The study on recrystallization annealing the plate of high-strength Al-Zn-Mg-Cu alloy
TÓM TẮT
NGHIÊN CỨU CHẾ ĐỘ Ủ KẾT TINH LẠI TẤM HỢP KIM NHÔM
ĐỘ BỀN CAO HỆ Al-Zn-Mg-Cu
Hợp kim nhôm độ bền cao hệ Al-Zn-Mg-Cu sau khi đúc dạng thỏi thường
được cán thành các tấm có chiều dày khác nhau. Để trở lại tổ chức ban đầu
sau khi biến dạng, các tấm hợp kim nhôm phải tiến hành ủ kết tinh lại. Chế
độ độ ủ kết tinh lại phụ thuộc vào các yếu tố chính như: nhiệt độ, thời gian ủ.
Chất lượng ủ kết tinh lại được đánh giá bởi tổ chức tế vi, ảnh hiển vi điện tử
quét (SEM) và độ cứng của hợp kim. Bằng phương pháp xác định tổ chức tế
vi, ảnh SEM và độ cứng của hợp kim nhôm dạng tấm hệ Al-Zn-Mg-Cu ở các
chế độ ủ kết tinh lại khác nhau cho thấy chế độ ủ kết tinh lại hợp lý là nhiệt
độ 415 oC, giữ nhiệt 150 phút. Phôi tấm sau khi ủ có tổ chức đồng đều, độ
cứng đạt 67,2 HB.
Từ khóa: Hợp kim Al-Zn-Mg-Cu, Hợp kim 7075, Ủ kết tinh lại.
Tóm tắt nội dung tài liệu: The study on recrystallization annealing the plate of high-strength Al-Zn-Mg-Cu alloy
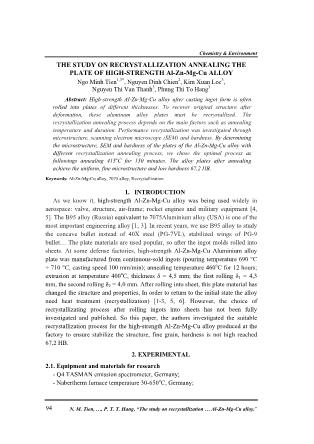
Chemistry & Environment N. M. Tien, , P. T. T. Hang, “The study on recrystallization Al-Zn-Mg-Cu alloy.” 94 THE STUDY ON RECRYSTALLIZATION ANNEALING THE PLATE OF HIGH-STRENGTH Al-Zn-Mg-Cu ALLOY Ngo Minh Tien1,3*, Nguyen Dinh Chien2, Kim Xuan Loc3, Nguyen Thi Van Thanh3, Phung Thi To Hang3 Abstract: High-strength Al-Zn-Mg-Cu alloy after casting ingot form is often rolled into plates of different thicknesses. To recover original structure after deformation, these aluminum alloy plates must be recrystallized. The recrystallization annealing process depends on the main factors such as annealing temperature and duration. Performance recrystallization was investigated through microstructure, scanning electron microscope (SEM) and hardness. By determining the microstructure, SEM and hardness of the plates of the Al-Zn-Mg-Cu alloy with different recrystallization annealing process, we chose the optimal process as followings annealing 415oC for 150 minutes. The alloy plates after annealing achieve the uniform, fine microstructure and low hardness 67,2 HB. Keywords: Al-Zn-Mg-Cu alloy, 7075 alloy, Recrystallization. 1. INTRODUCTION As we know it, high-strength Al-Zn-Mg-Cu alloy was being used widely in aerospace: valve, structure, air-frame; rocket engines and military equipment [4, 5]. The B95 alloy (Russia) equivalent to 7075Aluminium alloy (USA) is one of the most important engineering alloy [1, 3]. In recent years, we use B95 alloy to study the concave bullet instead of 40X steel (PG-7VL), stabilized wings of PG-9 bullet The plate materials are used popular, so after the ingot molds rolled into sheets. At some defense factories, high-strength Al-Zn-Mg-Cu Aluminium alloy plate was manufactured from continuous-sold ingots (pouring temperature 690 °C ÷ 710 °C, casting speed 100 mm/min); annealing temperature 460oC for 12 hours; extrusion at temperature 400oC, thickness δ = 4,5 mm; the first rolling δ1 = 4,3 mm, the second rolling δ2 = 4,0 mm. After rolling into sheet, this plate material has changed the structure and properties, In order to return to the initial state the alloy need heat treatment (recrystallization) [1-3, 5, 6]. However, the choice of recrystallizating process after rolling ingots into sheets has not been fully investigated and published. So this paper, the authors investigated the suitable recrystallization process for the high-strength Al-Zn-Mg-Cu alloy produced at the factory to ensure stabilize the structure, fine grain, hardness is not high reached 67,2 HB. 2. EXPERIMENTAL 2.1. Equipment and materials for research - Q4 TASMAN emission spectrometer, Germany; - Nabertherm furnace temperature 30-650oC, Germany; Research Journal of Military Science and Technology, Special Issue, No.54A, 05 - 2018 95 - Struers cut-off equipment with cutting speed of 100-400 rpm, Denmark; - Metal polishing equipment, USA; - SiC paper have a particle size ranging from 120 to 2000; - Cr2O3 polishing powder, size μm; - Chemicals to etching: HCl, HF, HNO3 of china; distilled water - AXIO A2M equipment, Germany; - Brinel HP-250 Hardness Testers, Germany; -JSM-7001FA FE-SEM Scanning Electron Microscope Analysis JEOL, Japan, magnification 2000 times at Shimane University, Japan. 2.2. Fabrication 2.2.1. Fabricate rrecrystallization sample - Fabricate the sample on Struers, cutting speed 200 rpm, size 10 x 10 x 4 mm; - Examination of different tempering samples with a constant heat up rate of 5 °C/min in the temperature range of 250 ÷ 450 °C and a heat retention time of 30 ÷ 180 minutes; Cooling the same furnace. 2.2.2. Determine the microscopic organization of the sample - Clip the sample using a dedicated tool or epoxy pour to position the flat smooth sample; - Grinding SiC paper has different grain level increasing from 180 to 2000 ensuring flat, smooth, no visible scratches on the surface.; - Polishing the specimen using a special machine, using Cr2O3 grinding powder ensure smooth surface; - Etch based on Keller solution; 2.2.3. Determination of hardness, degree of recrystallization of sample - Hardness of the sample on a Brinell HP-250 equipment with a load of 250 kg; D = 5 mm; - The degree of recrystallization Xs (%) is determined by the expression: Xs = (H0-H)/(H0-Hrec) [5]; Where: Xs - crystallization; H0 - initial plate hardness; H - hardness after recrystallization; Hrec - hardness after recrystallization completely. 3. RESULTS AND DISCUSSION 3.1. Survey of original materials The sample was Al-Zn-Mg-Cu aluminum alloy rolled in the factory (symbol X59), the composition of Table 1. Table 1. Component composition X59, B95 (Russia) equivalent to 7075 (USA). Alloy sample Composition of aluminum alloy,% Fe Si Mn Ni Cr Ti Al Cu Mg Zn B95 Max Max 0,2- Max 0,1- Max 86,3- 1,4- 1,8- 5,0- Chemistry & Environment N. M. Tien, , P. T. T. Hang, “The study on recrystallization Al-Zn-Mg-Cu alloy.” 96 (Russia) 0,5 0,5 0,6 0,1 0,25 0,05 91,5 2,0 2,8 7,0 X59 0,338 0,094 0,390 0,006 0,181 0,023 89,286 1,836 2,103 5,668 According to Table 1, X59 is a high strength Al-Zn-Mg-Cu aluminum alloy and has the same composition as B95 (Russia) or 7075 (USA). To better understand the X59 the high strength aluminum alloy sheet specimen, the team conducted a microscopic imaging (Figure 1), SEM image (Figure 2), and determined the hardness of the sample after rolling H0 is quite high, reaching an average of 123 HB. The microstructure (Fig. 1) and the SEM image (Fig. 2) after extruding in the factory exhibited uneven distribution phases in the roll strip. Cause when the particles are deformed by the rolling method: The small phase hardness is not broken but dispersed into strips in parallel with the rolling, so it will affect the properties of the product compared to the original pattern. Figure 1. Microstructure of the X59, X500. Figure 2. SEM image X59, X2000. The alloys after rolling need to choose the suitable recrystallization mode for uniform component, stable structure and properties. 3.2. Survey of recrystallization temperature The recrystallization temperature of the alloy was investigated by the authors at different temperatures from 250 °C to 450 °C. The results of the microstructure analysis, SEM images are shown in Figure 3. a) At 250 oC b) At 300 oC c) At 350 oC Research Journal of Military Science and Technology, Special Issue, No.54A, 05 - 2018 97 d) At 415 oC e) At 450 oC f) At 415 oC Fig. 3. a-e) Image of the alloyed microstructure after recrystallization at different temperatures at 500 times magnification and f) SEM image at 415 °C, X2000 The result of microscopic image of the alloy after recrystallization (Figure 3) showed that the post-recrystalline alloy samples had a more uniform structure, smoother fineness, and progressive strip loss than the original sample. However, at different annealing temperatures there are different microstructures, at the higher temperature, the better the microscopic distribution, the gradual strips are removed. At the temperatures of 250 °C, 300 °C, 350 °C arranged in milled leaves are still but fading. This proves that recrystallization process at these temperatures is effective but not yet high. However, the annealing temperature is not sufficient to ensure that the structure is oriented smoothly. Increase recrystallization temperature to 415oC, the microstructure of the alloy is dispersed phase, small smooth, no longer see the rolling strip (Figure 3d). This is explained that at 415oC, the first recrystallization process occurs completely, the microstructure is uniform, not yet recombined. This is also consistent with the SEM image observation (Figure 3f) showing that the dispersed phases are smooth, no longer smooth strips such as the original X59 (Figure 2). As the temperature rises to 450oC, the microstructure of the alloy consists of several large phases mixed with little phase and no strips in the microstructure of the sample (Figure 3e). This may be due to the fact that at a temperature of 450 °C, the first recrystallization process has occurred completely and the phenomenon of the second recrystallization phase begins. The second recrystallization process is undesirable as it affects the uniformity of the microstructure and the properties of the reduced material. To better understand the influence of temperature on the mechanical properties of materials, the team determined the hardness of the alloy at different recrystallization temperatures. The results are shown in table 2. The results showed that the alloys after tempering decreased hardness compared to the X59 sample (123 HB). However, at different annealing temperatures, the hardness decreases and the degree of recrystallization of the alloy is different. Chemistry & Environment N. M. Tien, , P. T. T. Hang, “The study on recrystallization Al-Zn-Mg-Cu alloy.” 98 Table 2. Hardness of the alloy after recrystallization at different temperatures. Recrystallization temperatures, oC Hardness, HB Xs, % At 1 At 2 At 3 Average H0 Hrec 250 76,0 77,0 76,0 76,3 123 67,2 83,69 300 72,0 72,5 73,0 72,5 123 67,2 90,50 350 68,9 68,9 68,9 68,9 123 67,2 96,95 400 67,7 67,8 67,9 67,8 123 67,2 98,93 415 67,2 67,2 67,2 67,2 123 67,2 100 450 67,1 67,2 67,3 67,2 123 67,2 100 As the annealing temperature increases, the hardness decreases, the recrystallization efficiency increases. The smallest hardness was 67,2 HB, the recrystallization efficiency was 100% at annealing temperature of 415oC to 450oC. This result is perfectly consistent with the microstructure obtained in Figure 3. 3.3. Survey of recrystallization time The authors investigated the tempering samples at 415 °C, the heating rate of 5 °C/min with the period time varied from 30 minutes to 180 minutes. The results of the microstructure analysis are shown in Figure 4. It has been observed from Figure 4, that the recrystallization time for 120 minutes, the microstructure of the alloy consists of small, alternating, unevenly distributed layers (Fig. 4a). When the period time is increased to 150 minutes, the microstructure of the alloy is smooth, evenly distributed, no longer recognizing the strips (Fig. 4b). This will be done because of annealing temperature at 120 minutes the first recrystallization has been done but hasn’t been done completed when the last 150 minutes the first recrystallization has been done completely. If continue to increase at 415oC for 180 minutes, the alloy microstructure includes several multi phase, many large phase and low fine phase, lost rolling strip. This showed that, when increasing the time to 180 minutes, the second recrystallization occurred, the merged phases grew and the fine phases had been dissolved. This is an unwanted crystallization stage in the recrystallization process of the alloy. a) At 120 minutes b) At 150 minutes c) At 180 minutes Figure 4. The microstructure image of the alloy after crystallization at 415°C for different period times with magnification of 500 times. Research Journal of Military Science and Technology, Special Issue, No.54A, 05 - 2018 99 To understand the effect of recrystallization time to be better, the authors investigated the hardness of the alloy at different period times (Table 3). Table 3. Hardness of the alloy after recrystallization at different times. Recrystallization time, minute Hardness, HB Xs, % At 1 At 2 At 3 Average H0 Hrec 30 76,4 76,4 76,7 76,5 123 67,2 83,33 60 70,7 70,6 70,5 70,6 123 67,2 93,91 90 70,4 70,1 70,1 70,2 123 67,2 94,62 120 69,5 69,6 69,4 69,5 123 67,2 95,88 150 67,2 67,2 67,2 67,2 123 67,2 100 180 67,1 67,2 67,3 67,2 123 67,2 100 The results showed that the sample after annealing had a much lower hardness than the original alloy. Hardness decreases much and efficiency increases as the annealing time increases. Recrystallization occurs completely when the period time is 150 minutes. When increasing the annealing time for 180 minutes, the hardness of the alloy does not change. Thus, the recrystallization optimized for the X59 aluminum alloy plates is 150 minutes at 415 °C, the obtained product is organized micro-fine phase, smooth distribution, no longer strips, hardness achieved smallest 67,2 HB and the first recrystallization process occurred completely. 4. CONCLUSION From the results of the study on the recrystallization of the X59 alloy plates after rolling the high-strength Al-Zn-Mg-Cu aluminum alloy, the authors show some conclusions: - The aluminum alloy sheets after rolling should be tempered to recrystallize to stabilize the organization, structure and properties. - The recrystallization was completely crystallized for the X59 specimens after rolling at a temperature of 415 °C for 150 minutes, speed of heat up 5 °C/min. After recrystallizing, the alloy is no longer oriented according to the rolling direction, the fineness is smooth, dispersed, low hardness average 67,2 HB. REFERENCES [1]. Lê Công Dưỡng, “Vật liệu Học”, NXB Khoa học và Kỹ thuật, Hà Nội, 2000. [2]. Phạm Minh Phương, Tạ Văn Thất, “Công nghệ nhiệt luyện”, NXB Giáo dục, Hà Nội, 2000. [3]. Nguyễn Khắc Xương, “Vật liệu kim loại màu”, NXB Khoa học và Kỹ thuật, Hà Nội, 2003. Chemistry & Environment N. M. Tien, , P. T. T. Hang, “The study on recrystallization Al-Zn-Mg-Cu alloy.” 100 [4]. Williams J.C. and Starke E.A. Jr., "Progress in structural materials for aerospace systems", Acta Material, 51(19), 2003, 5775-5799. [5]. M. Tajally and Z. Huda "Recrystallization kinetics for aluminum alloy 7075", Metal Science and Heat Treatment, Vol.53, Nos.5–6, September, 2011. [6]. A.C Umamaheshwer Rao, V. Vasu, M. Govindaraju and K.V. Sai Srinadh, "Influence of cold rolling and annealing on the tensile properties of aluminum 7075 alloy", Procedia Materials Science 5, International conference on advances in manufacturing and materials engineering AMME 2014, 86-95. TÓM TẮT NGHIÊN CỨU CHẾ ĐỘ Ủ KẾT TINH LẠI TẤM HỢP KIM NHÔM ĐỘ BỀN CAO HỆ Al-Zn-Mg-Cu Hợp kim nhôm độ bền cao hệ Al-Zn-Mg-Cu sau khi đúc dạng thỏi thường được cán thành các tấm có chiều dày khác nhau. Để trở lại tổ chức ban đầu sau khi biến dạng, các tấm hợp kim nhôm phải tiến hành ủ kết tinh lại. Chế độ độ ủ kết tinh lại phụ thuộc vào các yếu tố chính như: nhiệt độ, thời gian ủ. Chất lượng ủ kết tinh lại được đánh giá bởi tổ chức tế vi, ảnh hiển vi điện tử quét (SEM) và độ cứng của hợp kim. Bằng phương pháp xác định tổ chức tế vi, ảnh SEM và độ cứng của hợp kim nhôm dạng tấm hệ Al-Zn-Mg-Cu ở các chế độ ủ kết tinh lại khác nhau cho thấy chế độ ủ kết tinh lại hợp lý là nhiệt độ 415 oC, giữ nhiệt 150 phút. Phôi tấm sau khi ủ có tổ chức đồng đều, độ cứng đạt 67,2 HB. Từ khóa: Hợp kim Al-Zn-Mg-Cu, Hợp kim 7075, Ủ kết tinh lại. Received 28th December 2017 Revised 25th March 2018 Accepted 20th April 2018 Author affiliations: 1 Institute of Chemistry and Materials, Academy of Military Science and Technology; 2 Military Technical Academy; 3 Hanoi University of Technology. * Email: tienngominh.klh@gmail.com.
File đính kèm:
the_study_on_recrystallization_annealing_the_plate_of_high_s.pdf