Hướng dẫn Đồ án công nghệ chế tạo máy - Chương 4: Hướng dẫn xác định chế độ cắt - Nguyễn Quang Tuyến
CHƯƠNG 4
HƯỚNG DẪN XÁC ĐỊNH CHẾ ĐÔ CẮT
NGUYÊN TẮC CHUNG KHI XÁC ĐỊNH CHẾ ĐÔ CẮT
1.1 Khái niệm chung
Chọn chế độ cắt là xác định chiều sâu cắt, số lần chạy dao, luợng chạy dao, tốc độ cắt và công suất cần thiết trong điều kiện gia công nhất định.
Chế độ cắt có lợi là chế độ cắt ít tốn thời gian nhất để chế tạo sản phẩm do vậy mà giá thành của nó rẻ nhất.
Nếu chọn đúng kết cấu dao, thông số hình học phần cắt, vật liệu, phuong pháp mài sắc và mài bóng cũng nhu xác định đúng đắn cách gá đặt kẹp chặt dao và phôi, điều chỉnh máy tốt, trang bị công nghệ có kết cấu hợp lý. sẽ tạo điều kiện để chọn chế độ cắt hợp lý và có lợi.
Bạn đang xem 20 trang mẫu của tài liệu "Hướng dẫn Đồ án công nghệ chế tạo máy - Chương 4: Hướng dẫn xác định chế độ cắt - Nguyễn Quang Tuyến", để tải tài liệu gốc về máy hãy click vào nút Download ở trên
Tóm tắt nội dung tài liệu: Hướng dẫn Đồ án công nghệ chế tạo máy - Chương 4: Hướng dẫn xác định chế độ cắt - Nguyễn Quang Tuyến
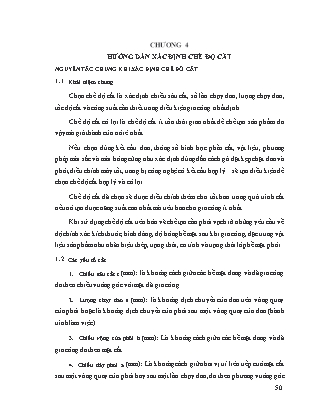
CHƯƠNG 4 HƯỚNG DẪN XÁC ĐỊNH CHẾ ĐỘ CẮT NGUYÊN TẮC CHUNG KHI XÁC ĐỊNH CHẾ ĐÔ CẮT Khái niệm chung Chọn chế độ cắt là xác định chiều sâu cắt, số lần chạy dao, luợng chạy dao, tốc độ cắt và công suất cần thiết trong điều kiện gia công nhất định. Chế độ cắt có lợi là chế độ cắt ít tốn thời gian nhất để chế tạo sản phẩm do vậy mà giá thành của nó rẻ nhất. Nếu chọn đúng kết cấu dao, thông số hình học phần cắt, vật liệu, phuong pháp mài sắc và mài bóng cũng nhu xác định đúng đắn cách gá đặt kẹp chặt dao và phôi, điều chỉnh máy tốt, trang bị công nghệ có kết cấu hợp lý... sẽ tạo điều kiện để chọn chế độ cắt hợp lý và có lợi. Chế độ cắt đã chọn sẽ đuợc điều chỉnh thêm cho tốt hơn trong quá trình cắt nếu nó tạo đuợc năng suất cao nhất mà tiêu hao cho gia công ít nhất. Khi sử dụng chế độ cắt trên bản vẽ chế tạo cần phải vạch rõ những yêu cầu về độ chính xác kích thuớc, hình dáng, độ bóng bề mặt sau khi gia công, đặc trung vật liệu sản phẩm nhu nhãn hiệu thép, trạng thái, cơ tính và trạng thái lớp bề mặt phôi. Các yếu tố cắt Chiều sâu cắt t (mm): là khoảng cách giữa các bề mặt đang và đã gia công đo theo chiều vuông góc với mặt đã gia công. Lượng chạy dao s (mm): là khoảng dịch chuyển của dao trên vòng quay của phôi hoặc là khoảng dịch chuyển của phôi sau một vòng quay của dao (hành trình làm việc). Chiều rộng của phôi b (mm): Là khoảng cách giữa các bề mặt đang và đã gia công đo theo mặt cắt. Chiều dày phoi a (mm): Là khoảng cách giữa hai vị trí liên tiếp cuả mặt cắt sau một vòng quay của phôi hay sau một lần chạy dao, đo theo phương vuông góc với chiều rộng phôi. Diện tích phoi f (mm2): Là tích số chiều sâu cắt t với lượng chạy dao s hoặc chiều rộng phoi b với chiều dày a ( f = t.s = ba). Tốc độ cắt: Là đoạn đường dịch chuyển của lưỡi cắt đối với mặt đang gia công trong một đơn vị thời gian. Tốc độ cắt tính ra m/phút. Tốc độ cắt khi mài đánh bóng và các nguyên công tương tự tính ra m/s. II. TIỆN VẢ BẢO 2.1 Chế độ cắt khi tiện Chiều sâu cắt và số lần chạy dao: Để giảm bớt thời gian gia công, kể cả thời gian phụ, nên sử dụng số lần chạy dao là ít nhất. Khi gia công thô, nên sử dụng chiều sâu cắt cực đại, tương ứng với lượng dư trong một lần chạy dao. Chiều sâu cắt có có ảnh hưởng rất lớn tới lực cắt, công suất cắt và rung động. Do đó, khi các yếu tố này của máy bị hạn chế, phải gia công bằng 2 Ạ 3 lần chạy dao. Gia công bán tinh độ nhám cấp 4 Ạ 6 được thực hiện bởi 1 Ạ 2 lần chạy dao. Chiều sâu cắt khi đó phụ thuộc vào độ chính xác cần thiết, vào độ bóng bề mặt, thông thường trong vòng từ 1 Ạ 4 mm. Khi gia công bằng dao có lưỡi cắt phụ thuộc vào góc nghiêng chính j = 0 với lượng chạy dao lớn, thì chiều sâu cắt bị hạn chế bới độ bền lưỡi cắt phụ hay phụ thuộc vào độ bền của mảnh hợp kim. Khi gia công tinh nên dùng tất cả lượng dư hớt đi trong một lần chạy dao. Lượng chạy dao: Khi dùng lượng chạy dao nên chú ý những yếu tố sau đây: yêu cầu độ bóng bề mặt, độ chống rung động của hệ thống máy - chi tiết - dao, độ bền vững cuả dao cụ, độ bền vững và công suất máy.các giátrị lượng chạy dao được cho và có thể tra trong các bảng phụ lục. Lượng chạy dao chọn theo bảng khi gia công thô cần phải kiểm tra độ bền mảnh hợp kim, độ chính xác gia công và độ bền các co cấu trong máy. Nếu kiểm tra lượng chạy dao đã chọn theo độ bền mảnh hợp kim, thì phải tính lực cắt thẳng đứng Pz ứng với lượng chạy dao đã chọn, sau đó so sánh với lực cắt cho phép ở điều kiện gia công nhất định cho trong bảng 14. Nếu lực cắt thực tế không lớn hon giá trị cho phép thì lượng chạy dao chọn đúng, ngược lại cần giảm lượng chạy dao. Kiểm tra lượng chạy dao theo độ bền thân dao chủ yếu là độ bền uốn. Lực Pz theo độ bền thân dao xác định theo công thức: P = B.’-^KG z 6l Đối với thân dao tiết diện vuông ( H = B) P = B 3[s KG z 6l Thân dao tròn: 3 H 32l KG Ở ĐÂY: B là chiều rộng thân dao (mm) H- chiều cao thân dao (mm) l- Tay đòn (mm) d- Đường kính thân tròn (mm) s - ứng suất uốn cho phép của vật liệu thân dao (KG/mm2 Khi chế tạo thân dao bằng thép kết cấu có giới hạn bền ơbp = 60 70 cóthể lấy [ơ-Ị, = 20KG / mm2. Bảng 4.1 Lượng chạy dao tiện thô mặt ngoài và tiện cắt đứt bằng dao thép gió và dao hợp kim cứng Đường kính phôi (mm) Chiều sâu cắt 5 8 12 30 Lượng chạy dao s mm/ vòng < 18 < 0,2 - - > 18 < 30 0,2 - 0,5 0,3 - 0,6 - > 30 < 50 0,4 - 0,8 0,5 - 1,0 - > 50 < 80 0,6 - 1,2 0,7 - 1,3 0,5 - 1,0 > 80 < 120 1,0 - 1,6 1,1 - 1,8 0,8 - 1,5 >120 <180 1,4 - 2,0 1,5 - 2,0 1,1 - 2,0 1,0 - 1,5 >180 <260 1,8 - 2,6 1,8 - 2,8 1,5 - 2,5 1,3 - 2,0 > 260 < 360 2,0 - 3,2 2,5 - 3,0 2,0 - 3,0 1,5 - 2,5 > 360 Chú thích: Lấy lượng chạy dao lớn khỉ gia công thép mêm, khỉ gia công chống trên mũi tâm nếu L/D <6 hoặc trong mâm cặp nếu L/D <2, còn giá trị nhỏ dùng khi gia công thép cứng, gang và khi gia công phôi có đường kính nhỏ nhưng lớn hơn chiều dài. Kiểm tra lượng chạy dao theo độ chính xác gia công có thể xuất phát từ điều kiện: Độ võng chi tiết gia công không vượt quá 0,25 dung sai của lầngia công đang tiêh hành. Lực cắt hướng kính Py kể đêh độ chính xác gia công xác định theo các công thức (khi tiện ngoài các trục nhẵn): Bảng 4.2. Lượng chạy dao khi tiện ngoài thép tôi bằng dao hợp kim cứng Giới hạn bền sbp (KG/mm2) Độ cứng HRC Lượng chạy dao s (mm/vòng) 160 49 0,1 - 0,3 180 54 0,07 - 0,2 200 58 0,05 - 0,15 Tiện chống hai tâm: Một đầu chống tâm đầu kia cặp vào mâm cặp: P -- f ^KG Khi chỉ kẹp trong mâm cặp: -E- P - f --- KG ở đây: f- Độ võng chi tiết (mm) 1- Chiều dài chi tiết (mm) E- Môđuyn đàn hổi bằng 21.000KG/mm2 đối với thép pD4 64 - Mômem quán tính thiết diện ngang của chi tiết (mm4) bằng » 0,05D4 với D 1à đường kính của chi tiết (khi chống hai tâm, một đầu cặp đầu kia chống tâm) hoặc 1à đường kính phôi (khi cặp). Khi kiểm tra độ bền các cơ cấu máy theo lượng chạy dao, phải xác định lực chiều trục Px. So sánh Px với lực cho phép về độ bền cơ cấu. Xuất phát từ lực Pz và đường kính chi tiết gia công ta xác định được mô men xoắn kéo theo: p .D „„ 2Mk = * z KGm 1000 Với: Pz - lực cắt thẳng đứng (KG) D- Đường kính chi tiết gia công (mm) Lấy Mômen xoắn kép vừa tính so sánh với Mômen cho phép của cơ cấu trong chuyển động chính. Giá trị lực và Mômen xoắn kép tính với lượng chạy dao đã chọn mà vượt quá trị số cho phép thì phải giảm lượng chạy dao. Lượng chạy dao cho phép trong trường hợp gia công các loạt vật liệu khác nhau bằng các loại dao khác nhau được cho trong bảng ở phần phụ lục kèm theo. Lực cắt: Công thức tính lực cắt cho ở bảng 4.3 ứng với dao có >o0, với các loại dao cắt và các loại vật liêụ cắt gọt khác nhau cho trong các bảng ở phần phụ lục. Bảng 4.3 Công thức tính lực cắt khi j > 00. Lực cắt Công thức Tiếp tuyến (thẳng đứng) Pz p = Cpz.tXpz .Sypz Vnpz ,kM (KG) Hướng kính Py py = c J .Sypy Vnpy .kM (KG) y py M py Lực chạy dao (hướng trục) Px p = C.t .SV .kM (KG) x px M px Cpz, Cpy, Cpx là hệ số. t- Chiều sâu cắt (mm) S- Luợng chạy dao (mm/vòng) k- hệ số phụ thuộc vật liệu gia công; xp,yp, np- Số mũ v- Vận tốc cắt (m/phút) Trong đó các hệ số và số mũ cuả chiều sâu, luợng chạy dao, vận tốc cắt đuợc xác định bằng thực nghiệm. Khi gia công vật liệu khác với bảng 4.2, khi dao mòn và thông số hình học thay đổi, lực cắt tính theo bảng 4.3 và 4.4 phải nhân với hệ số trong bảng 4.5. Khi gia công vật liệu khác phải tra các công thức và hệ số tuơng ứng trong các bảng tra ở phần phụ lục.. Tuổi bền dao: Tuổi bền dao phụ thuộc nhiều yếu tố: giá thành dao, số lần mài lại đến khi dao mòn hoàn toàn, giá thành mài bóng và mài sắc, thời gian thay dao, giá thành sử dụng máy, mức độ ảnh huởng của vận tốc cắt đến tuổi bền dao... Trừ dao bào, dao cắt ren, dao định hình có thể lấy tuổi bền dao T = 60 phút. Đối với dao bào, dao cắt ren, dao định hình lấy T = 120 phút còn dao có luỡi cắt phụ và j1 = 00, T = 30 45 phút. Khi gia công bằng nhiều dao một lúc, những trị số này nên tăng gần tỷ lệ với dao đổng thời tham gia cắt. Tốc độ cắt: Khi tham gia bằng dao thép gió, tốc độ cắt tính theo công thức trong bảng 23, 24. Truờng hợp tiện rộng lỗ, tốc độ cắt tính theo công thức này phải nhân với hệ số 0,9. Bamg 4.4 Hệ số và số mũ trong công thức bảng 4.3 Vật liệu gia công Dạng gia công Vật liệu phần cắt Hệ số và số mũ Lực tiếp tuyến Lực hướng kính Lực chạy dao c ^pz pz Y Npz c 1" Ypy Npy py c v-'px Xpx Y px Npx Thép và vật đúc bằng thép Tiện ngoài, tiện rộng Hợp kim cứng 300 0,75 1 0,15 243 0,9 -0,3 0,6 339 1 0,5 -0,4 Thép gió 208 0,75 1 0 141 0,9 0 0,75 66,8 1,2 0,65 0 Tiện rãnh, tiện cắt đứt Hợp kim cứng 408 0,8 0,72 0 172 0,73 0 0,67 - - - - Thép gió 247 1,0 1 0 - - - - - - - - Gang xám Tiện ngoài, tiện rộng Hợp kim cứng 92 0,75 1 0 54 0,9 0 0,75 46 1 0,4 0 Thép gió 118 0,75 1 0 54 0,9 0 0,75 51,4 1,2 0,65 0 Tiện rãnh, tiện cắt đứt Thép gió 153 1,0 1 0 129 - - - - - - - Bảng 4.5 Hệ số điều chỉnh khi tính lực cắt phụ thuộc vật liệu gia công Vật liệu gia công Hệ số trong thức Lực tiếp tuyến Lực huớng kính Lực chạy dao Hợp kim cứng Thép gió Hợp kim cứng Thép gió Hợp kim cứng Thép gió Thép sbp < 60 KG / mm2 z _ X 0,35 k = (^bbp. J ppz 75 ) z _ \0,35 r = 1 J Ỉ^1LL' = t 75 J z _ \1,35 ML =75 J Z _ ,2 75 J r = (J KMpx = 1 75 Z _ X1,5 75 J sbp > 60KG /mm2 Z ,0,75 75 J Gang xám r = (_]0,4 Mpz L190 ) r =( H.} 055 Mpz 1,190J r = (—ì Mpy L190 J ( hb 2’ Mpy L190 J J “ Mpx 190 J (HB J1'1 Mpx L190 J Bảng 4.6 Công thức tính tốc độ cắt khi gia công bằng dao thép gió Dạng gia công Công thức tính Ký hiệu Tiện ngoài C V60 = k m / p t x .s V60 : Tốc độ cắt ứng với t=60p. V120 : Tốc độ cắt khi t=120p t: Chiều sâu cắt (mm) S: Lượng chạy dao (mm/vòng) Cv: Hệ số Xv, yv: Số mũ Tiện rãnh cắt đứt C V60 = \. m / p .s Tiện định hình C V120 = - m / p ,sy' Bảng 4.7. Giá trị hệ số Cv và số mũ xv, yv. Vật liệu gia công Dạng gia công Lượng chạy dao (mm/vòng) Điều kiện gia công Có dung dịch Không có dung dịch Hệ số và số mũ Cv xv yv Cv xv yv Thép két cấu ơhp = 75KG / mm' Tiện ngoài S < 0,25 S > 0,25 49,9 31,6 0,25 0,33 0,66 30,4 24,3 0,25 0,50 0,66 Tiện rãnh cắt đứt - 6,77 - 0,66 - - - Định hình - 5,4 - 0,5 - - - Gang dẻo HB150 Tiện ngoài S < 0,25 S > 0,25 65,0 46,0 0,2 0,25 0,5 - - - Tiện rãnh cắt đứt - 13,4 - 0,5 - - - Gang xám HB190 Tiện ngoài S < 0,25 S > 0,25 - - - 24,7 23,6 0,15 0,30 0,40 Tiện rãnh cắt đứt - - - - 9,78 - 0,4 Đổng thau HB = 100 -140 s < 0,25 s > 0,25 - - - 99 63 0,12 0,25 0,50 Bảng 4.8 Hệ số khả năng gia công của các vật liệu khác nhau Vật liệu gia công Hệ số khả năng gia công Thép cácbon C < 0,6% 1,0 C > 0,6% 0,85 Thép tự động 1,2 Thép crôm; crôm - niken; măng gan; crôm - môlipđen; crôm - niken - môlipđen; crôm - nhôm; crôm - môlipđen - nhôm; crôm - niken - vôníram. 0,8 Thép crôm- mănggan; crôm - silic; silic - mănggan. 0,7 Thép gió 0,6 Nhôm 5 - 6 Đuya-ra 4 - 6 Xiluymin và hợp kim nhôm đúc 4 - 5 Bảng 4.9. Công thức tính toán hệ số Km Vật liệu gia công Thép Gang rèn Gang xám Đổng thau Công thức f "\n 75 k = —— \ơbP 7 k = í 150 Ỵ m t HB 7 , 190 Ỵ '' ~ t hb 7 k J120 Ỵ m t hb 7 Vật liệu gia công số mũ n Thép tự động, cácbon, crôm 1,75 Thép crôm - niken, manggan, crôm- manggan, crôm silic - manggan, crôm - silic, silic - manggan, crôm- niken - manggan 1,5 Thép crôm - môlipđen, crôm - niken - môlipđen, crôm - môlipđen - nhôm, thép gió. 1,25 Gang dẻo, gang xám và đổng thau 1,7 Bảng 4.10. Hệ số khi tính tốc độ cắt Nhân tố ảnh hưởng Hệ số Trạng thái phôi Để nguyên Nhiệt luyện Cán Thường hoá ủ Làm tốt Kéo nguội Cán nguội 1,1 1 0,95 0,9 0,8 Yếu tố ảnh hưởng đến tốc độ cắt Góc nghiêng chính j 30 45 60 90 Hệ số Góc nghiêng chính j Thép, vật đúc bằng thép, hợp kim Al và Mn 126 1 0,84 0,66 Gang 1,2 1 0,88 0,73 Hợp kim đổng - 1,13 1 0,83 Góc nghiêng phụ j1 Góc j1 10 15 20 30 45 Hệ số 1 0,97 0,94 0,91 0,87 Bán kính Bán kính r (mm) 1 2 3 4 Hệ số 0,9 1 1,05 1,12 Tiết diện thân dao Tiết diện thân dao (mm) 10x10 f10 f12 12x12 10x16 16x16 12x20 f16 20x20 16x25 f20 f25 20x30 20x30 f30 30x30 25x40 f40 30x45 40x40 40x60 60x90 Hệ số Gang 0,87 0,9 0,93 0,97 1 1,04 1,08 1,12 1,19 Thép 0,93 0,95 0,97 0,98 1 1,02 1,04 1,06 1,09 Độ mòn mặt trước của dao Vật liệu gia công Loại dao Độ mòn trước mặt h8 (mm) 0,5 1 1,5 2 1,5 2 3,5 4 Thép, gang rèn Tiện mặt Tiện Hệ số 0,93 0,95 0,97 1 - - - - Tiện rãnhcắt đứt 0,85 1,00 - - - - - - Gang xám Tiện ngoài - - - 0,93 0,94 0,95 0,97 1 Tiện trong 0,94 0,96 0,97 1 - - - - Tiện rãnhcắt đứt 0,85 0,9 0,95 1 - - - - Nhân tố ảnh Hệ số hưởng Trạng thái bề mặt Không có vỏ cứng Có vỏ cứng do đức Thông thường Có xỉ bẩn Thép Gang Hợp kim đông Thép Gang Hợp kim đông 1 0,75- 0,85 0,7 - 0,8 0,9 - 0,95 0,5 - 0,6 0,5 - 0,6 0,7 - 0,8 Vật liệu dao Thép gió Thép gió 90MnSi CD110A CD120A 1 1 0,6 0,5 và < TUỔI BỀN Vật liệu gia công Loại dao Tuổi bền dao (phút) 30 60 90 120 240 360 Hệ số Thép, vật đúc bằng thép, gang đúc nvn pnu, tiện mặt, tiện rộng 1,09 1 0,95 0,92 0,85 0,80 ± ivn rãnh cắt đứt 1,19 1 0,9 0,83 0,71 0,64 Định hình - - 1,09 1 0,81 0,72 Gang xám c s 1,07 1 0,96 0,93 0,87 0,84 c xí 1,11 1 0,94 0,90 0,81 0,76 Hợp kim đồng Tất cả các loại 1,16 1 0,91 0,84 0,73 0,66 Hợp kim Al+Mn Tất cả các loại 1,23 1 0,88 0,81 0,66 0,58 Dạng truớc mặt Dạng truớc mặt Phẳng Cong Vát Hệ số 1 1,05 1,15 Nếu gia công các thép khác nhau, gia công nhôm và hợp kim nhôm, giá trị tốc độ cắt tính đuợc phải nhân với hệ số khả năng gia công ở bảng 4.11. Truờng hợp cơ tính vật liệu gia công khác trong bảng 4.8, tốc độ cắt theo bảng 4.8 - 4.9 phải nhân với hệ số KMv theo bảng 4.11. Nếu kể các yếu tố ảnh huởng đến tốc độ cắt phải nhân với hệ số trong bảng 4.11. Công thức tính tốc độ cắt khi gia công bằng dao hợp kim cứng cho ở bảng phụ lục. Nếu cơ tính vật liệu gia công khác trong bảng 28, giá trị tốc độ cắt phải nhân với hệ số KMv cho trong bảng phụ lục. Ngoài ra, ứng với từng loại vật liệu gia công, tốc độ cắt phải nhân với hệ số khả năng gia công trong bảng 4.9. Trên thực tế vận tố cắt gọt cũng được tra trong bảng cho trước và sau đó lấy theo só vòng quay thực tế cuả loại máy đã lưạ chọn. Người thiết kế không nhất thiết phải tính giá trị cuả vận tốc Bào Lượng chạy dao: Bảng 31 cho lượng chạy dao bào thô, bào bán tinh cho trong bảng 7. Tốc độ cắt: Tính tốc độ cắt khi bào trên máy bào giường giống như khi tiện ngoài (bảng 23-30). Tính tốc độ cắt cho máy bào ngang cũng giống như khi tiện ngoài nhưng phải nhân với hệ số trong bảng 32. Công suất hiệu dụng tính như trên. b) Gia công gang: giống dao hợp kim cứng BK6 và phải nhân với hệ số . Tốc độ cắt gia công chất dẻo kết cấu lấy như sau: Dao bằng thép dụng cụ v = 75^100m/f. Khi gia công bằng dao thép gió V < 300m/p. Gia công bằng dao hợp kim cứng V < 800m/p. Công suất cắt hiệu dụng tính theo công thức sau: Nỡ = .V 60.102 KW Pz là lực cắt thẳng đứng (KG). V là vân tốc cắt m/p Khi gia công đổng thời nhiều dao cụ thì công suất hiệu dụng bằng tổng công suất của từng dao. Bảng 4.11. Lượng chạy dao bào thô Vật liệu gia công Góc nghiêng chính j0 Chiều sâu cắt t (mm) < 5 < 12 < 20 < 30 > 30 Lượng chạy dao (mm/vòng) Thép 30 3,5 - 5,5 3,5 - 5,0 2,8 - 4,0 2,1- 3,5 - 45 - 75 2,5 - 4 2,5 - 3,5 2,0 - 3,0 1,5 - 2,5 1,2 - 1,8 90 - 2,0 - 3,0 1,5 - 2,0 1,2 - 2,0 1 - 1,5 Gang 30 4,0 - 6,0 4,0 - 5,5 3,5 - 5,0 2,5 -4,0 - 45 - 75 3,0 - 4,5 3,0 - 4,0 2,5 - 3,5 1,8 - 2,8 1,4 - 2,0 90 3,0 - 4,5 2,5 - 3,5 2-3 1,4 - 2,3 1,2 - 1,8 Chú thích: 1. Lượng chạy dao trong bảng ứng với phôi có vỏ cứng. Khi gia công phôi không có vỏ cứng nên tâng 10 +15%. 2. Nếu gia công đồng thời nhiều dao phải dùng lượng chạy dao và tốc độ cắt theo chiều sâu cắt cho một dao. Bảng 4.12. Hệ số tính tốc độ cắt trên máy baò ngang và máy xọc Máy Chiều dài hành trình dao (mm) 50 100 150 200 300 500 Hệ số Bào ngang 0,94 0,89 0,81 0,80 0,77 0,70 Xọc 0,71 0,67 0,61 0,60 0,57 0,52 IU. KHOAN VẢ KHOAN RỘNG Lỗ Chiều sâu t khi khoan vật liệu đặc t = (mm) và khi khoan rộng t = (mm) D - Đường kính khoan (mm). d - Đường kính lỗ đã khoan trước (mm). Lượng chạy dao khi khoan với: Mũi khoan bằng thép dụng cụ mài côn kép ở Bảng 4.13. Mũi khoan gắn mảnh hợp kim cứng ở bảng 36. Lượng chạy dao khi khoan rộng: Mũi khoan thép dụng cụ bảng 35. - Mũi khoan gắn hợp kim cứng bảng 37. 4.13 Lượng chạy dao khi khoan bằng mũi khoan mài côn kép bằng thép dụng cụ. Đường kính khoan (mm) Nhó m chạy dao Vật liệu gia công Thép cóơbp kg/mm2 Gang có HB Đên 80 Từ 80 đên 100 Từ 100 Đên 200 Từ 200 Chạy dao s (mm/ vòng) Đêh 5 I II III 0,08-0,18 0,06-0,11 0,04-0,08 0,06-0,014 0,05-0,10 2,03-0,07 0,04-0,10 0,04-0,08 0,02-0,05 0,14-0,03 0,10-0,23 0,07-0,15 0,08-0,20 0,06-0,15 0,04-0,10 Từ 5 đên 10 I II III 0,20-0,37 0,12-0,27 0,10-0,18 0,15-0,28 0,12-0,21 0,07-0,14 0,11-0,23 0,08-0,16 0,05-0,11 0,36-0,75 0,24-0,55 0,18-0,35 0,22-0,41 0,16-0,33 0,11-0,22 Từ 10 đên 20 I II III 0,38-0,64 0,28-0,45 0,18-0,32 0,30-0,48 0,21-0,32 0,13-0,21 0,24-0,38 0,16-0,26 0,11-0,17 0,74-1,2 0,55-0,82 0,36-0,52 0,45-0,77 0,34-0,58 0,23-0,37 Từ 20 đên 30 I II III 0,66-0,82 0,46-0,58 0,33-0,42 0,50-0,62 0,32-0,40 0,21-0,27 0,39-0,50 0,26-0,34 0,17-0,25 1,2-1,7 0,84-1,0 0,55-0,68 0,80-1,05 0,60-0,76 0,38-0,48 Từ 30 đêh 60 I II III 0,94-1,0 0,640,7 0,540,6 0,740,8 0,540,6 0,340,4 0,640,7 0,440,5 0,340,4 1,441,8 1,041,1 0,7040,75 1,1 4 1,2 0,8040,90 0,5040,55 Chú thích'. 1. Khỉ chiều sâu khoan lớn hơn 3D lượng chạy dao cẩn phải giảm, bằng nhân cách với một hệ số cho trong bảng 34. 2. Để tránh hư hỏng mũi khoan cẩn lưu ý khi mũi khoan gẩn thoát khỏi lỗ thì tắt chạy dao tự động và tiến hành dao bằng tay. Lượng chạy dao giới thiệu trên cho trong giới hạn đảm bảo độ bền cho phép của mũi khoan 4.14 Hệ số điều chỉnh khi lượng chạy dao phụ vào chiều sâu khoan (đối với một nhóm chạy dao Tỉ số giữa chiều sâi khoan với đường kính mũi khoan L x 3 5 7 10 Hệ số kLS 1 0,9 0,8 0,75 4.15. Lượng chạy dao khoan rộng lỗ khi dùng mũi khoan bằng thép dụng cụ mài côn kép Đường kính mũi khoan(m m) Vật liệu gia công Thép và đúc bằng thép Gang Nhóm chạy dao S (mm/vòng) I II III I II III Nhóm chạy dao Đên 25 10 15 0,741,1 0,841,2 1,540,7 0,640,8 0,340,4 0,440,5 1.141.5 1.241.6 0,741, 0 0,841, 1 0,440,5 0,4540, 6 Từ 25 đên 30 10 15 20 0,74-1,1 0,74-1,1 0,841,2 0,540,7 0,640,7 0,640,8 0,340,4 0,340,4 0,440,5 1,041,4 1.141.5 1.241.6 0,741, 1 0,841, 2 0,841, 2 0,440,5 0,4540, 55 0,540,6 Từ 40 đên 50 15 20 30 0,841,2 0,941,2 0,941,3 0,540,7 0,640,8 0,640,8 0,340,4 0,440,5 0,440,5 1,041,6 1.141.7 1.241.8 0,741, 1 0,841, 2 0,841, 3 0,440,5 0,540,6 0,640,7 Từ 40 đên 50 20 30 40 0,941,2 1,041,3 1,041,4 0,640,8 0,740,9 0,840,9 0,440,5 0,440,5 0,54,06 1,241,8 1,342,0 1,342,0 0,941, 3 1,041, 4 1,041, 4 0,540,6 0,640,7 0,740,8 Từ 50 đên 60 30 40 50 0,941,2 1,041,3 1,041,4 0,740,8 0,840,9 0,840,9 0,440,5 0,440,5 0,54,06 1,241,8 1,342,0 1,342,0 0,941, 2 0,940, 3 1,041, 4 0,5540, 6 0,640,7 0,740,8 Chú thích: Khỉ chọn các nhóm chạy dao cần theo sự chỉ dẫn đối với khoan. Chọn lượng chạy dao khoan khi khoan (Bảng 4.13 - 4.16). Lượng chạy dao lớn nhất (nhóm I) dùng khi koan lố trong phôi cứng: Không có dung sai hoặc có dung sai đêh cấp chính xác 5. Sau đó còn gia công bằng một số dụng cụ khác. Lượng chạy dao trung bình (nhóm II) dùng khi khoan các lỗ trong phôi không được cứng vững dạng hộp có thành mỏng: Không có dung sai hoặc có dung sai cấp chính xác 5. Sau đó còn gia công bằng một số dụng cụ khác. Trứoc khi cắt ren bằng ta rô. Bảng 4.16. Lượng chạy dao khi khoan bằng mũi khoan gắn hợp kim cứng Đường kính mũi khoan (mm) Thép cac bon thép hợp kim không tôi 055^85 kg/mm2 Vật liệu gia công Khi gia công không dùng dung dịch nguội lạnh ê-mun-xi Không dùng dung dịch nguội lạnh Thép tôi có độ cứng HRC Gang độ cứng Đến 40 40 55 64 HB<170 HB>170 Lượng chạy dao S (mm/vòng) 10 12 16 20 23 26 29 0,12-^0,16 0,14^0,2,0 0,16^0,22 0,20^0,26 0,22^0,28 0,24^0,32 0,26^0,35 0,04^0,05 0,03 0,025 0,02 0,25^0,45 0,3^0,5 0,35^0,6 0,4^0,7 0,45^0,8 0,5^0,85 0,5^0,90 0,20^0,35 0,20^0,35 0,25^0,40 0,25^0,40 0,30^0,45 0,35^50 0,40^0.60 Chứ thích: Khỉ chiều sâu khoan lớn hơn 3D cẩn phải nhân trị số đã cho trong bảng với hệ số chọn ở bảng 34. Mũi khoan là hợp kim BKS. Bảng 4.17. Lượng chạy dao khi khoan rộng lỗ bằng mũi khoan gắn hợp kim cứng. VẬT LIỆU GIA CÔNG Có dung dịch nguội lạnh ê- mun-xi Không có dung dịch nguội lạnh Thép cacbon và thép hợp kim không tôi Gang có độ cứng HB<170 HB>170 Lượng chạy dao s (mm/vòng) 25 10 15 0,3040,45 0,3040,50 0,6040,9 0,604-1,00 0,4040,60 0,4040,65 30 10 15 20 0,3540,55 0,3540,55 0,3540,60 0,6540,10 0,6540,10 0,6540,10 0,5040,8 0,5040,8 0,5040,8 Lượng chạy dao nhỏ nhất (nhóm II) khi khoan lỗ chính xác, sau đó gia công lần nữa bằng mũi khoét hoặc mũi doa và phôi có độ vững kém, mặt tựa không ổn định. Lượng chạy dao đảm bảo độ bền của mũi khoan tính theo công thức: " A A' D0-81 z Đoi với thép: s = 4,46. 094 (mm/vòng) d b . D081 Đoi với gang: s = 7,34. — (mm/vòng) HB s b: Giới hạn bền của thép được gia công (KG/mm2) HB: Độ cứng của gang được gia công. Theo lượng chạy dao của mũi khoan chọn trong bảng 33 xác định được lực cắt chiều trục, mà so với lực cắt do co cấu chạy dao của máy đảm bảo. Chọn lượng chay dao khi khoan rộng lỗ: (bảng 35 và bảng 37) lượng chạy dao lớn (nhóm I) dùng: Khi khoan rộng lỗ không có dung sai hoặc đạt cấp chính xác bậc 5. Khi khoan rộng lỗ để sau đó còn gia công bằng một số dụng cụ khác( mũi khoét hoặc dao tiện trong và mũi doa hoặc đầu doa). Khi khoan rộng lỗ sau đó còn cắt ren bằng ta rô hoặc bằng dao cắt gọt với điều kiện là gia công sau khi khoan bằng dao khoét hoặc bằng lưỡi dao doa. Lượng chạy dao (nhóm II) dùng: Khi khoan lỗ rộng sau đó cắt ren bằng ta rô hay tiện trong. Khi khoan lỗ rộng sau đó gia công 1 lần nữa bằng mũi khoét với chiều sâu cắt bình thường hoặc 2 lần. Chạy dao nhỏ (nhóm III) dùng khi gia công lỗ đạt cấp chính xác 4 và độ bóng V5 (với thép),V6 (đối với gang) với điều kiện sau đó gia công thêm một lần nữa bằng mũi khoét với chiều sâu cắt nhỏ, hoặc một lần bằng mũi doa. Tốc độ cắt: Mũi khoan bằng dụng cụ. Tốc độ cắt khi khoan và khoan rộng lỗ tính theo công thức cho trong Bảng 4.18 Tốc độ cắt khi mũi khoan bằng thếp dụng cụ. Khoan thép kết cấu, thép hợp kim, gang xám, gang dẻo. .. C Dzv , . 1T = TmSvy KMv m/phút Khoan rộng thép kết cấu, thép hợp kim, gang xám, gang dẻo. . . C Dzv , . VT = KMv m/phút T Tmtxv S'-’ Mv Bảng 4.19 Giá trị của các hệ số và số mũ của các công thức. Vật liệu gia công Dạng gia công Chạy dao s mm/vòng Hệ số và số mũ Cv Yv ”V Xv TM* Thép kết cấu cac bon và thép hợp kim. s b = 75KG/mm2 HB = 215 Khoan đến 0,2 8,9 0,7 0,4 - 0,2 Từ 0,2 12,4 0,5 Khoan rộng - - 0,5 0,4 0,2 0,2 Gang xám HB = 190 Khoan đến 0.3 17,6 0,55 0,25 - 0,125 Từ 0,3 30,3 0,4 Khoan rộng - - 0,4 0,25 0,1 0,125 Gang dẻo HB = 150 Khoan đến 0,3 26,2 0,55 0,25 - 0,125 Từ 0,3 30,3 0,4 0,25 Khoan rộng - - 0,4 0,1 0,125 Thép không rỉ và thép chịu nhiệt Khoan - - 0,45 0,5 - 0,12 * Xem Bảng 4.21 Bảng 4.20. Hệ số điều chỉnh tốc độ cắt với điều kiện làm việc thay đổi, phụ thuộc vào: a) Vật liệu gia công ' ■ ■ Vật liệu gia công kMV Loại thép kcv Tự động 93 Cán nguội 1,1 O 1,05 d bp Thép cac bon sb £ 55 KG/mm2 0,02.8 bp0,9 Cán nóng 1 Thép cac bon s b > 55 KG/mm2 48.7 Thường hoá 0,90 O 0,9 8 bp Thép hợp kim 48.7 ủ 0,9 O 0,9 8 bp Gang Gang xám, gang dẻo 917 Hoá tốt 0,8 HB1'3 b) Hình dáng mài và vật liệu dao Hình dáng mài Vật liệu gia công kfv Vật liệu dụng cụ (nhãn hiệu thép) kuv Mài côn kép m Ị Thép 1 P9 1 Gang 1 Mài thường H Thép 0,87 9XC 0,6 Gang 0,87 c) Tuổi bền của mũi k hoan Vật liệu gia công Chỉ số của độ bền tương đối Tỷ lệ giữa tuổi bền thực tế và tuổi bền tiêu chuẩn J V TH 0,25 0,5 1,0 2 4 6 8 12 Giá trị hệ số k^ Thép Gang 0.20 0,125 1,32 1,20 1,14 1,09 1 1 0,87 0,91 0,76 0,84 0,70 0,79 0,66 0,76 0,61 0,73 d) Chiều sâu khoan Tỉ lệ giữa chiều sâu lỗ khoan với đường kính khoan L/D 3 4 5 6 8 10 Giá trị hệ số klo 1,0 0,85 0,75 0,7 0,6 0,5 Hệ số điều chỉnh tốc độ cắt cho trong Bảng 4.20. Với mũi khoan hợp kim cứng: Tốc độ cắt khi khoan và khoan rộng lỗ tính theo công thức cho trong các bảng tra cho trong phần phụ lục. Lực cắt và mômen xoắn: Công thức tính lực cắt p (KG) và mômen xoắn MK (KGmm) đối với mũi khoan bằng thép gió xem Bảng 4.22 - 4.24 còn với mũi khoan hợp kim cứng xem bảng phụ lục. Bảng 4.21. Hệ số điều chỉnh tốc độ cắt phụ thuộc vào chiều sâu khoan Tỉ số giữa chiều sâu của lỗ và đường kính mũi khoan L/D 2,5 7,5 10 Hệ số kl 1 0,9 0,8 Chú thích: 1. Khỉ khoan làm lạnh với dung dịch 5% êmuxin. Khi làm lạnh bằng dung dịch nước co pha 5% cloruabari cho thêm 1% nitơrat natri, tóc độ cắt cho trong bảng sẽ nhân thêm với hệ sô 1,15. Khi mài sắc mũi khoan, bề mặt làm việc và lưỡi cắt không được có vết sước và ba via. Độ mòn cho phép ở phía bề mặt sau s = 1,0 1,2 mm. Công suất cắt hiệu dụng tính theo công thức. No = KGmm o 972.1000 Mk mômen xoắn (KGmm) n số vồng quay mũi khoan trong một phút. công thức tính tốc độ cắt (m/p) Vật liệu gia Lượng chay Dạng gia công công dao Khoan Khoan lỗ rộng Thép chưa tôi và thép kết cấu cac bon thép crôm thép niken làm lạnh bằng êmuxi s £ 0,2 (mm/vòng) 750.D0,6 - T0,25s0,3§bp0,9 750.D0,6 T0,25s0,3dbp0,9 s > 0,12 (mm/vòng) 490.D0,6 - T°,25s°,5Sbp0,9 Gang xám, gang dẻo không dùng dung dịch nguội lạnh 40000.D0,6 T0,4s0,5~pb1,3 750.D0,6 - T0,25s0,3§bp0,9 Công thức tính lực cắt và mômen xoắn khi khoan và khoan thép rộng lỗ thép các-bon, thép hợp kim, gang bằng mũi thép gió Dạng gia công Công thức để tính Lực cắt chiều trục p (KG) Mômen xoắn Mk (KGmm) Khoan p = CpDzpsypktp MK — CMD2,0syMkmm Khoan rộng p = Ct^sypk „ r — <xpt o KMp M — CMDtxsyMkmm Bảng 4.24. Giá trị các hằng số và số mũ trong công thức tính lực cắt và mômen xoắn đối với mũi khoan bằng thép gió Dạng gia công Vật liệu gia công Dạng mài của mũi khoan Giá trị của hằng số và số mũ theo công thức Lực cắt theo chiều trục Mômen Cp ”p Yp Yp Cm Ym Xm Khoan Thép thường và thép hợp kim ơb - 75KG/mm2 An 98,8 1 0,7 - 39 0,8 167 0,8 0,9 - Gang xám HB = 190 An 62 1 0,8 - 23,6 0,8 - Gang dẻo HB = 150 An 63 1 0,8 - 23,6 0,8 Khoan rộng Thép Cacbon và thép hợp kim ' HB = 125, ơb = 75KG/mm2 AP 46 0,7 1,3 93,5 0,8 0,9 Gang xám HB = 190 ap 28,7 - 0,4 1,2 88 0,8 0,75 4.25. Hệ số điều chỉnh lực cắt và mômen xoắn trong điều kiện làm việc thay đổi phụ thuộc vào. a) Vật liệu gia công Vật liệu gia công Thép Gang Hệ số kMP = kMM kMp = kMt=-V”-7' kMP = kMM =~ - "B ) 6 M 190 b) Hình dạng mài để khoan Dạng mài H AP' A^n, HaHBP XAP Vật liệu gia công Thép Gang Hệ số để tính toán lực chiều trục kfP Thép 1'33 1 - Gang 1'33 1 0'66 Hệ số để tính mômen xoắn ko M Thép 1,11 1 1 Gang 1'0 1 1 c) Dạng luỡi cắt của mũi khoan Luỡi cắt mũi khoan Sắc Cùn Hệ số để tính lực chiều trục K Sp 0'62 1 0,77 Hệ số để tính mômen xoắn K SM Chú thích: Các dạng mài được viết gọi theo ký hiệu H mài thường, Hn mài thường và mài lưỡi cắt ngang,Hỡn mài thường có mài lưỡi cắt ngang và cạnh viền, ỡnnmài kép và lưỡi cắt ngang, ỡnnmài kép có lưỡi cắt ngang và cạnh viền. XỒPAài kép có lưỡi mài cắt ngang theo phương pháp ÌKldpob 4.26. Hệ số điều chỉnh để tính lực cắt và mômen xoắn phụ thuộc trạng thái cắt mũi khoan Luỡi cắt mũi khoan Sắc Cùn Hệ số để tính lực chiều trục K Sp 0,62 1 Hệ số để tính mômen xoắn K SM 0,77 1 Chú thích : 1. Khi mài mũi khoan không làm suớc bề mặt làm việc và luỡi cắt 2 . Độ mòn cho phép của bề mặt sau mũi khoan s = 1,0 1,2 mm Các truờng hợp khác cần tra các bảng tuơng ứng trong phần phụ lục
File đính kèm:
huong_dan_do_an_cong_nghe_che_tao_may_chuong_4_huong_dan_xac.doc
pages_from_dacn2_5_5181_6055_537610.pdf