Giáo trình Vật liệu kĩ thuật (Phần 2)
CHƯƠNG 7. CÁC PHƯƠNG PHÁP NHIỆT LUYỆN THÉP
Nhiệt luyện là những quá trình công nghệ bao gồm việc nung nóng, giữ nhiệt và làm nguội
vật phẩm kim loại với mục đích thay đổi tổ chức (cấu trúc) và tính chất của chúng.
Nhiệt luyện áp dụng cho các thỏi đúc, vật đúc, bán thành phần, mối hàn, chi tiết máy và
dụng cụ các loại.
Các dạng cơ bản của nhiệt luyện bao gồm: ủ, tôi, ram và hoá già. Nếu như do kết quả của
tôi ở nhiệt độ 20 250C mà giữ được trạng thái dung dịch rắn ở nhiệt độ cao thì sự hoá bền đáng
kể của hợp kim trực tiếp sau khi tôi sẽ không xảy ra, sự hoá bền chủ yếu xảy ra khi nung trở lại ở
nhiệt độ thấp (ram) hoặc là trong thời gian giữ ở nhiệt độ 20 250C (hoá già tự nhiên)
Bạn đang xem 20 trang mẫu của tài liệu "Giáo trình Vật liệu kĩ thuật (Phần 2)", để tải tài liệu gốc về máy hãy click vào nút Download ở trên
Tóm tắt nội dung tài liệu: Giáo trình Vật liệu kĩ thuật (Phần 2)
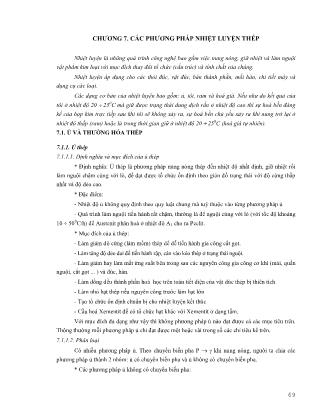
69 CHƯƠNG 7. CÁC PHƯƠNG PHÁP NHIỆT LUYỆN THÉP Nhiệt luyện là những quá trình công nghệ bao gồm việc nung nóng, giữ nhiệt và làm nguội vật phẩm kim loại với mục đích thay đổi tổ chức (cấu trúc) và tính chất của chúng. Nhiệt luyện áp dụng cho các thỏi đúc, vật đúc, bán thành phần, mối hàn, chi tiết máy và dụng cụ các loại. Các dạng cơ bản của nhiệt luyện bao gồm: ủ, tôi, ram và hoá già. Nếu như do kết quả của tôi ở nhiệt độ 20 250C mà giữ được trạng thái dung dịch rắn ở nhiệt độ cao thì sự hoá bền đáng kể của hợp kim trực tiếp sau khi tôi sẽ không xảy ra, sự hoá bền chủ yếu xảy ra khi nung trở lại ở nhiệt độ thấp (ram) hoặc là trong thời gian giữ ở nhiệt độ 20 250C (hoá già tự nhiên). 7.1. Ủ VÀ THƯỜNG HÓA THÉP 7.1.1. Ủ thép 7.1.1.1. Định nghĩa và mục đích của ủ thép * Định nghĩa: Ủ thép là phương pháp nung nóng thép đến nhiệt độ nhất định, giữ nhiệt rồi làm nguội chậm cùng với lò, để đạt được tổ chức ổn định theo giản đồ trạng thái với độ cứng thấp nhất và độ dẻo cao. * Đặc điểm: - Nhiệt độ ủ không quy định theo quy luật chung mà tuỳ thuộc vào từng phương pháp ủ - Quá trình làm nguội tiến hành rất chậm, thường là để nguội cùng với lò (với tốc độ khoảng 10 500C/h) để Austenit phân hoá ở nhiệt độ A1 cho ra Peclit. * Mục đích của ủ thép: - Làm giảm độ cứng (làm mềm) thép để dễ tiến hành gia công cắt gọt. - Làm tăng độ dẻo dai để tiến hành rập, cán vào kéo thép ở trạng thái nguội. - Làm giảm hay làm mất ứng suất bên trong sau các nguyên công gia công cơ khí (mài, quấn nguội, cắt gọt ... ) và đúc, hàn. - Làm đồng đều thành phần hoá học trên toàn tiết diện của vật đúc thép bị thiên tích - Làm nhỏ hạt thép nếu nguyên công trước làm hạt lớn - Tạo tổ chức ổn định chuẩn bị cho nhiệt luyện kết thúc - Cầu hoá Xementit để có tổ chức hạt khác với Xementit ở dạng tấm. Với mục đích đa dạng như vậy thì không phương pháp ủ nào đạt được cả các mục tiêu trên. Thông thường mỗi phương pháp ủ chỉ đạt được một hoặc vài trong số các chỉ tiêu kể trên. 7.1.1.2. Phân loại Có nhiều phương pháp ủ. Theo chuyển biến pha P khi nung nóng, người ta chia các phương pháp ủ thành 2 nhóm: ủ có chuyển biến pha và ủ không có chuyển biến pha. * Các phương pháp ủ không có chuyển biến pha: 70 Các phương pháp ủ không có chuyển biến pha có nhiệt độ ủ thấp hơn Ac1, khi đó không xảy ra chuyển biến P . + Ủ thấp (ủ non): - Định nghĩa: Ủ thấp là phương pháp ủ nung nóng thép tới nhiệt độ nhỏ hơn Ac1 để không có chuyển biến pha xảy ra. - Mục đích và đặc điểm: Ủ thấp có tác dụng làm giảm hay khử bỏ ứng suất bên trong ở các vật đúc hay các sản phẩm thép qua gia công cơ khí. +) Nếu ủ ở nhiệt độ thấp (200 3000C) chỉ có tác dụng làm giảm một phần ứng suất bên trong nhưng ở những nhiệt độ cao hơn (450 6000C) tác dụng khử bỏ ứng suất bên trong có thể hoàn toàn hơn. +) Do làm nguội nhanh, không đều, do chuyển pha khi đúc, trong vật đúc tồn tại ứng suất bên trong. Đối với một số vật đúc có yêu cầu đặc biệt không cho phép tồn tại ứng suất dư độ. Để khử bỏ hoàn toàn ứng suất dư, người ta tiến hành nung nóng đến 450 6000C + Ủ kết tinh lại: - Định nghĩa: Ủ kết tinh lại là phương pháp ủ nung nóng thép tới nhiệt độ nhỏ hơn Ac1 để không có chuyển biến pha xảy ra. - Mục đích và đặc điểm: Ủ kết tinh lại được tiến hành cho các thép qua biến dạng nguội bị biến cứng cần khôi phục lại tính dẻo, độ cứng trước khi gia công cơ khí. Nhiệt độ ủ kết tinh lại cho thép cacbon là từ 600 7000C tức là thấp hơn nhiệt độ Ac1. Loại ủ này làm thay đổi được kích thước hạt và giảm độ cứng, nhưng rất ít áp dụng cho thép vì khó tránh tạo nên hạt lớn. Các phương pháp ủ có chuyển biến pha: Các phương pháp ủ có chuyển biến pha có nhiệt độ ủ cao hơn Ac1, khi đó có xảy ra chuyển biến P . + Ủ hoàn toàn: - Định nghĩa: Ủ hoàn toàn là phương pháp ủ gồm nung nóng thép tới trạng thái hoàn toàn Austenit, tức là phải nung cao hơn nhiệt độ Ac3 hoặc Accm. - Mục đích và đặc điểm: +) Làm nhỏ hạt. Nếu chỉ nung quá nhiệt độ Ac3 khoảng 20 30 0C ứng với nhiệt độ ủ trong khoảng 780 8600C, hạt Austenit nhận được vẫn giữ được kích thước bé, sau đó làm nguội chậm có tổ chức Ferit + Peclit hạt nhỏ. Tổ chức này có độ dai tốt. +) Làm giảm độ cứng và tăng độ dẻo, dễ cắt gọt và rập nguội. Do làm nguội chậm, Austenit phân hoá ra tổ chức Ferit + Peclit (tấm) có độ cứng trong khoảng 160 200HB, bảo đảm cắt gọt tốt và dẻo, dễ rập nguội. Như vậy nhiệt độ ủ hoàn toàn là T0ủ hoàn toàn = 0 Ac3 T + (20 30)0C. Loại ủ này chỉ áp dụng cho thép trước cùng tích có hàm lượng cacbon lớn hơn hoặc bằng 0,3%C + Ủ không hoàn toàn: 71 - Định nghĩa: Là phương pháp ủ gồm nung nóng thép tới trạng thái chưa hoàn toàn là Austenit, nhiệt độ cao hơn Ac1 nhưng thấp hơn Ac3 hay Accm. - Mục đích và đặc điểm: +) Làm giảm độ cứng đến mức có thể cắt gọt được, sự chuyển biến pha ở đây là không hoàn toàn chỉ có P còn Ferit hoặc XeII vẫn còn (do vậy khi làm nguội không làm thay đổi kích thước hạt của 2 pha đó). +) Đối với thép trước cùng tích, loại thép có yêu cầu độ dai cao vì không làm nhỏ được hạt Ferit nên không áp dụng dạng ủ này. Do vậy, ủ không hoàn toàn thường được áp dụng chủ yếu cho thép cùng tích và sau cùng tích với hàm lượng cacbon > 0,7%. +) Đối với thép có hàm lượng cacbon > 0,7% mà chủ yếu là thép cùng tích và sau cùng tích (thép có độ cứng khá cao, khó cắt gọt). Nếu tiến hành ủ hoàn toàn thép này, tổ chức nhận được là Peclit tấm, độ cứng có thể lớn hơn 220HB gây cho việc cắt gọt gặp khó khăn. Nếu tiến hành ủ không hoàn toàn, thì ở nhiệt độ nung do đạt được tổ chức Austenit và các phần tử XeII chưa tan hết nên khi làm nguội, các phần tử này như là những mầm giúp cho tạo nên Peclit hạt. Sau khi ủ không hoàn toàn, thép có tổ chức Peclit hạt với độ cứng thấp hơn (khoảng 200HB) nên đảm bảo cắt gọt tốt hơn. Vậy nhiệt độ ủ không hoàn toàn cho mọi thép cacbon là: T0ủ.k.h.t = T 0 Ac1 + (20 30 0C) Dạng đặc biệt của ủ không hoàn toàn là ủ cầu hoá, trong đó nhiệt độ nung dao động tuần hoàn trên dưới A1: nung đến 750 770 0C rồi lại làm nguội xuống 650 6800C, cứ thế trong nhiều lần. Với cách làm như vậy, không những cầu hoá được Xementit của Peclit mà cả XeII thường ở dạng lưới trong thép sau cùng tích. H×nh 7.1 Ủ cầu hóa + Ủ khuếch tán: - Định nghĩa: Là phương pháp ủ gồm nung nóng thép đến nhiệt độ rất cao 1100 11500C và giữ nhiệt trong nhiều giờ (khoảng 10 15h) - Mục đích và đặc điểm: +) Tạo ra hạt quá lớn do nung lâu ở nhiệt độ cao, vì vậy chỉ áp dụng cho vật đúc trước khi gia công áp lực. Nếu không qua biến dạng dẻo để làm nhỏ hạt thì sau đó phải ủ lại bằng cách ủ hoàn toàn để làm nhỏ hạt. +) Làm đều thành phần của thép do hiện tượng thiện tích gây ra. Cách ủ này áp dụng cho các thỏi đúc bằng thép hợp kim cao, thường có hiện tượng không đồng nhất về thành phần hoá học. 30500C 3 0 5 0 0 C t lµm nguéi cïng lß 0C Ac 1 72 + Ủ đẳng nhiệt: - Định nghĩa: là phương pháp ủ gồm nung nóng thép tới nhiệt độ ủ (xác định theo là ủ hoàn toàn hay không hoàn toàn), giữ nhiệt rồi làm nguội nhanh xuống dưới A1 khoảng 50 100 0C tuỳ theo yêu cầu về tổ chức nhận được. - Mục đích và đặc điểm: +) Việc giữ nhiệt lâu trong lò ở nhiệt độ dưới A1 để Austenit phân hoá thành phần hỗn hợp Ferit + Xementit +) Thời gian giữ nhiệt tuỳ thuộc vào tính ổn định Austenit quá nguội của thép ủ ở nhiệt độ giữ đẳng nhiệt (thường giữ hàng giờ) +) Giảm độ cứng để thu được độ cứng thấp nhất ứng với tổ chức của Peclit. 7.1.2. Thường hóa thép 7.1.2.1. Định nghĩa Thường hoá là phương pháp nhiệt luyện gồm nung nóng thép đến trạng thái hoàn toàn Austenit (cao hơn Ac3 hoặc Accm); giữ nhiệt rồi làm nguội tiếp theo trong không khí tĩnh (thường kéo ra để nguội ở trên sàn) để Austenit phân hoá thành Peclit phân tán hay Xoocbit với độ cứng tương đối thấp. Nhiệt độ thường hoá là :Tth = T 0 (Ac3 hay Accm) + (20 30) 0C 7.1.2.2. Đặc điểm của thường hoá thép - So với ủ thép, thường hoá kinh tế hơn do không phải làm nguội trong lò do vậy thường được áp dụng. - Tốc độ nguội ngoài không khí tĩnh lớn hơn tốc độ nguội trong lò khi ủ, tốc độ nguội tăng tức là độ quá nguội T càng lớn do vậy hạt thu được có kích thước nhỏ hơn so với khi ủ làm cho cơ tính được tăng lên. - Tăng năng suất của quá trình công nghệ. - Với thép sau cùng tích thì phá được lưới XeII và tạo ra tổ chức phù hợp trước khi nhiệt luyện kết thúc. - Với thép có hàm lượng cacbon trung bình (%C = 0,35 0,5%) thì thường hoá tạo ra tổ chức Peclit có độ cứng tương đối cao (24 28HRC) nên có thể dùng làm nhiệt luyện kết thúc thay tôi và ram với chi tiết không quan trọng. 7.1.2.3. Các trường hợp áp dụng của thường hóa Trên cơ sở phân tích các đặc điểm của thường hoá, ta có thể thấy sử dụng thường hoá có thể đạt được các mục đích yêu cầu sau: - Đạt độ cứng thích hợp để gia công cắt gọt với thép cacbon thấp (%C < 0,25%) Đối với thép có hàm lượng cacbon > 0,3% thường tiến hành ủ còn đối với thép có hàm lượng cacbon thấp cần tiến hành thường hoá. Thép có hàm lượng cacbon thấp như vậy nếu đem ủ hoàn toàn sẽ cho độ cứng rất thấp (nhỏ hơn 140HB), thép dẻo, phoi khó gẫy, quấn lấy dao, khi 73 thường hoá sẽ cho độ cứng cao hơn (khoảng 140 180HB), thích hợp với các chế độ gia công cắt gọt. Như vậy, để đảm bảo tính gia công cắt gọt, với thép có hàm lượng cacbon < 0,25% phải thường hoá, từ 0,3 0,65% cần ủ hoàn toàn và thép có hàm lượng > 0,7% cần ủ không hoàn toàn (hoặc ủ cầu hoá). - Làm nhỏ Xementit để chuẩn bị cho nhiệt luyện kết thúc. Khi thường hoá tạo ra tổ chức Peclit phân tán hay Xementit có kích thước bé. Mặt khác, Xementit càng nhỏ biên giới hạt càng nhiều, do vậy khi Austenit hoá sẽ tạo ra nhiều mầm Austenit, nhận được hạt Austenit nhỏ mịn và chuyển biến xảy ra nhanh. Yêu cầu này rất cần thiết đối với trường hợp tôi bề mặt. - Làm mất XeII ở dạng lưới của thép sau cùng tích Nhiều trường hợp sau khi làm nguội chậm sau khi ủ thép sau cùng tích hay bề mặt thép thấm cacbon, trong tổ chức xuất hiện XeII ở dạng lưới liên tục bao quanh Peclit làm thép rất dòn và ảnh hưởng đến độ nhẵn bóng khi gia công cắt gọt. Thường hoá có thể khắc phục được trạng thái này, do làm nguội nhanh hơn, Xementit không kịp tiết ra ở dạng liền nhau mà ở dạng đứt rời, cách xa nhau làm thép ít dòn hơn, bề mặt đạt được độ nhẵn bóng cao hơn. 7.1.2.4. Nhiệt độ ủ và thường hoá thép theo giản đồ trạng thái H×nh 7.2 NhiÖt ®é ñ vµ th-êng hãa cña thÐp 7.2. TÔI THÉP 7.2.1. Định nghĩa Tôi thép là phương pháp nhiệt luyện nung thép lên cao quá nhiệt độ tới hạn (Ac1) để làm xuất hiện tổ chức Austenit, giữ nhiệt rồi làm nguội nhanh thích hợp để Austenit chuyển biến thành Mactenxit hay các tổ chức không ổn định khác với độ cứng (như Bainit, Trustit khi tôi đẳng nhiệt) và tính chống mài mòn cao. 0.2 0.4 0.6 0.8 1.0 1.2 1.4 200 400 600 800 1100 1000 U hoan toan U khong hoan toan U khuech tan U ket tinh lai t 0 % C U thap F + P P + Xe II + Xe P Thuong hoa 74 7.2.2. Đặc điểm - Phải làm nguội trong các môi trường có tốc độ nguội phù hợp (vng ≥ vng.tới hạn) - Tổ chức thu được sau khi tôi là tổ chức không ổn định nên phải kết hợp với ram để tạo tổ chức ổn định hơn. - Do tốc độ nguội nhanh, đồng thời xảy ra chuyển biến Mactenxit nên chi tiết sau khi tôi dễ tồn tại biến dạng và ứng suất dư. - Độ cứng của sản phẩm sau khi tôi phụ thuộc vào hàm lượng cacbon trong thép và tốc độ nguội (môi trường hay phương pháp làm nguội). 7.2.3. Mục đích của tôi thép - Nâng cao độ cứng và tính chống mài mòn của thép do đó kéo dài được thời gian làm việc của các chi tiết chịu mài mòn. Độ cứng của thép tôi phụ thuộc vào lượng cacbon. Thép có lượng cacbon quá thấp < 0,25% khi tôi có độ cứng không cao, không đủ chịu mài mòn. Vậy, muốn đạt được mục đích này thép tôi phải có hàm lượng cacbon trung bình và cao từ 0,3% cacbon trở lên. - Nâng cao độ bền do đó nâng cao được sức chịu tải của chi tiết máy. Nhờ tính chất này mà người ta tiến hành tôi thép cho các chi tiết máy quan trọng (chịu tải nặng, chóng mòn và gẫy), các chi tiết quyết định khả năng làm việc lâu dài của máy. Nguyên công tôi thép đóng vị trí quan trọng đặc biệt trong nhiệt luyện vì các lý do sau: +) Quyết định cơ tính của thép phù hợp với điều kiện làm việc do vậy quyết định tuổi thọ của chi tiết máy. +) Là một trong những nguyên công cuối cùng, chi tiết đã ở dạng thành phẩm. Các mục đích nêu trên chỉ đạt được bằng sự kết hợp với ram tiếp theo. 7.2.4. Tốc độ tôi tới hạn và độ thấm tôi 7.2.4.1. Tốc độ tôi tới hạn - Định nghĩa: Là tốc độ nguội nhỏ nhất cần thiết để Austenit chuyển biến thành Mactenxit với từng loại thép khác nhau. vng.tới hạn = )/( 0 . 1 sC t TAr hg o Ar1: nhiệt độ tới hạn dưới của thép T0: nhiệt độ ứng với Austenit quá nguội kém ổn định nhất Tgh: thời gian kém ổn định nhất của Austenit H×nh 7.3 Tèc ®é t«i tíi h¹n cña thÐp To τgh 75 Ý nghĩa của tốc độ tôi tới hạn: +) Tốc độ tới hạn của thép càng nhỏ thép càng dễ tôi cứng vì lúc đó chỉ cần dùng các môi trường nguội chậm cũng đủ để đạt độ cứng. +) Tốc độ tôi tới hạn của các thép khác nhau cũng khác nhau. Tốc độ tôi tới hạn phụ thuộc vào vị trí của đường cong chữ "C" hay là tính ổn định của Austenit quá nguội. Tính ổn định của Austenit quá nguội càng lớn, đường cong chữ "C" dịch sang phải càng nhiều, tốc độ tôi tới hạn càng nhỏ. Các yếu tố ảnh hường đến tốc độ tôi tới hạn: Mọi yếu tố làm tăng tính ổn định của austenit quá nguội (τgh) đều làm giảm vth. Mặt khác các yếu tố giúp cho sự tạo nên hỗn hợp Ferit – Xementit đều làm giảm tính ổn định cảu austenit và làm tăng vth. Các yếu tố đó là: 1. Sự đồng nhất của austenit. Austenit có thành phần cacbon càng đồng nhất thì càng dễ biến thành Mactenxit. Khi austenit có thành phần cacbon phân bố không đều thì dễ tạo thành hỗn hợp Ferit – Xementit hơn, trong đó vùng có cacbon cao dễ biến thành Xementit, vùng có cacbon thấp dễ biến thành Fẻit. Nâng cao nhiệt độ tôi tạo cho austenit đồng đều về thành phần cacbon sẽ nâng cao tính ổn định của austenit quá nguội. 2. Các phần tử rắn chưa tan hết vào austenit khi nung nóng như các phần tử cacbit - Xementit, làm khó khăn cho chuyển biến austenit - Mactenxit, do đó làm tăng vth. 3. Kích thước hạt austenit – như đã biết khi chuyển biến Peclit, mầm đầu tiên sinh ra ở biên giới hạt austenit, do vậy hạt austenit nhỏ với tổng biên giới hạt lớn sẽ thúc đẩy chuyển biến thành Peclit và khó chuyển biến Mactenxit. Vì thế mặc dầu hạt austenit to tạo nên các sản phẩm có tính dòn cao, nhưng tốc độ tôi tới hạn nhỏ hơn. 4. Thành phần hợp kim của austenit. Như đã trình bày sơ bộ ở trên, austenit càng chứa nhiều nguyên tố hợp kim tính ổn định của nó càng tăng, vth càng nhỏ. Do vậy thép hợp kim có vth nhỏ hơn so với thép cacbon. Lượng cacbon trong austenit cũng ảnh hưởng tới vth. Khi tăng hàm lượng cacbon vth giảm đi, tới 0.8 – 1.0%C vẫn đạt đến giá trị n ... g thời thảo mãn các yêu cầu trên. Tuy nhiên hiện nay đã có nhiều loại hợp kim làm ổ trượt tương đối tốt, được dùng nhiều trong chế tạo máy. 11.3.3. Phân loại hợp kim ổ trượt Người ta chia các hợp kim là ổ trượt ra làm hai nhóm lớn: có nhiệt độ chảy cao và nhiệt độ chảy thấp. 11.3.3.1.Hợp kim ổ trượt có nhiệt độ chảy thấp Hợp kim ổ trục trên cơ sở của kim loại có nhiệt độ chảy thấp như Sn, Pb, Al, Zn.có tên chung là babit. Nói chung các babit rất mềm nên ít làm mòn cổ trục thép, có hệ số ma sát bé và giữ dầu tốt, tuy nhiên nó không chịu được áp suất và nhiệt độ cao. Bảng sau cho biết thành phần một số loại babit thường gặp ở Việt Nam Bảng11.4: Thành phần hoá học của một số babit Loại Số hiệu Thành phần các nguyên tố % Sn Pb Sb(Ca) Cu(Na) Nguyên tố khác Babit Sn SnSb11Cu6 SnSb8Cu3 Còn lại Còn lại - 10-12 7,3-7,8 5,5-6,5 2,5-3,5 - 0,8-1,2Cd 0,15-0,25Ni Babit Pb-Ca-Na PbCaNa PbSn2 - 1,5-2,1 Còn lại Còn lại (0,95-1,15) (0,30-0,55) (0,7-0,9) (0,2-0,4) 0,05-0,2Al 0,06-0,11Mg Babit Pb-Sn PbSn16Sb16Cu2 PbSn6Sb6 PbSn10Sb14 15-17 5,5-6,5 9-11 Còn lại Còn lại Còn lại 15-17 5,5-6,5 13-15 1,5-2,0 0,1-0,3 1,5-2,0 - - 0,1-0,7Cd 0,1-0,5Ni 0,5-0,9As Babit thiếc Babit thiếc là loại babit dùng đầu tiên có ưu điểm lớn là kết hợp tốt nhất giữa cơ - lý tính và tính ít ma sát, tính chống ăn mòn cao, song nhược điểm là chứa nhiều thiếc (80-90%Sn) nên khá đắt. Thường dùng trong các ổ trượt quan trọng làm việc với tốc độ lớn và trung bình trong các tuabin hơi, máy nén kiểu tuốcbin, động cơ diêzen, ổ đỡ trục chân vịt. Các số hiệu thường dùng là SnSb8Cu3 và SnSb11Cu6 Người ta không dùng loại babit thiếc chỉ có Sn và Sb mà luôn luôn có chứa thêm một lượng Cu, sở dĩ như vậy là vì hợp kim hai nguyên Sn – Sb khi kết tinh bị thiên tích mạnh do khối lượng riêng của các pha khác nhau, nếu đưa thêm Cu vào, khi kết tinh Cu3Sn sẽ kết tinh trước ở dưới 139 dạng sao phân tán đều trong pha lỏng tạo nên xương, khung ngăn không cho pha kết tinh tiếp theo nổi lên trên. Babit chì thiếc Babit chì thiếc là loại hợp kim ổ trượt ngoài Pb và Sn còn chứa một lượng khác lớn Sb (6-15%) và một lượng nhỏ Cu (1-2%). Các số hiệu thường dùng là PbSn6Sb15Cu3Cd2, PbSn10Sb14Cu2Ni và PbSn6Sb6 PbSn6Sb15Cu3Cd2 có lượng Sn và Sb tương đối cao (15 – 17% mỗi nguyên tố) với tổ chức tế vi có nhiều các hạt cứng SnSb, Cu3Sn do đó tương đối giòn. Nó được dùng để thay thế cho SnSb11Cu6 trong điều kiện không va đập như ổ đỡ của các đầu máy chạy điện, đầu máy hơi nước, tuốc bin thuỷ lực. PbSn10Sb14Cu2Ni có lượng Sn và Sb ít hơn(9-11% Sn, 13-15%Sb) và được hợp kim hoá thêm Cd, As và Ni, trong đó Cd nâng cao tính chống ăn mòn, As cải thiện tính chảy loãng và độ bền nhiệt, Ni hoá bền dung dịch rắn , nâng cao cơ tính. Nó được dùng làm ổ trượt chịu tải trọng va đập và thay thế cho SnSb11Cu6 làm ổ trượt của động cơ đốt trong, tuốcbin hơi và máy hơi nước. Hiện nay có xu hướng dùng ngày một phổ biến PbSn6Sb6 để làm các ổ trượt cho các động cơ xăng của ô tô, máy kéo, máy công cụ làm việc trong điều kiện tải trọng va đập. So với các số hiệu trên hợp kim này rẻ tiền hơn do chứa ít Sn hơn và thoả mãn khá tốt các yêu cầu của ổ trượt. Babit kẽm Hợp kim kẽm để làm ổ trượt là hợp kim ba nguyên Zn – Cu – Al và các số hiệu thường dùng ZnAl10Cu5 và ZnAl9Cu1,5. So với các loại babit trên babit có tính dẻo thấp (δ=0,5-1%) hệ số ma sát và hệ số nở dài lớn. Ưu điểm của babit kẽm là rẻ. Babit nhôm So với các babit trên babbit nhôm là loại hợp kim ổ trượt có nhiều triển vọng hơn cả do có hệ số ma sát nhỏ, nhẹ, tính dẫn nhiệt cao, tính chống ăn mòn cao trong dầu, cơ tính cao và chống mài mòn tốt, riêng tính công nghệ tuy thua kém các loại babit khác nhưng vẫn đảm bảo yêu cầu. Công nghệ chế tạo ổ trượt bằng babit nhôm theo các bước sau: chế tạo hợp kim nhôm ở dạng băng rồi sau đó cán ép đồng thời nó với máng thép trên máy cán để tạo nên các băng kim loại ghép (bimetal), cuối cùng chế tạo ổ trượt từ băng kim loại bằng cách rập. Có thể chia các babit nhôm thành hai hệ chính: Al-Sb và Al-Sn có hệ số ma sát nhỏ, cơ tính cao nên được dùng để thay thế cho BPb30 tương đối đắt trong các động cơ diezen, hoặc được dùng làm lót trục khuỷu của động cơ đốt trong ở dạng kim loại ghép,làm ổ trượt trong tầu thuỷ và công nghiệp giao thông vận tải. 11.3.3.2.Hợp kim ổ trượt có nhiệt độ chảy cao Ưu điểm chung của hợp kim ổ trượt có nhiệt độ chảy cao là chịu được áp lực lớn do có độ bền cao (có thể làm việc trong điều kiện áp lực riêng lớn). Thường dùng brông và gang xám. Gang xám Thường dùng loại gang xám chất lượng cao với tổ chức nền kim loại là Peclit nhỏ mịn và với một lượng khá lớn graphit tấm. Tổ chức như vậy thuộc loại nền cứng, hạt mềm, ở đây các graphit có độ bền gần bằng không sẽ bóc đi, trên bề mặt tiếp xúc chừa lại “các hố” là những nơi chứa dầu bôi trơn rất tốt. ổ trượt bằng gang xám rẻ có tính chịu nén tốt nhưng tốc độ vòng quay thấp vì hệ số 140 ma sát của cặp gang – thép khá lớn (mặc dù graphit tạo ra hiệu ứng bôi trơn cho ổ trượt, nhưng không phải nhờ đó hệ số ma sát của ổ trượt gang với thép thấp như ở cacbit) Ngoài ra cũng có thể dùng gang dẻo, gang cầu với nền P và gang xám austenit để làm ổ trượt. Brông thiếc Như đã trình bày, brông thiếc dùng làm ổ trượt là loại có nền mềm là dung dich rắn và hạt cứng là cùng tích . Ưu điểm của brông thiếc là chịu được áp lực lớn và tốc độ vòng cao hơn gang xám, thường làm các ổ trượt quan trọng. Có thể dùng với các số hiệu BSn10V1 và BSn8Pb12. Trong thực tế thường dùng brông thiếc phức tạp để làm các bạc lót có yêu cầu chống mài mòn và ít ma sát. Để làm bạc lót cổ biên giữa thanh truyền và cổ biên của trục khuỷu thường dùng brông thiếc với số hiệu BSn5Zn5Pb5 (ở trạng thái đúc) và BSn4Zn4Pb2,5 (ở trạng thái biến dạng), trong đó Pb không tan trong Cu ở trạng thái rắn, ở dạng các hạt riêng rẽ làm giảm ma sát. Brông chì Brông chì có đặc điểm nổi bật là ít ma sát và hệ số dẫn nhiệt cao, ngoài ra chịu đựng tốt tải trọng và đập và chịu mỏi. Chính vì vậy brông chì được dùng làm các ổ trượt quan trọng, chịu tải cao và tốc độ lớn như ổ trượt của các động cơ máy bay, điezen, tuốcbin. Hiện nay thường dùng nhất số hiệu BPb30 với lượng chì khoảng 30%. Do Pb không tan trong Cu ở trạng thái rắn và tan hạn chế trong trạng thái lỏng do vậy khi đúc có hiện tương thiên tích do vậy để tránh hiện tượng thiên tích cần phải cho kim loại lỏng kết tinh với tốc độ nhanh để tránh hiện tương phân lớp và để các hạt Pb nhỏ phân bố đều trên nền đồng. Khi làm việc các hạt Pb bị mòn đi nhanh tạo nên rãnh chứa dầu, còn nền Cu thì đỡ lấy trục (tổ chức nền cứng hạt mềm). Cơ tính của BPb30 ở trạng thái đúc khá thấp (σb = 60N/mm 2, δ = 4%, 25HB) nên cơ tính thường được đúc tráng lên máng thép hoặc ống, rồi từ đó mới chế tạo nên ổ trượt. Hợp kim hoá thêm bằng Sn, Ni, Mn sẽ tạo nên dung dịch rắn với Cu nâng cao được độ bền của hợp kim và có thể dùng ngay không cần máng thép. Khi dùng ổ trượt bằng brông chì phải chú ý làm cổ trục thép có độ cứng cao để tránh mòn trục và dầu dùng bôi trơn phải có độ axit thấp. CÂU HỎI ÔN TẬP Câu 1: Đồng và hợp kim đồng Câu 2: Nhôm và hợp kim nhôm Câu 3: Các loại hợp kim ổ trượt. Câu 4: Đọc ký hiệu hợp kim màu 141 PHỤ LỤC Các hệ thống ký hiệu vật liệu kim loại Mỗi nước đều có tiêu chuẩn quy định các nước (ký hiệu) cũng như các yêu cầu kỹ thuật cho các sản phẩm kỹ thuật của mình và có cách viết tên ký hiệu (mác) khác nhau. Ngoài tiêu chuẩn Việt Nam như đã trình bày, chúng ta thường gặp tiêu chuẩn quốc tế của các nước lớn trên thế giới: Mỹ, Nhật Bản, Nga, Trung Quốc, Pháp, Đức, Anh....và của EU Tổ chức tiêu chuẩn quốc tế ISO (International Standard Organization) tuy có đưa ra bộ tiêu chuẩn nhưng quá muộn so với các nước công nghiệp phát triển vì họ đưa ra hệ thống ký hiệu từ trước và đã quen dùng không dễ gì thay đổi; vì thế chỉ có tác dụng đối với các nước đang phat triển đang xây dựng tiêu chuẩn, Tiêu chuẩn Nga ГOCT, Trung Quốc GB có phần quen thuộc ở nước ta. Do các quan hệ lịch sử tiêu chuẩn Việt Nam và Trung Quốc đều được xây dựng trên nguyên tắc của ГOCT. Đối với thép cán thông dụng: - Các loại thép chỉ quy định (bảo đảm) cơ tính: ГOCT có các mác từ CT0 đến CT6, GB: A1 đến A7 (con số chỉ cấp độ bền tăng dần. Để phân biệt thép sôi, nửa lặng và lặng sau các mác của ГOCT có đuôi KП, ПC, CП; của GB có đuôi F,b (thép lặng không có đuôi)). - Các loại thép quy định bảo đảm thành phần: ГOCT có mác từ БCT0 đến БCT6, GB: B1 đến B7 - Các loại thép quy định (bảo đảm) cả cơ tính lẫn thành phần: ГOCT có các mác BCT1 đến BCT5; GB có từ C2 đến C5 Đối với thép cacbon chế tạo máy ГOCT và GB có ký hiệu giống hệt nhau: theo số phần vạn cacbon, ví dụ mác 45 là thép có trung bình 0,45%C. Đối với thép cacbon chế tạo máy ГOCT có các mác từ Y7 đến Y13, GB có ký hiệu từ T7 đến T13 (chỉ số phần nghìn cacbon trung bình) Đối với thép hợp kim có cả chữ (chỉ nguyên tố hợp kim) lẫn số (chỉ lượng cacbon và nguyên tố hợp kim) theo nguyên tắc: - Hai số đầu chỉ phần vạn cacbon (nếu không nhỏ hơn 1%C thì không cần) - Tiếp theo là ký hiệu của từng nguyên tố và số chỉ phần trăm của nó (nếu gần 1% hay không nhỏ hơn 1% thì không cần) ГOCT dùng các chữ cái Nga để ký hiệu nguyên tố hợp kim như sau: X chỉ Crom, H: Niken, B: Volfram, M: Molipden, T: Titan, K: Coban, C: Silic, Г: Mangan, P: bo, Ю: Nh«m, Д: ®ång, Б: niobi, Ц: zieccon, A: nit¬, Ч: ®Êt hiÕm (riêng chữ A sau cùng chỉ thép có chất lượng cao ít P, S) GB dùng chính ký hiệu hóa học để biểu thị từng nguyên tố Đối với hợp kim màu ГOCT ký hiệu như sau: - Д chỉ dduarra tiếp theo là số thứ tự, AД chỉ hợp kim nhôm đúc tiếp sau là số thứ tự. - Л chỉ la tông, tiếp sau là chỉ số phần trăm đồng, Бp chỉ brong tiếp sau là dãy nguyên tố hợp kim và dãy số chỉ phần trăm của các nguyên tố tương ứng. 142 GB chỉ ký hiệu hợp kim màu như sau: - LF hợp kim nhôm không gỉ, LY: duyra (cả hai loại tiếp theo sau là số thứ tự), ZL: hợp kim nhôm đúc với ba số tiếp sau (trong đó số đầu tiên chỉ loại) - H: chỉ latong tiếp theo sau là chỉ số phần trăm đồng; Q chỉ brong tiếp sau là nguyên tố hợp kim chính, số chỉ phần trăm của nguyên tố chính, số chỉ phần trăm của nguyên tố chính và tổng các nguyên tố khác. Đối với gang ГOCT ký hiệu như sau: - CЧ: chỉ gang xám và số tiếp theo chỉ σb (kG/mm 2), BЧ chỉ gang cầu và số tiếp theo chỉ σb (kG/mm2), KЧ chỉ gang dẻo với các chỉ số chỉ σb (kG/mm 2) và φ (%). GB ký hiệu gang như sau: - HT cho gang xám và số tiếp theo chỉ b (MPa), QT cho gang cầu và các số chỉ σb (MPa) và φ (%). KTH cho gang dẻo ferit, KTZ cho gang dẻo peclit và các số tiếp theo chỉ σb (MPa) và φ (%). Mỹ là nước có rất nhiều hệ thống tiêu chuẩn nên phức tạp, song có ảnh hưởng lơn đối với thế giới. Ở đây trình bày hệ tiêu chuẩn thường được dùng nhất đối với từng loại vật liệu kim loại. Đối vơi thép cán nóng thường dùng ASTM (American Society for Testing and Materials) ký hiệu theo các số (42,50,60,65) chỉ σ0,2 min (ksi) Đối với thép HSLA thường dùng SAE (Society for Automotive Engineers) ký hiệu bắt đầu bằng con số 9 và hai số tiếp theo chỉ b 0,2 min (ksi) Đối với thép cacbon và thép hợp kim kết cấu cho chế tạo máy thường dùng hệ thống AISI/SAE với bốn số trong đó hai số dầu chỉ loại thép, hai số cuối cùng chỉ phần vạn cacbon: 10xx thép cacbon 4xxx thép Mo 11xx thép dễ cắt có S 5xxx thép Cr 12xx thép dễ cắt có S và P 6xxx thép Cr-V 13xx thép Mn (1,00-1,765%) 7xxx thép W-Cr 2xxx thép Ni 8xxx thép Ni-Cr-Mo 3xxx thép Ni-Cr 9xxx thép Si-Mn xxBxx thép B xxLxx thép chứa Pb Muốn biết thành phần cụ thể phải tra bảng Nếu thép được đảm bảo bằng độ thấm tôi thì đằng sau ký hiệu thêm chữ H Đối với thé dụng cụ thông thường dùng hệ thống của AISI (American Iron and Steel Institute) được ký hiệu bằng một chữ cái chỉ đặc điểm của thép và số chỉ thứ tự quy ước: M thép gió molipden T thép gió vonfram (tungsten) H thép làm khuôn rập nóng (hot work) A thép làm khuôn dập nguội hợp kim trung bình tự tôi, tôi trong không khí D thép làm khuôn rập nguội crom và cacbon cao O thép làm khuôn rập nguội tôi dầu S thép làm dụng cụ chịu va đập 143 L thép dụng cụ hợp kim thấp P thép làm khuôn nhựa cacbon thấp W thép dụng cụ cacbon tôi nước Đối với thép không gỉ tiêu chuẩn AISI không những thịnh hành ở Mỹ mà cũng được nhiều nước đưa vào tiêu chuẩn của mình, nó được ký hiệu bằng ba chữ số trong đó bắt đầu bằng 2 hoặc 3 là thép austenit, bằng 4 là thép ferit hay mactenxit Đối với hợp kim nhôm, tiêu chuẩn AA Aluminum Ascolation có uy tín nhất ở Mỹ và trên thế giới cũng được nhiều nước chấp nhận, nó ký hiệu bằng bốn chữ số đối với loại biến dạng: 1xxx lớn hơn 99%Al 5xxx Al-Mg 2xxx Al-Cu 6xxx Al-Si-Mg 3xxx Al-Mn 7xxx Al-Zn 4xxx Al-Si 8xxx Al-nguyờn tố khác Hợp kim nhôm đúc cũng có bốn chữ số song trước số cuối (thường là số 0) có dấu chấm: 1xx.0 nhôm sạch thương phẩm 2xx.0 Al-Cu 3xx.0 Al-Si-Cu (Mg) 4xx.0 Al-Si 5xx.0 Al-Mg 7xx.0 Al-Zn 8xx.0 Al-Sn Đối với hợp kim đồng người ta dùng hệ thông CDA (Copper Development Association): 1xx không nhỏ hơn 99%Cu (riêng 19x lớn hơn 97% Cu) 2xx Cu-Zn 3xx Cu-Zn-Pb 4xx Cu-Zn-Sn 5xx Cu-Sn 60x-64x Cu-Al và Cu-Al- nguyên tố khác 65x-69x Cu-Si và Cu-Zn- nguyên tố khác 7xx Cu-Ni và Cu-Ni- nguyên tố khác Nhật Bản chỉ dùng một tiêu chuẩn JIS (Japanese Industrial Standards) với đặc điểm là toàn dùng hệ đo lường quốc tế, cụ thể là ứng suất theo Mpa Tất cả các thép đều bắt đầu bằng chữ S Thép cán thông dụng được ký hiệu bằng chỉ số giới hạn bền kéo hay giới hạn chảy thấp nhất (tuy từng loại). SS – thép cán thường có tác dụng chung, SM thép cán làm kết cấu hàn, nếu thêm chữ A là SMA – thép chống ăn mòn trong khí quyển, SE – thép tấm làm nồi hơi. Thép cacbon để chế tạo máy: SxxC hay SxxCK trong đó xx chỉ phần vạn cacbon trung bình (chữ K ở cuối là loại cú chất lượng cao: lượng P, S không lớn hơn 0,025%). Thép hợp kim để chế tạo máy gồm hệ thống chữ và số: 144 - Bắt đầu bằng SCr – thép crom, SMn – thép Mn, SNC – thép niken-crom, SNCM – thép niken-crom-molipden, SCM – thép crom-molipden, SACM – thép nhôm-crom-molipden, SMnC – thép mangan-crom. - Tiếp theo là ba chữ số trong đó hai chữ cuối cùng chỉ phần vạn cacbon trung bình. Thép dễ cắt được ký hiệu bằng SUM, thép đàn hồi SUP, thép ổ lăn – SUJ và số thứ tự. Thép dụng cụ cắt bắt đầu bằng chữ SK và số thứ tự: SKx – thép dụng cụ cacbon SKHx – thép gió SKSx – thép làm dao cắt và khuôn rập nguội SKD và SKT – thép làm khuôn rập nóng, đúc áp lực Thép không gỉ được ký hiệu bằng SUS và số tiếp theo trùng với số của AISI, thép chịu nhiệt được ký hiệu bằng chữ SUH. Gang xám được ký hiệu bằng FCxxx, gang cầu FCDxxx, gang dẻo – FCMBxxx, trắng – FCMWxxx, peclit – FCMPxxx, các số xxx đều chỉ giới hạn bền. Các hợp kim nhôm và đồng có nhóm số lấy theo AA và CDA với phía trước có A (chỉ nhôm), C (chỉ đồng)
File đính kèm:
giao_trinh_vat_lieu_ki_thuat_phan_2.pdf