Influence of curing parameters on chemical fixation and water resistance of modified beech veneers
ẢNH HƯỞNG CỦA THÔNG SỐ CHẾ ĐỘ XỬ LÝ NHIỆT
ĐẾN SỰ CỐ ĐỊNH LẠI CỦA HÓA CHẤT VÀ KHẢ NĂNG CHỐNG HÚT NƯỚC
CỦA VÁN MỎNG GỖ BEECH BIẾN TÍNH
TÓM TẮT
Trong nghiên cứu này, ván mỏng lạng từ gỗ Beech (Fagus sylvatica. L) với kích thước 37 × 0.5 × 50 mm3 (XT
× TT × DT) đã được lọc rửa qua thiết bị soxhlet bằng nước nóng và các dung môi hữu cơ (cyclohexan và
ethanol, tỷ lệ thể tích 2:1), sau đó ván mỏng được sấy khô trước khi ngâm tẩm với các dung dịch hóa chất biến
tính. Ba loại hóa chất đã được sử dụng để biến tính ván mỏng là: N-methylol melamine (NMM-1 - sử dụng ở
hàm lượng rắn 10%), fatty acid modified N-methylol melamine/paraffin (mNMM-2 - sử dụng ở hàm lượng rắn
5%), alkyl ketene dimer (AKD - sử dụng ở hàm lượng rắn 1%). Ván mỏng sau khi tẩm hóa chất biến tính được
hong phơi 2 ngày ở điều kiện phòng rồi xử lý nhiệt (curing) trong máy ép nhiệt với các thông số chế độ ép
(nhiệt độ và thời gian) khác nhau. Cụ thể: nhiệt độ: 130°C, 160°C; áp suất: 1 N/mm2; thời gian ép: 5, 10, 20
phút. Kết quả nghiên cứu cho thấy: thời gian ép 5 phút và nhiệt độ ép 130°C không gây ảnh hưởng xấu đến tỷ
lệ tăng khối lượng (WPG) và tỷ lệ tăng kích thước chiều tiếp tuyến (RBE), độ ẩm thăng bằng (EMCR) và tỷ lệ
trương nở chiều tiếp tuyến (RS) (trong môi trường 20°C, độ ẩm 65%), và tỷ lệ tổn hao khối lượng (WL). Bên
cạnh đó, khả năng chống hút nước của ván mỏng biến tính sau khi bị lọc rửa qua thiết bị soxhlet với các dung
môi hữu cơ và các lần ngâm nước cho kết quả tốt nhất trong trường hợp ván mỏng được xử lý nhiệt ở chế độ:
thời gian ép 5 phút và nhiệt độ ép 130°C. Hơn thế nữa, giảm thời gian và nhiệt độ của quá trình xử lý nhiệt
trong máy ép nhiệt có thể ngăn chặn được hiện tượng “sấy quá” của ván mỏng trước khi tráng keo để sản xuất
ván dán. Do đó, thời gian ép 5 phút và nhiệt độ ép 130°C đã được lựa chọn để xử lý nhiệt ván mỏng trong máy
ép nhiệt. Ảnh hưởng của thông số chế độ xử lý nhiệt (bằng máy ép nhiệt) đến các tính chất của ván mỏng biến
tính với mỗi loại hóa chất đã được thảo luận chi tiết trong bài báo.
Từ khóa: Alkyl ketene dimer, độ ẩm thăng bằng, khả năng chống hút nước, N-methylol melamine, sự cố
định lại của hóa chất, ván mỏng gỗ beech (Fagus sylvatica. L).
Tóm tắt nội dung tài liệu: Influence of curing parameters on chemical fixation and water resistance of modified beech veneers
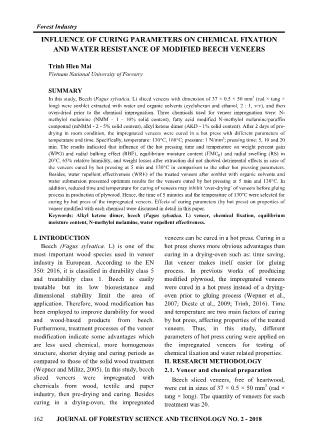
Forest Industry JOURNAL OF FORESTRY SCIENCE AND TECHNOLOGY NO. 2 - 2018 162 INFLUENCE OF CURING PARAMETERS ON CHEMICAL FIXATION AND WATER RESISTANCE OF MODIFIED BEECH VENEERS Trinh Hien Mai Vietnam National University of Forestry SUMMARY In this study, Beech (Fagus sylvatica. L) sliced veneers with dimension of 37 × 0.5 × 50 mm3 (rad × tang × long) were soxhlet extracted with water and organic solvents (cyclohexan and ethanol, 2 : 1, v/v), and then oven-dried prior to the chemical impregnation. Three chemicals used for veneer impregnation were: N- methylol melamine (NMM - 1 - 10% solid content), fatty acid modified N-methylol melamine/paraffin compound (mNMM - 2 - 5% solid content), alkyl ketene dimer (AKD - 1% solid content). After 2 days of pre- drying in room condition, the impregnated veneers were cured in a hot press with different parameters of temperature and time. Specifically, temperature: 130°C, 160°C; pressure: 1 N/mm2; pressing time: 5, 10 and 20 min. The results indicated that influence of the hot pressing time and temperature on weight percent gain (WPG) and radial bulking effect (RBE), equilibrium moisture content (EMCR) and radial swelling (RS) in 20°C, 65% relative humidity, and weight losses after extraction did not showed detrimental effects in case of the veneers cured by hot pressing at 5 min and 130°C in comparison to the other hot pressing parameters. Besides, water repellent effectiveness (WRE) of the treated veneers after soxhlet with organic solvents and water submersion presented optimum results for the veneers cured by hot pressing at 5 min and 130°C. In addition, reduced time and temperature for curing of veneers may inhibit ‘over-drying’ of veneers before gluing process in production of plywood. Hence, the time of 5 minutes and the temperature of 130°C were selected for curing by hot press of the impregnated veneers. Effects of curing parameters (by hot press) on properties of veneer modified with each chemical were discussed in detail in this paper. Keywords: Alkyl ketene dimer, beech (Fagus sylvatica. L) veneer, chemical fixation, equilibrium moisture content, N-methylol melamine, water repellent effectiveness. I. INTRODUCTION Beech (Fagus sylvatica. L) is one of the most important wood species used in veneer industry in European. According to the EN 350: 2016, it is classified in durability class 5 and treatability class 1. Beech is easily treatable but its low bioresistance and dimensional stability limit the area of application. Therefore, wood modification has been employed to improve durability for wood and wood-based products from beech. Furthermore, treatment processes of the veneer modification indicate some advantages which are less used chemical, more homogenous structure, shorter drying and curing periods as compared to those of the solid wood treatment (Wepner and Militz, 2005). In this study, beech sliced veneers were impregnated with chemicals from wood, textile and paper industry, then pre-drying and curing. Besides curing in a drying-oven, the impregnated veneers can be cured in a hot press. Curing in a hot press shows more obvious advantages than curing in a drying-oven such as: time saving, flat veneer makes itself easier for gluing process. In previous works of producing modified plywood, the impregnated veneers were cured in a hot press instead of a drying- oven prior to gluing process (Wepner et al., 2007; Dieste et al., 2009; Trinh, 2016). Time and temperature are two main factors of curing by hot press, affecting properties of the treated veneers. Thus, in this study, different parameters of hot press curing were applied on the impregnated veneers for testing of chemical fixation and water related properties. II. RESEARCH METHODOLOGY 2.1. Veneer and chemical preparation Beech sliced veneers, free of heartwood, were cut in sizes of 37 × 0.5 × 50 mm3 (rad × tang × long). The quantity of veneers for each treatment was 20. Forest Industry JOURNAL OF FORESTRY SCIENCE AND TECHNOLOGY NO. 2 - 2018 163 Three chemicals were diluted with water to the different concentrations as follows: a) N-methylol melamine (NMM-1): 10% solid content (15.5% stock concentration) Madurit MW 840/75 WA (NMM-1) delivered by INEOS company, is an N- methylol melamine resin dissolved in water. NMM-1 is a colorless and clear liquid with pH value from 10 - 11 at 20°C. NMM-1 is used for impregnation of solid wood with a solid content between 10 and 40%. The drying process of impregnated wood includes two steps. In the first step, the temperature during the first 24 h must be lower than 50oC to remove the bulk of water and protect the wood against the formation of cracks. In the second step, a sufficient condensation of the resin is needed, if the temperature is not up to 100oC, the time for reaction must last longer. b) Fatty acid modified N-methylol melamine/paraffin compound (mNMM-2): 5% solid content (13.2% stock concentration) with catalyst RB 1.9% (equal to 15% of mNMM-2 stock solution w/w). Phobotex VFN (mNMM-2) delivered by Ciba company, is a fatty acid of modified N- methylol melamine (methoxymethylen melamine and paraffin). mNMM-2 is a white dispersion with pH value from 4 - 6 at 20oC. mNMM-2 is a product for washfast and water repellent finishes which can be used as a finishing agent for textiles. mNMM-2 should be combined with catalyst RB(aluminium salt) to obtain optimal water repellent effect. mNMM-2 can be diluted in cold water and applied by padding at room temperature for cotton fibers, then dried at 120 - 140oC and cured for 2 min at 160oC or 4 - 5 min at 150oC. c) Alkyl ketene dimer (AKD): 1% solid content (6.7% stock concentration) Basoplast AKD delivered by BASF company, is a fatty acid alkyl ketene dimer (AKD) in form of a white dispersion with average pH value from 3.5 - 4.5. AKD is hydrophobization of paper, especially when made under alkaline conditions. AKD is widely used for liquid containers, ink-jet printing paper, and many other grades of paper and paperboard. AKD is especially favored for products that need to resist water over a long period. 2.2. Treatment of the veneers The veneers were soxhlet extracted with water and organic solvents, and then oven- dried prior to the chemical impregnation. Water extraction was performed with total running time of 6 h. Organic solvent (cyclohexan and ethanol, 2 : 1, v/v) extraction was carried out in the same way as the water extraction. After 2 days of pre-drying in room condition, the impregnated veneers were cured in a hot press with different parameters of temperature and time: - Temperature: 130oC, 160oC; Pressure: 1 N/mm2 ; Time: 5, 10 and 20 min. Veneers impregnated with water served as control specimens. The test procedure is presented in figure 1. 2.3. Chemical fixation and water related properties of the veneers Prior to the tests, the treated and control veneers were conditioned in a climate chamber at 20oC and 65% RH until constant weight. Then, 5 veneers from each treatment were oven-dried for determination of moisture content of the veneers at 20oC and 65% RH as the following: 100(%) 1 1 W WW M c (Equation 1) Where: W1: Oven-dry weight of veneers (g) after conditioning (the same as oven-dried weight after curing); Wc: Constant weight of veneer (g) conditioned in the climate chamber 20oC, 65% RH; M: Moisture content of veneer (%) at 20oC and 65% RH. Hence, the oven-dry weight of the other 15 Forest Industry JOURNAL OF FORESTRY SCIENCE AND TECHNOLOGY NO. 2 - 2018 164 veneers after curing was calculated by extrapolation from the constant weight and moisture content of the veneers at 20oC and 65% RH, using Equation 2: 100 100 1 M W W c (Equation 2) The WPG and RBE of the treated and control veneers were determined as in Equation 3 and Equation 4, respectively: 100(%) 1 o o W WW WPG (Equation 3) Where: WPG: Weight percent gain of the treated veneer (%); W1: Oven-dry weight of veneer after curing (g); Wo: Oven-dry weight of veneer before chemical impregnation (g). 100(%) 1 o o RD RDRD RBE (Equation 4) Where: RBE: Radial bulking effect of the treated veneer (%); RD1: Radial dimension of oven-dry veneer after curing (mm); RDo: Radial dimension of oven-dry veneer before chemical impregnation (mm). Similarly, EMCR and RS were calculated according to Equation 5 and Equation 6, respectively: 100(%) 14 o R W WW EMC (Equation 5) 100(%) 1 14 RD RDRD RS (Equation 6) Where: EMCR and RS: Equilibrium moisture content and radial swelling of the veneer (%); Wo: Oven-dry weight of the veneer before chemical treatment (g); W1 and RD 1: Oven-dry weight (g) and radial dimension (mm) of the veneer after curing (before conditioning); W4 and RD4: Weight (g) and radial dimension (mm) of veneer after conditioning. The cyclohexan and ethanol (2:1, v/v) extraction was carried out for 6 h with 5 veneers per treatment. The weight loss (WLE) determination was calculated in the same way as in the water extraction (Equation 7): 100(%) 1 31 W WW WLE (Equation 7) Where: WLE: Weight loss after extraction (%); W1: Oven-dry weight of veneer after curing (g); W3: Oven-dry weight of veneer after extraction (g). Ten veneers per treatment were submersed one by one in a water bath at room temperature for the continuous times: 1 min, 10 min, 1 h, 2 h, 4 h (submersion 1). The water uptake (WU) and water repellent effectiveness (WRE) were calculated following Equation 8 and Equation 9: 100(%) o ba W WW WU (Equation 8) Where: WU: Water uptake (%); Wa: Veneer weight (g) after water submersion (1 min, 10 min, 1 h, 2 h, 4 h); Wb: Veneer weight before water submersion (g); Wo: Oven-dry weight of veneer before chemical impregnation (g). For comparison of the water uptake between the treated and the control veneers, water repellent effectiveness (WRE) was expressed as in Equation 9: 100(%) control treatedcontrol WU WUWU WRE (Equation 9) Where: WRE: Water repellent effectiveness (%); WUcontrol: Water uptake of control veneer (%); WUtreated: Water uptake of treated veneer (%). Then, the veneers were continued with oven-drying, organic solvent extraction, submersion 2 or submersion 3 (similar like submersion 1) as described in Fig 1. The weight loss of the veneers was based on oven-dried weight after curing and oven- dried weight after extraction or submersion as follows: Forest Industry JOURNAL OF FORESTRY SCIENCE AND TECHNOLOGY NO. 2 - 2018 165 100(%) 1 21 W WW WL (Equation 10) Where: WL: Weight loss after extraction, submersion (%); W1: Oven-dry weight of veneer after curing (g); W2: Oven-dry weight of veneer after extraction, submersion (g). Figure 1. Test procedure of the veneers Drying veneers at 103°C, 24 h Vacuum/pressure impregnation Pre-drying at room temperature for 2 days Curing by hot press at the different parameters Conditioning veneers in a climate chamber at 20°C and 65% RH (20 veneers/treatment) Cyclohexan and Ethanol (2:1) extraction 1 for 6 h (5 veneers/treatment) Submersion 1 (10 veneers/treatment) WRE1 Drying at 103°C, 24 h (5 veneers/treatment) Weight loss 1 Cyclohexane and Ethanol (2:1) extraction 2 for 6 h (5 veneers/treatment) Drying at 103°C, 24 h (5 veneers/treatment) Drying at 103°C, 24 h (5 veneers/treatment) Weight loss 3 Submersion 3 (5 veneers/treatment) WRE3 Submersion 2 (5 veneers/treatment) WRE2 Drying at 103°C, 24 h (5 veneers/treatment) Weight loss 2 Drying at 103°C, 24 h (5 veneers/treatment) Drying at 103°C, 24 h (5 veneers/ treatment) M, WPG, RBE, EMCR, RS Water extraction, 6 h Cutting veneers (37 × 0.5 × 50) mm3 Cyclohexan and ethanol (2:1) extraction, 6 h Forest Industry JOURNAL OF FORESTRY SCIENCE AND TECHNOLOGY NO. 2 - 2018 166 III. RESULTS AND DISCUSSION 3.1. Weight percent gain and radial bulking effect The veneers were extracted with hot water, and then cyclohexane and ethanol (2:1, v/v) prior to the impregnation and hot pressing. The WPGs of the control veneers showed minor negative values because the extractives in the veneers were continued removing during the impregnation and hot pressing (Figure 2). WPGs of the veneers treated with 5% solid content of mNMM-2 (catalyst RB) or 1% solid content of AKD did not change significantly when the temperature of the hot pressing increased from 130oC to 160oC. These WPGs did not depend on the pressing times (5 min, 10 min, 20 min), either (Figure 2). WPGs of 10% NMM-1 treated veneers changed considerably when the temperature of the hot pressing increased from 130oC to 160oC (WPGs were reduced from 22.6% to 15.9%, relatively). Figure 2. Weight percent gain (WPG) and radial bulking effect (RBE) of the control and treated veneers Another experiment was processed to evaluate if the WPG of NMM-1 treated veneers reduced with increasing temperature of the hot pressing. Glass dishes containing 20 g of NMM-1 stock solution were oven-dried for 24 h at different temperatures: 103oC, 120°C, 140°C, and 160°C. Then, these dishes were allowed to cool in desiccators to room temperature. Calculation of solid content was based on the weight of dried NMM-1 (solid, after drying) and the weight of NMM-1 stock solution (before drying) in each glass dish (w/w %). There were 3 replicates regard to each temperature. The results of this test are shown in table 1. Table 1. Solid content of NMM-1 stock solution at different temperatures Temperature (°C) 103 120 140 160 Solid content (w/w %) 74.8 71.9 70.5 68.5 Due to evaporation of some constituents in NMM-1 solution e.g. formaldehyde emission, the solid content of NMM-1 stock solution reduced with an increasing of oven-dried temperature. This is seen to be the reason for the decrease in WPG of NMM-1 treated veneers at higher temperature of the hot pressing besides loss in wood. -5 0 5 10 15 20 25 5 10 20 Pressing time (min) W e ig h t p e rc e n t g a in [ % ] Control 130°C NMM-1 130°C mNMM-2 130°C AKD 130°C Control 160°C NMM-1 160°C mNMM-2 160°C AKD 160°C -1.0 -0.5 0.0 0.5 1.0 1.5 2.0 2.5 3.0 Pressing time (min) R a d ia l b u lk in g e ff e c t [% ] Control 130°C NMM-1 130°C mNMM-2 130°C AKD 130°C Control 160°C NMM-1 160°C mNMM-2 160°C AKD 160°C 5 10 20 Forest Industry JOURNAL OF FORESTRY SCIENCE AND TECHNOLOGY NO. 2 - 2018 167 With regard to above WPGs, only NMM-1 treated veneers indicated a radial bulking effect (RBE, 1.9 - 2.7%), whereas the control, mNMM-2 and AKD treated veneers showed no RBE, even negative values (Figure 2). This bulking effect did not depend on the time or temperature of the hot pressing. Thus, longer pressing time or higher temperature did not enhance the deposition of these chemicals into the cell wall. Higher WPG and better penetration ability of melamine molecules into the cell wall resulted in bulking effect for NMM-1 treated veneers. While low WPGs together with large particle sizes of mNMM-2 and AKD particles could be reasons for no bulking effect of the treated veneers. 3.2. Equilibrium moisture content and radial swelling of the treated veneers at 20°C and 65% RH As can be seen in figure 3, EMCR and RS of the veneers did not change when temperature and pressing time were changed. Only NMM-1 treated veneers exposed significantly lower EMCR and RS than the control veneers (2 - 3%). High dimensional stability of melamine resin treated wood under humid condition was confirmed in many previous studies (Deka and Saikia, 2000; Inoue et al., 1993; Pittman et al., 1994). EMCR and RS of the veneers treated with mNMM-2 and AKD were not clearly different from those of the control veneers. Figure 3. Equilibrium moisture content (EMC) radial swelling (RS) of the control and treated veneers at 20°C and 65% RH Compared to the veneers cured in a drying- oven (Trinh and Nguyen, 2017), EMCR and RS of the veneers cured in the hot press were reduced in case of NMM-1 treatment due to higher WPG. On the contrary, EMCR and RS of mNMM-2 treated veneers cured in a hot press were higher than those cured in a drying- oven because of the lower WPG. While AKD treated veneers always showed the same EMCR and RS values as the controls in both cases cured in an oven and a hot press machine, regardless of WPG. 3.3. Water repellent effectiveness WRE 1 is the water repellent effectiveness of submersion 1 (as depicted in figure 1). This is the submersion of the veneers after curing and conditioning at 20°C and 65% RH. Similarly, WRE 2 is the water repellent 8 9 10 11 12 13 14 15 5 10 20 Pressing time (min) E q u il ib ri u m m o is tu re c o n te n t [% ] Control 130°C NMM-1 130°C mNMM-2 130°C AKD 130°C Control 160°C NMM-1 160°C mNMM-2 160°C AKD 160°C 1.0 1.5 2.0 2.5 3.0 5 10 20 Pressing time (min) R a d ia l s w e ll in g [ % ] Control 130°C NMM-1 130°C mNMM-2 130°C AKD 130°C Control 160°C NMM-1 160°C mNMM-2 160°C AKD 160°C Forest Industry JOURNAL OF FORESTRY SCIENCE AND TECHNOLOGY NO. 2 - 2018 168 effectiveness of submersion 2 for the dried- veneers after undergoing submersion 1. WRE 3 was used for the dried-veneers after submersion 1 and an organic solvent extraction. A B C Figure 4. Water repellent effectiveness (WRE) of the veneers treated with 10% solid content of NMM-1, cured in a hot press (A: WRE 1, B: WRE 2, C: WRE 3) As described in figure 4, WRE 1 of 10% NMM-1 treated veneers was higher than WRE 2 and WRE 3, regardless of hot pressing parameters (time and temperature). These results showed the same tendency as NMM-1 treated veneers cured in a drying-oven when submersed in water after the cycles (Trinh and Nguyen, 2017). This can be explained by the leaching of NMM-1 after submersion 1. The WRE 3 was not reduced significantly compared to the WRE 2 because the veneers treated with NMM-1 resulted in no weight loss through cyclohexan and ethanol extraction. A B C Figure 5. Water repellent effectiveness of the veneers treated with 5% solid content of mNMM-2 (catalyst RB), cured in a hot press (A: WRE 1, B: WRE 2, C: WRE 3) Like the oven-cured veneers, WRE 2 and WRE 3 of 5% mNMM-2 treated veneers (with catalyst RB) were improved compared to WRE 1 (Figure 5) most probable because hydrophilic compounds in the formulation were removed through submersion 1 and ongoing 0 10 20 30 40 50 60 70 80 90 0 50 100 150 200 250 Water submersion time [min] W R E 1 - N M M -1 [ % ] 130°C, 5 min 160°C, 5 min 0 10 20 30 40 50 60 70 80 90 0 50 100 150 200 250 Water submersion time [min] W R E 2 - N M M -1 [ % ] 130°C, 10 min 160°C, 10 min 0 10 20 30 40 50 60 70 80 90 0 50 100 150 200 250 Water submersion time [min] W R E 3 - N M M -1 [ % ] 130°C, 20 min 160°C, 20 min 0 10 20 30 40 50 60 70 80 90 0 50 100 150 200 250 Water submersion time [min] W R E 3 - m N M M -2 [ % ] 130°C, 20 min 160°C, 20 min 0 10 20 30 40 50 60 70 80 90 0 50 100 150 200 250 Water submersion time [min] W R E 1 - m N M M -2 [ % ] 130°C, 5 min 160°C, 5 min 0 10 20 30 40 50 60 70 80 90 0 50 100 150 200 250 Water submersion time [min] W R E 2 - m N M M -2 [ % ] 130°C, 10 min 160°C, 10 min Forest Industry JOURNAL OF FORESTRY SCIENCE AND TECHNOLOGY NO. 2 - 2018 169 condensation occurred during the drying process. There was high weight loss due to the organic extraction; however, the WRE 3 was not lower than the WRE 2. A B C Figure 6. Water repellent effectiveness of the veneers treated with 1% solid content of AKD, cured in a hot press (A: WRE 1, B: WRE 2, C: WRE 3) WRE of 1% AKD treated veneers was slightly reduced from submersion 1 to submersion 3 (Figure 6) due to leaching of AKD, the tendency is different from 10% AKD treated veneers cured in drying-oven (Trinh and Nguyen, 2017). This might be explained by leaching effect of hydrophilic emulsifier (cationic starch) in 10% AKD treated veneers. Water repellence of the veneers treated with 10% NMM-1, 5% mNMM-2 (catalyst RB) or 1% AKD was stable after the extraction with water and organic solvents. For these chemicals, curing at 130°C brought better results of WREs. 3.4. Fixation of the chemicals Figure 7. Weight loss after cyclohexane and ethanol extraction of the control and treated veneers Figure 8. Weight loss after submersion 1 and submersion 2 of the control and treated veneers In this study, the fixation of the chemicals (N-methylol melamine and ADK) in the treated veneers was reflected by different weight losses after cyclohexane and ethanol extraction, water submersion. The weight losses after cyclohexane and ethanol extraction 1 (weight loss 1) of the control and NMM-1 treated veneers showed negative values for all processes. In contrast, the weight loss 1 of mNMM-2 (catalyst RB) and AKD treated veneers was quite high, even more than 50% comparable to their WPGs. There was 0 10 20 30 40 50 60 70 80 90 0 50 100 150 200 250 Water submersion time [min] W R E 1 - A K D [ % ] 130°C, 5 min 160°C, 5 min 0 10 20 30 40 50 60 70 80 90 0 50 100 150 200 250 Water submersion time [min] W R E 2 - A K D [ % ] 130°C, 10 min 160°C, 10 min 0 10 20 30 40 50 60 70 80 90 0 50 100 150 200 250 Water submersion time [min] W R E 3 - A K D [ % ] 130°C, 20 min 160°C, 20 min -3 -2 -1 0 1 2 3 4 5 Pressing time (min) W e ig h t lo s s 1 [ % ] Control 130°C NMM-1 130°C mNMM-2 130°C AKD 130°C Control 160°C NMM-1 160°C mNMM-2 160°C AKD 160°C 5 10 20 -1 0 1 2 3 4 5 10 20 Pressing time (min) W e ig h t lo s s 2 [ % ] Control 130°C NMM-1 130°C mNMM-2 130°C AKD 130°C Control 160°C NMM-1 160°C mNMM-2 160°C AKD 160°C Forest Industry JOURNAL OF FORESTRY SCIENCE AND TECHNOLOGY NO. 2 - 2018 170 insignificant difference of weight loss 1 between the different hot pressing processes of the veneers (Figure 7). Weight loss 2 of the control, NMM-1 and AKD treated veneers were low (less than 1.0%). As compared to the WPG, weight loss 2 of NMM-1 was very small while weight loss 2 of mNMM-2 treated veneers was high (Figure 8). Figure 9. Weight loss after submersion 1, cyclohexane and ethanol extraction, and submersion 3 of the control and treated veneers For the control and NMM-1 treated veneers, weight loss 2 and weight loss 3 were not considerably different, because these veneers did not get weight loss through the extraction with cyclohexan and ethanol. On the contrary, weight loss 3 of mNMM-2 and AKD treated veneers was significantly higher than weight loss 2 (Figure 9). There were no influences of hot pressing time and temperature on weight losses of the control, NMM-1 and AKD treated veneers. Weight losses of mNMM-2 treated veneers were lower at the higher hot pressing temperature (160°C), however, WRE 3 of mNMM-2 treated veneers was higher for the veneers pressed at 130°C. IV. CONCLUSIONS Regardless of the chemical treatments, water repellent effectiveness of the treated veneers after soxhlet with organic solvents and water submersion imparted optimum results for the veneers cured by hot pressing at 5 min and 130°C. The influence of the hot pressing time and temperature on WPG and radial bulking, EMCR and radial swelling, and weight loss after extraction did not showed detrimental effects in case of the veneers cured by hot pressing at 5 min and 130°C in comparison to the other hot pressing processes. Hence, the time of 5 minutes and the temperature of 130°C were selected for curing by hot press of the impregnated veneers. The applied concentrations of the selected chemicals NMM-1 (10% solid content), mNMM-2 (5% solid content, catalyst RB 1.9%), AKD (1% solid content) have been shown to bring about sufficient water repellent effect for the treated veneers. REFERENCES 1. Deka, M. and Saikia, C.N. (2000). Chemical modification of wood with thermosetting resin: effect on dimensional stability and strength property. Bioresource Technology, 73(2): 179-181. 2. Dieste, A., Krause, A., Bollmus, S. and Militz, H. (2009). Gluing ability of plywood produced with DMDHEU-modified veneers of Fagus sp., Betula sp., and Picea sp. International Journal of Adhesion and Adhesives, 29: 206-209. 3. EN 350:2016 Durability of wood and wood- based products - Testing and classification of the durability to biological agents of wood and wood- based materials. 4. Inoue, M., Ogata, S., Nishikawa, M., Otsuka, Y., Kawai, S. and Norimoto, M. (1993). Dimensional stability, mechanical-properties, and color changes of a low-molecular-weight melamine-formaldehyde -1 0 1 2 3 4 5 6 5 10 20 Pressing time (min) W ei g h t lo s s 3 [ % ] Control 130°C NMM-1 130°C mNMM-2 130°C AKD 130°C Control 160°C NMM-1 160°C mNMM-2 160°C AKD 160°C Forest Industry JOURNAL OF FORESTRY SCIENCE AND TECHNOLOGY NO. 2 - 2018 171 resin impregnated wood. Mokuzai Gakkaishi, 39(2): 181-189. 5. Pittman, C.U., Kim, M.G., Nicholas, D.D., Wang, L.C., Kabir, F.R.A., Schultz, T.P. and Ingram, L.L. (1994). Wood enhancement treatments 1. Impregnation of Southern yellow pine with melamine- formaldehyde and melamine-ammeline-formaldehyde resins. Journal of Wood Chemistry and Technology, 14(4): 577-603. 6. Trinh Hien Mai (2016). Effect of veneer curing process on bonding quality of modified plywood. Journal of Forest Science and Technology, Vietnam National University of Forestry, ISSN 1859-3828, Volume 3, 2016. 7. Trinh Hien Mai, Nguyen Minh Hung (2017). Water uptake, moisture absorption and wettability of Beech veneer treated with N-methylol melamine compounds and alkyl ketene dimer. Journal of Forest Science and Technology, Vietnam National University of Forestry, ISSN 1859-3828, Volume 5, 2017. 8. Wepner and Militz (2005). Fungal resistance, dimensional stability and accelerated weathering performance of N-methylol treated veneers of Fagus sylvatica. Proceeding of the second European conference on wood modification. 9. Wepner, F., Krause, A. and Militz, H. (2007). Weather resistance of N-methylol treated plywood panels. Proceedings of the 2nd International Symposium on the Veneer Processing and Products, Vancouver, B.C, Canada, 305-314. ẢNH HƯỞNG CỦA THÔNG SỐ CHẾ ĐỘ XỬ LÝ NHIỆT ĐẾN SỰ CỐ ĐỊNH LẠI CỦA HÓA CHẤT VÀ KHẢ NĂNG CHỐNG HÚT NƯỚC CỦA VÁN MỎNG GỖ BEECH BIẾN TÍNH Trịnh Hiền Mai Trường Đại học Lâm nghiệp TÓM TẮT Trong nghiên cứu này, ván mỏng lạng từ gỗ Beech (Fagus sylvatica. L) với kích thước 37 × 0.5 × 50 mm3 (XT × TT × DT) đã được lọc rửa qua thiết bị soxhlet bằng nước nóng và các dung môi hữu cơ (cyclohexan và ethanol, tỷ lệ thể tích 2:1), sau đó ván mỏng được sấy khô trước khi ngâm tẩm với các dung dịch hóa chất biến tính. Ba loại hóa chất đã được sử dụng để biến tính ván mỏng là: N-methylol melamine (NMM-1 - sử dụng ở hàm lượng rắn 10%), fatty acid modified N-methylol melamine/paraffin (mNMM-2 - sử dụng ở hàm lượng rắn 5%), alkyl ketene dimer (AKD - sử dụng ở hàm lượng rắn 1%). Ván mỏng sau khi tẩm hóa chất biến tính được hong phơi 2 ngày ở điều kiện phòng rồi xử lý nhiệt (curing) trong máy ép nhiệt với các thông số chế độ ép (nhiệt độ và thời gian) khác nhau. Cụ thể: nhiệt độ: 130°C, 160°C; áp suất: 1 N/mm2; thời gian ép: 5, 10, 20 phút. Kết quả nghiên cứu cho thấy: thời gian ép 5 phút và nhiệt độ ép 130°C không gây ảnh hưởng xấu đến tỷ lệ tăng khối lượng (WPG) và tỷ lệ tăng kích thước chiều tiếp tuyến (RBE), độ ẩm thăng bằng (EMCR) và tỷ lệ trương nở chiều tiếp tuyến (RS) (trong môi trường 20°C, độ ẩm 65%), và tỷ lệ tổn hao khối lượng (WL). Bên cạnh đó, khả năng chống hút nước của ván mỏng biến tính sau khi bị lọc rửa qua thiết bị soxhlet với các dung môi hữu cơ và các lần ngâm nước cho kết quả tốt nhất trong trường hợp ván mỏng được xử lý nhiệt ở chế độ: thời gian ép 5 phút và nhiệt độ ép 130°C. Hơn thế nữa, giảm thời gian và nhiệt độ của quá trình xử lý nhiệt trong máy ép nhiệt có thể ngăn chặn được hiện tượng “sấy quá” của ván mỏng trước khi tráng keo để sản xuất ván dán. Do đó, thời gian ép 5 phút và nhiệt độ ép 130°C đã được lựa chọn để xử lý nhiệt ván mỏng trong máy ép nhiệt. Ảnh hưởng của thông số chế độ xử lý nhiệt (bằng máy ép nhiệt) đến các tính chất của ván mỏng biến tính với mỗi loại hóa chất đã được thảo luận chi tiết trong bài báo. Từ khóa: Alkyl ketene dimer, độ ẩm thăng bằng, khả năng chống hút nước, N-methylol melamine, sự cố định lại của hóa chất, ván mỏng gỗ beech (Fagus sylvatica. L). Received : 26/01/2018 Revised : 30/3/2018 Accepted : 05/4/2018
File đính kèm:
influence_of_curing_parameters_on_chemical_fixation_and_wate.pdf