Giáo trình Cơ sở cắt gọt kim loại - Chương 7: Chất lượng chi tiết gia công cơ
7.1. CHẤT LƯỢNG CHI TIẾT GIA CÔNG.
Quá trình gia công kim loại thường phải đáp ứng các yêu cầu sau:
* Chỉ tiêu về chất lượng: đảm bảo chất lượng chi tiết theo yêu cầu.
* Chỉ tiêu về năng suất: đảm bảo năng suất gia công lớn nhất hay thời gian
gia công chi tiết là nhỏ nhất.
* Chỉ tiêu về kinh tế: đảm bảo chi phí gia công nhỏ nhất.
Quá trình gia công là quá trình cơ lý phức tạp chịu ảnh hưởng của nhiều yếu tố và điều
kiện cắt gọt, liên quan đến nhiều trang thiết bị và tính chất sản xuất. Các yêu cầu trên khó có
thể đáp ứng đồng thời, nhiều khi mâu thuẩn nhau, tuy nhiên tuỳ theo tính chất sản phẩm và
yêu cầu cụ thể mà ta tính toán cân đối các chỉ tiêu cho phù hợp.
Trong đó chất lượng chi tiết gia công luôn là chỉ tiêu quan trọng có ảnh hưởng rất lớn
đến khả năng làm việc và tuổi thọ của chi tiết máy.
Tóm tắt nội dung tài liệu: Giáo trình Cơ sở cắt gọt kim loại - Chương 7: Chất lượng chi tiết gia công cơ
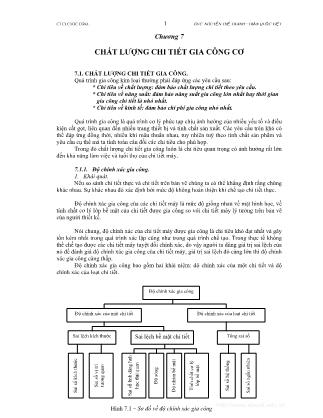
C7 CLCTGC CGKL 1 GVC NGUYỄN THẾ TRANH - TRẦN QUỐC VIỆT Chương 7 CHẤT LƯỢNG CHI TIẾT GIA CÔNG CƠ 7.1. CHẤT LƯỢNG CHI TIẾT GIA CÔNG. Quá trình gia công kim loại thường phải đáp ứng các yêu cầu sau: * Chỉ tiêu về chất lượng: đảm bảo chất lượng chi tiết theo yêu cầu. * Chỉ tiêu về năng suất: đảm bảo năng suất gia công lớn nhất hay thời gian gia công chi tiết là nhỏ nhất. * Chỉ tiêu về kinh tế: đảm bảo chi phí gia công nhỏ nhất. Quá trình gia công là quá trình cơ lý phức tạp chịu ảnh hưởng của nhiều yếu tố và điều kiện cắt gọt, liên quan đến nhiều trang thiết bị và tính chất sản xuất. Các yêu cầu trên khó có thể đáp ứng đồng thời, nhiều khi mâu thuẩn nhau, tuy nhiên tuỳ theo tính chất sản phẩm và yêu cầu cụ thể mà ta tính toán cân đối các chỉ tiêu cho phù hợp. Trong đó chất lượng chi tiết gia công luôn là chỉ tiêu quan trọng có ảnh hưởng rất lớn đến khả năng làm việc và tuổi thọ của chi tiết máy. 7.1.1. Độ chính xác gia công. 1. Khái quát. Nếu so sánh chi tiết thực và chi tiết trên bản vẽ chúng ta có thể khẳng định rằng chúng khác nhau. Sự khác nhau đó xác định bởi mức độ không hoàn thiện khi chế tạo chi tiết thực. Độ chính xác gia công của các chi tiết máy là mức độ giống nhau về mặt hình học, về tính chất cơ lý lớp bề mặt của chi tiết được gia công so với chi tiết máy lý tưởng trên bản vẽ của người thiết kế. Nói chung, độ chính xác của chi tiết máy được gia công là chỉ tiêu khó đạt nhất và gây tốn kém nhất trong quá trình xác lập cũng như trong quá trình chế tạo. Trong thực tế không thể chế tạo được các chi tiết máy tuyệt đối chính xác, do vậy người ta dùng giá trị sai lệch của nó để đánh giá độ chính xác gia công của chi tiết máy, giá trị sai lệch đó càng lớn thì độ chính xác gia công càng thấp. Độ chính xác gia công bao gồm hai khái niệm: độ chính xác của một chi tiết và độ chính xác của loạt chi tiết. Độ chính xác gia công Độ chính xác của một chi tiết Độ chính xác của loạt chi tiết Sai lệch kích thước Sai lệch bề mặt chi tiết Tổng sai số Sa i s ố kí ch th ướ c Sa i s ố vị tr í tư ơn g qu an Sa i s ố h ình d án g hìn h họ c đạ i q ua n Đ ộ só ng Đ ộ nh ám b ề m ặt Tí nh c hấ t c ơ lý lớ p bề m ặt Sa i s ố hệ th ốn g Sa i s ố ng ẫu n hi ên Hình 7.1 – Sơ đồ về độ chính xác gia công C7 CLCTGC CGKL 2 GVC NGUYỄN THẾ TRANH - TRẦN QUỐC VIỆT Trong nền sản xuất tự động, khi toàn bộ quá trình thiết kế và chế tạo được thực hiện nhờ trợ giúp của máy điện tử, người thiết kế phải đảm nhận luôn công việc của người công nghệ. Độ chính xác của chi tiết gia công cần phải đánh giá theo các chỉ tiêu sau đây: • Độ chính xác về kích thước của mặt gia công (kích thước thẳng, kích thước góc), • Độ chính xác về hình dạng hình học đại quan của bề mặt gia công (độ côn, độ ô van, hình trống, hình yên ngựa...) là mức độ phù hợp lớn nhất của chúng so với hình dạng hình học lý tưởng. • Độ chính xác về vị trí tương quan giữa các bề mặt gia công với nhau (độ đồng tâm, độ song song, độ vuông góc...) thực chất là sự xoay đi một góc của bề mặt này so với bề mặt kia. • Độ sóng của bề mặt được quan sát trong một phạm vi nhỏ. • Sai lệch hình học tế vi (độ nhấp nhô tế vi) còn gọi là độ nhám bề mặt. • Tính chất cơ lý lớp bề mặt chi tiết gia công. Thông thường độ nhám bề mặt và tính chất cơ lý lớp bề mặt là những chỉ tiêu quan trọng để đánh giá chất lượng bề mặt gia công. Khi xét đến độ chính xác gia công của một loạt chi tiết chúng ta còn quan tâm đến sai số hệ thống và sai số ngẫu nhiên, thực tế kích thước thực của mỗi chi tiết trong một loạt đều khác nhau, khác cả với kích thước điều chỉnh, dao động trong một giới hạn nào đó. Tính chất phân bố, đường cong phân bố, phương sai v.v..của kích thước thực trong mỗi loạt chi tiết gia công được đề cập trong khái niệm dung sai. Có nhiều nguyên nhân gây ra sai số: a. Sai số hệ thống: • Các nguyên nhân sinh ra sai số hệ thống không đổi: - Sai số lý thuyết của phương pháp cắt. - Sai số chế tạo của máy, đồ gá, dụng cụ cắt. - Độ biến dạng của chi tiết gia công. • Các nguyên nhân sinh ra sai số hệ thống thay đổi: - Dụng cụ cắt bị mòn theo thời gian cắt. - Biến dạng vì nhiệt của máy, dao, đồ gá. b. Sai số ngẫu nhiên: sinh ra do các nguyên nhân sau: - Tính chất vật liệu không đồng đều. - Lượng dư gia công không đều. - Vị trí của phôi trong đồ gá thay đổi. - Sự thay đổi của ứng suất dư. - Do gá dao, mài dao, thay đổi máy nhiều lần. - Do hiện tượng dao động nhiệt. 2. Điều chỉnh đạt độ chính xác yêu cầu. Để đảm bảo dộ chính xác của từng nguyên công cần phải tiến hành điều chỉnh máy. Đây là quá trình xác định vị trí tương đối giữa dụng cụ và mặt cần gia công nhằm giảm bớt các sai số gia công, đạt được các yêu cầu đã cho trên bản vẽ. Trong sản xuất đơn chiếc và loạt nhỏ, độ chính xác yêu cầu có thể đạt được bằng phương pháp cắt thử. Trong sản xuất hàng loạt lớn và hàng khối, độ chính xác gia công nhận được bằng phương pháp tự động đạt kích thước trên máy đã điều chỉnh sẵn. Hiện nay các phương pháp điều chỉnh hay dùng nhất là : - Điều chỉnh tĩnh, - Điều chỉnh theo chi tiết cắt thử bằng Calíp, - Điều chỉnh theo chi tiết cắt thử bằng dụng cụ đo vạn năng, - Điều chỉnh tự động, C7 CLCTGC CGKL 3 GVC NGUYỄN THẾ TRANH - TRẦN QUỐC VIỆT - Điều chỉnh nhờ kỹ thuật điều khiển số ( máy NC và CNC). Ngày nay, nhờ sự phát triển mạnh mẽ của lĩnh vực tự động hoá, chất lượng gia công còn có thể đảm bảo nhờ có sử dụng bộ điều chỉnh tự động hồi tiếp. Về nguyên tắc, sơ đồ khối của bộ tự động điều chỉnh có hồi tiếp như trên hình 7.2. Trên các máy công cụ điều khiển theo chương trình số, quá trình gia công được thực hiện một cách tự động nhờ đưa vào hệ thống một chương trình gia công lập sẵn. Hệ thống điều khiển số cho khả năng thực hiện các lệnh này và kiểm tra chúng nhờ một hệ thống đo dịch chuyển của các bàn trượt của máy. Ở đây máy công cụ tự động được lập trình để thực hiện một loạt các hoạt động ở một chế độ xác định trước nhằm tạo ra chi tiết có các kích thước và các thông số vật lý hoàn toàn có thể dự đoán trước, do vậy đạt được độ chính xác cao. Độ chính xác là chỉ tiêu rất quan trọng của chất lượng máy móc, quyết định khả năng làm việc, độ tin cậy, tuổi thọ, năng suất và các tính chất khác của máy. Việc tăng tốc độ, tải trọng của máy chỉ thực hiện được bằng cách nâng cao độ chính xác gia công chi tiết. Do vậy nâng cao độ chính xác chi tiết gia công có những ý nghĩa sau đây: • Tăng độ tin cậy, tuổi bền của máy, giảm chi phí phục vụ sửa chữa máy. • Giảm khối lượng gia công chi tiết, giảm hao phí nguyên vật liệu do giảm lượng dư, giảm thời gian lắp ráp vì không phải tốn thời gian để lắp sửa, cho phép lắp ráp theo dây chuyền. Khi giải quyết vấn đề độ chính xác cần phải định ra độ chính xác chế tạo sản phẩm xuất phát từ yêu cầu, chức năng làm việc và cần phải xác định phương pháp cũng như thiết bị thực hiện và kiểm tra. 7.1.2. Chất lượng bề mặt. Chất lượng của chi tiết máy không những phụ thuộc vào độ chính xác gia công mà còn phụ thuộc vào chất lượng lớp kim loại bề mặt ngoài của nó. Từ yêu cầu thực tế về chức năng và điều kiện làm việc của máy móc mà thiết bị ngày càng đòi hỏi rất cao về chất lượng bề mặt của chi tiết máy. Những yêu cầu đó là: • Tốc độ làm việc cao. • Tải lớn. • Công suất lớn. • Áp suất và nhiệt độ cao. • Tuổi thọ và độ tin cậy cao. • Độ chính xác làm việc cao. • Trọng lượng tương đối bé. Khả năng làm việc của chi tiết máy phụ thuộc rất nhiều vào chất lượng lớp bề mặt. 2 3 5 4 6 1 7 8 Hình 7-2 : Sơ đồ khối bộ tự động điều chỉnh có hồi tiếp C7 CLCTGC CGKL 4 GVC NGUYỄN THẾ TRANH - TRẦN QUỐC VIỆT Chất lượng bề mặt của chi tiết máy là tập hợp nhiều tính chất quan trọng hình học và cơ lý của lớp bề mặt, cụ thể là: - Hình dáng lớp bề mặt ( độ sóng, độ nhám.. .). - Trạng thái và tính chất cơ lý của lớp bề mặt ( độ cứng, chiều sâu biến cứng, ứng suất dư.. .). - Phản ứng của lớp bề mặt đối với môi trường làm việc (tính chống mòn, khả năng chống xâm thực hóa học, độ bền mõi .. .). Chất lượng bề mặt chi tiết máy phụ thuộc vào phương pháp và điều kiện gia công cụ thể. Chất lượng bề mặt là mục tiêu chủ yếu cần đạt ở bước gia công tinh các bề mặt chi tiết máy. Khác với bề mặt lý thuyết của chi tiết trên bản vẽ, bề mặt thực bao giờ cũng có độ nhấp nhô với hình dáng và chiều cao rất khác nhau. Chiều cao, hình dáng, đặc điểm phân bố và hướng nhấp nhô bề mặt phụ thuộc vào rất nhiều yếu tố như: • Chế độ cắt. • Chế độ bôi trơn, làm nguội. • Vật liệu gia công. • Vật liệu làm dao. • Kết cấu, hình học của dao. • Loại máy, độ cứng vững của hệ thống công nghệ. • Dụng cụ phụ và đồ gá. 7.2. CÁC THÔNG SỐ ĐÁNH GIÁ CHẤT LƯỢNG BỀ MẶT 7.2.1. Tính chất hình học của bề mặt gia công: Tính chất hình học của bề mặt gia công được đánh giá bằng độ nhấp nhô tế vi và độ sóng bề mặt. • Độ nhấp nhô tế vi. Trong quá trình cắt, lưỡi cắt của dụng cụ cắt và sự hình thành phoi tạo ra những vết xước cực nhỏ trên bề mặt gia công được đặc trưng bằng khái niệm độ nhám hay độ nhấp nhô tế vi của bề mặt. Nhám bề mặt là tập hợp các nhấp nhô của profil bề mặt, với bước tương đối nhỏ được xét trong một chiều dài giới hạn gọi là chiều dài chuẩn hay cơ sở. Độ nhấp nhô tế vi được đánh giá bằng nhiều thông số: - Chiều cao nhấp nhô RZ: là trị số trung bình của 5 khoảng cách từ 5 đỉnh cao nhất đến 5 đáy thấp nhất của nhấp nhô bề mặt tế vi trong phạm vi chiều dài chuẩn l. Hình 7.3 - Độ sóng bề mặt Wz: Là giá trị trung bình số học của 5 giá trị chiều cao nhấp nhô, đo trong phạm vi chiều dài chuẩn. Wmax: Là khoảng cách của điểm cao nhất và thấp nhất của prophin sóng, đo trên một bước sóng đầy đủ trong giới hạn chiều dài chuẩn Ln. C7 CLCTGC CGKL 5 GVC NGUYỄN THẾ TRANH - TRẦN QUỐC VIỆT Sw: là giá trị trung bình số học của các khoảng cách Swi giữa các sóng kế tiếp nhau cùng đo theo đường trung bình trong giới hạn chiều dài chuẩn. ∑ = = n i WiW Sn S 1 1 Độ sóng có thể là dọc (vuông góc với chiều chuyển động dao) có độ lớn nhỏ. Sóng ngang (trùng với chuyển động của dụng cụ cắt) có độ lớn hơn. - Độ nhám bề mặt. (S/H< 50). Là tập hợp các nhấp nhô của prôphin bề mặt với bước tương đối nhỏ, được xét trong chiều dài giới hạn bằng chiều dài chuẩn. Khi đánh giá chất lượng bề mặt gia công thường phải dùng đến khái niệm đường trung bình. Đường trung bình của prôphin là đường thẳng chuẩn, có hình dạng của prôphin danh nghĩa và có trị số sai lệch bình phương trung bình đến prôphin trong giới hạn chiều dài chuẩn là nhỏ nhất. Khi xác định vị trí đường trung bình trên prôphinlogramcho phép dùng qui ước là đường thẳng mà chia bề mặt trong giới hạn chiều dài chuẩn sao cho tổng diện tích phần lồi bẳng tổng diện tích phần lõm. F1+F3+F5+...+F2n-1 = F2+F4+F6+...+F2n Hình 7.4 - Prophin bề mặt chi tiết gia công • Sai lệch trung bình số học Ra. Là trị số trung bình số học tuyệt đối của prôphin trong giới hạn chiều dài chuẩn. Được xác định theo công thức: dxxyRa ∫= 1 0 )( hay theo công thức gần đúng: ∑ = = n i ia xyn R 1 1 )( • Chiều cao nhấp nhô trung bình theo 10 điểm Rz. Là tổng sai lệch trung bình số học tuyệt đối khoảng cách từ 5 đỉnh cao nhất và 5 đáy thấp nhất trong giới hạn chiều dài chuẩn. Được xác theo công thức: ⎟⎠ ⎞⎜⎝ ⎛ += ∑∑ == 5 1 5 15 1 i i i iz HHR minmax hoặc: ⎟⎠ ⎞⎜⎝ ⎛ −= ∑∑ == 5 1 5 15 1 i i i iz hhR minmax C7 CLCTGC CGKL 6 GVC NGUYỄN THẾ TRANH - TRẦN QUỐC VIỆT Trong đó: Himax: Sai lệch năm đỉnh cao nhất của profil. Himin: Sai lệch năm đỉnh thấp nhất của profil. himax : Khoảng cách từ năm đỉnh cao nhất đến đường thẳng song song với đường trung bình và không cắt profil. himin : Khoảng cách từ năm đỉnh thấp nhất đến đường thẳng song song với đường trung bình và không cắt profil. • Sai lệch trung bình bình phương Hck được xác định theo công thức: n y dxy l H n i l ck ∑∫ === 1 2 1 0 21 ' • Chiều cao lớn nhất của prophin Rmax' Là khoảng cách giữa đường đỉnh và đường đáy của prôfil trong giới hạn chiều dài chuẩn. • Bước nhấp nhô trung bình của profil Sm' Là trị số trung bình số học của bước nhấp nhô prôfil trong giới hạn chiều dài chuẩn. Được xác định theo công thức: ∑ = = n i mim Sn S 1 1 • Bước nhấp nhô trung bình của prôfil theo đỉnh S. Là trị số trung bình số học của bước nhấp nhô prôfil theo đỉnh trong giới hạn chiều dài chuẩn được xác định theo công thức: ∑ = = n i im Sn S 1 1 • Chiều dài tựa của prôphin (p). Là tổng chiều dài các đoạn cắt trong giới hạn chiều dài chuẩn, cắt vật liệu phần lồi prôphin bằng đường thẳng cách đều đường trung bình. Được tính theo công thức: ∑ = = n i ip l 1 η Hình 7.5 - Chiều dài tựa của Prophin h: chiều dài tựa tương đối của prôphin tp: là tỉ số chiều dài prôphin trên chiều dài chuẩn Được tính theo công thức: ∑ = == n i i p p lll t 1 100100 %% η Độ nhám bề mặt được xác định bởi sai lệch số học trung bình Ra và chiều cao trung bình Rz. TCVN 2511: 1995 qui định 14 cấp độ nhám và các giá trị số của các thông số nhám Ra và Rz. Trị số nhám càng bé thì bề mặt càng nhẵn. C7 CLCTGC CGKL 7 GVC NGUYỄN THẾ TRANH - TRẦN QUỐC VIỆT Bảng1 : Bảng thông số nhám Thông số nhám (μm) Độ bóng bề mặt Loại Ra Rz Chiều dài chuẩn (mm) 1 2 3 4 5 - - - - - - - - - - từ 320 đến 160 dưới 160 đến 80 " 80 " 40 " 40 " 20 " 20 " 10 8,0 2,5 6 a b c từ 2,5 đến 2,0 dưới 2,0 đến 1,6 " 1,6 " 1,25 - - - 7 a b c " 1,25 " 1,00 " 1,00 " 1,80 " 0,80 " 0,63 - - - 8 a b c " 0,63 " 0,5 " 0,50 " 0,40 " 0,40 " 0,32 - - - 0,8 9 a b c " 0,32 " 0,25 " 0,25 " 0,20 " 0,20 " 0,16 - - - 10 a b c " 0,160 " 0,125 " 0,125 " 0,100 " 0,100 " 0,080 - - - 0,25 11 a b c " 0,080 " 0,063 " 0,063 " 0,050 " 0,050 " 0,040 - - - 0,25 12 a b c " 0,040 " 0,032 " 0,032 " 0,025 " 0,025 " 0,020 - - - 13 a b c - - - từ 0,100 đến 0,080 dưới 0,08 đến 0,063 dưới 0,063 đến 0,050 14 a b c - - - dưới 0,050 đến 0,040 dưới 0,040 đến 0,032 dưới 0,032 đến 0,025 0,08 7.2.2.Thông số vật lý của bề mặt gia công. Tính chất cơ lý của bề mặt gia công bao gồm sự biến cứng bề mặt và ứng suất dư: a. Sự biến cứng bề mặt. Trong quá trình gia công dưới tác dụng của lực cắt, trên bề mặt của kim loại sinh ra biến dạng dẻo. Các hạt tinh thể bị kéo lệch mạng gây nên ứng suất giữa các tinh thể. Tác dụng này làm giảm mật độ kim loại, nâng cao giới hạn bền, nâng cao độ cứng và độ giòn, làm giảm tính dẻo và tính dai...hiện tượng này gọi là sự biến cứng và chiều sâu biến cứng của bề mặt kim loại. Mức độ biến cứng (H có thể xác định theo công thức sau: Sh = (HS - Ht/Ht) 100% .100%s th t H HS H −= hoặc: k = (HS/Ht) 100% Trong đó: HS, Ht là độ cứng tế vi sa ... cơ lý này ảnh hưởng rất lớn đến kết quả gia công ra sản phẩm. 7.3. CÁC NGUYÊN NHÂN ẢNH HƯỞNG ĐẾN CHẤT LƯỢNG BỀ MẶT. 7.3.1. ẢNH HƯỞNG ĐẾN ĐỘ NHẤP NHÔ BỀ MẶT. C7 CLCTGC CGKL 9 GVC NGUYỄN THẾ TRANH - TRẦN QUỐC VIỆT Khi gia công bằng phương pháp cắt gọt, có rất nhiều nguyên nhân gây nên độ nhấp nhô bề mặt. Chiều cao, hình dáng của nhấp nhô, đặc tính phân bố cũng như hướng của các vết gia công đều phụ thuộc vào phương pháp gia công , chế độ cắt gọt, điều kiện bôi trơn làm nguội, dụng cụ cắt, vật liệu gia công... Như vậy có rất nhiều nguyên nhân gây nên độ nhấp nhô bề mặt và có thể chia chúng thành những nhóm sau đây: • Những nguyên nhân có liên quan đến hình dạng hình học của dao cắt. • Những nguyên nhân có liên quan đến biến dạng đàn hồi và biến dạng dẻo của vật liệu gia công. • Những nguyên nhân có liên quan đến độ cứng vững của hệ thống công nghệ và rung động. Có thể nói rằng quá trình xuất hiện các nhấp nhô bề mặt do các nguyên nhân hình học của dao là do sự sao chép (in dập) quĩ đạo chuyển động và hình dáng của dao lên bề mặt gia công. Chiều cao hình dáng và phân bố của các nhấp nhô phụ thuộc vào hình dáng, trạng thái của lưỡi cắt, các thông số v, s, t của chế độ cắtvà ảnh hưởng của quĩ đạo chuyển động dao cắt so với bề mặt gia công. Trong các điều kiện gia công khác nhau, biến dạng dẻo, biến dạng đàn hồi của vật liệu gia công và rung động sẽ làm méo mó hình dạng hình học của nhấp nhô đồng thời phá hủy qui luật phân bố cũng như làm tăng chiều cao nhấp nhô.Trong một số trường hợp biến dạng dẻo và rung động gây nên độ nhấp nhô dọc rất lớn. Thông thường chỉ có một trong ba nguyên nhân kể trên là có ảnh hưởng lớn nhất đến độ nhấp nhô bề mặt. Song trong một số trường hợp đặ biệt nhấp nhô xuất hiện do tác dụng đông thời của các nguyên nhân kể trên nên nó không có qui luật rõ ràng. 1. Ảnh hưỏng của hình dạng hình học dao cắt và chế độ cắt đến chất lượng bề mặt. Mối quan hệ giữa các thông số hình học của dụng cụ cắt và chế độ cắt với chất lượng bề mặt của chi tiết gia công được nghiên cứu cụ thể ứng với từng phương pháp gia công: tiện, phay, bào, mài... Ta xét trường hợp điển hình là khi tiện. Sau một vòng quay của phôi dao tiện sẽ dịch chuyển một đoạn s1 từ vị trí 1 sangvị trí 2. Trên bề mặt gia cốngẽ bị chừa lại một phần kim loại m không được hớt đi bởi dụng cụ cắt. Chiều cao nhấp nhô Rz phụ thuộc vào lượng tiến dao s, bán kính mũi dao r, các góc nghiêng chính và phụ thuộc của dao ϕ và ϕ1 , cũng như chiều dày nhỏ nhất của lớp phoi amin. Nếu giảm lượng chạy dao thì chiều dài nhấp nhô giảm. Nếu tăng bán kính mũi dao thì chiều cao nhấp nhô cũng giảm và nhấp nhô có dạng hình cong. Để xác định chiều cao nhấp nhô ta có công thức sau: • Với chiều dày phoi bất kỳ: 1ϕϕ gg SRz cotcot += • Khi S> 0.15 mm/ vòng: r SRz 8 2 = • Còn khi S< 0.1 mm/ vòng giá trị chiều cao nhấp nhô sẽ là: ⎥⎦ ⎤⎢⎣ ⎡ ++= 2 2 1 28 s ara r SRz minmin . C7 CLCTGC CGKL 10 GVC NGUYỄN THẾ TRANH - TRẦN QUỐC VIỆT Hình 7.7 - Ảnh hưởng của các thông số hình học của dụng cụ cắt và chế độ cắt đến Rz Trong thực tế, chiều dày lớp phoi nhỏ nhất amin phụ thuộc đáng kể vào bán kính mũi dao r. nếu lưỡi cắt được mài bằng đá kim cương cả mặt trước và mặt sau của dao có thể đạt được r = 10μm, thì amin = 4μm. Khi dao được mài bằng đá bình thường, đối với dao hợp kim cứng r = 40μm, thì amin = 20μm. Khi dao chế tạo mới hoặc cùn đi, bề mặt nhấp nhô, khuyết tật của nó sẽ ảnh hưởng đến độ nhấp nhô bề mặt của chi tiết gia công. Kinh nghiệm thực tế đã chứng tỏ, khi tiện bằng dao cùn hoặc có khuyết tật thì độ nhấp nhô bề mặt tăng lên 50 ÷60 %, khi phay bằng dao phay phụ thì độ nhấp nhô tăng lên 100 ÷115%, khi phay bằng dao phay mặt đầu thì nhấp nhô tăng lên 35 ÷45%, khi khoan tăng lên 30 ÷40%, khi doa tăng lên 20 ÷30%. Chiều sâu cắt trong thực tế hầu như không có ảnh hưởng tới chiều cao nhấp nhô RZ, theo quang điểm in dọc hình học. Tuy nhiên nó sẽ góp phần gây ảnh hưởng tới chất lượng bề mặt thông qua hiện tượng biến dạng dẻo lớp bề mặt. 2. Ảnh hưởng của biến dạng dẻo và biến dạng đàn hồi của kim loại ở lớp ngoài đến độ nhấp nhô bề mặt. Khi gia công kim loại dẻo lớp bề mặt bị biến dẻo mạnh, các cấu trúc tinh thể nhỏ biến thành cấu trúc sợi do đó làm thay đổi rất nhiều hình dạng và trị số nhấp nhô. Khi gia công kim loại giòn, các hạt tinh thể cá biệt bị rời ra củng làm tăng kích thước và hình dáng nhấp nhô. Mức độ biến dạng nhiều hay ít phụ thuộc vào một số yếu tố sau: Vật liệu gia công. Chế độ cắt Dung dịch trơn nguội.. . Khi gia công thép cacbon (thép 30, 40, 50), nếu tốc độ cắt nhỏ (v = 1m/phút) thì nhiệt tỏa ra ít và tạo thành phoi vụn. Phoi tách ra rất dể dàng và biến dạng trên bề mặt gia công không đáng kể. Chiều cao nhấp nhô của bề mặt gia công nhỏ. Khi tăng tốc độ cắt đến 40 m/phút trong quá trình tạo phoi sẽ tỏa ra một lượng nhiệt rất lớn. Dưới tác dụng của lực, lớp kim loại bị ép vào mặt trước của dao, và với một nhiệt độ cao như vậy nó sẽ làm tăng hệ số ma sát và làm cho lớp kim loại dính vào mặt trước của dao (và C7 CLCTGC CGKL 11 GVC NGUYỄN THẾ TRANH - TRẦN QUỐC VIỆT một phần mặt sau) tạo thành lẹo dao. Trong khoảng tốc độ v = 20 ÷ 40 m/phút lẹo dao có giá trị lớn nhất và bền vững nhất. Nếu tiếp tục tăng tốc độ cắt, nhiệt tỏa ra sẽ nhiều hơn. Khi đó phần lẹo dao sẽ được đốt nòng nhanh hơn các phần còn lại và nó bị mềm ra, lực dính kết của lưởi dao không thắng nổi lực ma sát do phoi tạo ra do đó bị cuốn đi và phoi bị mất. Do vậy lẹo dao giảm dần trong khoảng tốc độ cắt v = 60 ÷ 70 m/phút và bị triệt tiêu. Độ nhấp nhô bề mặt phụ thuộc nhiều vào quá trình tạo phoi và ảnh hưởng đến tốc độ cắt đến chiều cao nhấp nhô (do hiện tượng lẹo dao tạo ra) khi cắt kim loại thể hiện bởi đồ thị: Hình 7.8 - Mối quan hệ giữa tốc độ cắt v và Rz Khi gia công vật liệu dòn (gang), đồng thời vối việc cắt kim loại sẽ xảy ra hiện tượng xô lệch, trược hoặc trọc kim loại ra không theo thứ tự sẽ làm tăng tốc độ nhấp nhô tế vi lớp bề mặt. Khi tăng tốc độ cắt sẽ giảm được hiện tượng vỡ vụn kim loại, làm giảm chiều cao nhấp nhô tế vi, tăng độ nhẵn bóng bề mặt. Lượng chạy dao s là thành phần thứ hai của chế độ cắt ảnh hưởng đến chiều cao nhấp nhô Rz. Điều đó không những do liên quan kể trên về kết cấu hình học của dao mà còn do biến dạng dẻo và biến dạng đàn hồi của lớp bề mặt ngoài. Khi cắt kim loại bằng dso tiện cạnh cắt bao giờ củng có bán kính cong ϕ (tuy nhỏ). Khi tiến dao vào bề mặt gia công phoi sẽ tách ra theo mặt phẳng A-A. Lúc đó phần kim loại nằm dưới điểm B sẽ không được cắt mà bị nén xuống (do cạnh cắt cong ϕ ) gây nên biến dạng đàn hồi và biến dạng dẻo. Sau khi dao đi qua, phần kim loại chưa được cắt ( bị nén xuống) sẽ có biến dạng đàn hồi một phần sẽ trở về hướng của dao và gây nên ma sát ở mặt sau của dao. C7 CLCTGC CGKL 12 GVC NGUYỄN THẾ TRANH - TRẦN QUỐC VIỆT Hình 7.9 - Nhấp nhô hình thành do bán kính mũi dao Mức độ biến dạng đàn hồi khác nhau của đỉnh và đáy các nhấp nhô sẽ làm tăng chiếu cao nhấp nhô của bề mặt sau khi gia công cơ. Chiều dày nhỏ nhất Tmin sẽ phụ thuộc vào tính chất vật liệu gia công và tốc độc cắt.. Nếu giảm bán kính và tăng yốc độ cắt thì Tmin sẽ giảm. Hình 7.10 - Ảnh hưởng của tốc độ cắt v và chiều sâu cắt Tmin đến Rz Khi tiện mỏng bằng dao tiện có bán kính đỉnh là r, về lý thuyết thì sẽ tạo ra phoi có chiều dày cắt thay đổi và đỉnh thì nhỏ. Một phần A-B của đỉnh này có chiều dàu cắt nhỏ hơn Tmin do đó không cắt mà bị nén lại( hình. 2-2a) phần kim loại thực tế chỉ được cắt ở đoạn B-C vì có chiều dày lớn hơn chiều sâu cắt tối thiểu tmin. Sau khi dao tiện đi qua, phần kim loại đã biến dạng lại phần nào( biến dạng đàn hồi) và làm tăng chiều cao nhấp nhô đến Rztt. Chiều cao nhấp nhô thực tế Rztt chỉ bằng 2 S /8r trong trường hợp lượng chạy dao lớn sao cho S2/8r >=tmin. Khi cắt với lượng chạy dao nhỏ (s<0.05mm/vòng) bán kính cạnh cắt r = 0. 8 ÷1mm chiều cao nhấp nhô không những không được giảm đi mà lại tăng lên vì nó đã giảm chiều sâu cắt của phoi và làm tăng chiều dày đoạn kim loại biến dạng A-B. (hình. 22b). Trong trường hợp giảm lượng chạy dao s tì áp lực sẽ tăng, mức độ biến dạng dẻo của bề mặt gia công và của phoi cũng tăng, làm tăng nhấp nhô Rz. Khi tiện với lượng chạy dao s<0, 12mm/vòng thì chiều cao nhấp nhô không giảm theo đường cong parabol S2/8r mà nhấp nhô sẽ giảm một ít theo đường cong (2) hoặc tăng theo đường cong (1). C7 CLCTGC CGKL 13 GVC NGUYỄN THẾ TRANH - TRẦN QUỐC VIỆT Hình 7.11 - Quan hệ giữa lượng chạy dao s với Rz. Trong phần gạch chéo sẽ xảy ra tăng chiều cao nhấp nhô bề mặt do biến dạng dẻo và biến dạng đàn hồi. Như vậy ngay cả khi gia công với lượng chạy dao nhỏ nhất vẫn không thể loại trừ hoàn toàn độ nhấp nhô bề mặt, mà trong trường hợp đó chiều cao nhấp nhô xác định bởi chiều dày nhỏ nhất và biến dạng dẻo của vật liệu gia công. Như trên hình. 2-21, khi lượng chạy dao s thay đổi trong khoảng 0. 02 ÷0. 1 mm/vòng rất ít ảnh hưởng đến chiều cao nhấp nhô. Cho nên để đảm bảo độ nhấp nhô nhỏ nhất và năng suất cao khi tiện tinh thép cacbon, cần chọn lượng chạy dao trong khoảng s =0.05 ÷ 0.12mm/vòng. Khi gia công hợp kim màu bằng dao kim cương thì giá trị s có thể giảm, vì vậy để giảm chiều cao nhấp nhô có thể cho lượng chạy dao s = 0.01 ÷ 0.03 mm/vòng. chiều sâu cắt không ảnh hưởng đến chiều cao nhấp nhô nhưng nếu giảm đến 0.02 ÷ 0.03 mm thì lưởi cắt sẽ trược trên bề mặt gia công, nó sẽ theo chu kỳ ăn vào bề mặt gia công và cắt thành những đoạn rời rạc, gây ảnh hưởng sấu đến chất lượng bề mặt. Vậy không nên chọn chiều sâu cắt quá bé. Vật liệu dẻo và dai (thép ít cacbon) sẽ biến dạng dẻo nhiều và độ nhấp nhô bề mặt lớn. Để giảm chiều cao nhấp nhô cần phải tiến hành thường hóa thép cacbon ở nhiệt độ 850 ÷ 870 0 C và ram ở nhiệt độ 900 0 C trong vòng năm giờ. Nhiều thí nghiệm chứng tỏ rằng:khi độ cứng aang lên thì chiều cao nhấp nhô giảm. Giảm tình dẻo của vật liệu bằng biến chứng bề mặt cũng làm giảm chiều cao nhấp nhô, sử dụng dung dịch trơn nguội làm giảm ma sát phoi dễ tách ra và chiều cao nhấp nhô cũng giảm. 3. Ảnh hưởng của độ cứng vững của hệ thống công nghệ và rung động đến độ nhấp nhô bề mặt. Hiện tượng rung động trong quá trình cắt sẽ tạo ra chuyển động tương đối có chu kỳ giữa dụng cụ cắt và bề mặt chi tiết bia công, làm thay đổi điều kiện ma sát gây nên độ sóng và độ nhấp nhô tế vi trên bề mặt gia công. Sai lệch của các bộ phận mấy làm chuyển động của nó không ổn định sẽ gây ra dao dộng cưởng bức của hệ thống công nghệ. Khi hệ thống công nghệ bị dao động, độ sóng và nháp nhô tế vi sẽ tăng nếu chiều sâu cắt lớn, lực cắt tăng và tốc độ tăng cao. Muốn đạt được độ nhấp nhô tế vi thấp trước hết phải đảm bảo độ cứng vững của hệ thống công nghệ, điều chỉnh máy tốt và không để cho rung động của các máy sung quanh truyền tới nó, đồng thời nâng cao độ chính xác của các chi tiết truyền động, cân bằng các chi tiết có chuyển động C7 CLCTGC CGKL 14 GVC NGUYỄN THẾ TRANH - TRẦN QUỐC VIỆT quay nhanh, tránh va đập khi gia công các bề mặt có yêu cầu chính xác cao. Dùng cơ cấu giảm rung và cách ly với xung quanh. Ngoài dao động cưởng bức khi cắt gọt kim loại còn tồn tại hiện tượng tự rung. Hiện tượng tự rung này do chính bản thân quá trình chuyển động khi cắt gây ra, khi ngưng chuyển động thì hiện tượng tự rung cũng kết thúc. 7.3.2. CÁC NGUYÊN NHÂN ẢNH HƯỞNG ĐẾN ĐỘ BIẾN CỨNG BỀ MẶT Quá trình biến cứng kim loại ở bề mặt ngoài của chi tiết phát triển dưới tác dụng của lực cắt. Cường độ và chiều sâu biến cứng sẽ tăng khi lực cắt tăng, thời gian tác động kéo dài và mức độ biến dạng dẻo lớn. Song song với hiện tượng biến cứng có hiện tượng biến mềm do tác dụng nhiệt trong vùng cắt. Khi nhiệt độ nung nóng cao và thời gian dài thì hiện tượng biến mềm sẽ làm cho chi tiết hết biến cứng mà nó được tạo ra trong quá trình gia công cơ. Trạng thái cuối cùng của kim loại bề mặt ngoài phụ thuộc vào mức độ tác động của lực và nhiệt. Mức độ chiều sâu biến cứng thay đổi phụ thuộc vào phương pháp gia công, chế độ cắt, hình dạng hình học của dao cắt. Thay đổi chế độ cắt làm cho lực cắt thay đổi, mức độ biến dạng dẻo tăng và làm tăng mức độ biến dạng cứng. Thời gian tác động lực kéo dài cũng làm tăng chiều sâu biến cứng. Thay đổi chế độ cắt làm tăng nhiệt độ trong vùng cắt và làm kim loại biến mềm. Trong thực tế, ảnh hưởng nhiệt độ cắt đến độ biến cứng rất phức tạp bởi vì còn có lực ma sát, điều kiện thoát nhiệt từ vùng cắt, cấu trúc kim loại thay đổi. Aính hưởng của chế độ cắt đến độ biến cứng được thể hiện bằng các đồ thị sau: Hình 7.12- Ảnh hưởng của lượng chạy dao s và bán kính mủi dao r đến độ biến cứng bề mặt chi tiết máy C7 CLCTGC CGKL 15 GVC NGUYỄN THẾ TRANH - TRẦN QUỐC VIỆT Hình 7.13 - Ảnh hưởng của góc trước γ đến lớp biến cứng bề mặt. Góc trước tăng từ âm đến dương thì mức độ và chiều sâu lớp biến cứng giảm. Điều kiện trên làm giảm lực cắt, do đó làm giảm mức độ biến dạng dẻo và biến cứng giảm. Trong trường hợp ngược lại, γ giảm dần sẽ gây biến cứng tăng dần. Vận tốc cắt có tác dụng kéo dài hoặc rút ngắn thời gian tác động của lực cắt và nhiệt độ cắt trên bề mặt gia công chi tiết. Khi tăng vận tốc cắt thời gian tác động của lực biến dạng giảm cho nên chiếu sâu biến cứng giảm. Đồng thời khi tăng vận tốc cắt, ma sát sẽ tăng và nhiệt độ tỏa ra nhiều, cho nên đối với những kim loại khó thay đổi cấu trúc tinh thể khi tăng vận tốc cắt thì độ biến cứng sẽ giảm. Đối với những kim loại dễ thay đổi cấu trúc tinh thể khi tăng tốc độ cắt thì độ biến cứng sẽ tăng. Trong thực tế chiều sâu lớp biến cứng thường ứng với trị số nhiệt cắt cố định. khi tăng lượng tiện dao s chiều sâu biến cứng có lúc tăng, có lúc giảm vì yếu tố quyết định là nhiệt cắt. Ngoài ra dụng cụ cắt bị mòn cũng làm tăng chiều sâu lớp biến cứng. 7.3.3 CÁC NGUYÊN NHÂN ẢNH HƯỞNG ĐẾN ỨNG SUẤT DƯ BỀ MẶT Khi cắt quá trình hình thành ứng suất dư trên lớp bề mặt quyết định bởi biến dạng đàn hồi, biến dạng dẻo, biến đổi nhiệt và chuyển pha trong kim loại, quá trình này rất phức tạp. Trong nhiều trường hợp khi thay đổi phương pháp gia công và chế độ cắt thường dẫn tới tăng ảnh hưởng của lực và biến dạng dẻo làm tăng ứng suất dư nén, giảm ứng suất dư kéo. Thực chất có nhiều nguyên nhân ảnh hưởng đến ứng suất dư lớp bề mặt, tuy nhiên rất khó xác lập quan hệ cụ thể. Nếu đánh giá một cách định tính như sau: • Khi tăng tốc độ cắt cũng có thể tăng, cũng có thể giảm ứng suất tiếp. Khi v tăng từ 50 ÷ 200 m/phút thường làm cho ứng suất tiếp giảm xuống. • Khi bước tiến s tăng lên sẽ làm tăng chiều sâu có ứng suất dư. • Khi gia công bằng dao có lưỡi, nếu cắt vật liệu giòn sẽ gây ra ứng suất dư nén, còn khi cắt vật liệu dẻo sẽ gây ra ứng suất dư kéo. • Mà bằng đá mài bề mặt gia công có ứng suất dư kéo lớn, còn mài bằng đai mài có ứng suất dư nén. • Trong điều kiện gia công cụ thể có thể suất hiện những ứng suất tiếp tuyến và ứng suất hướng trục trái dấu nhau.
File đính kèm:
bai_giang_co_so_cat_got_kim_loai_chuong_7_chat_luong_chi_tie.pdf