Giáo trình Cơ sở cắt gọt kim loại
Gia công kim loại bằng cắt gọt là một phương pháp gia công kim loại rất phổ biến trong
ngành cơ khí chế tạo máy.
Quá trình cắt kim loại là quá trình con người sử dụng dụng cụ cắt để hớt bỏ lớp kim
loại thừa khỏi chi tiết, nhằm đạt được những yêu cầu cho trước về hình dáng, kích thước, vị
trí tương quan giữa các bề mặt và chất lượng bề mặt của chi tiết gia công.
Lớp kim loại thừa trên chi tiết cần hớt bỏ đi gọi là lượng dư gia công cơ.
Lớp kim loại đã bị cắt bỏ khỏi chi tiết gọi là phoi cắt.
Bạn đang xem 20 trang mẫu của tài liệu "Giáo trình Cơ sở cắt gọt kim loại", để tải tài liệu gốc về máy hãy click vào nút Download ở trên
Tóm tắt nội dung tài liệu: Giáo trình Cơ sở cắt gọt kim loại
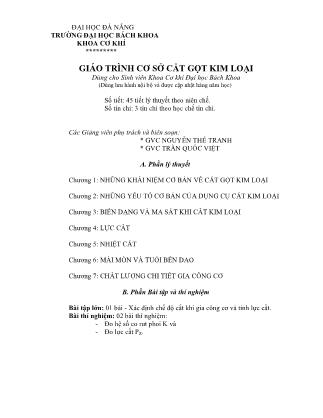
ĐẠI HỌC ĐÀ NẴNG TRƯỜNG ĐẠI HỌC BÁCH KHOA KHOA CƠ KHÍ ********* GIÁO TRÌNH CƠ SỞ CẮT GỌT KIM LOẠI Dùng cho Sinh viên Khoa Cơ khí Đại học Bách Khoa (Dùng lưu hành nội bộ và được cập nhật hàng năm học) Số tiết: 45 tiết lý thuyết theo niên chế. Số tín chỉ: 3 tín chỉ theo học chế tín chỉ. Các Giảng viên phụ trách và biên soạn: * GVC NGUYỄN THẾ TRANH * GVC TRẦN QUỐC VIỆT A. Phần lý thuyết Chương 1: NHỮNG KHÁI NIỆM CƠ BẢN VỀ CẮT GỌT KIM LOẠI Chương 2: NHỮNG YẾU TỐ CƠ BẢN CỦA DỤNG CỤ CẮT KIM LOẠI Chương 3: BIẾN DẠNG VÀ MA SÁT KHI CẮT KIM LOẠI Chương 4: LỰC CẮT Chương 5: NHIỆT CẮT Chương 6: MÀI MÒN VÀ TUỔI BỀN DAO Chương 7: CHẤT LƯỢNG CHI TIẾT GIA CÔNG CƠ B. Phần Bài tập và thí nghiệm Bài tập lớn: 01 bài - Xác định chế độ cắt khi gia công cơ và tính lực cắt. Bài thí nghiệm: 02 bài thí nghiệm: - Đo hệ số co rut phoi K và - Đo lực cắt PZ. C 1 KNCB CGKL 1 GVC NGUYỄN THẾ TRANH - TRẦN QUỐC VIỆT Chương 1 NHỮNG KHÁI NIỆM CƠ BẢN VỀ CẮT GỌT KIM LOẠI Gia công kim loại bằng cắt gọt là một phương pháp gia công kim loại rất phổ biến trong ngành cơ khí chế tạo máy. Quá trình cắt kim loại là quá trình con người sử dụng dụng cụ cắt để hớt bỏ lớp kim loại thừa khỏi chi tiết, nhằm đạt được những yêu cầu cho trước về hình dáng, kích thước, vị trí tương quan giữa các bề mặt và chất lượng bề mặt của chi tiết gia công. Lớp kim loại thừa trên chi tiết cần hớt bỏ đi gọi là lượng dư gia công cơ. Lớp kim loại đã bị cắt bỏ khỏi chi tiết gọi là phoi cắt. Hiểu biết và vận dụng tốt những kết quả nghiên cứu về cắt gọt giúp tạo ra các chi tiết, các sản phẩm cơ khí ngày càng hoàn hảo và nền cơ khí chế tạo hiện đại ngày càng phát triển. Mặt khác những thành tựu trong lĩnh vực nghiên cứu cắt gọt đã góp phần vào việc tính toán thiết kế máy, dao, đồ gá và công nghệ một cách chính xác và kinh tế. 1.1. HỆ THỐNG CÔNG NGHỆ SỬ DỤNG TRONG GIA CÔNG CẮT GỌT. Muốn hoàn thành nhiệm vụ cắt gọt, con người phải sử dụng một hệ thống thiết bị nhằm tách được lớp kim loại thừa khỏi chi tiết, đồng thời phải đảm bảo các yêu cầu kỹ thuật đã cho trên bản vẽ. Hệ thống thiết bị dùng để hoàn thành nhiệm vụ cắt gọt đó được gọi là hệ thống công nghệ. Hệ thống công nghệ bao gồm: máy, dao, đồ gá và chi tiết gia công, thường được viết tắt là hệ thống M - D - G - C. Trong đó: Máy có nhiệm vụ cung cấp năng lượng và các chuyển động cần thiết cho quá trình cắt gọt. Dao trong hệ thống công nghệ có nhiệm vụ trực tiếp cắt bỏ lớp lượng dư ra khỏi chi tiết nhờ năng lượng của máy cung cấp thông qua các chuyển động tương đối. Đồ gá là một bộ phận của hệ thống công nghệ có nhiệm vụ xác định và giữ vị trí tương quan chính xác giữa dao và chi tiết gia công trong suốt quá trình gia công chi tiết. Chi tiết gia công là một thành phần của hệ thống công nghệ - là đối tượng của quá trình cắt gọt. Mọi hậu quả của quá trình cắt đều được phản ảnh lên chi tiết gia công. Tất nhiên để hoàn thành nhiệm vụ cắt gọt, mỗi bộ phận của hệ thống công nghệ có nhiệm vụ riêng, đồng thời phải có mối quan hệ tác động lẫn nhau. 1.2. CÁC PHƯƠNG PHÁP CẮT GỌT KIM LOẠI. Bề mặt gia công trên chi tiết rất đa dạng, vì vậy phải có nhiều phương pháp cắt gọt để thoả mãn những yêu cầu đa dạng đó. Xuất phát từ mục đích nghiên cứu, sử dụng khác nhau, có nhiều cách phân loại các phương pháp gia công: Xuất phát từ nguyên lý tạo hình bề mặt ta phân ra phương pháp gia công chép hình, phương pháp gia công định hình,phương pháp gia công bao hình. Xuất phát từ yêu cầu kỹ thuật của chi tiết gia công ta có gia công thô, gia công bán tinh, gia công tinh và gia công bóng. Phổ biến hơn cả là phân loại theo máy gia công. Theo cách phân loại này ta có: Gia công trên máy tiện, gia công trên máy phay, gia công trên máy bào, gia công trên máy khoan, gia công trên máy mài... Ngoài ra còn căn cứ vào bề mặt gia công ta phân ra: gia công mặt phẳng, gia công mặt trụ ngoài, gia công lỗ, gia công rãnh... C 1 KNCB CGKL 2 GVC NGUYỄN THẾ TRANH - TRẦN QUỐC VIỆT 1.3. BỀ MẶT ĐƯỢC HÌNH THÀNH TRÊN CHI TIẾT TRONG QUÁ TRÌNH CẮT. Bất kỳ phương pháp gia công nào, quá trình hớt bỏ dần lớp lượng dư gia công cơ (quá trình cắt) đều hình thành trên chi tiết ba bề mặt có đặc điểm khác nhau. Xét tại một thời điểm nào đó trong quá trình gia công (khi tiện), ba bề mặt trên chi tiết được phân biệt như hình 1.1. Vïng c¾t MÆt ®· gia c«ng MÆt ®ang gia c«ng MÆt sÏ gia c«ng n t s Hình 1.1 Mặt sẽ gia công là bề mặt củ phoi mà dao sẽ cắt đến theo qui luật chuyển động. Tính chất của bề mặt này là tính chất bề mặt phoi. Mặt đang gia công là bề mặt trên chi tiết mà lưỡi dao đang trực tiếp thực hiện tách phoi. Trên bề mặt này đang diễn ra các hiện tượng cơ-lý phức tạp. Mặt đã gia công là bề mặt trên chi tiết mà dao đã cắt qua. Tính chất của bề mặt này là phản ảnh những kết quả của các hiện tượng cơ-lý trong quá trình cắt. Vùng cắt là phần kim loại của chi tiết vừa được tách ra sát mũi dao và lưỡi cắt cảu dao nhưng chưa thoát ra ngoài. Đây là vùng đang xảy ra các quá trình cơ-lý phức tạp. 1.4. CÁC CHUYỂN ĐỘNG CẮT GỌT. Tuỳ thuộc vào phương pháp gia công, tuỳ thuộc vào yêu cầu tạo hình bề mặt, hệ thống công nghệ cần tạo ra những chuyển động tương đối nhằm hình thành nên bề mặt cần gia công. Những chuyển động tương đối nhằm hình thành bề mặt gia công gọi là chuyển động cắt gọt. Những chuyển động cắt gọt được phân làm hai loại chuyển động: - Chuyển động chính - Các chuyển động phụ 1.4.1. Chuyển động chính và tốc độ cắt v Chuyển động chính là chuyển động tạo ra phoi và tiêu hao năng lượng cắt lớn nhất. Chuyển động chính có thể là chuyển động quay tròn như tiện, khoan, phay, mài; cũng có thể là chuyển động tịnh tiến như bào, xọc, chuốt. MÆt ®· gia c«ng MÆt ®ang gia c«ng MÆt sÏ gia c«ng Vïng c¾t C 1 KNCB CGKL 3 GVC NGUYỄN THẾ TRANH - TRẦN QUỐC VIỆT Chuyển động chính có thể là do các cơ cấu chấp hành khác nhau thực hiện. Ví dụ do chi tiết thực hiện như trong tiện; do dao thực hiện như trong bào, xọc, khoan, phay. Để đặc trưng cho chuyển động chính, ta sử dụng hai đại lượng: - Số vòng quay n (hoặc số hành trình kép) trong đơn vị thời gian. Số đo là vg/ph, htk/ph. Theo hệ ISO ký hiệu là S (Speed). - Tốc độ chuyển động chính hay gọi là vận tốc cắt (tốc độ cắt) ký hiệu là v. Đơn vị là m/ph. Riêng tốc độ cắt trong trường hợp mài lấy đơn vị là m/sec. Tốc độ cắt v là lượng dịch chuyển tương đối giữa dao và chi tiết theo phương vận tốc cắt v ứng với một đơn vị thời gian (ph). Nếu chuyển động chính là chuyển động quay tròn, thì giữa vận tốc cắt (v), số vòng quay n (vg/ph) và đường kính chi tiết D (mm) có quan hệ sau: 1000 Dnv (m/ph) (1.1) Nếu chuyển động chính là chuyển động tịnh tiến, thì giữa vận tốc cắt v (m/ph), số hành trình kép n (hkt/ph) và chiều dài hành trình L (mm) có quan hệ sau: 2 1000 Lnv (m/ph) (1.2) 1.4.2. Các chuyển động phụ Chuyển động phụ là những chuyển động tiếp tục tạo phoi. Như ta đã biết: lớp lượng dư là một khối không gian, do vậy để tách hết lớp không gian đó thì số chuyển động tối thiểu phải được thực hiện theo ba phương của hệ trục toạ độ không gian vuông góc. Như vậy ngoài chuyển động chính cần phải có hai chuyển động nữa vuông góc với nhau và vuông góc với phương chuyển động chính. Hai chuyển động này trong cắt gọt kim loại là chuyển động chạy dao và chuyển động theo phương chiều sâu cắt. (hình 1.1) 1. Chuyển động chạy dao và lượng chạy dao s. Chuyển động chạy dao là một chuyển động phụ nhằm cắt hết lượt trên bề mặt chi tiết. Phương chuyển động chạy dao được ký hiệu là s . Để đặc trưng cho chuyển động chạy dao, thường dùng các đại lượng: - Lượng chạy dao, ký hiệu là s, là lượng dịch chuyển tương đối giữa dao và chi tiết theo phương chạy dao tương ứng với 1 vòng quay (hoặc 1 hành trình kép) của chuyển động chính. Đơn vị đo là mm/vòng hoặc mm/htk. - Tốc độ chạy dao, ký hiệu là vs, là lượng dịch chuyển tương đối giữa dao và chi tiết theo phương chạy dao ứng với một đơn vị thời gian. Đơn vị tính là mm/ph. Theo ISO ký hiệu là F. - Lượng chạy dao răng. Khi dao có nhiều lưỡi cắt (nhiều răng dao) thì ngoài lượng chạy dao s, tốc độ chạy dao vs, ta còn dùng khái niệm lượng chạy dao răng để biểu thị chuyển động chạy dao, ký hiệu là sz, là lượng dịch chuyển tương đối giữa dao và chi tiết theo phương chạy dao ứng với khi dao quay một góc răng dao, ví dụ trong trường hợp phay. Đơnvị tính là mm/răng. Với những định nghĩa trên ra có mối quan hệ giữa vs, s và sz, như sau: . . .s zv s n s Z n [mm/ph ] (1.3) Z: là số răng hoặc số lưỡi cắt trên dao. C 1 KNCB CGKL 4 GVC NGUYỄN THẾ TRANH - TRẦN QUỐC VIỆT 2. Chuyển động theo phương chiều sâu cắt và chiều sâu cắt Chuyển động theo phương chiều sâu cắt là một chuyển động phụ nhằm cắt hết chiều dày lớp lượng dư gia công cơ. Chuyển động chiều sâu cắt là chuyển động gián đoạn được thực hiện sau mỗi lần chạy dao. Đại lượng do chuyển động chiều sâu cắt là chiều sâu cắt t, là lượng dịch chuyển tương đối giữa dao và chi tiết theo phương chiều sâu cắt ứng với mỗi lần chạy dao. Đơn vị tính là mm. Trong cắt gọt kim loại người ta gọi các đại lượng đặc trưng của chuyển động chính và các chuyển động phụ (v,s,t) là chế độ cắt khi gia công cơ. 1.5. LỚP CẮT VÀ TIẾT DIỆN LỚP CẮT. Lớp kim loại bị hớt bỏ đi ứng với một vòng quay hay một hành trình kép của chuyển động chính gọi là lớp cắt. Nếu cắt lớp cắt bằng một mặt phẳng chứa lưỡi cắt và vuông góc với vectơ vận tốc cắt v ta sẽ nhận được những tiết diện lớp cắt. (hình 1.2) Hình 1.2: Các loại tiết diện lớp cắt khi tiện Tiết diện lớp cắt có ý nghĩa quan trọng trong công tác nghiên cứu cắt gọt kim loại. Từ hình 1.2 ta dễ dàng nhận thấy độ lớn của tiết diện lớp cắt (diện tích) được đặc trưng bởi hai cặp kích thước: a,b và s,t. Trong đó: a là chiều dày lớp cắt là một kích thước của tiết diện lớp cắt được đo theo phương vuông góc với lưỡi cắt chính - tính bằng mm. b là chiều rộng lớp cắt là một kích thước khác của tiết diện lớp cắt, b chính là chiều dài cắt thực tế của lưỡi cắt - tính bằng mm. s và t là hai thông số của các chuyển động phụ. Cũng từ hình 1.2 rõ ràng là: Trong trường hợp cắt a thì a # s, t # b và giữa chúng có mối quan hệ sau: a = s.sin , b = t/sin Trường hợp b. thì a = s và t = b. Đặc biệt trong trường hợp c. thì chiều dày cắt a thay đổi trên suốt chiều dài làm việc thực tế của lưỡi cắt. Để đặc trưng chiều dày cắt, người ta dùng khái niệm chiều dày cắt trung bình - ký hiệu là atb. Ta gọi q là diện tích tiết diện lớp cắt - đơn vị tính là mm2, thì theo hình 1.2, một cách tổng quát ta có thể viết: . .tbq s t a b (mm 2) (1.4) n s t b ts a o n s t ao t s b s t b n t s C 1 KNCB CGKL 5 GVC NGUYỄN THẾ TRANH - TRẦN QUỐC VIỆT Từ (1.4) ta có: .tb s ta b (mm) (1.5) Cần nhấn mạnh là: độ lớn của tiết diện lớp cắt được đặc trưng bằng hai cặp thông số s,t và a,b. Trong đó chiều rộng cắt b là chiều dài thực tế của lưỡi cắt, và chiều dày cắt a là chiều dày lớp kim loại cần tách trong một lần chạy dao. Đây là hai thông số mà độ lớn của nó ảnh hưởng rất lớn đến quá trình cắt gọt. Vì vậy trong nghiên cứu cắt gọt, người ta dùng hai thông số này để giải thích nhiều hiện tượng cơ-lý phức tạp xảy ra khi cắt kim loại. Cũng chính vì vậy mà hai thông số chiều dày cắt và chiều rộng cắt có ý nghĩa vật lý quan trọng trong công tác nghiên cứu. Tuy vậy a và b là hai thông số không thể nhận được bằng cách điều chỉnh máy, mà băng điều chỉnh máy thì chỉ có thể nhận được chiều sâu cắt t và lượng chạy dao s. Xuất phát từ yêu cầu lý thuyết giải thích bản chất quá trình cắt gọt xà xuất phát từ yêu cầu điều chỉnh sử dụng thực tế mà người ta phải đồng thời sử dụng hai cặp thông số đặc trưng cho tiết diện lớp cắt. C 2 YTCB DCCKL 1 GVC NGUYỄN THẾ TRANH - TRẦN QUỐC VIỆT Chương 2 NHỮNG YẾU TỐ CƠ BẢN CỦA DỤNG CỤ CẮT KIM LOẠI Dụng cụ cắt hay còn gọi là dao là bộ phận của hệ thống công nghệ có nhiệm vụ trực tiếp tách phoi để hình thành bề mặt gia công. Kinh nghiệm cho thấy: dao có ảnh hưởng rất lớn đến quá trình cắt gọt. Nó không những tác động trực tiếp tới chất lượng chi tiết mà còn chi phối không nhỏ tới vấn đề năng suất và giá thành chế tạo sản phẩm. Vì lý do khách quan như vậy nên những hiểu biết về dao nhằm sử dụng chúng một cách hợp lý là một trong những trọng tâm của công tác nghiên cứu cắt gọt kim loại. Trong thực tế vì bề mặt gia công là muôn hình muôn vẻ, do đó dao để phục vụ gia công cũng rất đa dạng. Để thuận tiện cho công tác nghiên cứu, tuỳ thuộc vào mục đích yêu cầu nghiên cứu, sử dụng mà người ta phân loại dao thành các nhóm khác nhau. Ví dụ: Dựa vào vật liệu chế tạo dao thì có dao thép cacbon dụng cụ, dao thép hợp kim dụng cụ, dao thép gió, dao hợp kim cứng, dao kim cương... Dựa vào yêu cầu tính chất gia công dao được phân ra: dao gia công thô, dao gia công tinh, dao gia công bóng. Dựa vào số lưỡi cắt trên dao ta lại có các loại: loại một lưỡi cắt (như dao tiện, dao bào), dao hai lưỡi cắt (như mũi khoan), dao nhiều lưỡi cắt tiêu chuẩn (như dao phay, dao chuốt), dao phi tiêu chuẩn nhiều lưỡi cắt (như đá mài). Dựa vào kết cấu và đặc điểm làm việc ta có loại dao thường và loại dao định hình. Phổ biến hơn cả là căn cứ vào phương pháp gia công ta chia ra dao tiện, dao phay, mũi khoan, dao khoét, dao doa, đá mài, dao chuốt... Trong tất cả các loại dao, do đặc điểm cấu tạo, dao tiện được coi là dao điển hình nhất. Tất cả những loại dao khác chẳng qua là sự phân tích hoặc tổng hợp của dao tiện. Vì vậy khi nghiên cứu về dao thì những nét chung nhất đều được minh hoạ bằng ví dụ dao tiện. Tiếp theo ta lần lượt nghiên cứu một số vấn đề cơ bản về dụng cụ cắt kim loại. 2.1. Kết cấu của dụng cụ cắt kim loại Dao cắt kim loại được cấu tạo bởi ba phần: phần làm việc còn gọi là phần cắt, phần gá đặt dao và phần cán dao (hình 2.1). Phần làm việc của dao (phần cắt) là phần của dao trực tiếp tiếp xúc với chi tiết gia công để làm nhiệm vụ tách phoi, đồng thời còn là phần dự trữ mài dao lại khi dao đã bị mòn. Phần gá đặt dao là một bộ phận của dao dùng để gá đặt dao lên máy nhằm bảo đảm vị trí tương quan giữa dao và chi tiết. Phần thân dao cũng là một phần trên dao nối liền giữa phần cắt và phần gá đặt dao. Để hoàn thành tốt nhiệm vụ cắt gọt, về mặt kết cấu thì phần cắt của dao được tạo bởi các bề mặt và lưỡi cắt thích hợp, bao gồm: C 2 YTCB DCCKL 2 GVC NGUYỄN THẾ TRANH - TRẦN QUỐC VIỆT MÆt tríc MÆt c¾t phô MÆt sau phô PhÇn th©n dao PhÇn c¾tMòi dao Lìi c¾t chÝnh MÆt sau chÝnh PhÇn g ¸®Æt Hình 2.1. Kết cấu của dao (1) Mặt trước dao là mặt của dao để phoi trượt lên đó thoát ra khỏi vùng cắt trong quá trình gia công. (2) Mặt sau chính là mặt của dao đối diện với bề mặt đang gia công trên chi tiết. Vị trí tương quan của mặt này với mặt đang gia công của chi tiết quyết định mức độ ma sát giữa mặt sau chính dao và mặt đang gia công trên chi tiết. (3) Mặt sau phụ là mặt trên phần cắt dao đối diện với bề mặt đã gia công trên chi tiết. ý nghĩa của nó tương tự như ... , t3 (t1 + t2 + t3 = h). Sẽ giới thiệu cụ thể trong công nghệ chế tạo máy. 2. Vấn đề tận lượng tăng lượng chạy dao s h t m ax a b h t m ax Hình 8.1 - Chọn t C8 BPCTDKC CGKL 3 GVC NGUYỄN THẾ TRANH - TRẦN QUỐC VIỆT Với chiều sâu cắt t đã được lựa chọn, việc tăng lượng chạy dao s sẽ bị hạn chế bởi lực cắt, vì nếu lực cắt quá lớn sẽ làm cho hệ thống công nghệ biến dạng quá lớn dẫn đến sai số gia công vượt quá giới hạn cho phép. Thường trong lý lịch các máy (hoặc trong sổ tay cắt gọt) người ta có quy định giá trị cho phép của lực tác dụng lên máy, lên dao và lên chi tiết. Vậy việc lựa chọn lượng chạy dao s phải chú ý thoả mãn: lực cắt thực tế sinh ra với chế độ cắt lựa chọn phải nhỏ hơn (hoặc tối đa là bằng) lực cắt cho phép P = [P] Trong phần phân tích lực cắt đã chỉ rõ: Thành phần lực cắt chính Pv tác dụng lên dao, nếu lực cắt chính vượt quá giới hạn bền của dao sẽ làm phá huỷ dao. Muốn đảm bảo dao làm việc được thì: ][... vpv yx pvv PKstCP pvpv Từ công thức trên ta tính được: pv pv y pv x pv v KtC Ps .. ][ 1 (mm/vòng) Thành phần lực cắt theo phương chạy dao Ps tác dụng lên máy. Nếu Ps quá lớn sẽ làm phá huỷ các cơ cấu yếu của máy đó là cơ cấu chạy dao. Như vậy, để máy làm việc an toàn thì: ][... sps yx pss PKstCP psps Từ công thức trên ta có: ps ps y ps x ps s KtC Ps .. ][ 2 (mm/vòng) Thành phần lực cắt theo phương chiều sâu cắt Pt tác dụng lên chi tiết gia công làm cho chi tiết bị biến dạng một lượng f. Để đảm bảo kích thước gia công thì biến dạng do lực cắt gây nên phải nhỏ hơn biến dạng cho phép [f] - tức là: f [f] [f] được cho dựa trên cơ sở giới hạn sai lệch cho phép - trong gia công thô tương đương với IT13. Từ quan hệ f [f] ta tính được lực giới hạn [Pt]. Tức là Pt [Pt]. Ta có: ][... tpt yx ptt PKstCP ptpt Suy ra lượng chạy dao s3. yt pt y pt x pt t KtC Ps .. ][ 3 Sau khi đã có s1, s2, s3 ta so sánh và chọn giá trị smin trong ba giá trị s đã tính làm lượng chạy dao tính toán hợp lý, tức là: st = stính = smin = min (s1, s2, s3 ) C8 BPCTDKC CGKL 4 GVC NGUYỄN THẾ TRANH - TRẦN QUỐC VIỆT Dựa trên stính tra trong lý lịch máy ta chọn giá trị lượng chạy dao kinh tế (schọn = sc) Cần lưu ý rằng: từ st, tìm sc = sm (lượng chạy dao thực tế có trên máy) sẽ có thể xuất hiện 3 khả năng: st = sm; st sm. Nếu st = sm thì sc = sm Nếu st < sm thì ta chú ý đảm bảo S.n constant tức là nếu sc < sm thì tăng một cấp n và ngược lại sc > sm thì giảm n một cấp (n là số vòng quay của trục chính máy được chọn sau khi tính vận tốc v) Cũng cần đặc biệt chú ý: nếu s1, s2, s3 khác nhau qua lớn, nếu chọn smin sẽ không sử dụng hết khả năng của hệ thống công nghệ. Chính vì vậy, trước khi chọn smin ta cần tìm mọi cách để làm cho s1, s2, s3 có giá trị gần nhau, bằng cách chọn hợp lý hệ thống công nghệ, cải thiện điều kiện cắt như tưới dung dịch trơn nguội... 3. Tính tốc độ cắt kinh tế: Sau khi xác định và s ta tiến hành tính toán tốc độ cắt kinh tế theo công thức tuổi bền dao. Tiếp tục để đảm bảo máy đã chọn có thể đảm bảo thực hiện gia công, ta cần kiểm nghiệm công suất động cơ. Công thức kiểm nghiệm là: Nc Nđc . (KW) 6120 .vPN vc (KW) trong đó: Pv (KG); v(m/ph) là hiệu suất của máy ( = 0,6 - 0,8) Tóm lại, xác định chế độ cắt kinh tế khi gia công thô được tiến hành theo trình tự sau: (1) Lựa chọn phương pháp gia công dựa vào hình dạng, kích thước chi tiết gia công đã cho trên bản vẽ. (2) Lựa chọn dao (hình dáng và vật liệu) trên cơ sở biết chi tiết và phương pháp gia công. (3) Chọn chiều sâu cắt t trên cơ sở lượng dư gia công h và hình dáng dao. (4) Tra các thành phần lực cho phép [Ps], [Pt], [Pv] trong lý lịch máy. (5) Tính toán lượng chạy dao hợp lý và xác định lượng chạy dao chọn (6) Tính tốc độ cắt kinh tế với t, s đã biết và điều kiện cắt khác đã chọn. (7) Kiểm nghiệm công suất động cơ. Để dễ thấy trình tự, cơ sở và quan hệ của các bước tiến hành ta xây dựng sơ đồ hình 8.2 8.1.3. Xác định chế độ cắt khi gia công tinh Đối với gia công tinh ngoài yêu cầu tách lớp lượng dư gia công cơ trong thời gian ngắn, yêu cầu đảm bảo độ bóng bề mặt ghi trên bản vẽ là yêu cầu quan trọng. Chi tiết gia công máy Chọn dao t [P] s v NC N®c Hình 8.2 – Sơ đồ tính chế độ cắt C8 BPCTDKC CGKL 5 GVC NGUYỄN THẾ TRANH - TRẦN QUỐC VIỆT Khi xác định độ lớn nhấp nhô, trước hết cần chú ý vật liệu gia công, hình dáng hình học của dao, và lượng chạy dao, đồng thời cần thấy rõ: nếu tốc độ cắt càng cao thì độ bóng đạt được càng cao. Do đặc điểm gia công tinh như trên, nên việc xác định chế độ cắt kinh tế khi gia công tinh cần thay đổi một ít so với gia công thô. Cụ thể trình tự tính toán như sau: (1) Chọn phương pháp gia công trên cơ sở bản vẽ chế tạo chi tiết đã cho (đặc biệt chú trọng yêu cầu độ bóng bề mặt). (2) Lựa chọn vật liệu hình dáng hình học dao trên cơ sở đã biết chi tiết gia công (vật liệu), phương pháp gia công, độ bóng bề mặt chi tiết. Chú ý khi gia công tinh cần chọn vật liệu dao cho phép cắt ở tốc độ cao. (3) Chọn chiều sâu cắt xuất phát từ lượng dư gia công và kết cấu của dao. (4) Tra bảng trong sổ tay cắt gọt để chọn lượng chạy dao theo độ bóng bề mặt, vật liệu gia công, hình dáng hình học của dao với sự lưu ý đến các gá trị tốc độ cắt thường dùng đối với vật liệu dao đã chọn. (5) Tính độ cắt theo tuổi bền dao. Nếu tốc độ cắt tính ra không đảm bảo yêu cầu độ bống thì cần giảm lượng chạy dao và tính lại đến khi nào thoả mãn yêu cầu thì thôi. (6) Kiểm nghiệm công suất động cơ trên cơ sở tính lực cắt chính Pv và tốc độ cắt đã tính ở bước 5 Những nguyên tắc xác định chế độ cắt kinh tế khi gia công thô và gia công tinh đã nêu ở trên là phổ biến cho tất cả các phương pháp gia công. Việc tính toán xác định chế độ cắt kinh tế là một bước quan trọng khi lập quy trình công nghệ gia công chi tiết. Cụ thể là: Trong sản xuất hàng loạt, sau khi xác định chế độ cắt kinh tế, ta lựa chọn trong phân xưởng những máy có khả năng hoàn thành việc gia công với chế độ cắt đã cắt một cách kinh tế nhất. Trong sản xuất hàng khối, trên cơ sở cắt kinh tế đã được xác định (số liệu hướng dẫn theo thống kê cho trong các bảng của sổ tay cắt gọt) ta tiến hành lựa chọn hoặc thiết kế máy theo yêu cầu. 8.2. BÔI TRƠN VÀ LÀM NGUỘI KHI CẮT. Một trong những biện pháp quan trọng nhằm cải thiện điều kiện cắt là tưới dung dịch trơn nguội vào vùng cắt trong quá trình gia công. Tưới dung dịch trơn nguội vào vùng cắt có ba tác dụng. (1) Tác dụng bôi trơn để tăng độ bóng bề mặt đã gia công. (2)Tác dụng làm nguội vùng cắt để tăng tuổi bền dao và giảm tác dụng xấu của nhiệt cắt đến hệ thống công nghệ. (3) Đẩy phoi ra khỏi vùng cắt (nhất là khi gia công phoi vụn, khoan lỗ sâu) Tác dụng bôi trơn và làm nguội là những mục tiêu cơ bản của việc tưới dung dịch trơn nguội. 8.2.1. Cơ sở của vấn đề bôi trơn làm nguội khi cắt 1. Cơ sở làm nguội bằng cách tưới dung dịch. Dung dịch được tưới vào vùng cắt lan truyền trên các bề mặt đã được đốt nóng do nhiệt cắt. Một phần dung dịch đã nhận bớt nhiệt lượng ở vùng cắt, phần khác bị bốc hơi cũng mang C8 BPCTDKC CGKL 6 GVC NGUYỄN THẾ TRANH - TRẦN QUỐC VIỆT một nhiệt lượng nhất định đi khỏi vùng cắt. Như vậy lượng dung dịch đưa vào đã chia xẻ bớt nhiệt lượng sinh ra trong vùng cắt nhờ vậy làm giảm nhiệt độ của vùng cắt. Điều này có lợi cho tuổi bền của dao, đồng thời cũng làm giảm bớt tác dụng nhiệt đến hệ thống công nghệ. Từ phân tích trên, rõ ràng tác dụng làm nguội chỉ là tác dụng đơn thuần về mặt vật lý. Thật vậy khi hệ số dẫn nhiệt, nhiệt dung, nhiệt hoá hơi của dung dịch càng lớn thì tác dụng làm nguội càng tăng. Ở đây cần lưu ý tới khả năng gây ẩm ướt của dung dịch. Hình 8.3 cho ta phân biệt một giọt dung dịch trên bề mặt và gây ẩm trên bề mặt. Hình 8.3.a biểu thị một giọt chất lỏng trên bề mặt hình 8.3.b biểu thị gây ẩm trên bề mặt. Khả năng gây ẩm phụ thuộc vào sức căng bề mặt của dung dịch. Những dung dịch có sức căng bề mặt lớn thì trong thời gian ngắn không dễ dàng đi vào các lỗ hổng nhỏ. Điều đó cho ta giải thích được khi tưới bằng nước có pha dung dịch gây ẩm có tác dụng làm nguội tốt hơn khi tưới là nước thường. Mặt khác ta thấy rằng bốc nhiệt bằng cách bốc hơi sẽ tăng lên nếu dung dịch được đưa vào vùng cắt với áp lực lớn, điều đó được giải thích bằng tác dụng liên tục hơn của màn sương dung dịch phun vào. Thực nghiệm cho thấy, nếu sử dụng hợp lý loại dụng dịch và phun với áp lực phù hợp nhiệt độ cắt có thể được giảm 100 - 1500C. 2. Cơ sở việc bôi trơn bằng cách tưới dung dịch: Tác dụng bôi trơn khi tưới dung dịch thể hiện ở việc làm giảm ma sát giữa mặt trước dao và phoi, giữa bề mặt sau dao và chi tiết. Trong đó việc giảm ma sát giữa mặt trước dao và phoi có tác dụng lớn đến việc nâng cao tuổi bền dao. Như ra đã biết: các chất hoạt tính bề mặt quyết định tác dụng bôi trơn của dung dịch. Ta biết rằng: khi tưới một chất lỏng lên bề mặt rắn, thì trên bề mặt vật rắn sẽ được phủ bởi một màng mỏng chất lỏng. Nếu cho vật rắn tiếp xúc và chuyển động tương đối với vật rắn khác, thì màng mỏng chất lỏng chính là màng đệm có tác dụng làm giảm ma sát giữa hai bề mặt tiếp xúc. Khi cắt giữa các bề mặt tiếp xúc trong vùng cắt có áp suất lớn và nhiệt độ cao. Do vậy dung dịch dùng để tưới vào muốn tạo được màng đệm cần phải được các chất hoạt tính bề mặt như mỡ, dầu thực vật, axit béo no... Các khu vực khi tiếp xúc cắt gọt có thể biểu diễn bằng mô hình ở hình 8.4. Khi cắt tại các vùng tiếp xúc bao giờ cũng xuất hiện các lỗ hỗng nhỏ. Nguyên nhân hình thành các lỗ Hình 8.3 - Sức căng bề mặt của chất lỏng V Hình 8.4 – Mô hình cắt 1 a. b. C8 BPCTDKC CGKL 7 GVC NGUYỄN THẾ TRANH - TRẦN QUỐC VIỆT hổng do sự xuất hiện và mất đi một cách đột ngột của các khối lẹo dao, cũng có thể do sự rạn nứt đột ngột của các bề mặt tiếp xúc. Vì nguyên nhân xuất hiện như vậy, nên khi mới hình thành các lỗ hổng này là những lỗ chân không . Khi tưới dung dịch trơn nguội được hút vào các lỗ hổng chân không đó bằng những đường mao dẫn (vết nứt tế vi). Đó chính là các nguyên nhân đưa dung dịch vào các vùng tiếp xúc và hình thành các màng đệm. Kết quả thí nghiệm cho thấy: nếu sử dụng hợp lý dung dịch bôi trơn, lực cắt sẽ giảm đượ chúng tôi 0 - 30%, mài mòn dao sẽ giảm và nhờ đó cho phép tăng tốc độ cắt 10 - 40%, độ bóng bề mặt gia công tăng được 1 - 2 cấp. 8.2.2. Các loại bôi trơn làm nguội 1. Các yêu cầu của chất bôi trơn - làm nguội. Để đạt được mục đích bôi trơn và làm nguội khi cắt, các chất bôi trơn - làm nguội phải đáp ứng được các yêu cầu sau: (1) Giảm được ma sát (2) Giảm được nhiệt độ. (3) Có khả năng giảm mài mòn (4) Làm tăng độ bóng bề mặt chi tiết (5) Tạo điều kiện đẩy phoi ra dễ dàng (6) Không gây tác hại đến sản phẩm gia công (như ăn mòn) (7) Không làm tổn hại đến hệ thống công nghệ (8) Không gây hại cho sức khoẻ con người. 2. Các chất bôi trơn làm nguội - khi cắt Tuỳ thuộc vào vật liệu gia công, đặc điểm phương pháp gia công thiết bị gia công, có thể sử dụng các loại chất bôi trơn - làm nguội sau: (1) Thể khí như CO2. (2) Thể lỏng như nước, nước xà phòng... (3) Thể rắn (như than chì, disulfatmôluypden) Trong cắt gọt kim loại thường dùng loại thể lỏng - được gọi là dụng dịch trơn - nguội. Dung dịch trơn nguội được phân làm ba nhóm chính: (1) Nhóm 1 là nhóm có tác dụng làm nguội là chủ yếu (các dung dịch nước điện ly). (2) Nhóm 2 là nhóm dung dịch làm nguội; một phần có tác dụng bôi trơn như dung dịch nước xà phòng, dung dịch emulxi. (3) Nhóm 3 là nhóm có tác dụng bôi trơn, một phần có tác dụng làm nguội như các chất dầu, mỡ... 3. Một số kinh nghiệm khi sử dụng dung dịch trơn - nguội Về nguyên tác chung, muốn chọn sử dụng hợp lý dung dịch trơn - nguội ta căn cứ vào ba yếu tố: (1) Vật liệu chi tiết gia công (2) Phương pháp gia công và tính chất gia công (3) Loại thiết bị gia công Một cách cụ thể theo kinh nghiệm ta có: C8 BPCTDKC CGKL 8 GVC NGUYỄN THẾ TRANH - TRẦN QUỐC VIỆT Chọn theo vật liệu gia công Khi gia công vật liệu dòn (gang, đồng thanh) thường không nên dùng dung dịch trơn - nguội chủ yếu ở đây là bảo vệ hệ thống công nghệ, bởi vì khi cắt vật liệu dòn sẽ tạo ra phoi vụn, dung dịch trơn nguội dễ cuốn vào các khe hở lắp ghép của mát, đồ gá, làm tổn hại thiết bị. Cùng gia công vật liệu dòn, nhưng nếu hệ thống che chắn và bảo vệ tốt, dẫn dung dịch trơn nguội vào vùng cắt bằng những phương pháp tiên tiến như dẫn bên trong (khi khoan lỗ sâu), tưới, thổi (thể khí) với áp lực lớn thì khi sử dụng chất trơn - nguội cho phép tăng tốc độ cắt lên 15-30% so với không bôi trơn làm nguội. Khi chọn loại dung dịch trơn - nguội cần đặc biệt chú ý tránh gây phản ứng hoá học giữa dung dịch trơn - nguội và vật liệu gia công. Chọn vật liệu theo phương pháp gia công: cần lưu ý: (1) Khi gia công thô: nhiệt cắt, lực cắt và công suất cắt lớn - Vì vậy làm nguội là yêu cầu chủ yếu, bên cạnh đó cũng cần giảm bớt lực cắt bằng cách giảm ma sát. Vì vậy nên chọn nhóm 2. (2) Khi gia công mục đích chính là làm tăng độ bóng bề mặt và đảm bảo tuổi bền dao. Thích hợp gia công tinh nên chọn nhóm 3. (3) Khi cắt ở tốc độ cao bằng dao hợp kim cứng thường không nên tưới dung dịch trơn nguội để tránh gây nứt vỡ hợp kim cứng đồng thời tránh gây bắn dung dịch tung toé ra xung quanh. Cũng cần lưu ý rằng: nhiều trường hợp vẫn phải cần tưới dung dịch trơn nguội, lúc đó cần chú ý tưới liên tục và lượng tưới lớn. Chọn thiết bị gia công cần lưu ý tránh việc thâm nhập của dung dịch vào thiết bị. Để tiện việc lựa chọn sử dụng xin giới thiệu 2 bảng sau: Bảng 8.1. Các dung dịch trơn nguội thường dùng. Nhóm Tên gọi Công dụng Thành phần% 1 Dung dịch nước Làm nguội Nước 98 Cacbonatcanxi 2 Nước 99 Ninatrifotfat 0,8 Nitritnatri 0,2 2 Dung dịch nước và xà phòng Chủ yếu làm nguội có tác dụng bôi trơn Nước 98,2 Xà phòng 0,9 Trinatrifotfat 0,5 Nitritnatri 0,4 10% Emulxi Nước 90 Emulxi 10 3 Sulfattfrezon Chủ yếu bôi trơn có tác dụng làm nguội Dầu cọc sợi số 3 80 Nigron 180 Lưu huỳnh 2 Dầu phức hợp Sulfofrezon 70 Dầu thực vật 30 C8 BPCTDKC CGKL 9 GVC NGUYỄN THẾ TRANH - TRẦN QUỐC VIỆT Bảng 8.2. Kinh nghiệm sử dụng dung dịch trơn - nguội Vật liệu gia công Loại dung dịch Dùng trong các phương pháp gia công tiện phay khoan dao cắt ren Cắt răng chuốt Thép Thép dụng cụ Emulxi Sulfofrezon Dầu thực vật + + + + + + + + + + + + + + + Thép đúc Emulxi Dầu thực vật Sulfofrezon + + + + + + + + + + + + Gang Không dùng Dầu mỏ + + + + + + + + + + Thép đúc Đặc biệt Emulxi + + + + + + Đồng Không dùng Emulxi Không khí + + + + + + + + + + + Nhôm Không dùng Emulxi Dầu mỏ + + + + + + + + + + + + Dura Không dùng Dầu mỏ Emulxi + + + Silimin Emulxi Dầu Dầu mỏ + + + + + + +
File đính kèm:
giao_trinh_co_so_cat_got_kim_loai.pdf