Giáo trình Dung sai lắp ghép và đo lường kỹ thuật (Phần 1)
MỤC TIÊU MÔN HỌC.
Học xong môn học này người học có khả năng:
- Giải thích đúng các ký hiệu, các quy ước về dung sai (sai lệch) trên bản vẽ chi
tiết, bản vẽ lắp mối ghép.
- Lựa chọn các kiểu lắp ghép phù hợp yêu cầu làm việc của mối ghép.
- Tính toán các sai lệch, dung sai của chi tiết, mối ghép.
- Liệt kê đầy đủ các quy ước về vẽ lắp các mối ghép thường dùng trong chế tạo
máy.
- Trình bày đúng cấu tạo, nguyên lý làm việc, cách sử dụng dụng cụ đo thường
dùng trong chế tạo máy.
- Đo các kích thước trên chi tiết bằng dụng cụ đo phù hợp.
- Bảo đảm an toàn, vệ sinh công nghiệp trong quá trình đo lường.
- Độc lập, sáng tạo trong quá trình thực hiện công việc đo lường.
Bạn đang xem 20 trang mẫu của tài liệu "Giáo trình Dung sai lắp ghép và đo lường kỹ thuật (Phần 1)", để tải tài liệu gốc về máy hãy click vào nút Download ở trên
Tóm tắt nội dung tài liệu: Giáo trình Dung sai lắp ghép và đo lường kỹ thuật (Phần 1)
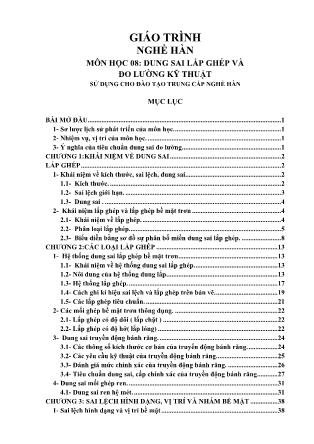
GIÁO TRÌNH NGHỀ HÀN MÔN HỌC 08: DUNG SAI LẮP GHÉP VÀ ĐO LƯỜNG KỸ THUẬT SỬ DỤNG CHO ĐÀO TẠO TRUNG CẤP NGHỀ HÀN MỤC LỤC BÀI MỞ ĐẦU................................................................................................................. 1 1- Sơ lược lịch sử phát triển của môn học. .............................................................. 1 2- Nhiệm vụ, vị trí của môn học. .............................................................................. 1 3- Ý nghĩa của tiêu chuẩn dung sai đo lường.......................................................... 1 CHƯƠNG 1:KHÁI NIỆM VỀ DUNG SAI ................................................................. 2 LẮP GHÉP ..................................................................................................................... 2 1- Khái niệm về kích thước, sai lệch, dung sai........................................................ 2 1.1- Kích thước. .................................................................................................... 2 1.2- Sai lệch giới hạn. ........................................................................................... 3 1.3- Dung sai . ....................................................................................................... 4 2- Khái niệm lắp ghép và lắp ghép bề mặt trơn .................................................... 4 2.1- Khái niệm về lắp ghép. ................................................................................. 4 2.2- Phân loại lắp ghép......................................................................................... 5 2.3- Biểu diễn bằng sơ đồ sự phân bố miền dung sai lắp ghép. ....................... 8 CHƯƠNG 2:CÁC LOẠI LẮP GHÉP ....................................................................... 13 1- Hệ thống dung sai lắp ghép bề mặt trơn .......................................................... 13 1.1- Khái niệm về hệ thống dung sai lắp ghép. ................................................ 13 1.2- Nôi dung của hệ thống dung lắp. ................................................................ 13 1.3- Hệ thống lắp ghép. ....................................................................................... 17 1.4- Cách ghi kí hiệu sai lệch và lắp ghép trên bản vẽ. .................................... 19 1.5- Các lắp ghép tiêu chuẩn. ............................................................................. 21 2- Các mối ghép bề mặt trơn thông dụng. ............................................................ 22 2.1- Lắp ghép có độ dôi ( lắp chặt ) ................................................................... 22 2.2- Lắp ghép có độ hở( lắp lỏng) ...................................................................... 22 3- Dung sai truyền động bánh răng. ..................................................................... 24 3.1- Các thông số kích thước cơ bản của truyển động bánh răng. ................. 24 3.2- Các yêu cầu kỹ thuật của truyền động bánh răng. ................................... 25 3.3- Đánh giá mức chính xác của truyền động bánh răng. ............................. 26 3.4- Tiêu chuẩn dung sai, cấp chính xác của truyền động bánh răng ............ 27 4- Dung sai mối ghép ren. ....................................................................................... 31 4.1- Dung sai ren hệ mét. .................................................................................... 31 CHƯƠNG 3: SAI LỆCH HÌNH DẠNG, VỊ TRÍ VÀ NHÁM BỀ MẶT ................ 38 1- Sai lệch hình dạng và vị trí bề mặt .................................................................... 38 1.1- Khái niệm chung. ......................................................................................... 38 1.2- Sai lệch hình dạng. ....................................................................................... 38 1.3- Sai lệch vị trí các bề mặt. ............................................................................ 42 1.4- Cách ghi kí hiệu trên bản vẽ. ...................................................................... 44 1.5- Xác định dung sai hình dạng và vị trí bề mặt. .......................................... 46 2- Nhám bề mặt ....................................................................................................... 47 2.1- Bản chất nhám bề mặt ................................................................................ 47 2.2- Chỉ tiêu đánh giá nhám bề mặt .................................................................. 47 2.3- Xác định giá trị thông số cho phép của nhám bề mặt .............................. 48 2.4- Ghi ký hiệu thông số nhám bề mặt trên bản vẽ. ....................................... 48 3- Ghi kích thước cho bản vẽ chi tiết. .................................................................... 51 3.1- Quy định chung ............................................................................................ 51 3.2- Đường kích thước và đường gióng ............................................................. 51 3.3- Chữ số kích thước ........................................................................................ 53 3.4- Các ký hiệu ................................................................................................... 54 CHƯƠNG 4: CÁC DỤNG CỤ ĐO LƯỜNG THÔNG DỤNG TRONG CHẾ TẠO MÁY .............................................................................................................................. 57 1- Dụng cụ đo có độ chính xác thấp. ...................................................................... 57 2- Dụng cụ đo dạng thước cặp. .............................................................................. 58 2.1- Công dụng. ................................................................................................... 58 2.2- Cấu tạo. ......................................................................................................... 58 2.3- Cách đọc kết quả.......................................................................................... 59 3. Dụng cụ đo dạng panme. .................................................................................... 60 3.1. Panme đo ngoài. ........................................................................................... 60 3.2- Panme đo trong. ........................................................................................... 64 4. Dụng cụ đo dạng đồng hồ so............................................................................... 65 4.1- Công dụng. ................................................................................................... 65 4.2- Cách sử dụng. ............................................................................................... 66 4.3- Cách bảo quản. ............................................................................................ 66 5. Các dụng cụ đo kiểm khác. ................................................................................. 67 5.1- Căn mẫu. ....................................................................................................... 67 5.2- Calíp. ............................................................................................................ 69 Phụ lục 1: Dung sai lắp ghép bề mặt trơn ................................................................. 73 GIÁO TRÌNH MÔN HỌC DUNG SAI LẮP GHÉP VÀ ĐO LƯỜNG KỸ THUẬT Mã môn học: MH08 Thời gian môn học: 45h (Lý thuyết: 24h, Thực hành: 21h) MỤC TIÊU MÔN HỌC. Học xong môn học này người học có khả năng: - Giải thích đúng các ký hiệu, các quy ước về dung sai (sai lệch) trên bản vẽ chi tiết, bản vẽ lắp mối ghép. - Lựa chọn các kiểu lắp ghép phù hợp yêu cầu làm việc của mối ghép. - Tính toán các sai lệch, dung sai của chi tiết, mối ghép. - Liệt kê đầy đủ các quy ước về vẽ lắp các mối ghép thường dùng trong chế tạo máy. - Trình bày đúng cấu tạo, nguyên lý làm việc, cách sử dụng dụng cụ đo thường dùng trong chế tạo máy. - Đo các kích thước trên chi tiết bằng dụng cụ đo phù hợp. - Bảo đảm an toàn, vệ sinh công nghiệp trong quá trình đo lường. - Độc lập, sáng tạo trong quá trình thực hiện công việc đo lường. NỘI DUNG MÔN HỌC - Nội dung tổng quát và phân phối thời gian: Số TT Tên chương mục Thời gian Tổng số Lý thuyết Bài tập thực hành Kiểm tra (LT hoặc TH) 1 Mở đầu 1 1 0 0 1 Khái niệm về dung sai lắp ghép 5 4 1 0 2 Các loại lắp ghép 13 8 4 1 3 Sai lệch hình dạng,vị trí và nhám bề mặt 5 3 1 1 4 Các dụng cụ đo lường thông dụng trong chế tạo máy. 21 7 13 1 Tổng cộng 45 23 19 3 1 BÀI MỞ ĐẦU Thời gian(giờ) Tổng số Lý thuyết Thực hành 1 1 0 MỤC TIÊU Học xong bài này người học có khả năng: Trình bày được sự ra đời và phát triển của môn học, nội dung nghiên cứu, tính chất và nhiệm vụ, vai trò, vị trí môn học đối với người thợ cơ khí hàn. NỘI DUNG 1- Sơ lược lịch sử phát triển của môn học. Môn dung sai lắp ghép sau khi nền đại công nghiệp triển. Nhu cầu của con người là chi tiết máy chế tạo phải đạt được yêu cầu về độ chính xác và thỏa mãn tính lắp lẫn. Để đạt được tính lắp lẫn người ta cần đưa ra một tiêu chuẩn thống nhất để các nước thực hiện. Trên thế giới, trước chiến tranh thế giới thứ 2 có một số nước thiết lập các tiêu chuẩn thông nhất về dung sai(ISA). Tổ chức này ngày càng có nhiều nước tham gia và sau đổi tên thành (ISO) là tiêu chuẩn Quốc tế hiện nay mà đại đa số các nước trên thế giới đều sử dụng tiêu chuẩn quốc tế (ISO). Năm 1963 ở Việt Nam TCVN về dung sai lắp ghép được ban hành dựa trên cơ sở tiêu chuẩn nhà nước Liên Xô(OCT). Các nước trên thế giới đều dùng tiêu chuẩn (OCT) gồm: Bungari, Mông Cổ, Trung Quốc, Triều Tiên. Để đáp ứng với thực tế sản xuất ngày càng phát triển, các nước trong cộng đồng tương trợ kinh tế (Khối CĐB) đã ban hành tiêu chuẩn thống nhất về dung sai lắp ghép (1975). Năm 1977, Viêt Nam biên soạn TCVN về dung sai lắp ghép mới, năm 1979 đưa vào sử dụng thay thế tiêu chuẩn đã ban hành năm 1963. Năm 1999 Cập nhật và bổ xung một số tiêu chuẩn mới cho phù hợp với thực tế sản xuất. 2- Nhiệm vụ, vị trí của môn học. Nhiệm vụ của môn dung sai lắp ghép và đo lường kỹ thuật giúp cho chúng ta khi thiết kế, chế tạo và sửa chữa sản phẩm đạt được yêu cầu chức năng làm việc của chi tiết một cách hợp lý nhất. Đây là môn học không thể thiếu đối với người công nhân cũng như kỹ thuật viên vì nó giúp ta quản lý được tiêu chuẩn chất lượng sản phẩm trong quá trình sản xuất. 3- Ý nghĩa của tiêu chuẩn dung sai đo lường. Tiêu chuẩn dung sai đo lường phản ánh trình độ phát triển khoa học kỹ thuật, là thước đo sự tiến bộ khoa học, kỹ thuật, trình độ công nghệ và kỹ thuật sản xuất. Vì vậy, cần được sự quan tâm của thế giới để có hệ tiêu chuẩn về dung sai lắp ghép chung (ISO). 2 CHƯƠNG 1:KHÁI NIỆM VỀ DUNG SAI LẮP GHÉP Thời gian (giờ) Tổng số Lý thuyết Thực hành 5 4 1 MỤC TIÊU Học xong bài này người học có khả năng: - Hiểu được những kiến thức cơ bản về dung sai lắp ghép, những kiến thức về dung sai kích thước trong gia công cơ khí. - Nhận thức được tầm quan trọng của kích thước trên bản vẽ. - Biết cách hiểu diễn bằng sơ đồ sự phân bố miền dung sai của lắp ghép. NỘI DUNG 1- Khái niệm về kích thước, sai lệch, dung sai 1.1- Kích thước. - Kích thước là giá trị bằng số của đại lượng đo chiều dài theo đơn vị đo được lựa chọn. Trong chế tạo máy đơn vị đo thường dùng là mm. 1m = 1000mm; 1mm = 1000µm 1.1.1- Kích thước danh nghĩa. Là kích thước được xác định bằng tính toán dựa trên cơ sở chức năng của chi tiết, sau đó quy tròn (về phía lớn hơn) theo các giá trị của dãy kích thước thẳng danh nghĩa tiêu chuẩn. a) b) Hình 1.1 – Hình biểu diễn kích thước danh nghĩa Kích thức danh nghĩa của chi tiết trục được kí hiệu là dn (hình 1.1a) Kích thước danh nghĩa của chi tiết lỗ được kí hiệu là DN (hình 1.1b) Kích thước danh nghĩa được ghi trên bản vẽ dùng làm gốc để tính các sai lệch kích thức. 1.1.2- Kích thước thực. 3 Là kích thước nhận được kết quả đo trên chi tiết gia công với sai số cho phép. Ví dụ: khi đo kích thước trục bằng thước cặp có độ chính xác là 1/20, kết quả đo nhận được là 28,25mm tức là kích thước thực của trục là dt = 28,25mm với sai số cho phép là ±0,05mm. Kích thước thực được ký hiệu là dt đối với trục và Dt đối với lỗ. 1.1.3- Kích thước giới hạn. Để xác định phạm vi cho phép của sai số chế tạo kích thước, người ta quy định hai kích thước giới hạn: Kích thước giới hạn lớn nhất là kích thước lớn nhất cho phép khi chế tạo chi tiết, ký hiệu đối với trục dmax và đối với lỗ Dmax Kích thước giới hạn nhỏ nhất là kích thước nhỏ nhất cho phép khi chế tạo chi tiết, ký hiệu đối với trục dmin và đối với lỗ Dmin Vậy điều kiện để kích thước của chi tiết sau khi chế tạo đạt yêu cầu là: dmin ≤ dt ≤ dmax Dmin ≤ Dt ≤ Dmax 1.2- Sai lệch giới hạn. Là hiệu đại số giữa các kích thước giới hạn và kích thước danh nghĩa. 1.2.1- Sai lệch giới hạn lớn nhất (sai lệch giới hạn trên) Là hiệu đại số giữa kích thước giới hạn lớn nhất và kích thước danh nghĩa, sai lệch giới hạn trên được ký hiệu là es, ES. Với trục: es = dmax – dN ES = Dmax – DN Hình 1.2 - Sơ đồ biểu diễn kích thước giới hạn và sai lệch giới hạn 1.2.2- Sai lệch giới hạn nhỏ nhất (sai lệch giới hạnh dưới) Là hiệu đại số giữa kích thước giới hạn nhỏ nhất và kích thước danh nghĩa, sai lệch giới hạn nhỏ nhất được ký hiệu là ei, EI. Với trục: ei = dmin - dN với lỗ: 4 EI = Dmin – DN Sai lệch giới hạn có thể có giá trị dương “+”, âm “-”, hoặc băng “0”/ * Sai lệch giới hạn được ghi bên cạnh kích thước danh nghĩa với cỡ chữ nhỏ hơn: D ví dụ: 50 020,0 041,0 1.3- Dung sai . Là phạm vi cho phép của sai số kích thước. Trị số dụng sai bằng hiệu số giữa kích thước giới hạn lớn nhất và kích thước giới hạn nhỏ nhất, hoặc là hiệu sai số giữa sai lệch giữa sai trên và sai lệch dưới. Dung sai được kí hiệu là T (Tolerance) Dung sai kích thước trục: Td = dmax - dmin Hoặc Td = es – ei Dung sai kích thước lỗ: TD = Dmax – Dmin Hoặc: TD = ES = EI Dung sai luôn luôn có giá trị dương. Trị số dung sai càng nhỏ thì độ chính xác kích thước càng cao. Trị số dung sai càng lớn thì độ chính xác kích thước càng thấp. Ví dụ: Biết kích thước của chi tiết lỗ là : 50 mm Tính các kích thước giới hạn và dung sai. Kích thước thực của lỗ sau khi gia công đo được là: Dt = 49,950 mm, hỏi chi tiết lỗ đã gia công có đạt yêu cầu không? Giải: Kích thước giới hạn lớn nhất của lỗ: Dmax = DN + ES = 50 + 0,020 mm Kích thước giới hạn nhỏ nhất của lỗ: Dmin = DN + EI = 50 +- 0,041 = 49,59mm Dung sai của lỗ: TD = ES – EI = 0,020 – (- 0,041) Chi tiết lỗ đạt yêu cầu khi kích thước thực của nó thỏa mãn: Dmin ≤ Dt ≤ Dmax Ta thấy: Dmin = 49,959 > Dt = 49,950 Vậy chi tiết lỗ đã gia công không đạt yêu cầu. * Khi gia công thì người thợ phải nhẩm tính các kích thước giới hạn rồi đối chiếu ... ển động trong hợp tốc độ của động cơ máy bay, ô tô, tua bin Bánh răng trong truyển động thường có mô đun trung bình, chiều dài răng lớn, tốc độ vòng của bánh răng có thể đạt tới (120÷150)m/s, công suất truyển động tới 40.00KW. Yêu cầu về “mức tiếp xúc mặt răng”lớn đặc biệt là tiếp xúc theo chiều dài. Mức tiếp xúc mặt răng đảm bảo độ bền của răng khi truyền mô men xoắn lớn. Ví dụ trục, cầu trục Bánh răng trong truyền động thường có mô đun lớn và chiều dài răng lớn. 26 Yêu cầu “độ hở mặt bên”giữa các mặt răng phía không làm việc của cặp răng ăn khớp (mức khe hở cạnh răng) hình 4.14. Bất kỳ bộ truyền bánh răng nào cũng yêu cầu độ hở mặt bên để tạo điều kiện bòi trơn bánh răng bồi thường cho sai số giãn nở nhiệt, sai số do gia công và lắp ráp, tránh hiện tượng kẹt răng. Hình 3.2- Mức chính xác khe hở cạnh răng. Như vậy dối với bất kỳ truyển động bánh răng nào cũng đồi hỏi cả 4 yêu cầu trên, nhưng tùy theo chức năng sử dụng mà yêu cầu nào là chủ yếu. Tất nhiên yêu cầu chủ yếu ấy phải ở mức chính xác cao hơn các yêu cầu khác. Ví dụ: truyền động bánh răng trong hộp tốc độ thì yêu cầu chủ yếu là “mức làm việc êm” và nó phải ở cấp chính xác cao hơn yêu cầu “mức chính xác động học” và “mức tiếp xúc mặt răng”. 3.3- Đánh giá mức chính xác của truyền động bánh răng. Để đáng giá mức chính xác và khe hở cạnh răng của bánh răng và bộ truyền người ta dung các chỉ tiêu sau: + Sai số động học của bánh răng F1r + Sai số tích lũy bước răng của bánh răng Fpkr + Độ đảo hướng tâm của vành răng Frr + Độ dao động khoảng pháp tuyến chung Fvwr + Độ dao động khoảng cách trục đô ứng với một vòng quay của bánh răng F”ir + Sai số động học cục bộ của bánh răng F’ir + Sai lệch bước ăn khớp fpbr + Sai lệch bước răng ffr + Sai số profin răng ffr + Viết tiếp xúc tổng + Sai số tổng của đường tiếp xúc Fkr + Sai số hướng răng Fβr + Độ không song song của các đường trục và độ xiên của các đường trục f f xr Lượng dịch chuyển profin gốc EH Khái niệm các chỉ tiêu trên được chỉ dẫn trong bảng 4.8 Trong thiết kế chế tọa bánh răng để chọn bộ thong số đáng giá mức chính xác người ta dựa vào cấp chính xác của truyền động, đồng thời dựa vào điều kiện sản xuất 27 và kiểm tra ở từng cơ sở sản xuất. Chọn bộ thong số cần kết hợp sao cho kiểm tra ở từng cơ sở sản xuất. Chọn bộ thong số cần kết hợp sao cho kiểm tra đơn giản nhất, số dụng cụ ít nhất. Chọn bộ thông số kiểm tra bánh răng có thể dựa vào bảng 4.9. 3.4- Tiêu chuẩn dung sai, cấp chính xác của truyền động bánh răng 3.4.1- Cấp chính xác chế tạo bánh răng Theo tiêu chuẩn TCVN 1067-84, cấp chính xác chế tạo bánh răng được quy định 12 cấp kí hiệu là 1,2,, 12, Cấp chính xác giảm dần xác giảm dần từ 1 đến 12. Ở mỗi cấp chính xác tiêu chuẩn quy định giá trị dung sai và sai lệch giới hạn cho các thông số đáng giá mức chính xác. Việc chọn cấp chính xác tiêu chuẩn của truyền động bánh răng khi thiết kế phải dựa vào điều kiện làm việc cụ thể của truyền động, chẳng hạn tốc độ vòng quay, công suất truyền Trong sản xuất cơ khí thường sử dụng cấp chính xác 6, 7, 8, 9. Ngoài ra khi thiết kế chế tạo bánh răng việc chọn cấp chính xác có thể dựa theo kinh nghiệm. 3.4.2- Dạng đối tiếp mặt răng và dung sai độ hở bên: Tjn Tùy theo cầu về giá trị độ hở mặt bên nhỏ nhất, jnmin mà tiêu chuẩn quy định 6 dạng đối tiếp, kí hiệu là H, E, D,C B, A, theo TCVN 1067-84. Dạng H có giá trị độ hở mặt bên nhỏ nhất (jnmin = 0) và độ hở tăng dần từ H đến A. Hình 3.3- Dạng đối tiếp mặt răng và dung sai độ hở bên. Trong điều kiện làm việc bình thường thì sử dụng dạng đối tiế B, dạng này cũng được dung phổ biến trong chế tạo cơ khí. Tiêu chuẩn cũng quy định 8 miền dung sai của độ hở mặt bên, kí hiệu là h, d, c, b, a x, y, z. Trong thiết kế có thể sử dụng dạng đối tiếp và miền dung sai tương ứng, ví dụ dạng đối tiếp B, Miền dung sai b. Nhưng cũng có thể kiểm tra trực tiếp giá trị độ hở mặt bên nhỏ nhất jnmin. 3.4.3- Ghi kí hiệu cấp chính xác và dạng đối tiếp mặt răng Trên bản vẽ thiết kếm chế tạo bánh răng thì cấp chính xác và dạng đối tiếp được ghi kí hiệu như sau, ví dụ: 7-8-8B.TCVN1067 – 84 Từ trái sang phải lần lượt ký hiệu là: 7 – cấp chính xác của mức chính xác động học 8 – cấp chính xác của mức làm việc êm 28 8 – cấp chính xacs của mức tiếp xúc mặt răng B – dạng đối tiếp mặt răng và dung sai độ hở mặt bên tương ứng là b Bảng 4.8- Các chỉ tiêu đánh giá mức chính xác truyền động bánh răng. Chỉ tiêu đáng giá Kí hiệu Định nghĩa Fi’r Sai số lớ nhất của góc quay bánh răng trong giới hạn một vòng quy khi nó ăn khớp với bánh mẫu chính xác. Fpkt Sai số lớn nhất về vị trí tương quan của hai profin răng cùng tên bất kỳ đo theo vòng tròn đồng tâm với tâm quay bánh răng và đi qua giữa chiều cao răng. Frr Độ dao động lớn nhất của khoảng cách từ dây cung cố định trên răng (hoặc rãnh răng) đến tâm quay bánh răng Fvwr Hiệu pháp tuyến chung lớn nhất và nhỏ nhất đo trên cùng một bánh răng. Fvwr = Wmax = Wmin 29 Chỉ tiêu đáng giá Ký hiệu Định nghĩa Fir” Hiệu khoảng cách trục đo lớn nhất và nhỏ nhất trong một vòng quay của bánh răng Fir’ Hiệu lớn nhất giữa sai số động học cục bộ lớn nhất và nhỏ nhất bánh răng Fpbr Hiệu giữa bước ăn khớp thực và bước ăn khớp danh nghĩa: fpbr = Pbth - Pb Fptr Hiệu giữa hai bước vòng bất kỳ đo trên cùng một đường tròn của bánh răng: fptr = Pt1 – Pt2 Ftr Khoảng cách pháp tuyến giữa hai profin rằng lý thuyết bao lấy profin răng thực, trong giới hạn phần làm việc của profin răng. 30 Phần bề mặt bên của răng trên đó có vết tiếp xúc của nó với răng của bánh răng ăn khớp. vệt tiếp xúc được đánh giá theo hai chiều: - Theo chiều cao răng hm/hp100% Theo chiều dài răng (a-c)/B.100% Chỉ tiêu đánh giá Kí hiệu Định nghĩa Fβr Khoảng cách giữa hai hướng rằng lý thuyết nằm trên mặt trụ đi qua giữa chiều cao răng và bao lấy hướng răng thực. fxr fyr fxr – độ không song của hình chiếu các đường tân quay của bánh răng trên mặt phẳng lý thuyết chung của chúng (đô trên chiều dài bằng chiều rộng bánh răng) Eh Lượng dịch chuyển của profin gốc so với vị trí dang nghĩa của nó 31 Bảng 4.9- Bộ thông số đánh giá mức chính xác của bánh răng trụ. Số bộ Thông số đánh giá, kí hiệu Dung sai, kí hiệu Cấp chính xác khi m≥1 Mức chính xác động học 1 F’ir F’i 3-8 2 Fpr’Fpkr Fp’Fpk 3-6 3 Fpr Fp 7-8 4 Frr’Fvwr Fr’Fvwr 3-8 5 Frr’Fer Fr’Fc 3-8 6 Fir’Fvwr F”i, Fvw 5-8 7 F”ir,Fcr F”i,Fc 5-8 8 F”ir F”i 9-12 9 Frr Fr 7-8 Mức làm việc êm (với <1,25) 1 f’ir f’i 3-8 2 fpbr’ ffr fpb’ ff 3-8 3 fpbr’fptr fpb’ff 3-8 4 f”ir f"i 5-8 Mức tiếp xúc răng trong truyền động 1 Vết tiếp xúc tổng - 3-11 2 Fr F 3-12 3 Fkr Fk 3-12 -hệ số trùng khớp dọc dang nghĩa 4- Dung sai mối ghép ren. 4.1- Dung sai ren hệ mét. Mối ghép ren được dùng nhiều trong các máy và dụng cụ. Chi tiết lắp ghép ren dung nối các chi tiết với nhau để kẹp chặt hoặc truyền lực Các mối ghép ren này tùy theo tính chất được phân thành nhiều loại: ren hệ mét, ren hệ anh nhưng những chi tiết ren hệ mét được dùng phổ biết nhất. 4.1.1. Các thông số kích thước cơ bản. Trên hình 4.1 là mặt cắt dọc theo trục ren để thể hiện profin ren của mỗi ghép. Chi tiết bao có ren trong là đại ốc, chi tiết bị bao có ren ngoài là bù lông. 32 Hình 4.1- Mặt cắt dọc theo trục ren. Các thông số: d-đường kính ngoài của ren ngoài (bulông) D-đường kính ngoài của ren trong (đai ốc) d2-đường kính trung bình của ren ngoài D2-đường kính trung bình của trong d1-đường kính trong của ren ngoài D1-đường kính trong của ren ngoài P-bước ren α-góc profin ren (α = 60o với hệ mét, α = 55o với ren hệ Anh) H- chiều cao của profin gốc H1 – chiều cao làm việc của profin ren Để quy định dung sai kích thước rent a phải khảo sát ảnh hưởng các yếu tố kích thước đển tính đổi lẫn của ren. 4.1.2 Ảnh hưởng tới tính đổi lẫn của ren. Ảnh hưởng tới tính đổi lẫn của ren không chỉ có sai số của kích thước đường kính ren mà còn có cả sai số bước ren (P) và góc profin ren (α). Nhưng khi phân tích ảnh hưởng sai số bước ren và góc profin ren, người ta đã quy lượng ảnh hưởng của chúng về phương của đường kính trung bình gọi là lượng bù hướng kính của đường kính trung bình với: Lượng bù đường kính của sai số bước ren: Fp = ∆Pncotg 2 = 1,732∆Pn(µm) Lượng bù đương kính sai số góc nửa profin ren: fα = 0,36P.∆ m 2 Trong đó: ∆Pn: sai số tính lũy n bước ren (µm) 33 ∆ 2 : sai số góc profin ren (phút góc) ∆ 2 22 2 traiphai a P: tính theo mm Đường kính trung bình có tính đến ảnh hưởng của sai số bước và góc profin ren được gọi là “đường kính trung bình biểu kiến (d2, D2). Trị số của chúng được tính theo công thức sau: d2 = d2th + fp+ fα đối với ren vít D2 = D2th – (fp+fα) đối với ren đại ốc D2th, D2th là đường kính trung bình thực. Như vậy để đảm bảo tính đối lẫn của ren, tiêu chuẩn chỉ quy định dung sai kích thước đường kính ren: d2,d đối với ren vít và D2, D1 đối với ren đai ốc tùy theo cấp chính xác chế tạo ren. 4.1.3. Cấp chính xác chế tạo ren. TCVN 1917-93 quy định các cấp chính xác chế tạo ren hệ mét lắp có độ hở theo bảng 4-1: Bảng 4.1- Cấp chính xác kích của ren. Dạng ren Đường kính của ren Cấp chính xác Ren ngoài d 4;6;8 d2 3;4;5;6;7;8;9 Ren trong D2 4;5;6;7;8 D1 4;5;6;7;8 Trị số dung sai đường kính ren ứng với các cấp chính xác khác nhau tra theo bảng TCVN 1917-93. 4.1.4 Lắp ghép ren hệ mét Lắp ghép ren cũng có đặc tính như lắp ghép trụ trơn là: lắp có độ hở, lắp có độ dôi và lắp trung gian. Trong chương này ta chỉ giới thiệu lắp ghép ren có độ hở (thường dung cho ren kép chặt và truyển động). Lắp ghép ren được hình thành bằng cách phối hợp các miền dung sai kích thước ren ngoài và ren trong. Giá trị sai lệch giới hạn các kích thước ren ứng với các miền dung sai được quy định theo TCVN 1917-93 * Ghi ký hiệu sai lệch và lắp ghép ren trên bản vẽ: Trên bản vẽ lắp, ký hiệu lắp ghép được ghi dưới dạng phân số sau ký hiệu ren. Ví dụ: M12 x 1 - 67 7 gg H . Ký hiệu lần lượt là: ren hệ mét đường kính d = 12mm bước ren p = 1. Miền dung sai đường kính trung bình D2 và đường kính trong D1 đến là 7H. Miền dung sai đường kính trung bình d2 là 7g, đường kính ngoài d là 6g. Trên bản vẽ chi tiết, từ ký hiệu lắp ghép trên ta có thể ghi kí hiệu trên bản vẽ chi tiết như sau: 34 M12 x 1-7H đối với ren đại ốc. M12 x 1-7g6g đối với ren vít. Bảng 4.2-Miền dung sai kích thước ren(lắp ghép có độ hở) Loại chính xác Chiều dài văn ren S N L Miền dung sai ren ngoài Chính xác (3h4h) 4g 4h (5h4h) Trung bình 5g6g (5h6h) 6d 6e 6f 6g 6h (7e6e) 7g6g (7h6h) Thô 8g (8h) (9g8g) Miền dung sai ren trong Chính xác 4H 4H 5H 6H Trung bình 5G 5H 6G 5H 6H (7G) 7H Thô 7G 7H (8G) 8H 1 Miền dung sai được ưu tiên sử dụng 2. ()Miền dung sai hạn chế sử dụng 3. Khi chiều dài vận ren thuộc nhóm ngắn (S) và nhóm dài (L) thì cho phép sử dụng miền dung sai được quy định cho chiều dài văn ren thuộc nhóm bình thường (N). Ví dụ: Cho ký tự hiệu lắp ghép ren M24 x 2 - g H 6 7 Yêu cầu: - Giải thích kí hiệu lắp ghép - Tra sai lệch giới hạn và dung sai kích thước ren - Giả sử một bu lông sau khi chế tạo người ta đo được các thong số sau: Đường kính trung bình ren: d2th = 22.540mm Sai số bước ren: ∆ 2 phải = 50’; 2 trái = -30’ Sai số tích lũy bước: ∆P = 0,024mm Hỏi ren bu lông có đạt yêu cầu không? Giải: - Kí hiệu lắp ghép ren đã cho là: M24x2_7H/6g, có nghĩa là ren hệ mét có đường kính d = 24mm, bước ren p = 2mm, miền dung sai ren trong (đai ốc) là 7H miền dung sai ren ngoài (bu lông) là 6g. - Sai lệch giới hạn kích thước D1, D2 ứng với miền dung sai 7H (tra theo bảng 18, phụ lục 3) 35 D2 mEÉ EI 280 0 D1 mEÉ EI 450 0 Sai lệch giới hạn kích thước d2, d ứng với miền dung sai 6g, tra theo bảng 19, phục lục 3 d2 38 208 es mei d mé mei 38 318 - Để đánh giá xem ren bu lông có đạt yêu cầu không ta phải tính đường kính trung bình biểu kiến, theo quả đã cho. Theo công thức 4.3 ta có: d2 = d2th+fp+fα với +d2th = 22,540mm (theo kết quả đo đã cho) +fp = 1,732 ∆P ở đây ∆P = 0,024mm (theo kết quả đo đã cho) fp = 1,732 x 0,024 = 41,6µm +fα = 0,36P. m 310. 2 (theo công thức) Với bước ren p = 2mm; sai số góc profin ren đã cho: 40 2 '30'50 2 22 2 traiphai fα = 0,36.2.40’.103 = 28.8µm. Thay các trỉ số bằng số vào công thức (4.3)ta được: d2 = 22,540 + 0,0416 + 0,0288 = 22,663mm Ren bu lông đạt yêu cầu khi đường kính trung bình biểu kiến d2 thỏa mãn công thức sau: d2min≤d2≤d2max với d2min = d2N+ es = 22,701-0,208 = 22,493mm d2max = d2N+es = 22,701 – 0,038 = 22,663mm (d2N – tra theo bảng 17, phục lục 3) Ta thấy d2min = 22,493<d2 = 22,610< d2max = 22.663` 36 CÂU HỎI 1. Tiêu chuẩn dung sai lắp ghép bề mặt trơn TCNV 2244-99 quy định bao nhiêu cấp chính xác và ký hiệu chúng như thế nào? 2. Thế nào là hệ thống lắp ghép lỗ cơ bản và trục cơ bản? vẽ hình minh họa. 3. Sai lệch cơ bản là gì? Tiêu chuẩn TCVN 2244-99 quy định dãy các sai lệch cơ bản như thế nào. 4. Có mấy nhóm lắp ghép tiêu chuẩn và đặc tính của chúng như thế nào. 5. Cho ví dụ về sai lệch và lắp ghép trên bản vẽ, giải thích các kỹ hiệu đó, 6. Nếu phạm vi ứng dụng của 2 kiều lắp sau: 6 7 , 7 7 k H f H 7. Tiêu chuẩn đã quy định dung sai cho những yếu tố kích thước nào của ren vít và đai ốc trong lắp ghép ren. 8. Thế nào là đường kính trung bình biểu kiến, nêu công thức tính nó với ren vít và đai ốc 9. Nêu các yêu cầu kĩ thuật đối với truyền động bánh răng, một truyền động bánh răng bất kỳ thì cần có những yếu tố nào? 10. Tiêu chuẩn TCVN 1067-84 quy định mấy cấp chính xác chế tạo bánh răng nêu phương pháp chọn cấp chính xác cho truyền động bánh răng khi thiết kế. BÀI TẬP 1. Cho các lắp ghép trụ trơn ghi trong bảng 1 dưới đây. Hãy ghi kí hiệu sai lệch và lắp ghép bằng chữ và bằng số trên bản vẽ. Bảng 1: TT dN,mm Kiều lắp TT dn, mm Kiều lắp 1 30 8 9 8 8 h E và e H 1 92 6 7 6 7 h K và k H 2 40 6 7 6 7 h G và g H 2 115 6 7 6 7 h P và s H 3 50 6 7 6 7 h và j H J S s 3 124 6 7 6 7 h N và n H 2. Cũng với các lắp ghép trụ trơn cho trong bảng 1. - Hãy lập sơ đồ phân bố miền dung sai của lắp ghép. - Lắp ghép đã cho thuộc nhóm lắp ghép nào? Xác định độ hở, độ dôi giới hạn của chúng. 3. Với đặc tính yêu cầu của lắp ghép cho trong bảng 2 dưới đây. T T dN mm Smaxy c µm Smaxy c µm T T dN,mm Smaxy c µm Smaxy c µm TT dN,m m Smaxy c µm Smaxy c µm 1 2 3 42 56 62 80 180 76 25 60 0 4 5 6 46 66 86 42 60 93 1 11 36 7 8 9 48 76 82 8 39 25 -33 -10 -32 - Chọn kiều lắp tiêu chuẩn cho từng trương hợp. 37 - Xác định sai lệch giới hạn kích thước lỗ và trục.
File đính kèm:
giao_trinh_dung_sai_lap_ghep_va_do_luong_ky_thuat_phan_1.pdf