy”, Tuyển tập các công trình NCKH Viện Nghiên cứu Cơ khí, Tập I, trang 16-23; [6]. Hà Minh Hùng, (2002), “Nghiên cứu ảnh hưởng của biến dạng dẻo đến tính chất bimetal thép + hợp kim đồng thiêu kết”, Tạp chí Cơ khí Việt Nam, số 68, trang 32-35; [7]. Trần Sỹ Kháng và các tác giả, (2006), “Nghiên cứu chế tạo má phanh máy bay L-39 bằng công nghệ ép nóng”, Tạp chí Kỹ thuật và Trang bị, số 74,11/2006, trang 45- 47.
File đính kèm:
vat_lieu_ma_sat_luyen_kim_bot_trong_che_tao_may.pdf