Hướng dẫn Đồ án công nghệ chế tạo máy - Chương 2: Thiết kế sơ bộ phương án công nghệ - Nguyễn Quang Tuyến
Thiết kế quy trình công nghệ phụ thuộc rất nhiều yếu tố: Dạng sản xuất, điều kiện sản xuất và đặc điểm của sản phẩm gia công. Do đó phân tích đánh giá và chọn lựa các phuơng án công nghệ có nhiều phuơng án. Phuong án tối uu chỉ có thể đuợc xác định thông qua các chỉ tiêu kinh tế kỹ thuật cụ thể đạt đuợc trong thực tế gia công.
Khi thiết kế sơ bộ phuơng án công nghệ cần thực hiện các công việc sau:
_ Chọn và xác định dạng sản xuất.
_ Phân tích các quá trình công nghệ hiện hành.
_ Chọn phôi và phuơng pháp chế tạo phôi.
_ Thiết lập tiến trình công nghệ gia công.
Bạn đang xem 20 trang mẫu của tài liệu "Hướng dẫn Đồ án công nghệ chế tạo máy - Chương 2: Thiết kế sơ bộ phương án công nghệ - Nguyễn Quang Tuyến", để tải tài liệu gốc về máy hãy click vào nút Download ở trên
Tóm tắt nội dung tài liệu: Hướng dẫn Đồ án công nghệ chế tạo máy - Chương 2: Thiết kế sơ bộ phương án công nghệ - Nguyễn Quang Tuyến
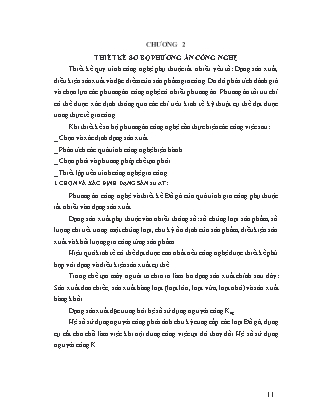
CHƯƠNG 2 THIẾT KẾ SƠ BỘ PHƯƠNG ÁN CÔNG NGHỆ Thiết kế quy trình công nghệ phụ thuộc rất nhiều yếu tố: Dạng sản xuất, điều kiện sản xuất và đặc điểm của sản phẩm gia công. Do đó phân tích đánh giá và chọn lựa các phuơng án công nghệ có nhiều phuơng án. Phuong án tối uu chỉ có thể đuợc xác định thông qua các chỉ tiêu kinh tế kỹ thuật cụ thể đạt đuợc trong thực tế gia công. Khi thiết kế sơ bộ phuơng án công nghệ cần thực hiện các công việc sau: _ Chọn và xác định dạng sản xuất. _ Phân tích các quá trình công nghệ hiện hành. _ Chọn phôi và phuơng pháp chế tạo phôi. _ Thiết lập tiến trình công nghệ gia công. I. CHỌN VẢ XÁC ĐỊNH DẠNG SẢN xu AT: Phuơng án công nghệ và thiết kế Đổ gá của quá trình gia công phụ thuộc rất nhiều vào dạng sản xuất. Dạng sản xuất phụ thuộc vào nhiều thông số: số chủng loại sản phẩm, số luợng chi tiết trong một chủng loại, chu kỳ ổn định của sản phẩm, điều kiện sản xuất và khối luợng gia công từng sản phẩm. Hiệu quả kinh tế có thể đạt đuợc cao nhất nếu công nghệ đuợc thiết kế phù hợp với dạng và điều kiện sản xuất cụ thể. Trong chế tạo máy nguời ta chia ra làm ba dạng sản xuất chính sau đây: Sản xuất đơn chiếc; sản xuất hàng loạt (loạt lớn, loạt vừa, loạt nhỏ) và sản xuất hàng khối. Dạng sản xuất đặc trung bởi hệ số sử dụng nguyên công Kng Hệ số sử dụng nguyên công phản ảnh chu kỳ cung cấp các loại Đổ gá, dụng cụ cắt cho chỗ làm việc khi nội dung công việc tại đó thay đổi. Hệ số sử dụng nguyên công K sẽ được xác định theo công thức sau: Kng = z NCo P,, -1- CM Trong đó SNCO là tổng số các nguyên công khác nhau được tổ sản xuất thực hiện trong thời gian quy ước. PCM là số công nhân thực tế của tổ sản xuất khi thực hiện các nguyên công trong thời gian quy ước. Bảng 2.1 Hệ số sử dụng nguyên công cho các dạng sán xuất khác nhau Dạng sản xuất Hệ số sử dụng nguyên công Kng Sản xuất hàng khối. 0,1 Ạ 1,0 Sản xuất loạt lớn. 1 < Kng < 10 Sản xuất loạt vừa. 10 < Kng < 20 Sản xuất loạt nhỏ. 20 < Kng Xác định dạng sản xuất theo phương pháp gần đúng (tra bảng). Trong một số trường hợp cần xác định nhanh dạng sản xuất mà không yêu cầu độ chính xác cao có thể sử dụng phương pháp tra bảng. Khi xác định dạng sản xuất bằng phương pháp tra bảng cần xác định khối lượng của chi tiết gia công và số lượng chi tiết tổng cộng cần chế tạo trong một năm. Số lượng chi tiết tổng cộng trong một năm được xác dịnh theo công thức sau; N = N1m fl + 0^1 1 100 ) Trong đó: N1 là số lượng sản phẩm cần chế tạo trong 1 năm theo kế hoạch. m là số lượng chi tiết trong một sản phẩm. a là lượng sản phẩm dự phòng sai hỏng khi tạo phôi gây ra. b là lượng sản phẩm dự trù cho hỏng hóc và phế phẩm trong quá trình gia côcng cơ. Thường chọn atừ 3% Ạ 6%; b từ 5% Ạ 7%; Khối luợng chi tiết được xác định theo công thức Q = V.g (kg) Trong đó: Q là khối lượng chi tiết (kg) V là thể tích của chi tiết (cm3) g là khối luowngj riêng của vật liệu (kg/cm3) Với thép, g = 7,852 kg/dm3 k với gang dẻo g = 7,2 Ạ 7,4 kg/dm3 k với gang xám g = 6,8 Ạ 7,4 kg/dm3 k với nhôm g = 2,6 Ạ 2,8 kg/dm3 với đổng g = 8,72 kg/dm3. Dựa vào giá trị tính toán của N và Q ta tra bảng 2.2 để xác định dạng sản xuất. Barng 2.2 Xác định dạng sản xuất theo khối lượng chi tiết Dạng sản xuất Khối lượng chi tiết (kg) < 4 4 Ạ 200 > 200 Sản lượng hàng năm (chiếc) Đon chiếc < 100 < 10 < 5 Loạt nhỏ 100 Ạ 500 10 Ạ 200 55ạ 10 Loạt vừa 500 Ạ 5000 200 Ạ 500 100 Ạ 300 Loạt lớn 5000 Ạ 50000 500 Ạ 1000 300 Ạ 1000 Hàng khối > 50000 > 5000 > 1000 H. PHÂN TÍCH QUÁ TRÌNH CÔNG NGHỆ HIỆN HÃNH: Hầu hết các chi tiết sẽ được thiết kế công nghệ và Đổ gá của học sinh khi làm đổ án đều đang được gia công tại các co sở sản xuất hoặc có trong tài liệu chuyên ngành. Quá trình công nghệ gia công được xây dựng trên co sở điều kiện trang thiết bị, tổ chức, kinh tế, nguổn nhân lực của co sở sản xuất cụ thể. Vì vậy có nhiều vấn đề phải phân tích đánh giá một cách nghiêm túc thì mới hoàn thiện được quá trình công nghệ phù hợp với điều kiện thiết kế cụ thể cho trong nhiệm vụ của đổ án. Phân tích quá trình công nghệ hiện hành phải được thực hiện trên quan điểm bảo đảm chất lượng sản phẩm với chi phí gia công nhỏ nhất. Học sinh phải đánh giá xem quá trình này có cho phép đảm bảo các yêu cầu đề ra trên bản vẽ chi tiết hay không, các yêu cầu đó có khả năng thực hiện trong điều kiện sản xuất cụ thể hay không. Quá trình phân tích đó thực hiện theo nội dung và trình tự sau đây: _ Mức độ hợp lý của phương pháp tạo phôi với quy mô sản xuất đã cho. _ Mức độ tương ứng của phôi với chi tiết thực, hệ số sử dụng vật liệu thế nào. _ Chọn chuẩn thô, chuẩn tinh có hợp lý không. Có tuân thủ nguyên tắc chọn chuẩn thô, chuẩn tinh, chọn chuẩn thống nhất hay không. _ Trình tự các nguyên công và các bước công nghệ có hợp lý không, có cho phép đạt độ chính xác theo điều kiện kỹ thuật trên bản vẽ thiết kế không? _ Các thông số của thiết bị đã chọn có phù hợp với yêu cầu về độ chính xác và năng suất của nguyên công không? _ Mức độ trang bị của nguyên công thế nào? _ Khả năng sử dụng các loại dụng cụ có năng suất cao, các loại vật liệu mới cho các loại dụng cụ cắt thế nào? _ Khả năng ổn định chất lượng của quá trình công nghệ gia công. _ Mức dộ tập trung nguyên công của quá trình công nghệ và các nội dung khác thế nào? Cần lưu ý đến các nguyên nhân gây phế phẩm hoặc độ không ổn định của chất lượng, tình trạng ổn định thực tế của thiết bị và các giải pháp công nghệ nhằm loại bỏ các nguyên nhân gây phế phẩm. Tóm lại phân tích đánh giá quá trình công nghệ hiện hành là một phần rất quan trong là cơ sở cho phương án đã được chọn sau này. HI. CHỌN PHÔI VẢ PHƯƠNG PHÁP TẠO PHÔI: Hưóng dẫn chung khi chọn phôi: Phương pháp tạo phôi phụ thuộc vào rất nhiều vấn đề như chức năng kết cấu của chi tiết máy trong cụm máy, vật liệu sử dụng, yêu cầu kỹ thuật, hình dáng bề mặt, kích thước của chi tiết, quy mô của dạng sản xuất. Chọn phôi nghĩa là chọn loại vật liệu chế tạo, phươpng pháp hình thành phôi, xác định lượng dư gia công cho các bề mặt, tính toán kích thước, dung sai cho quá trình chế tạo phôi. Chọn phôi hợp lý không phải dễ dàng. Phương án cuối cùng chỉ có thể được quyết định sau khi tính toán giá thành của phôi và giá thành của sản phẩm sau khi gia công cơ. Trong giới hạn của một đổ án của chung cấp chế tạo máy, học sinh có thể phân tích, so sánh hai phương án chế tạo phôi theo một số nội dung sau đây: + Tính kinh tế của phương án trong điều kiện sản xuất cụ thể. + Tính hợp lý của quá trình công nghệ tạo phôi. + Chất lượng của phôi. + Hệ số sử dụng vật liệu của phương pháp +Khối lượng gia công và năng suất tạo phôi x Quá trình thiết kế bản vẽ phôi trên cơ sở của bản vẽ chi tiết và phương án tạo phôi đã chọn nên thực hiện theo trình tự sau: + Chọn dạng phôi tuỳ thuộc vào đặc tính kết cấu, vật liệu, dạng sản xuất, hệ số sử dụng vật liệu yêu cầu. + Tính toán lượng dư cho các bề mặt quan trọng, tra bảng lượng dư cho các bề mặt không quan trọng. + Lập bản vẽ phôi. + Tính giá thành phôi, trong đổ án thường dùng các loại phôi như phôi đúc, phôi cán, phôi rèn, phôi dập. Phôi cán: Các dạng phôi cán, đặc tính và lĩnh vực sử dụng của chúng được cho trong bảng 2.3. Phôi cán có thể sử dụng chế tạo trực tiếp chi tiết hoặc dùng làm nguyên liệu ban đầu khi tạo phôi bằng phương pháp biến dạng dẻo. Dung sai của một số loại phôi cán nóng hình tròn cho trong bảng 2.4. Trong bảng 2.5 là dung sai của một số loại phôi cán theo cấp chính xác tương ứng. Các loại phôi cán chuyên dụng được sử dụng trong dạng sản xuất loạt và khối cho phép giảm đáng kể lượng dư và khối lượng gia công, góp phần làm giảm giá thành sản phẩm. Bảng 2.3 Các loại phôi cán và lĩnh vực sử dụng của chúng Dạng phôi cán hoặc Prôíin Lĩnh vực sử dụng Phôi cán thường: _ Cán nóng, tiết diện tròn, độ chính xác thường và cao. _ Tiết diện tròn độ chính xác cao. _ Tiết diện vuông sáu cạnh. _ Phôi cán nóng dạng tấm, độ chính xác thông thường. _ Phôi cán tinh tiết diện vuông, 6 cạnh. Chế tạo các trục bậc có độ chênh đường kính không lớn, các chi tiết dạng cốc có đường kính tới 50 mm, bạc có đường kính ngoài tới 25 mm. Các chi tiết kẹp chặt, các thanh đòn, tấm gá và thanh chêm. Phôi cán tấm: _ Phôi cán nóng có chiều dày lớn. _ Phôi tấm cán nóng và nguội có chiều dày nhỏ. Bích, vòng chặn, chi tiết phẳng, bạc rỗng hình trụ. Phôi ống các loại, cán nóng và nguội, không có mối ghép hàn. Xi lanh, bạc, ống đỡ trục chính, cốc đỡ, con lăn, trục rỗng. Prôíin có tiết diện dọc thay đổi theo chu kỳ. Trục bậc trong sản xuất loạt lớn và hàng khối. Phôi cán trên máy cán trục vít nằm ngang. Trục, bạc và các chi tiết khác trong sản xuất hàng khối và loạt lớn. Bảng 2.4 Sai lệch giới hạn của kích thước đường kính phôi thép tròn cán nống Đường kính (mm) Sai lệch giới hạn theo đường kính (mm) khi độ chính xác cán: Cao Nâng cao Thường + - + - + - 5; 5,5; 6; 6,3; 6,5; 7 đến 9 0,1 0,2 0,2 0,5 0,3 0,5 10 đến 19 0,1 0,3 0,2 0,5 0,3 0,5 20 đến 25 0,2 0,3 0,2 0,5 0,4 0,5 50; 52 đến 58 0,2 0,5 0,2 0,7 0,4 0,7 60; 62; 63; 65; 68;70; 72; 75; 78 0,2 0,8 0,2 1,0 0,4 1,0 80; 82; 85; 90; 95 0,3 0,9 0,3 1,1 0,5 1,1 100; 105; 110; 115 0,3 1,1 0,3 1,3 0,5 1,3 120; 125; 130; 135 - - 0,4 1,7 0,6 1,7 140; 150 - - 0,6 2,0 0,8 2,0 160; 170; 180; 190; 200 - - - - 0,9 2,5 210; 220; 230; 240; 250 - - - - 1,2 3,0 Chú thích: L_ chiều dài thanh thép. Thép cố đường kính tới 9 mm được cuộn, lớn hơn 9 mm để ở dạng thanh. Độ cong của phôi thanh không vượt quá 0,5% L. Theo yêu cầu của người đặt hàng phôi thanh cố thể cố độ cong không vượt quá 2%0 L. Độ cong cho phép khi cắt phôi thanh không vượt quá 3 mm cho các phôi cố đường kính tới 30 mm; 5 mm cho các phôi cố đường kính lớn hơn 30 mm. Bảng 2.5 Dung sai đường kính phôi thép cán theo cấp chính xác Đường kính (mm) Dung sai đường kính (mm) khi cấp chính xác của phôi là 7 9 10 11 12 3 + 6 0,018 0,025 0,048 0,08 0,16 6,1 + 10 0,022 0,030 0,058 0,10 0,20 10,2 + 18 0,027 0,035 0,070 0,12 0,24 18,5 + 30 0,033 0,045 0,084 0,14 0,28 31 + 50 - 0,050 0,100 0,17 0,34 52 + 65 - 0,060 0,120 0,20 0,40 67 + 80 - - - 0,20 0,40 82 + 100 - - - 0,23 0,46 3.3. Phôi rèn và phôi dập: Đặc tính và lĩnh vực sử dụng của một số loại phôi rèn và phôi dập thông thường, sử dụng khi thiết kế đổ án công nghệ trong điều kiện sản xuất hàng loạt và hàng khối được cho trong bảng 2.6. Phôi dập trên các máy dập trục khuỷu có năng suất cao hơn nhiều so với dập trên máy búa và lượng dư gia công có thể giảm bớt được 30%, tiêu hao vật liệu giảm 15%. Các chi tiết dạng trục nhỏ dần về hai phía, các loại bạc, các chi tiết có lỗ thông hoặc không thông nên tạo phôi trên máy rèn ngang. Bảng 2.6 Đặc tính và lĩnh vực sử dụng của một số loại phôi rèn và phôi dập Phương pháp tạo phôi Kích thước hoặc khối lượng Độ chính xác của phôi Độ nhám bề mặt Rz , pm Dập trên máy búa và máy ép Tới 200 kg, thành mỏng tối đa 2,5 mm - 320 + 160 Dập thô sau đó dập tinh nguội Khối lượng tới 100 kg, thành mỏng tối đa là 2,5 mm 0,05 + 0,1 mm 40 + 10 Dập và vuốt trên Khối lượng từ 0,1 đến 320 + 160 máy rèn ngang 100 kg đuờng kính phôi tới 315 mm Dập ép Đuờng kính tới 200 mm 0,2 Ạ 0,5 mm 320 Ạ 80 3.4. Phôi đúc: Phôi đúc có nhiều loại tuỳ thuộc phuơng pháp đúc, kiểu khuôn đúc. Phôi Đúc đuợc chia làm ba cấp chính xác cho cả phôi đúc bằng gang và bằng thép. Bảng 2.7 Sai lệch kích thuớc giới hạn của phôi đúc từ thép và gang xám Kích thuớc lớn nhất của phôi, mm Kích thuớc danh nghĩa của phôi cần xác định dung sai, mm Tới 50 50Ạ1 20 120ạ 260 260ạ 500 500ạ 800 800ạ 1250 1250Ạ 2000 Cấp chín 1 xác 1 Tới 120 ± 0,2 ± 0,3 - - - - - 120ạ260 ± 0,3 ± 0,4 ± 0,6 - - - - 260ạ500 ± 0,4 ± 0,6 ± 0,8 ± 1,0 - - - 500Ạ1250 ± 0,6 ± 0,8 ± 1,0 ± 1,2 ± 1,4 ± 1,6 - 1250Ạ3150 ± 0,8 ± 1,0 ± 1,2 ± 1,4 ± 1,6 ± 2,0 ± 2,5 3150Ạ5000 ± 1,0 ± 1,2 ± 1,5 ± 1,8 ± 2,0 ± 2,5 ± 3,0 Cấp chín i xác 2 Tới 260 ± 0,5 ± 0,8 ± 1,0 - - - - 260^500 ± 0,8 ± 1,0 ± 1,2 ± 1,5 - - - 5004-1250 ± 1,0 ± 1,2 ± 1,5 ± 2,0 ± 2,5 ± 3,0 - 1250^3150 ± 1,2 ± 1,5 ± 2,0 ± 2,5 ± 3,0 ± 4,0 ± 5,0 3150^6300 ± 1,5 ± 1,8 ± 22 , ± 3,0 ± 4,0 ± 5,0 ± 6,0 Chú ý: Cấp chính xác 3 chỉ dùng cho sản xuất đơn chiếc nên không cho trong bảng này. Việc đầu tiên phải làm khi chọn phôi đúc là chọn cấp chính xác của phôi theo điều kiện của cơ sở sản xuất cụ thể. Các điều kiện này bao gồm quy mô của quá trình tạo phôi, phương pháp tạo phôi, trang thiết bị của quá trình tạo phôi, trình độ tự độnh hoá của xí nghiệp. Để chọn cấp chính xác của phôi có thể sử dụng các hướng dẫn trong bảng 2.8. Cần lưu ý, tiêu chí cơ bản để quyết định cấp chính xác của phôi chính là giá thành của nó. Sự tăng giá thành của các loại phôi có độ chính xác cao sẽ được bù đắp lại trong quá trình gia công do lượng dư và khối luợng gia công giảm . Bảng 2.8 Quan hệ giữa các cấp chính xác của phôi đúc với dạng sản xuất Cấp chính xác Đặc tính sản xuất Số chi tiết trong một năm Trang bị Chế tạo Khuôn Thao đúc 1 Từ loạt lớn đến hàng khối > 10000 Mẫu kim loại, hòm khuôn kim loại có bạc dẫn để chỉnh Lắp thao đúc vào bạc dẫn bằng máy Chỉnh vị trí thao đúc bằng máy trước khi lắp ráp vị trí thao đúc. 2 Từ loạt vừa tới loạt lớn 1000 tới 10000 Mẫu và hòm khuôn kim loại Chế tạo khuôn bằng máy Thao có kích thước lớn, lắp bằng máy, thao có kích thước nhỏ lắp bằng tay IV. THIẾT KẾ Sơ BỘ TIẾN TRÌNH CÔNG NGHỆ GIA CÔNG cơ: 4.1. Khái niệm chung về quy trình công nghệ gia công cơ: Chất lượng của chi tiết máy, độ tin cậy, tuổi thọ, tính kinh tế phụ thuộc vào kết cấu, quy trình công nghệ đổ gá gia công cơ. Đặc tính kỹ thuật và độ chính xác của sản phẩm nhận được sau khi gia công cơ phụ thuộc rất nhiều yếu tố: Vật liệu, phương pháp tạo phôi, tình trạng thiết bị gia công, dụng cụ cắt, chế độ gia công, trình độ tổ chức quản lý và điều hành quy trình sản xuất x Để giải quyết mục đích cuối cùng của mọi quá trình công nghệ gia công chế tạo là tạo ra sản phẩm có chất lượng, tính năng sử dụng tốt, giá thành nhỏ, chúng ta phải giải quyết một loạt vấn đề đổng bộ. Trong đó xác định trình tự gia công hợp lý là một nhiệm vụ quan trọng bậc nhất khi thiết kế quá trình công nghệ gia công cơ. Quá trình công nghệ gia công cơ được hiểu là một tập hợp của các tác động đến phôi theo một trình tự nhất định làm thay đổi kích thước, hình dáng, trạng thái cơ lý tính của nó để tạo ra sản phẩm theo thiết kế ban đầu. Qúa trình thay đổi kích thước và hình dáng hình học của phôi được thực hiện trong quá trình gia công cơ. Còn tính chất và trạng thái cơ lý của bề mặt sẽ được biến đổi trong quá trình nhiệt luyện. Trong công nghệ thông thường, quá trình công nghệ gia công cơ được hình thành từ các nguyên công, bước công nghệ. Còn trong công nghệ gia công trên máy CNC và trung tâm gia công, quá trình công nghệ được hình thành từ các nguyên công thành phần có dạng các câu lệnh nối tiếp nhau. Các nguyên công này được hiểu là một chuyển động tương đối trọn vẹn của dụng cụ so với chi ... ình 2-7) Hình 2.8 Sự hình thành sai số chuẩn 2/ Cố gắng chọn chuẩn định vị trùng với gốc kích thước để sai số chọn chuẩn = 0 ec(A) = 0 Hình 2.9 Sơ đổ kẹp chặt khi gia công biên. 3/ Chọn chuẩn sao cho khi gia công chi tiết không bị biến dạng do lực cắt, lực kẹp. Mặt chuẩn phải đủ diện tích định vị. Ví dụ như sơ đổ kẹp chặt khi gia công biên sau: 4/ Chọn chuẩn sao cho kết cấu đổ gá đơn giản và thuận tiện khi sử dụng. 5/ Cố gắng chọn chuẩn thống nhất, có nghĩa là trong nhiều lần gá cũng chỉ dùng một chuẩn để thực hiện các nguyên công của cả quá trình công nghệ. Vì khi thay đổi chuẩn sẽ sinh ra sai số tích lũy ở những lần gá sau. Xác định các bước công nghệ gia công cho từng bề mặt và trình tự thực hiện gia công các bề mặt đó. a) Các nguyên tắc chung khi xác định trình tự gia công các bề mặt Quy trình công nghệ gia công cơ chi tiết là một bài toán nhiều phương án. Lời giải cụ thể phụ thuộc vào rất nhiều yếu tố như đặc tính kỹ thuật của sản phẩm, tính năng sử dụng của nó, loại phôi, điều kiện sản xuất, quy mô sản xuất và rất nhiều yếu tố khác. Tuy vậy, việc thiết kế các quá trình công nghệ gia công và trình tự gia công các bề mặt của chi tiết cũng có những nguyên tắc cơ bản mà nếu không tuân thủ sẽ dẫn đến những sai sót nghiêm trọng. Sau đây là một số nguyên tắc cơ bảnh khi xác định trình tự các bước và các nguyên công công nghệ gia công các bề mặt: Cần tham khảo các quy trình công nghệ chế tạo các chi tiết tương tự hoặc các chi tiết cùng nhóm có trong tài liệu tham khảo và thực tế sản xuất để tránh các sai sót lớn. Phân tích ưu nhược điểm của các quá trình công nghệ hiện hành và định hướng các thay thế sửa đổi sẽ được thực hiện với chúng. Để gia công một bề mặt trên chi tiết với các yêu cầu kỹ thuật cho trước, có thể sử dụng nhiều phương pháp gia công khác nhau. Việc chọn phương pháp gia công nào là tùy thuộc vào kết cấu, kích thuớc và trọng luợng của chi tiết, độ chính xác và chất luợng của bề mặt gia công, vật liệu và phuong pháp tạo phôi, yêu cầu về năng suất và điều kiện thiết bị của co sở sản xuất. Khi chọn so bộ phuong pháp gia công có thể tham khảo số liệu trong bảng 2.9 Bảng 2.9 Độ chính xác kinh tế và độ nhám bề mặt đạt đượcBằng các phương pháp gia công khác nhau. Phuong pháp gia công Cấp chính xác Độ nhám bề mặt Tiện thô ngoài và trong, bào thô. 12 Rz = 320 Ạ 80 mm Tiện bán tinh ngoài và trong, bào bán tinh. 11 Rz = 40 Ạ 1,25 pm Tiện tinh ngoài và trong, bào tinh. 9 Rz = 1,25 Ạ 0,63 pm Phay thô. 11 Rz = 320 Ạ 40 mm Phay tinh. 9 Rz = 40 Ạ 10 pm Khoan. 12 Rz = 40 Ạ 10 pm Khoét. 11 Rz = 40 Ạ 1,25 pm Doa thô. 9 Rz = 40 Ạ 0,63 pm Doa tinh. 7 Rz = 2,5 Ạ 0,62 pm Chuốt thô. 8 Rz = 0,63 Ạ 0,16 pm Chuốt tinh. 7 Rz = 0,32 Ạ 0,08 pm Mài thô. 9 Ạ 10 Rz = 2,5 Ạ 0,63 pm Mài bán tinh. 7 Rz = 0,63 Ạ 0,16 pm Mài tinh. 5 Ạ 6 Rz = 0,32 Ạ 0,08 pm Mài khôn thô. 6 Rz = 0,32 Ạ 0,08 pm Mài khôn tinh. 5 Rz = 0,16 Ạ 0,04 pm Nghiền thô. 6 Rz = 2,5 Ạ 0,32 pm Nghiền bán tinh. 5 Rz = 0,63 Ạ 0,16 pm Nghiền tinh. 5 Rz = 0,32 Ạ 0,04 pm Xọc răng, phay răng thô. 11 Rz = 40 Ạ 1,25 pm Xọc răng, phay răng tinh. 6 Rz = 2,5 Ạ 0,63 pm Cà răng. 6 Rz = 0,63 mm Trong bảng 2.10 là độ chính xác kinh tế và độ nhám bề mặt có thể đạt được khi gia công mặt tròn ngoài theo các phương án gia công khác nhau. Số liệu về độ chính xác và độ nhám bề mặt của các phương pháp sử dụng để gia công các loại bề mặt khác nhau và trình tự thực hiện các bước công nghệ khác nhau có thể tham khảo trong các bảng 2.11; 2.12; 2.13; 2.14 Bảng 2.10 Độ chính xác kinh tế và độ nhám bề mặt khỉ gia công mặt tròn ngoài. Phương pháp gia công Cấp chính xác Độ nhám Rz (pm) Tiện một lần. 12 6,3 Tiện bán thô. 11 Ạ 10 3,2 Tiện tinh. 10 Ạ 9 3,2 Tiện thô một lần. Mài thô một lần. 10 Ạ 8 1,6 Ạ 0,8 Tiện thô. Tiện tinh. Mài bán tinh một lần. 8 Ạ 6 0,8 Tiện thô. Tiện tinh. Tiện mỏng. 7 Ạ 6 0,4 Tiện thô một lần. Mài sơ bộ. 7 Ạ 6 0,4 Mài tinh. Tiện thô sơ bộ. Tiện tinh. Mài sơ bộ. Mài tinh. 6 0,4 Tiện thô sơ bộ. Tiện tinh. Mài sơ bộ. Mài mỏng. 6 Ạ 5 0,2 Tiện thô sơ bộ. Tiện tinh. Mài thô. Mài tinh. 5 0,2 Ạ 0,1 Bảng 2.11 Độ chính xác kinh tế và độ nhám bề mặt khỉ gia công mặt tròn trong. Phương pháp gia công Cấp chính xác Độ nhám Ra (pm) Trong vật liệu đặc Khoan. 12 2,5 Ạ 12,5 Khoan và khoét. 11 6,3 Ạ 3,2 Khoan và doa. 8 Ạ 9 3,2 Ạ 1,6 Khoan và chuốt. 9 Ạ 8 3,2 Ạ 0,4 Khoan, khoét và doa. 9 Ạ 8 1,6 Ạ 0,8 Khoan, doa lần 1, doa lần 2. 8 Ạ 7 1,6 Ạ 0,4 Khoan, khoét, doa lần 1, doa lần 2 8 Ạ 7 0,8 Ạ 0,4 Khoan, khoét, mài. 8 Ạ 7 0,8 Ạ 0,4 Khoan, chuốt và tống bóng. 8 Ạ 7 0,8 Ạ 0,4 Phôi có lỗ sẵn Khoét và móc lỗ. 12 6,3 Ạ 3,2 Khoan rộng lỗ. 12 2,5 Ạ 6,3 Khoét 2 lần hoặc móc lỗ qua 2 bước 11 12,5 Ạ 6,3 Khoét hoặc móc lỗ và doa 9 Ạ 8 3,2 Ạ 1,6 Khoét và móc lỗ. 9 Ạ 8 6,3 Ạ 3,2 Khoét thô, khoét tinh và doa hoặc móc lỗ qua 2 bước và doa. 9 Ạ 8 1,6 Ạ 0,8 Khoét hoặc móc lỗ và doa qua 2 bước. 8 Ạ 7 0,8 Ạ 0,4 Khoét hoặc móc lỗ qua 2 bước và doa qua 2 bước hoặc tiện mỏng lỗ. 8 Ạ 7 0,8 Ạ 0,2 Khoét hoặc tiện lỗ qua 2 bước và khôn lỗ. 8 Ạ 7 0,2 Ạ 0,05 Khoét và tiện lỗ, tiện mỏng và khôn lỗ. 8 Ạ 7 0,1 Ạ 0,02 Chuốt tiên tiến và mài lỗ. 8 Ạ 7 0,8 Ạ 0,2 Bảng 2.12 Độ chính xác kinh tế và độ nhám bề mặt khỉ gia công mặtphẳng. Phưong pháp gia công Độ chính xác Độ nhám bề mặt Ra (mm) Phay bằng dao phay mặt đầu. Phay thô. 14 Ạ 11 12,5 Ạ 3,2 Phay bán tinh và phay 1 lần 12 Ạ 11 3,2 Ạ 1,6 Phay tinh. 10 1,6 Ạ 0,8 Phay mỏng. 8 Ạ 6 1,6 Ạ 0,2 Chuốt thô phôi dập và đúc. 10 Ạ 11 3,2 Ạ 1,6 Chuốt tinh. 8 Ạ 6 1,6 Ạ 0,4 Mài một lần. 8 ạ7 1,6 Ạ 0,4 Mài sơ bộ. 9 Ạ 8 0,8 Ạ 0,4 Mài tinh. 7 0,4 Ạ 0,1 Mài mỏng. 6 0,2 Ạ 0,05 Bảng 2.13 Độ chính xác kinh tế và độ nhám bề mặt khỉ gia công ren. Phương pháp gia công Dung sai (độ chính xác) Độ nhám Ra (mm) Dùng dao cán tròn khi tạo ren thủ công. 8g 12,5 Ạ 6,3 Tạo ren bằng tarô. 6g 6,3 Ạ 3,2 Phay bằng dao phay đĩa. 6g 6,3 Ạ 1,6 Phay bằng dao phay lăn răng. 6g 6,3 Ạ 3,2 Tiện bằng dao tiện thường. 4h 3,2 Ạ 0,8 Tiện bằng dao răng lược. 6g 6,3 Ạ 0,8 Tiện bằng phương pháp gió lốc. 6g 3,2 Ạ 1,6 Tiện bằng đầu dao tự điều chỉnh đường kính. 4h 3,2 Ạ 1,6 Cán ren bằng đầu cán phẳng. 6g 0,8 Ạ 0,4 Cán ren bằng con lăn cán tròn. 6g Ạ 4h 0,8 Ạ 0,2 Bảng 2.14 Độ chính xác kinh tế và độ nhám bề mặt khi gia công răng. Phương pháp gia công Cấp chính xác Độ nhám bề mặt Ra (mm) Phay thô răng. 9 Ạ 10 12,5 Ạ 3,2 Phay tinh bằng dao phay đĩa. 8 ạ9 6,3 Ạ 1,6 Phay tinh bằng dao phay trục 7 Ạ 8 6,3 Ạ 1,6 vít. Xọc tinh. 6 Ạ 8 3,2 Ạ 0,8 Chuốt. 6 Ạ 7 3,2 Ạ 0,8 Bào tinh. 5 Ạ 7 3,2 Ạ 0,8 Cà răng. 6 Ạ 7 1,6 Ạ 0,4 Mài răng. 4 Ạ 5 0,8 Ạ 0,2 Số lượng các nguyên công và bước công nghệ gia công một bề mặt nào đó của chi tiết phụ thuộc vào yêu cầu kỹ thuật của nó (độ nhám bề mặt, độ chính xác) và phương pháp gia công đã chọn. Nếu phương pháp gia công bề mặt thay đổi, số bước và trình tự các bước cũng sẽ thay đổi. Ví dụ, để gia công mặt trụ ngoài phôi thanh có đường kính từ 30 Ạ 50 mm đạt độ chính xác cấp 9, có thể sử dụng hai phương án sau: _ Tiện thô, tiện bán tinh, tiện tinh. _ Tiện thô, mài thô. Trong trường hợp cần gia công lỗ trên phôi gang đúc đạt kích thước 055+ 0,G3. Cộ chính xác cần đạt của kích thước là cấp 7. Nếu phôi đặc thì các bước công nghệ gia công sẽ bao gồm: khoan 020; khoan 051; khoét bán tinh 054, 065; doa thô 054, doa thô 091; doa tinh 055. Tuy nhiên, nếu độ chính xác cần đạt giảm xuống cấp 8 thì các bước công nghệ gia công sẽ chỉ gồm: khoan 020, khoan 051, khoét bán tinh 054, 065; doa 055. Vì vậy khi thiết kế trình tự công nghệ, học sinh cần phải chú ý chọn phương án phù hợp nhất với điều kiện thiết kế đã cho. Mỗi phương án gia công có khả năng đảm bảo độ chính xác trong một khoảng nhất định. Với các nguyên công gia công thô, độ chính xác phụ thuộc chủ yếu vào chất lượng ban đầu của phôi, còn với các nguyên công gia công tinh độ chính xác phụ thuộc chủ yếu vào điều kiện thực hiện nguyên công, tình trạng thiết bị cụ thể. Nguyên công sau của quy trình phải nâng cao đuợc độ chính xác và độ nhẵn bóng của bề mặt so với nguyên công truớc đó. Khi gia công phôi và gia công thô, buớc hoặc nguyên công tiếp theo thuờng cho phép tăng độ chính xác gia công lên từ 2 đến 4 cấp, còn khi gia công tinh và gia công lần cuối, buớc gia công tiếp theo thuờng cho phép tăng độ chính xác lên từ 1 đến 2 cấp. Do đó việc phân chia số luợng các buớc trong một nguyên công và số luợng các nguyên công gia công từng bề mặt phải hợp lý, phù hợp với phuơng pháp đã chọn. Độ chính xác khi gia công các chi tiết từ gang và hợp kim màu bao giờ cũng cao hơn một cấp so với khi gia công các chi tiết bằng thép ở cùng điều kiện. Mặt đuợc dùng làm chuẩn công nghệ cho các nguyên công gia công các mặt còn lại phải đuợc gia công truớc tiên. Tiếp theo tiến hành gia công các bề mặt có luợng du gia công lớn nhất để kip thời phát hiện các khuyết tật phía trong và tránh ảnh huởng của lực cắt, nhiệt cắt đến các mặt gia công khác. Các nguyên công mà khi thực hiện cho phép dễ phát hiện các khuyết tật của phôi cũng nên thực hiện truớc. Thuờng thì nên gia công các bề mặt có luợng du lớn qua hai giai đoạn, thô và tinh. Gia công thô nên thực hiện truớc, gia công tinh thực hiện sau. Gia công thô đuợc thực hiện truớc sẽ tránh làm biến dạng các bề mặt có yêu cầu cao về độ chính xác và độ nhám bề mặt. Các bề mặt càng chính xác càng đuợc gia công sau. Các bề mặt yêu cầu độ chính xác cao phải đuợc gia công cuối cùng. Nếu vì một lý do nào đó, ví dụ: luợng du lớn, số luợng buớc gia công nhiều mà bề mặt này phải gia công truớc, thì sau đó nhất thiết phải đuợc gia công tinh lại lần cuối.ví dụ gia công tiện các mặt guơng của xilanh luôn đuợc thực hiện sau cùng trong các quy trình công nghệ để tránh bị ảnh huởng của lực cắt và nhiệt cắt khi thực hiện các nguyên công khác. Các lỗ nên đuợc gia công ở giai đoạn cuối cùng của quá trình công nghệ, trừ các lỗ làm chuẩn gá đặt. Không nên gia công tinh và thô bằng dao định kích thuớc trên cùng một máy(trừ các lỗ làm chuẩn khi gia công). Với các lỗ sử dụng làm chuẩn, nên khoan doa đổng thời trên cùng một máy để tránh sai số gá đặt. Với các chi tiết cần nhiệt luyện, quá trình gia công nên chia làm hai giai đoạn truớc và sau nhiệt luyện. Các nguyên công thực hiện bằng dao có luỡi thực hiện truớc khi nhiệt luyện, còn các nguyên công gia công bằng hạt mài bố trí sau nhiệt luyện. Khi thiết kế quy trình công nghệ gia công trên đuờng dây tự động phải chú ý đến các nguyên công phụ, những nguyên công phức tạp dế gây phế phẩm và nguyên công kiểm tra. Với các chi tiết có số bề mặt gia công lớn, số nguyên công và buớc công nghệ gia công từng bề mặt nhiều, xây dựng tiến trình công nghệ nên thực hiện theo trình tự sau: _ Liệt kê các bề mặt cần gia công. _ Xuất phát từ vật liệu phôi, phuơng pháp tạo phôi, năng suất gia công yêu cầu và điều kiện thiết bị cơ sở sản xuất để quyết định phuơng pháp gia công thô cho từng bề mặt. _ Xuất phát từ yêu cầu kỹ thuật trên bản vẽ chi tiết, vật liệu phôi và điều kiện thiết bị của cơ sở sản xuất để quyết định phuơng pháp gia công lần cuối cho từng bề mặt. _ Lập trình tự gia công (thứ tự các nguyên công và các buớc công nghệ) và chọn các nguyên công trung gian cho từng bề mặt. Bố trí các nguyên công trong công đoạn gia công thô, bán tinh và tinh hợp lý. _ Ghép các nguyên công của các công đoạn cùng tên của tất cả bề mặt vào cùng một nhóm. _ Quyết định thứ tự thực hiện các nguyên công trong một nhóm trên cơ sở bảo đảm nguyên tắc sử dụng chuẩn, gá đặt và các điều kiện khác. _ Lập tiến trình công nghệ với đầy đủ các nguyên công chính và phụ. b) dác định trình tự của các bước công nghệ trên nguyên công hợp lý: Khi thiết kế nguyên công cố gắng giảm bớt khối luợng gia công tới mức thấp nhất. Năng suất gia công của nguyên công phụ thuộc vào chế độ cắt, số buớc công nghệ, số đuờng chuyên dao và thứ tự thực hiện của chúng trên nguyên công. Do vậy truớc hết phải quyết định phuơng án và cấu trúc chung của nguyên công. Thông thuờng nguyên công của mỗi quá trình công nghệ gia công cơ đuợc hình thành từ một số buớc công nghệ nhất định. Mỗi buớc công nghệ lại gồm vài đuờng chuyển dao. Các buớc công nghệ có thể thực hiện tuần tự hoặc đồng thời trên máy một vị trí bằng một dụng cụ hoặc máy nhiều vị trí bằng nhiều dụng cụ đồng thời. Quyết định phuơng án gia công nào là do điều kiện của quá trình sản xuất. Trong sản xuất hàng khối, để nâng cao năng suất gia công, thông thuờng nguyên công đuợc xây dựng theo nguyên tắc gia công song song bằng nhiều dụng cụ trên máy nhiều vị trí. Còn trong sản xuất hàng loạt, nguyên công đuợc xây dựng theo nguyên tắc gia công tuần tự bằng một dụng cụ trên máy một vị trí. Tuy nhiên trong thực tế có thể kết hợp hai cấu trúc cơ bản trên cho mọi dạng sản xuất khi thiết kế nguyên công nếu điều kiện kinh tế và kỹ thuật cho phép. Số buớc công nghệ gia công và tuần tự thực hiện của chúng trên các nguyên công phụ thuộc chủ yếu vào độ chính xác cần đạt trên nguyên công đó, tình trạng phôi nhận đuợc từ nguyên công truớc. Việc thực hiện đồng thời một số buớc công nghệ sẽ đuợc quyết định bởi khả năng bố trí các dụng cụ cắt trên máy, kết cấu và độ cứng vững của chi tiết gia công. Cần lưu ý rằng các bước công nghệ có yêu cầu cao về độ chính xác và độ nhám bề mặt đôi khi được tách hẳn ra thành một nguyên công riêng biệt để thực hiện theo phương án gia công tuần tự bằng một dụng cụ trên máy một vị trí. Các nguyên công công nghệ thực hiện trên đường dây tự động thường được xây dựng theo nguyên tắc song song hoặc song song - tuần tự. Thời gian phụ lúc này chỉ gồm thời gian dịch chuyển phôi từ vị trí này sang vị trí khác, thời gian tiến và lùi nhanh dụng cụ trước và sau khi gia công. Phương án cấu trúc cuối cùng của nguyên công sẽ được chọn thông qua cách đánh giá kinh tế sơ bộ. Trong giới hạn của đồ án các loại, sinh viên chỉ cần phân tích, chọn lựa một phương án cấu trúc nguyên công để thông qua giáo viên hướng dẫn mà không phải thực hiện các tính toán kinh tế cụ thể. c) Ví dụ thiết kế trình tự nguyên công: Thiết kế trình tự nguyên công để gia công lỗ 028+0'023 trong vật liệu đặc bằng thép C45 có độ cứng 230 300 HB, độ nhám bề mặt Ra=0,5mp. Do phôi không có lỗ sẵn nên nguyên công đầu tiên là khoan. Đối với độ nhám Ra=0,5mm thì độ chính xác hình học của lỗ ước định là bình thường. Do vậy ta có các phương án như sau: + Phương án 1: Khoan lỗ 025,5; khoét bán tinh lỗ 027,75; doa thô 027,93; doa tinh lỗ 028 | Phương án 2: Khoan, khoét bán tinh; doa thô, chuốt tinh. + Phương án 3: Khoan, khoét bán tinh, doa thô, mài tinh. Chọn phương án nào là tùy thuộc vào điều kiện trạng bị của cơ sở sản xuất. Lập tiến trình công nghệ gia công cơ: Sau khi đã chọn được phương pháp gia công các bề mặt, số lượng các bước công nghệ và trình tự thực hiện theo các nguyên công, sinh viên phải tiến hành lập tiến trình công nghệ gia công theo mẫu trong bảng 2.15. Bảng 2.15 Bảng tiến trình công nghệ gia công No Tên và nội dung Nguyên công Độ chính xác cần đạt Độ nhám bề mặt cần đạt Kích thuớc gia công lớn nhất 1 2 3
File đính kèm:
huong_dan_do_an_cong_nghe_che_tao_may_chuong_2_thiet_ke_so_b.doc
pages_from_dacn2_3_6463_5187_537612.pdf