Hướng dẫn Đồ án công nghệ chế tạo máy - Chương 6: Thiết kế đồ gá - Nguyễn Quang Tuyến
CHƯƠNG 6
THIẾT KẾ ĐỔ GÁ
Trình tự thiết kế đổ gá
Xác lập sơ đổ gá đặt
Lựa chọn các chi tiết gá đạt tiêu chuẩn, các cơ cấu dẫn huớng và so dao
Tính lực cắt và mômen cắt gọt
Tính lực kẹp cần thiết
Kiểm tra độ bền của cơ cấu sinh lực kẹp. (tính bu lông hoặc đai ốc)
Xác định kết cấu các bộ phận khác trên đổ gá
Tính sai số gá đặt đổ gá
Bạn đang xem 20 trang mẫu của tài liệu "Hướng dẫn Đồ án công nghệ chế tạo máy - Chương 6: Thiết kế đồ gá - Nguyễn Quang Tuyến", để tải tài liệu gốc về máy hãy click vào nút Download ở trên
Tóm tắt nội dung tài liệu: Hướng dẫn Đồ án công nghệ chế tạo máy - Chương 6: Thiết kế đồ gá - Nguyễn Quang Tuyến
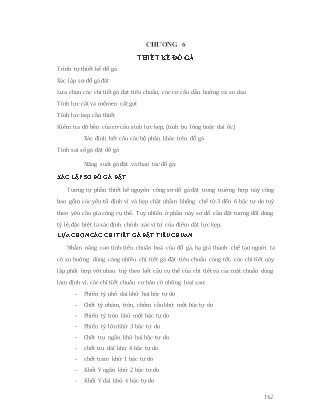
CHƯƠNG 6 THIẾT KẾ ĐỔ GÁ Trình tự thiết kế đổ gá Xác lập sơ đổ gá đặt Lựa chọn các chi tiết gá đạt tiêu chuẩn, các cơ cấu dẫn huớng và so dao Tính lực cắt và mômen cắt gọt Tính lực kẹp cần thiết Kiểm tra độ bền của cơ cấu sinh lực kẹp. (tính bu lông hoặc đai ốc) Xác định kết cấu các bộ phận khác trên đổ gá Tính sai số gá đặt đổ gá Năng suất gá đặt và thao tác đổ gá: XÁC LẬP SƠ ĐỔ GÁ ĐẶT Tuơng tự phần thiết kế nguyên công sơ dổ gá đặt trong truờng hợp này cũng bao gổm các yếu tố định vị và kẹp chặt nhằm khống chế từ 3 đến 6 bậc tự do tuỳ theo yêu cầu gia công cụ thể. Tuy nhiên ở phần này sơ đổ cần đặt tuơng đối đúng tỷ lệ, đặc biệt là xác định chính xác vị trí của điểm dặt lực kẹp. LỰA CHỌN CÁC CHI TIẾT GÁ ĐẶT TIÊU CHUAN Nhằm nâng cao tính tiêu chuẩn hoá của đổ gá, hạ giá thành chế tạo nguời ta có xu huớng dùng càng nhiều chi tiết gá đặt tiêu chuẩn càng tốt. các chi tiết này lắp phối hợp với nhau tuỳ theo kết cấu cụ thể của chi tiết và các mặt chuẩn dùng làm định vị. các chi tiết chuẩn cơ bản có những loại sau: Phiến tỳ nhỏ dài khử hai bậc tự do Chốt tỳ nhám, tròn, chỏm cầu khử một bậc tự do Phiến tỳ tròn khử một bậc tự do Phiến tỳ lớn khử 3 bậc tự do Chốt trụ ngắn khử hai bậc tự do chốt trụ dài khử 4 bậc tự do chốt trám khử 1 bậc tự do Khối V ngắn khử 2 bậc tự do Khối V dài khử 4 bậc tự do Khối V động khử một bậc tự do Các phối hợp thường gặp: Hai phiêh tỳ dài khử 3 bậc tự do Ba chốt tỳ tròn khử 3 bậc tự do Hai khối V ngắn khử 4 bậc tự do Để khử đủ 6 bậc tự do ta thường có các phối hợp sau: Mặt phẳng + Chốt trụ ngắn + chốt trám Mặt phẳng + phiên tỳ nhỏ dài + chốt nhám,tròn hoặc chỏm cầu Mặt phẳng + Khối V ngắn + khối V động Mặt phẳng nhỏ + Khối V hoặc trụ dài + chốt trám Mặt phẳng + khối V hoặc trụ ngắn + chốt trám Trong thực tê nhiều nguyên công chỉ cần khử 5 bậc tự do khi đó ta có các phối hợp sau của các chi tiêt định vị chuẩn: Khối V hoặc khối trụ dài + mặt phẳng nhỏ Hai khối V ngắn + mặt phẳng nhỏ Mặt phẳng lớn + mặt phẳng nhỏ Mặt phẳng kêt hợp với các loại chốt Việc lựa chọn các chi tiêt chuẩn cơ bản phải tuân kêt cấu cụ thể của chi tiêt cần gia công và các quy tắc chọn chuẩn trong công nghệ. Ngoài ra còn phải tính đên các yêu tố dễ thao tác, dễ chê tạo và giá thành của đổ gá cụ thể như sau: Đảm bảo chọn phương án kêt cấu đổ gá hợp lý về kỹ thuật và kinh tê, sử dụng các kêt cấu tiêu chuẩn; để đảm bảo điều kiện sử dụng tối ưu nhằm đạt được chất lượng nguyên công một cách kinh tê nhất trên cơ sở kêt cấu và tính năng của máy cắt sẽ lắp đổ gá. Đảm bảo các yêu cầu về an toàn kỹ thuật, đặc biệt là kỹ thuật thao tác và thoát phoi khi sử dụng đổ gá. Tận dụng các loại kết cấu đã đuợc tiêu chuẩn hoá. Đảm bảo lắp ráp và điều chỉnh đổ gá trên máy thuận tiện. Đảm bảo kết cấu đổ gá phù hợp với khả năng chế tạo và lắp ráp thực tế của co sở sản xuất. TÍNH Lực CẮT VẢ MÔMEN CẮT GỌT Các lực tác chủ động tác dụng nên đổ gá trong quá trình gia công co gổm: lực cắt và momen cắt gọt. Tuỳ theo so đổ đặt lực cụ thể mà một trong hai hay cả hai yếu tố trên là nguyên nhân chủ yếu ảnh huởng đên độ bền và kết cấu đổ gá. Vì vậy việc đầu tiên phải làm là tính giá trị lực cắt và mômen cắt với mỗi so đổ gá đặt và gia công cụ thể. Lực cắt và momen cắt gọt ứng với mỗi một phuong pháp gia công đuợc tính nhu trong phần chọn chế độ cắt. Xác định phuong, chiều và điểm đặt của lực cắt, mômen cắt. Để xác định giá trị cần thiết của lực kẹp chặt phôi trên đổ gá và bố trí đặt điểm của lực kẹp chặt phôi, lực cắt thuờng chọn xác định ở vị trí bắt đầu quá trình gia công. TÍNH Lực KẸP CAN THIÊT xác định trị số cuả lực kẹp Trị số cần thiết của lực kẹp chặt phôi trên đổ gá phải đảm bảo sao cho phôi cân bằng ổn định, không bị xê dịch trong suốt quá trình gia công duới tác dụng của ngoại lực, trong đó chủ yếu là lực cắt, mômen cắt, trọng luợng bản thân phôi và các lực loại hai sinh ra trong quá trình gia công. Nghĩa là có thể xác định đuợc lực kẹp gần đúng bằng cách giải bài toán cân bằng tĩnh tùy theo so đổ gá đặt cụ thể với các quan hệ. Đổ án chỉ giới hạn việc tính toán kiểm tra lực kệp cuả co cấu ren vít cho phù hợp với chuong trình đào taọ. Khi gá đặt chi tiết trên máy duới tác dụng cuả các lực cắt gọt và moment cắt gọt tuỳ theo số bạc tự do bị hạn chế mà có thể xảy ra các hiện tượng sau: Nếu số bậc tự do bị hạn chế là 3 hay 4 chi tiết có thể bị trượt hoặc bị quay hay cả hai. Trong trường hợp này lực kệp phải thoả mãn công thức: Khi chi tiết có xu hướng trượt W. f > Px .k W > ĩỷ f Khi chi tiết có xu hướng quay quanh một tâm: M„ .k > M, = W.f .R Trong đó w - Lực kẹp chặt phôi cần thiết . f - Hệ số ma sát giữa mặt chuẩn định vị và mặt làm việc của đổ định vị. K - Hệ số xét đến yêu cầu đảm bảo an toàn khi gia công. K = k0. ki .k2 .k3 .k4 .k5 .k6 ko : hệ số an toàn trong mọi tường hợp ko =1,5 kx: hệ số kể đến lượng dư không đều k2 : hệ số kể đến dao cùn làm lực cắt tăng k3: hệ số kể đến lực cắt không liên tục làm lực cắt tăng k3=1 k4: hệ số kể đến nguổn sinh lực không ổn định k5: hệ số kể đến sự thuận tiện của vị trí tay quay của co cấu kẹp chặt Mc - Mômen cắt. Pc _ Lực cắt. R là bán kính tay đòn lực kẹp Trong trường hợp chi tiết có cả hai xu hướng chuyển động trên thì lục kẹp tổng hợp sẽ bằng tổng lực kẹp lớn nhất xác định theo một trong hai công thức trên. Với những chi tiết khử đủ 6 bậc tự do không một chuyển động nào có thể xảy ra, thông thường lực kẹp được tính theo khả năng lật chi tiết quanh một tâm nào đó. Trong trường hợp này có thể tính theo công thức: M = W. f .l > k.Ml = pl .h hoặc M cl = W.l > k.Mi = Pl .h Trong đó: Mcl moment chống lật chi tiết quay quanh tâm nào đó. Công thức một dùng cho trường hợp momen chống lật là do lực ma sát sinh ra bởi lực kẹp. Công thức hai sử dụng khi lực kẹp chính là nguyên nhân chống lật. M là moment gây lật do lực cắt hay một thành phần naò đó cuả lực cắt gây ra Giá trị của lực cắt Pc và mômen cắt Mc được xác định theo các công thức cụ thể tuỳ theo phương pháp gia công, đã được trình bày trong các giáo trình nguyên lý cắt kim loại. Lực kẹp phải có giá trị vừa đủ, có phương chiều và đặt điểm hợp lý. Lực kẹp không quá lớn làm cho cơ cấu kẹp cổng kềnh và gây biến dạng cho chi tiết. Phương, chiều của lực kẹp chặt phôi phụ thuộc vào vị trí mặt chuẩn định vị chính, phụ thuộc chiều của lực cắt và chiều của trọng lượng bản thân phôi. Phương của lực kẹp chặt phôi nên vuông góc với mặt chuẩn định vị chính để có diện tích tiếp xúc lớn nhất, giảm áp lực và giảm biến dạng của phôi khi kẹp chặt. Chiều của lực kẹp chặt phôi nên hướng từ ngoài vào mặt chuẩn định vị, cùng chiều với lực cắt và trọng lượng của phôi để có lợi về lực và cơ cấu kẹp có kết cấu nhỏ gọn; cũng có thể chọn phương, chiều của lực kẹp vuông góc với lực cắt và trọng lưọng phôi. Điểm đặt của lực kẹp chặt phôi phải ở vào vị trí sao cho độ cứng vững của phôi và đổ gá lớn nhất để phôi khỏi bị biến dạng khi kẹp chặt cũng như khi gia công. Điểm đặt của lực kẹp phải nằm trong đa giác chân đế được tạo nên do các diểm tiếp xúc của mặt chuẩn định vị chính với mặt làm việc của các đổ định vị và nên gần mặt gia công để không gây ra mômen làm lật phôi. Chọn cơ cấu kẹp chặt phôi Cơ cấu kẹp chặt phôi được chọn phải thoả mãn các yêu cầu cơ bản đã nêu ở phần trên nghĩa là khi kẹp chặt phải giữ đúng vị trí của phôi, tạo ra đủ lực kẹp, không làm biến dạng phôi, kết cấu đơn giản, nhỏ gọn, không gây ra biến dạng, có tính tự hãm tốt, phù hợp với phương pháp gia công, thao tác nhẹ nhàng, thuận lợi, an toàn, đơn giản, dễ bảo quản, an toàn. Với cấc máy vạn năng cơ cấu kẹp châựt được lưạ chọ thường là: Ê tô Khối V động Mỏ kẹp (đơn hoặc liên động) Vít tỳ, Bu lông tỳ trực tiếp Chọn cơ cấu sinh lực Để giảm bớt nặng nhọc cho công nhân trực tiếp sản xuất, trong đổ gá có thể dùng nhiều loại cơ cấu sinh lực khác nhau để tác dụng vào cơ cấu kẹp như cơ cấu sinh lực bằng dầu ép, khí nén... Mỗi loại cơ cấu sinh lực có những yêu cầu riêng khi sử dụng, đòi hỏi các trang bị kèm theo làm cho kết cấu chung của đổ gá thêm phức tạp, song ngoài việc giảm nhẹ sức lao động khi thao tác, nó còn tạo ra được lực kẹp lớn và ổn định, tạo điều kiện giảm thời gian gá đặt, nâng cao năng suất gia công. Chọn cơ cấu sinh lực phải căn cứ vào quy mô sản xuất, năng lực sản xuất và các chỉ tiêu kinh tế kỹ thuật cần đạt. Như phần trên đã trình bày do hạn chế cuả chương trình đào tạo nên tài liệu chỉ tập trung hướng dẫn tính kiểm tra cơ cấu sinh lực bằng ren vít. XÁC ĐỊNH KẾT CAU CỦA CÁC BỘ PHẬN KHÁC TRÊN Đổ GÁ: Chọn cơ cấu dẫn hướng và kiểm tra vị trí dụng cụ cắt. Đây là một bộ phận quan trọng của đổ gá, có chức năng xác định trực tiếp vị trí của dụng cụ cắt và tăng độ cứng vững của nó trong quá trình gia công, đảm bảo hướng tiêh dao, giảm sai số gia công, thường dùng trong các nguyên công khoan, doa, khoét, chuốt lỗ... Co cấu kiểm tra vị trí dụng cụ cắt chỉ nhằm xác định (điều chỉnh) vị trí của dụng cụ cắt trước khi gia công và thường được dùng ở các loại đổ gá tiện, phay, bào, xọc, chuốt mặt ngoài... Bạc dẫn hướng khoan. Khi gia công lỗ dẫn hướng khoan, doa thường sử dụng đổ gá có co cấu dẫn hướng gổm bạc dẫn lắp trên phiên dẫn và phiên dẫn lắp trên đổ gá. Tuỳ theo yêu cầu gia công cụ thể mà có thể dùng các loại bạc dẫn tiêu chuẩn như: bạc dẫn cố định khi bạc chỉ sử dụng qua một bước công nghệ, bạc dẫn thay thế được dùng với phiên dẫn cố định khi lỗ chỉ qua một bước công nghệ, sau mỗi bước phải thay bạc dẫn hướng và dụng cụ cắt, bạc dẫn thay nhanh giống như bạc dẫn thay thế nhưng kết cấu cho phép rút bạc khỏi phiên dẫn nhanh khi thay thê để giảm thời gian nguyên công. Khi gia công trên máy doa, thường dùng bạc quay để chống bị kẹt phôi khi cắt làm lỗ bạc dẫn mòn nhanh. Phiến dẫn khoan có thể là phiên dẫn cố định, phiên dẫn tháo dời, phiên dẫn bản lề, phiên dẫn treo, phiên dẫn trụ trượt thanh răng... Phiên dẫn được chọn tuỳ thuộc vào tính chất nguyên công, yêu cầu về độ chính xác và năng suất gia công. Cơ cấu chép hình được sử dụng để gia công bề mặt phức tạp trên máy phay, bào, tiện, mài.. Trên máy phay, máy tiện co cấu chép hình dựa theo cam mẫu, dưỡng. Nói chung co cấu chép hình có nhiệm vụ xác định vị trí chính xác giữa dụng cụ cắt và phôi đổng thời xác định cả hướng chuyển động của dụng cắt nhằm đảm bảo hình dáng bề mặt theo yêu cầu gia công, giảm bớt thời gian gia công, tăng năng suất gia công. Tuỳ thuộc vào điều kiện gia công và kêt cấu của máy công cụ mà có thể lựa chọn để sử dụng các loại co cấu chép hình khác nhau như co cấu chép hình co khí, chép hình thuỷ lực, điện co hoặc phối hợp khí nén và dầu ép. Cữ so dao được sử dụng trong khi gia công các mặt phẳng cần đẩm bảo kích thước cần thiết về khoảng cách, độ vuông góc hay dô song song. Cữ so dao có thể thực hiện so một kích thước nhưng cũng có thể dùng so nhiều kích thước đổng thời. Chọn cơ cấu phân độ Tuỳ theo yêu cầu gia công, hình thức chuyển động khi phân độ mà chọn co cấu phân độ loại nào, phân độ tịnh tiến hay phân độ quay, có trục quay thẳng đứng hay nằm ngang, quay liên tục hay gián đoạn. Co cấu phân độ quay liên tục dùng để gia công các mặt định hình trên máy công cụ vạn năng, nhằm cung cấp cho quá trình gia công một trong số các chuyển động tạo hình thường dùng để phay rãnh nghiêng, rãnh xoắn trên máy phay đứng. Co cấu phân độ quay gián đoạn dùng để gia công tuần tự nhiều bề mặt giống nhau và có vị trí cách nhau đều đặn trên một chi tiết hoặc trên nhiều chi tiết có kết cấu giống nhau và có bề mặt gia công như nhau. Chọn thân đồ gá. Thân đổ gá phải chọn sao cho đảm bảo đủ chỗ để lắp các bộ phận khác của đổ gá lên nó, đảm bảo độ cứng vững cần thiết, thân đổ gá thường được chế tạo bằng gang, bằng thép có kết cấu hàn bằng một số hợp kim màu nhẹ. Thân đổ gá phải được chế tạo đạt độ chính xác cần thiết và có giá thành hợp lý. XÁC ĐỊNH SAI số CHÊ TẠO Đồ GÁ: Sai số chế tạo cho phép cuả đổ gá được xác định theo yêu cầu của nguyên công, các quy định về điều kiện kỹ thuật chế tạo và lắp ráp đổ gá. Nghĩa là phải xác định các đại lượng sau. * Sai số gá đặt cho phép e < |e gd] = [1 - 2)d egc = sl£ỉ + eK +£2gd = 7eỉ +eK +eỉt +ei +eid ỗ VDd.h + Dd.c + 3D2m + 3D2n + egd + Dh.d Trong đó: ỗ là dung sai cho phép của yêu cầu cần đảm bảo. * Sai số chế tạo đổ gá. Từ các điều kiên trên ta có: ec.t.1 £ vie2dg]-e2 -ek-em -eld Trong đó : ek - Sai số kẹp chặt phôi , trong truờng hợp này lực kẹp vuông góc với phuơng kích thuớc thực hiên ec - Sai số chuẩn do định vị chi tiết gia công Trong truờng hợp chuẩn định vị trùng với chuẩn kích thuớc sai số chuẩn có thể coi bằng không. Các truờng hợp khác có thể tra atlat đổ gá để tìm sai số chuấn theo sơ đổ gá đặt phù hợp. em - Sai số do mòn đổ gá : em = fixJN b = 0,14- 0,5 N - số sản phẩm đuợc gia công trên đổ gá edc - Sai số điều chỉnh VUI. NẢNG SUẤT GÁ ĐẶT VẢ THAO TÁC Đổ GÁ: Nâng cao năng suất gá đặt và hợp lý hoá thao tác đổ gá gia công cắt gọt là một trong những biên pháp chủ yếu nhằm rút ngắn thời gian phụ của nguyên công. Năng suất gá đặt phôi trên đổ gá phụ thuộc vào các yếu tố sau: Trình độ cơ khí hoá và tự động hoá quá trình gá đặt phôi. Số luợng phôi trong một lần gá đặt. Mức độ hợp lý hoá các thao tác và cơ cấu thao tác gá đặt phôi. Các yếu tố trên có liên quan chặt chẽ với dạng sản xuất và đuờng lối công nghê. Khi quy mô sản xuất càng lớn, càng phải xét toàn diên và chính xác hơn ảnh huởng của quá trình gá đặt phôi trên đổ gá cụ thể đối với năng suất gá đặt và năng suất gia công. Để nâng cao năng suất gá đặt phôi, thường dùng các cơ cấu sau: a) Cơ cấu kẹp nhiều phôi: Khi gia công các chi tiết nhỏ, có mặt gia công đơn giản, có thể dùng cơ cấu gá đặt nhiều phôi, gia công nhiều chi tiết đồng thời: - Kẹp chặt liên tục: cách này có lực bằng nhau, truyền từ phôi này sang phôi khác cùng chiều (hình 3.2). _ Kẹp song song: lực kẹp phân bố đều trên nhiều phôi theo cùng một hướng song song nhau, lực kẹp của mỗi phôi nhỏ hơn lực kẹp ban đầu (hình 3.3). _ Kẹp song song ngược chiều: lực kẹp phân bố song song nhưng ngược chiều tác dụng lên hai phôi hoặc hai nhóm phôi (hình 3.4). Hình 3.2 Cơ cấu kẹp có lực kẹp hên tục Hình 3.3 - Cơ cấu kẹp có lực kẹp song song Hình 3.4 Cơ cấu kẹp có lực kẹp song song ngược chiều. - Kẹp nhiều phôi bằng cách tổ hợp cả lực kẹp song song, ngược chiều (hình 3.5). Hình 3.5 Co cấu kẹp tổ hợp b) Cơ cấu kẹp nhanh.: Có nhiều loại co cấu kẹp nhanh như: Co cấu kẹp nhanh bằng tay. (Hình 3.6) Co cấu kẹp nhanh bằng dầu ép. Co cấu kẹp nhanh bằng khí nén. Co cấu kẹp nhanh bằng điện tử. Co cấu kẹp nhanh bằng chân không. Hình 3.6 Co cấu kẹp nhanh bằng tay Cơ cấu kẹp chặt tự động: Loại cơ cấu này đóng vai trò quan trọng trong quá trình tự động hoá quá trình công nghệ gia công cắt gọt. Điều chỉnh quá trình cắt gọt thuờng bằng cam. Cơ cấu sinh lực kẹp trong truờng hợp này có thể bằng lò so, ren ốc, hệ thống đòn kẹp, hệ thống khí nén, hệ thống thuỷ lực v.v... Việc dùng phuơng án nào là tuỳ thuộc vào yêu cầu sản suất đặc biệt là sản luợng, năng suất, cơ sở vật chất kỹ thuật, lực luợng sản xuất v.v... Sau khi sử dụng đổ gá phục vụ cho một chuyên công cần thiết phải thực hiện các thao tác sau đây: Đặt phôi vào và lấy phôi ra khỏi đổ gá. Đóng và mở đổ gá. Lau chùi ... m bảo an toàn khi thao tác, không được có cạnh sắc. Trong thực tế sản xuất đổ gá tiện có thể có các dạng cụ thể sau; _ Đổ gá gia công chi tiết lắp với trục chính của máy tiện, chi tiết gia công có chuyển động quay cùng trục chính của máy tiện, dụng cụ cắt có chuyển động tịnh tiến cùng bàn dao, ví dụ như mâm cặp, mũi tâm là các loại đổ gá tiện vạn năng trang bị theo máy tiện. _ Đổ gá gia công chi tiết lắp trên sống trượt của băng máy tiện, chi tiết gia công có chuyển động tịnh tiến cùng bàn dao, còn dụng cụ cắt lắp trên trục chính và có chuyển động quay tròn cùng với trục chính của máy tiện. _ Đổ gá gia công chi tiết được gá trên hai mũi tâm của máy tiện, chi tiết gia công có chuyển động quay cùng với trục chính của máy tiện như các loại trục gá. Kết cấu cụ thể của các loại đổ gá tiện thường có các bộ phận: _ Đổ gá gia công chi tiết lắp trên trục chính của máy tiện thường bao gổm các bộ phận: cơ cấu định vị phôi, cơ cấu kẹp chặt phôi, thân đổ gá, bộ phận định vị và kẹp chặt đổ gá trên trục chính của máy tiện, cơ cấu phân độ. _ Đổ gá gia công chi tiết lắp trên sống trượt của băng máy tiện gổm các bộ phận: Cơ cấu định vị phôi, cơ cấu kẹp chặt phôi, thân đổ gá, bộ phận định vị và kẹp chặt đổ gá trên băng máy tiện, cơ cấu phân độ. XI Ví dụ THIẾT KÊ ĐỔ GÁ NGUYÊN CÔNG KHOAN RỘNG Lỗ f 32) Sơ đồ gá đàt : Việc gia công lỗ f32 ngoài việc phải đảm bảo độ bóng và kích thước lỗ thì ta còn cần phải đảm bảo khoảng cách R 9O60’05 và góc lệch 3O0 61’ so với lỗ & 25 và phải vuông góc với các mặt phẳng đáy định vị . Vì thế ta định vị chi tiết bằng 1 phiến tỳ phẳng khống chế 3 bậc tự do , dùng 1 chốt trụ ngắn vào lỗ & 25 khống chế 2 bậc tự do và 1 chốt trám vào lỗ f11 thông 2 vách khống chế nốt bậc tự do xoay quanh chốt trụ ngắn của chi tiết . Lưa chon chi tiết gá đăt tiêu chuẩn Vì chi tiết có hình ndạng và kích thước tưong đối phức tạp do đó ta lưạ chọn các chi tiết định vị sau: Một phiến tỳ lớn dùng định vị mặt đáy phiến tỳ này bắt chặt với bề mặt đổ gá Một chốt trụ ngắn đóng trực tiếp lên mặt phẳng gá, vuông góc với mặt phẳng phiến tỳ Một chốt trám vuông góc với mặt phẳng gá và có trục đối xứng lớn vuông góc với đường nối tâm cuả hai lỗ 32 và 25. Tất cả các chi tiết này đều được chế taọ theo kích thước cuả chi tiết nên không thể coi là các chi tiêts tiêu chuẩn, Xác đinh lưc cắt Chon máy : Máy Khoan đứng K135 có đường kính lỗ khoan lớn nhất là : 35 (mm) khoảng cách từ trục chính tới bàn máy : 700 4 1120 (mm) Lỗ Côn Moóc số 4 Kích thước bàn máy là 810 4 1240 (mm) công suất máy là : NMax = NĐC X h = 6 X 0,8 = 4,8 (kw) Chon Dao : Mũi khoan ruột gà lưỡi cắt thép gió đuôi côn loại ngắn có: d = 31,6 (mm) L = 150 (mm) l = 60 (mm) Chế đô cắt: Chiều sâu cắt : t = 1,8 (mm) Lượng chạy dao : s = 0,65 (mm/vòng -Vận tốc cắt: CV XDq Tm Xtx XSy X Kv tra bảng 5 -29 ta có : Cv q X 23,4 0,25 0,1 Tuổi thọ trung bình của dao cắt : T = 105 (phút) hẹ số Kv = Kmv x k>v x Klv = 1 y m 0,4 0,125 Kmv 190 3 HB ) có HB = 190 Kưv Klv => => => Kmv = 1 = 1 ( bảng 5-6) = 1 ( bảng 5-31) T7 23,4 X 31,60’25 ... V = ^0m 01“ , - 4 X1»34,7 (m/ph) 1050’125 X1,80,1 X0,650’4 1000 X V 1000 X 34,7 n = " = " _—»349,7 (v/ph) p X D 3,14 X 31.6 chọn n theo máy n = 298 (v/ph) T, 298 X 3,14 X 31,6 , ... => Vtt = - = 29,6 (m/ph) Phương , chiều , điểm đăt , momen xoắn và lưc kep: Khi khoan mũi khoan có xu huớng tác dụng vào chi tiết một momen xoắn Mx và một lực cắt P0 huớng từ trên xuống . Để chống lại ảnh huởng của momen xoắn tới yêu cầu kỹ thuật của chi tiết ta phải có một momen ma sát cân bằng với momen xoắn. Vậy ta phải tạo ra một lực cũng có chiều từ trên xuống .Ta có thể dùng chính trọng luợng của chi tiết và lực cắt làm lực kẹp chặt chi tiết . Nhung trọng luợng của chi tiết không đáng kể so vói lực cắt m = 2,6 kg .Do đó ta phải tính toàn lực kẹp do lực cắt sinh ra và lực kẹp của đổ gá tạo ra : Ta có sơ đổ tính lực : Tính toán lưc cắt: Lực cắt của ta gổm 2 thành phần : Mx và lực chiều trục P0 + Mô men Xoắn : theo ST CNCTM II ta có : MX = 10 X CM X Dq X tX X Sy X Kp tra bảng 5 -32 : CM X y q 0,085 0,75 0,8 - tra bảng 5 - 9 : Kp = 0,6 => MX = 10 X 0,085 X 31,60 X 1,80,75 X 0,650,8 X 0, 6 = 17,8 (Nm) + Lực cắt : p0 = 10 X Cp X Dq X tX X Sy X Kp tra bảng 5- 32 : Cp X y q 23,5 1,2 0,4 - => P0 = 10 X 23,5 X 1,81,2 X 0,650,4 X 0,6 = 240 (N) Tính lưc kep : Điều kiện để có sự cân bằng về momen : Mx < K [Mms] ta có : Mms = f . R . ( w | P0 ) trong đó : Mx - Mômen xoắn w - Lực kep f - Hệ số ma sát : f = 0,1 Ạ 0,15 ta chọn f = 0,15 R - khoảng cách từ tâm lực kep đêh tâm mũi khoan R = 50 (mm) K - Hệ số an toàn : K = K0 . K1 . K2 . K3 . K4 . K5 . K6 K0 - Hệ số an toàn trong mọi trường hợp lấy K0 = 1,5 K - Hệ số an toàn tính đên trường hợp tăng lực cắt khi độ nhẵn bóng thay đổi ( lượng dư không đều ) K = 1,2 K2 - Hệ số tăng lực cắt khi dao mòn K2 = 1,2 K3 - Hệ số kể đên lực cắt không liên tục K3 = 1,2 K4 - Hệ số kể đên sai số của cơ cấu kep chặt K4 = 1,3 K5 - Hệ số kể đên mức độ kep thuận lợi K5 = 1 K6 - Hệ số kể đên momen làm quay trên các phiên tỳ K6 = 1 => K = 1,5 X 1,2 X 1,2 X 1,2 X 1,3 X 1 X 1 » 3,4 K XMX 3,4 X 17,8.103 Vậy ta có : W = / J - P0 = _ 240 » 7866 (N) f X R 0 0,15 X 50 Ớ nguyên công này ta sử dụng mỏ kep liên động với 2 mỏ kep 2 phía với tổng lực kep 2 phía là w = 7866 (N) => Lực kep do 1 mỏ kep tạo ra là : w1 = w2 = W = 78,66 = 3393 (N) Kiểm tra độ bền cuả cơ cấu sinh lực : Dùng cơ cấu kep liênđộng đơn giản , kep chặt bằng mối ghép ren , Lực kep hướng từ trên xuống thông qua mỏ kep Từ sơ đổ cơ cấu kẹp chặt ta có phương trình cân bằng của 1 phía mỏ kẹp : w ( L1 +L2 ) = Q X L2 ta có : L1 = 55 (mm) L2 = 43 (mm) => Q = 3933 X (55 + 43) » 8964 (N) 43 tra bảng : Q = 8964 (N) ứng với bu lông M16 L1 L) Lưa chon các thành phần khác cuả cơ cấu: Ta dùng phiến dẫn cố định với thân đổ gá bằng bulông , chốt định vị . Bạc dẫn hướng là loại bạc thay nhanh và có một bạc lót cố định cho bạc thay nhanh Có rãnh chữ u trên thân đổ gá và cố định đổ gá với bàn máy bằng Bulông , đai ốc . dác đỉnh các sai số trong chế tao đồ gá : Sai số gá đặt : e — / + e +_e2'+_e^ + e 2 £ [egd 1 = I — — — I ° egd = V ec + ek + em + ect + edc £ ega 1 = I 5 • 2 I ° lây \ẹgd ] — 3 3 S e — /\p ]2 \p2 I e2 I e I e ] Suy ra ect — Vegd ] - \ecc +ek + em + edc ] trong đó : £k - Sai số kẹp chặt phôi , trong trường hợp này lực kẹp vuông góc với phương kích thước thực hiện => £k = 0 £c - Sai số chuẩn do định vị chi tiết gia công Ta có sai số chuẩn £c = Ama; = ES - ei c ma; ES - Sai số trên của lỗ định vị f 25H6 = f 25|0,013 => ES = 0,013 (mm) ei - Sai số dưới của chốt định vị f 25h5 = f25.0 009 => ei = - 0,009 => £c = Amax = ES - ei = 0,022 (mm) = 22 (pm) £m - Sai số do mòn đổ gá : £m = /3xJn b = 0,1^ 0,5 ( ta sử dụng chốt định vị ) => chọn = 0,3 N - số sản phẩm được gia công trên đổ gá = 5.000 (chiếc) => £m = 0,3x75.000 - 21 (mm) — 0,021 (mm) £dc - Sai số điều chỉnh Lây £dc = 8 (mm) £gd - Sai số gá đXt \e] — 3 d d - Dung sai nguyên công là dung sai của khoảng cách từ tâm lố định vị tới tâm lỗ gia công : R9060,05 (mm) => ỗ = 0,1 (mm) => £gd = 3 X 0,1 — 0,33 (mm) — 33 (mm) => Sai số chế tạo : £a ^/\33]2 - \222 + 0 + 212 + 82 ] — 0,01 (mm) Yêu cầu kỹ thuât cùa đồ gá : Từ sai số chế tạo trên ta có các yêu cầu kỹ thuật của đổ gá : Độ không song song giữa mặt định vị với đáy đổ gá [ 0,01 (mm) Độ không vuông góc giữa mặt phẳng định vị với tâm chốt định vị [ 0,01 (mm) Độ không song song giữa 2 chốt định vị [ 0,01(mm) Kích thước , góc độ của chốt tru ngắn với tâm lỗ gia công được xác định với sai số cho phép [ 0,01 (mm) Tâm bạc dẫn hướng phải đảm bảo trùng với tâm lỗ gia công cũng với sai số cho phép [ 0,01 (mm) . Tính toán thiết kế đồ gá khoan hai lỗ 020 1. Sơ đồ gá đăt Chi tiết được khống chế 6 bậc tự do: +) Sử dụng 2 phiến tỳ khống chế được 3 bậc tự do +) 1 chốt ngắn khống chế 2 bậc tự do , +) 1 chốt trám khống chế 1 bậc tợ do. 2- Lưa cho các chi tiết cấu tao đồ gá: -thân-đế đổ gá đúc bằng gang -một chốt trụ ngắn -một chốt trám -một phiến tỳ phẳng -một bu lông kẹp chặt -hai phiến giữ -một phiến bắt bu lông -một má kẹp 3. Tính lưc cắt got Chọn máy: Máy khoan cần 2A55. Công suất động co Nđc = 4.5 KW Hiệu suất h = 0.8. Số cấp tốc độ : 12. Phạm vi tốc độ 42 Ạ 200 v/phút. Chọn dao: Sử dụng mũi khoan ruột gà, chuôi trụ, thép gió: + mũi khoan 020d=20mm k=56 + 254 mm, 1 = 33 + 166 mm Po = 10.Cp.Dq.Sy,Kp Tra bảng 5_23 StCnIIcó: Cp =42,7 k q =1k y = 0,8 => Po =10.42,7.201.0.530' Tính lưc key: - Vì lực kẹp vuông góc với lực cắt Po và mặt chuẩn chính nên ta có công thức: w.h > Po.1.k => w= P o h Trong đó: * -Po:1ực cắt(1ực chiều trục) *-1: khoảng cách từ tâm mũi khoan đêh điểm lật 1 = 80mm *-h: khoảng cách từ tâm má kẹp đên điểm 1ật h = 100mm *-k: hệ số an toàn k =k 0. k1 .k2 .k3 .k4 .k5 .k6 ko : hệ số an toàn trong mọi tuờng hợp ko =1,5 k1: hệ số kể dên 1uợng du không đều kx=1 k2: hệ số kể đên dao cùn1àm 1ực cắt tăng k2=1,2 k3: hệ số kể đên 1ực cắt không 1iên tục 1àm 1ực cắt tăng k3=1 .1=5138(N) k4: hệ số kể đêh nguồn sinh lực không ổn định k4=l,3 (vì kẹp bằng tay) k5: hệ số kể đên sự thuận tiện của vị trí tay quay của cơ cấu kẹp chặt k5=l,2 k6:hệ số tính đén mô men làm lật phôi quanh điểm tựa k6=l,5 K = l,5.l.l,2.l.l,3.l,2.l,5 =4,2 5138.80.4,2 lực kẹp w = — = 17263 N — 100 5. Kiểm tra đô bền cuả cơ cấu sinh ỉưc: Sử dụng cơ cấu kẹp ren vít. (7.2) đường kính của bu lông kep chặt : W , . 117263 d=C^ J—- = 1.4 J " = 20 mm M V 90 C=l.4 vì đây là ren hệ mét W:lực kẹp yêu cầu d :ứng suất kéo ,nén=(80^l00)N 6- tỉnh sai số chế tao: -vì chuẩn định vị trùng với gốc kích thước nên ta có £c=0 -vì lực kẹp có phương vuông góc với phương kích thước thực hiện nên ta có: e k =0 -sai số mòn: em= N:số lượng phôi được định vị trrog thời gian giữa 2 lần điều chỉnh cơ cấu của đổ gá N=1000 b :hẹ số phụ thuộc kết cấu định vị và điều kiện tiếp xúc với mặt phẳng chuẩn (bảng 62 trang 190 sách tính và thiết kế đổ gá):chọn b=0,2 => e m= =0,2. V1000 = 6,3ụm = 0,0063mm 1 0.037 -sai số gá đặt: egđ=3 d@= 3 = 0,0123 N dl:dung sai kích thước gia công -sai số điều chỉnh: eđc=10 Ụm =0,01mm -sai số đổ gá: e đg = y (k. .^2 - - e 2.. 1 ^/(0-01232 - 0 - 0) = 0.0123mm e ct=7e - em - e 1 ^/(0.01232 - 0.00632 - 0.0121 = 0.003 mm 7 -điều kiên k, thuât: +độ không song song và sai kích thước khoảng cách giữa hai lỗ của bạc dẫn<0.003mm +độ khôngvuông góc giữa các mặt phẳng của phiến tỳ và tâm lỗ với mặt B <0.003mm +độ không song song của tâm trục vít với mặt phẳng B <0.003mm tỉnh năng kĩ thuât: -khả năng địng vị và kẹp chặt tốt -độ cứng vững cao -năng suất cao,các thao tác của người thợ ít và đơn giản -đổ gá chế tạo đơn giản vì các chi tiết chủ yếu là theo tiêu chuẩn Tính toán và thiết kế đổ gá phay 2 mặt bên 1/ Sơ đồ gá đặt chỉ tiết a/ Định vị : Mặt đáy của chi tiết được định vị bằng 2 phiến tì sẽ khống chế 3 bậc tự do Mặt bên của 2 tai được định vị bằng 1 chốt trụ ngắn khống chế 2 bậc tự do và một chốt trám khống ché 1 bậc tự do. b/ Kẹp chặt : dùng cơ cấu mỏ kẹp liên động . 2) Tính lực cắt và moment cắt Chọn máy : Sử dụng máy phay nằm ngang 6H82 : Công suất động cơ : Nđc =7 kw . Hiệu suất : h= 0,75 . Số cấp tốc độ : 18 . Phạm vi : 30^1500 . Mặt làm việc : 320x1250 . Lực cắt lớn nhất Pmax=1500kg chọn dao : Sử dụng dao phay mặt đầu BK8. D =125 mm k d =40 mm k B =55 mm k Số răng z =8 răng . Tính toán chế độ cắt: Chiều sâu cắt : t = 2mm. Lượng chạy dao : Sz = 0,26 mm/răng . Tốc độ cắt : Số vòng quay của trục chính : _ 1000.V 1000.94 nm = = = 239 v/p . m p.D 3,14.125 Chọn nm=235 v/p Tốc độ cắt thực tế của máy : 125.3,14.235 , = 92 m/p 1000 r vt = Dpnm = 1000 = 0,26.8.235 = 489 mm/p Lượng chạy dao phút : Sph = Sz.Z.n Chọn Sph = 475 mm/p Lực cắt khi phay : Pz = 10 C .txS’.Bu Z K Pz = D* n mp Trong đó: z -số răng dao phay n-số vòng quay của dao KMp - hệ số điều chỉnh chất lượng của vật liệu gia công ( tra bảng 5- 9.STCNII) có KMp = 015 Cp và các số mũ tra bảng5-41 STCNII: Cp X y u w q 54,5 0,9 0,74 1 0 1 = > P = 10.54,5.20’9.0,260’74.55.8 z 125.2350.0,55 1 ' Các thành phần lực khác: + lực hướng kính:Py = (0,2-0,4).Pz = 0,3.1704 = 511 N +lực chạy dao : Ps = (0,3- 0,4).1704 = 0,35.1704 = 596 N +lực vuông góc với lực chạy dao :Pr = (0.85-0.9).1704 = 0,9.1704 = 1534 N Kiểm tra cơ cấu kẹp chặt: Tính lực kẹp : Vì lực kẹp w vuông góc với lực cắt Pz và mặt phẳng chuẩn (tính cho 1 mỏ kẹp ): K.P - Pr w = /1 + /2 2 Hệ số an toàn: k k=k0. k1 ±2 ±3 ±4 .k5 .k ko :hệ số an toàn trong mọi tường hợp ko =1,5 kphệ số kể dêh lượng dư không đều kx=1,2 k2 :hệ số kể đên dao cùnlàm lực cắt tăng k2=1,5 k3: hệ số kể đên lực cắt không liên tục làm lực cắt tăng k3=1,2 k4:hệ số kể đên nguồn sinh lực ổn định k4=1 k5:hệ số kể đên sự thuận tiện của vị trí tay quay của co cấu kẹp chặtk5=1 k6:hệ số tính đén mô men làm lật phôi quanh điểm tựa k6=1 => k= 1,5 . 1,2.1,5 .1,2.1 .1 . 1 = 3,2 f1 : hệ số ma sát giữa mỏ kẹp và chi tiết . = 0,15 f2 : hệ số ma sát giữa mặt chuẩn của chi tiêt và đồ định vị . f2 = 0,15 Pr : thành phần lực vuông góc với lực Pz (cùng chiều với lực kẹp ) . pr= 1534N 3.2.1704 3,2,Ị. -1534 Vậy ta có lực kẹp là : w = —0,3 2 = 8321 N . Tính đường kính bu lông kẹp chặt : . /8321 d = 8 . = .1,4.4--— = 14.2 mm . chọn d = 16 mm V õ ’ Ạ| 80 v Trong đó : w - lực kẹp yêu cầu d - ứng suất kéo nén . d = 80^100 N/mm c = 1,4 với ren hệ mét Mô men kẹp : M = o,1.d.w Trong đó : d- đường kính bu lông w - lực kẹp tác dụng nên chi tiết . => M = 0,1. 16.8321 =13314 (N.m) Lưạ chọn các chi tiết khác cuả đồ gá : Đế và thân đổ gá được đúc bằng gang . Hai chốt định vị . Hai phiến tì phẳng . Hai bu lông . Hai đòn kẹp , chốt tì điều chỉnh . Vòng đệm . Then dẫn hướng . Yêu cầu kỹ thuật của đổ gá Thân của đổ gá phải có độ cứng vững và độ bền . Kết cấu hợp lí, thuận tiện cho việc làm sạch phoi . Tháo và gá phôi dễ dàng, nhanh chóng . Dễ chế tạo, làm việc an toàn và tin cậy . Các phiến tì phải đổng phẳng . Các mối ghép phải chắc chắn . Tỉnh saỉ số đồ gá Tính sai số chế tạo: ek -vì chuẩn định vị trùng với gốc kích thuớc nên ta có e c=0 -vì lực kẹp có phuong vuông góc với phuong kích thuớc thực hiện nên ta có: =0 -sai số mòn: em= bN N: số luợng phôi đuợc định vị trong thời gian giữa 2 lần điều chỉnh co cấu của đổ gá N=1000 Hệ số phụ thuộc kết cấu định vị và điều kiện tiếp xúc với mặt phẳng chuẩn (bảng 62 trang 190 sách tính và thiết kế đổ gá): chọn b= 0,3 => em= bN =0,3. V1000 =9.4ụm=0,0094mm Sai số gá đặt: e gđ= 1.ổ|= 005 = 0,017 mm gđ 3 1 3 ổ @: Dung sai kích thước gia công Sai số điều chỉnh: eđc=10 Ụm =0,01mm Sai số đổ gá: e đg V 12 - e- ) = ^l(ũ.0032 - 0 - o) =0.°03mm -ect=7e -em -e) v(().0l7 2 -0.00942 -0.012) = 0.01 mm 9/ Điều kiện kỹ thuật : Đô không song song giữa mặt phẳng định vị với mặt đáy của đổ gá < 0,01 mm . Đôkhông song song giữa mặt mặt phẳng định vị với tâm chốt < 0,01 mm Đô không phẳng giữa mặt phẳng cữ so dao với mặt phẳng gia công < 0.01 Sai lệch về vị trí tâm chốt < 0.01
File đính kèm:
huong_dan_do_an_cong_nghe_che_tao_may_chuong_6_thiet_ke_do_g.doc
pages_from_dacn2_9_789_6002_537606.pdf