Chế tạo lớp phủ chống ăn mòn và mài mòn trên mặt trong các chi tiết dạng ống trụ tròn bằng công nghệ phun phủ hồ quang điện
Tóm tắt
Trong vài thập kỷ trở lại đây, các lớp phun phủ nhiệt đã được chế tạo thành công và ứng
dụng trong nhiều ngành công nghiệp khác nhau. Nhờ công nghệ phun phủ nhiệt người ta
có thể chế tạo các lớp phủ bảo vệ chống ăn mòn, chống mài mòn, hay các lớp phủ mang
tính trang trí cho các kết cấu và chi tiết khác nhau. Bài báo này tập trung nghiên cứu công
nghệ phun phủ hồ quang điện và ứng dụng trong chế tạo các lớp phủ babit thiếc, thép
không gỉ AISI 316 và hợp kim 37MXC (trên cơ sở Fe-Cr-B-C) trên bề mặt bên trong chi tiết
dạng ống trụ tròn (bạc lót, xy lanh) nhằm mục đích tăng tính chịu mài mòn và chống ăn
mòn khi làm việc trong các môi trường khác nhau.
Bạn đang xem tài liệu "Chế tạo lớp phủ chống ăn mòn và mài mòn trên mặt trong các chi tiết dạng ống trụ tròn bằng công nghệ phun phủ hồ quang điện", để tải tài liệu gốc về máy hãy click vào nút Download ở trên
Tóm tắt nội dung tài liệu: Chế tạo lớp phủ chống ăn mòn và mài mòn trên mặt trong các chi tiết dạng ống trụ tròn bằng công nghệ phun phủ hồ quang điện
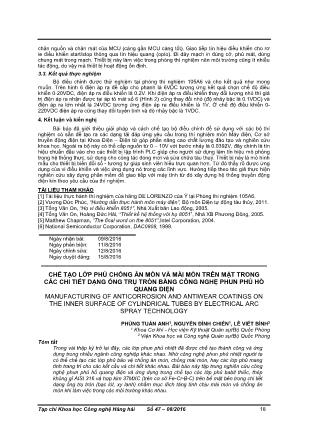
Tạp chí Khoa học Công nghệ Hàng hải Số 47 – 08/2016 18 chân nguồn và chân mát của MCU (càng gần MCU càng tốt). Giao tiếp tín hiệu điều khiển cho rơ le điều khiển start/stop thông qua tín hiệu quang (opto). Đi dây mạch in đúng cỡ, phủ mát, dùng chung mát trong mạch. Thiết bị này làm việc trong phòng thí nghiệm nên môi trường cũng ít nhiễu tác động, do vậy mà thiết bị hoạt động ổn định. 3.3. Kết quả thực nghiệm Bộ điều chỉnh được thử nghiệm tại phòng thí nghiệm 105A6 và cho kết quả như mong muốn. Trên hình 6 điện áp ra để cấp cho phanh là 6VDC tương ứng kết quả chọn chế độ điều khiển 0-20VDC, điện áp ra điều khiển là 0.2V. Khi điện áp ra điều khiển thay đổi lượng nhỏ thì giá trị điện áp ra nhận được tại áp tô mát số 6 (Hình 2) cũng thay đổi nhỏ (độ nhảy bậc là 0.1VDC) và điện áp ra lớn nhất là 24VDC tương ứng điện áp ra điều khiển là 1V. Ở chế độ điều khiển 0- 220VDC điện áp ra cũng thay đổi tuyến tính và độ nhảy bậc là 1VDC. 4. Kết luận và kiến nghị Bài báo đã giới thiệu giải pháp và cách chế tạo bộ điều chỉnh để sử dụng với các bộ thí nghiệm có sẵn để tạo ra các dạng tải đáp ứng yêu cầu trong thí nghiệm môn Máy điện, Cơ sở truyền động điện tại Khoa Điện – Điện tử góp phần nâng cao chất lượng đào tạo và nghiên cứu khoa học. Ngoài ra bộ này có thể cấp nguồn từ 0 – 10V với bước nhảy là 0.0392V, đây chính là tín hiệu chuẩn đầu vào cho các thiết bị lập trình PLC giúp cho người sử dụng làm tín hiệu mô phỏng trong hệ thống thực, sử dụng cho công tác đóng mới và sửa chữa tàu thuỷ. Thiết bị này là mô hình mẫu cho thiết bị biến đổi số - tương tự giúp sinh viên hiểu trực quan hơn. Từ đó thấy rõ được ứng dụng của vi điều khiển và việc ứng dụng nó trong các lĩnh vực. Hướng tiếp theo tác giả thực hiện nghiên cứu xây dựng phần mềm để giao tiếp với máy tính từ đó xây dựng hệ thống truyền động điện kín theo yêu cầu của thí nghiệm. TÀI LIỆU THAM KHẢO [1] Tài liệu thực hành thí nghiệm của hãng DE LORENZO của Ý tại Phòng thí nghiệm 105A6. [2] Vương Đức Phúc, “Hướng dẫn thực hành môn máy điện”, Bộ môn Điện tự động tàu thủy, 2011. [3] Tống Văn On, “Họ vi điều khiển 8051”, Nhà Xuất bản Lao động, 2005. [4] Tống Văn On, Hoàng Đức Hải, “Thiết kế hệ thống với họ 8051”, Nhà XB Phương Đông, 2005. [5] Matthew Chapman, “The final word on the 8051”,Intel Corporation, 2004. [6] National Semiconductor Corporation, DAC0808, 1999. Ngày nhận bài: 09/8/2016 Ngày phản biện: 11/8/2016 Ngày chỉnh sửa: 12/8/2016 Ngày duyệt đăng: 15/8/2016 CHẾ TẠO LỚP PHỦ CHỐNG ĂN MÒN VÀ MÀI MÒN TRÊN MẶT TRONG CÁC CHI TIẾT DẠNG ỐNG TRỤ TRÒN BẰNG CÔNG NGHỆ PHUN PHỦ HỒ QUANG ĐIỆN MANUFACTURING OF ANTICORROSION AND ANTIWEAR COATINGS ON THE INNER SURFACE OF CYLINDRICAL TUBES BY ELECTRICAL ARC SPRAY TECHNOLOGY PHÙNG TUẤN ANH1, NGUYỄN ĐÌNH CHIẾN1, LÊ VIẾT BÌNH2 1 Khoa Cơ khí - Học viện Kỹ thuật Quân sự/Bộ Quốc Phòng 2 Viện Khoa học và Công nghệ Quân sự/Bộ Quốc Phòng Tóm tắt Trong vài thập kỷ trở lại đây, các lớp phun phủ nhiệt đã được chế tạo thành công và ứng dụng trong nhiều ngành công nghiệp khác nhau. Nhờ công nghệ phun phủ nhiệt người ta có thể chế tạo các lớp phủ bảo vệ chống ăn mòn, chống mài mòn, hay các lớp phủ mang tính trang trí cho các kết cấu và chi tiết khác nhau. Bài báo này tập trung nghiên cứu công nghệ phun phủ hồ quang điện và ứng dụng trong chế tạo các lớp phủ babit thiếc, thép không gỉ AISI 316 và hợp kim 37MXC (trên cơ sở Fe-Cr-B-C) trên bề mặt bên trong chi tiết dạng ống trụ tròn (bạc lót, xy lanh) nhằm mục đích tăng tính chịu mài mòn và chống ăn mòn khi làm việc trong các môi trường khác nhau. Tạp chí Khoa học Công nghệ Hàng hải Số 47 – 08/2016 19 Từ khóa: Lớp phun phủ nhiệt, công nghệ phun phủ hồ quang điện, babit thiếc, thép không gỉ AISI 316, hợp kim 37MXC, chi tiết trụ tròn. Abstract Thermal spray coatings have already been successfully used for several decades in the different industries. The anticorrosion and antiwear coatings, decorative coatings for different constructions and machine elements are manufactured by thermal spray technology. In this paper, electrical arc spray technology and its application in manufacturing coatings of tin babbitt, AISI 316 stainless steel, 37MXC alloy (alloy based Fe-Cr-B-C) on the inner surfaces of cylindrical tubes (cylinders, bushes...) in order to improve anticorrosion and antiwear properties of these when working in different environments are studied. Key words: Thermal spray coatings, electrical arc spray technology, stainless steel AISI 316, tin babbitt, 37MXC alloy, cylindrical tube. 1. Đặt vấn đề Công nghệ phun phủ nhiệt nói chung và phun phủ kim loại nói riêng ngày càng trở nên phổ biến trong gia công cơ khí, đặc biệt là trong chế tạo phục hồi nhằm tăng các đặc tính bề mặt của chi tiết [1,2]. So với các phương pháp bảo vệ kim loại khác như sơn, mạ điện, nhúng, thấm..., phun phủ để tạo ra lớp bề mặt bảo vệ kim loại chống lại sự ăn mòn, mài mòn được ứng dụng đem lại hiệu quả kinh tế cao hơn. Nguyên liệu dùng trong phu phủ rất đa dạng, có thể ở dạng dây, que hoặc bột. Có rất nhiều phương pháp phun phủ khác nhau, mỗi phương pháp sử dụng một số loại vật liệu xác định và có những ưu nhược điểm nhất định. Công nghệ phun phủ có thể áp dụng cho cả lớp phủ trên bề mặt ngoài lẫn bề mặt bên trong các chi tiết. Công nghệ tạo lớp phủ trên bề mặt bên trong các chi tiết đã được ứng dụng khá phổ biến trên thế giới, tuy nhiên ở Việt Nam công nghệ này chưa được quan tâm nhiều do hạn chế về thiết bị. Bài báo này đi sâu nghiên cứu phương pháp phun phủ hồ quang điện, ứng dụng vào chế tạo, phục hồi bề mặt bên trong các chi tiết dạng trụ tròn (bạc lót, xy lanh) chịu mài mòn và ăn mòn trong điều kiện sản xuất ở Việt Nam. 2. Công nghệ phun phủ hồ quang điện 2.1. Nguyên lý phun phủ Hình 1. Sơ đồ nguyên lý cấu tạo của súng phun (đầu phun) hồ quang điện hai điện cực: 1- Dây hàn; 2 - Dòng khí nén; 3 - Con lăn cấp dây hàn; 4 - Lớp phủ; 5 - Kim loại nền Hình 2. Sơ đồ nguyên lý chế tạo lớp phủ trên bề mặt trong của chi tiết Nguyên lý chung của công nghệ phun phủ hồ quang điện được chỉ ra trên hình 1. Hai dây 1 tương ứng với hai điện cực được đặt trong bộ phận dẫn dây và dịch chuyển nhờ cặp con lăn 3. Các dây kim loại được nối với hai điện cực khác nhau bằng bộ phận tiếp điện nằm trong bộ phận dẫn dây, khi tiếp xúc nhau sẽ tạo ra vùng hồ quang có nhiệt độ cao làm nóng chảy đầu dây kim loại. Vận tốc cấp dây phải phù hợp với quá trình phun. Trong khi đó, kim loại nóng chảy được thổi bằng dòng khí nén 2 bố trí ở giữa hai điện cực. Dòng phun hồ quang 4 với vận tốc lớn được phủ Tạp chí Khoa học Công nghệ Hàng hải Số 47 – 08/2016 20 lên bề mặt chi tiết 5 đã được làm sạch và tạo nhám. Để tạo được lớp phủ dày và đồng đều người ta phải phun nhiều lớp mỏng chồng lên nhau. Đối với công nghệ phun phủ tạo lớp phủ trên bề mặt trong các chi tiết, nguyên lý làm việc cơ bản là phôi chi tiết quay tròn, súng phun tịnh tiến theo một tốc độ nhất định để đảm bảo thì được lớp phủ đồng đều. Sơ đồ nguyên lý của quá trình phun được chỉ ra trên hình 2. 2.2. Các tham số công nghệ chế tạo lớp phủ trên bề mặt bên trong các chi tiết Chất lượng lớp phun phủ trên bề mặt bên trong các chi tiết phụ thuộc rất nhiều vào chế độ công nghệ phun phủ. Các yếu tố liên quan tới chế độ phun phủ bao gồm góc phun, khoảng cách phun, áp lực khí nén, điện áp hồ quang, cường độ dòng điện, tốc độ chuyển động tương đối giữa súng phun và bề mặt chi tiết, tốc độ dịch chuyển ngang của súng phun. Góc phun được biểu thị bởi dòng các hạt kim loại nóng chảy sẽ va đập lên bề mặt chi tiết cần phun. Góc phun tốt ưu là 90o. Góc phun nhỏ nhất có thể chấp nhận được là 45o. Tuy nhiên, góc phun nên chọn trong khoảng từ 65 đến 90o vì góc phun càng nhỏ hơn 90o càng làm tăng độ rỗ xốp của lớp phủ [4]. Khoảng cách phun là yếu tố có ảnh hưởng rất lớn tới chất lượng lớp phủ như độ cứng, độ bám dính, độ chịu mài mòn. Nếu khoảng cách phun quá gần, độ cứng thấp vì lúc này lớp phủ bị quá nóng. Khi khoảng cách quá xa, các hạt phun không điền đầy khít với nhau, độ xốp tăng lên, do đó độ cứng sẽ giảm. Các thực nghiệm đều chứng tỏ khoảng cách phun tốt nhất nằm trong khoảng (75÷150) mm [1]. Áp lực khí nén cần đủ để thổi các giọt kim loại lỏng thành chùm hạt nhỏ và tạo biến dạng mạnh của các hạt khi va đập. Áp lực khí nén ảnh hưởng tới độ chịu mài mòn của lớp phủ và nó liên quan tới hệ số mất mát kim loại phủ. Việc tăng áp lực khí nén dẫn đến tăng tốc độ phun, tăng lượng tiêu hao khí nén. Áp lực khí nén thường chọn trong khoảng (0,35÷0,55) MPa [1,2]. Điện áp hồ quang cần thiết để tạo ra sự ổn định hồ quang, tạo điều kiện cho quá trình phun phủ được liên tục. Nếu điện áp hồ quang thấp thì hồ quang không ổn định và bị ngắt quãng, nếu điện áp hồ quang quá cao, mức độ oxy hoá các hạt sẽ tăng, do đó sẽ làm giảm chất lượng lớp phủ và tăng lượng kim loại bị mất mát. Thông thường, điện áp hồ quang nằm trong khoảng (20÷35) V. Cường độ dòng điện phụ thuộc vào công suất phun (tốc độ cấp dây), loại vật liệu, đường kính dây phun và được hiệu chỉnh tự động tương ứng với điện áp trong quá trình phun. Tốc độ chuyển động tương đối giữa súng phun và bề mặt chi tiết cần phun (còn gọi là tốc độ lướt trên bề mặt chi tiết của súng phun) là có giới hạn để tạo phủ đồng đều, liên tục. Tốc độ lướt thường lựa chọn trong khoảng (0,23÷0,76) m/s [2]. Nói chung, tốc độ lướt lý tưởng khoảng 0,5 m/s. Tốc độ lướt lý tưởng là tốc độ tạo lớp phủ có chiều dày xấp xỉ 25,4 µm/lần cho kim loại và vật liệu thô, và 12,7 µm/lần đối với vật liệu gốm và vật liệu mịn. Tốc độ này sẽ được tính toán và chuyển đổi thành tốc độ quay của chi tiết. Tốc độ dịch chuyển ngang qua bề mặt chi tiết của súng phun được tính toán sao cho lớp phun sau đè lên lớp phun trước từ 30 đến 50%. Một chu kỳ dịch chuyển của súng phun sẽ hình thành một lớp phun trên bề mặt chi tiết và nhiều lớp phun sẽ đạt chiều dày mong muốn. Với các chi tiết dạng trụ tròn, tốc độ dịch chuyển ngang của súng phun được tính toán sao cho quãng đường súng phun dịch chuyển sau một vòng quay của chi tiết đạt khoảng từ (3÷5) mm [2,4]. 3. Chế tạo và đánh giá lớp phủ trên bề mặt bên trong chi tiết dạng trụ tròn Các nghiên cứu thực nghiệm chế tạo lớp phủ yêu cầu được tiến hành trên hệ thống thiết bị phun phủ hồ quang điện TAFA Praxair 8830 MHU (Mỹ). Các thiết bị chính của hệ thống bao gồm tủ điện điều khiển, súng phun và các thiết bị phụ trợ đi kèm (máy nén khí, bình chứa khí nén, máy sấy khí, thiết bị phun cát làm sạch chi tiết và hệ thống đồ gá đỡ chi tiết và lắp đặt súng phun). Đối tượng nghiên cứu thực nghiệm là các chi tiết dạng trụ tròn cần tạo lớp phủ có tác dụng chống ăn mòn và mài mòn trên các bề mặt bên trong. Phương pháp nghiên cứu bao gồm xác định độ cứng, độ xốp, hệ số ma sát, tốc độ ăn mòn của lớp phủ. 3.1. Chế tạo lớp phủ babit thiếc (90Sn-7Sb-3Cu) chống ma sát Khi nghiên cứu chế tạo lớp phủ babit thiếc có thành phần 90Sn-7Sb-3Cu trên mặt trong trụ tròn thép C45 có đường kính trong 130 mm nhận thấy, chất lượng lớp phủ tốt nhất đạt được ứng với điện áp hồ quang 21 V, áp lực khí nén 0,45 MPa (65 psi), khoảng cách phun 100 mm, tốc độ Tạp chí Khoa học Công nghệ Hàng hải Số 47 – 08/2016 21 quay chi tiết (45÷50) vòng/phút, tốc độ dịch chuyển súng phun (180÷210) mm/phút. Khi đó, lớp phủ có độ xốp 11,43%, độ cứng lớp phủ đạt khoảng 30 HV, độ bám dính của lớp phủ với nền đạt khoảng 17,4 MPa. Tổ chức tế vi của lớp phủ babit thiếc được cho trên hình 3 gồm hai pha liên kim loại màu trắng SnSb và Cu6Sn5 phân bố trên nền dung dịch rắn giàu Sn. Các chấm đen chính là lỗ xốp đặc trưng cho lớp phủ. Giản đồ nhiễu xạ Rơnghen trên hình 4 chỉ ra rằng, lớp phủ có 3 pha: Pha nền giàu Sn có cường độ các vạch nhiễu xạ mạnh nhất, các pha cứng phân bố trên pha nền là Cu6Sn5 và SnSb có cường độ vạch nhiễu xạ yếu hơn. Một trong những chỉ tiêu quan trọng đánh giá lớp phủ babit là khả năng chống ma sát. Thử nghiệm mài mòn được thực hiện trong điều kiện không bôi trơn tại nhiệt độ phòng theo tiêu chuẩn ASTM G133. Kết quả xác định hệ số ma sát khô của lớp phủ được cho trên hình 5. Hệ số ma sát trung bình đạt khoảng 0,1996, tương đối phù hợp với các công trình đã công bố [5]. Quy trình công nghệ chế tạo lớp phủ babit thiếc trên nền thép có thể ứng dụng để chế tạo lớp phủ trên bề mặt bên trong các xy lanh, bạc lót có khả năng chống mài mòn và phục hồi các chi tiết bị mài mòn sau một thời gian làm việc nhất định. Hình 4. Giản đồ nhiễu xạ Rơnghen của lớp phủ babit thiếc Hình 5. Đồ thị biểu diễn hệ số ma sát của lớp phủ babit thiếc 3.2. Chế tạo lớp phủ 37MXC (hợp kim Fe-Cr-B-C) chống mài mòn Lớp phủ 37MXC (hợp kim Fe-Cr-B-C) được tạo ra từ dây lõi bột, về mặt cơ bản có thể coi là lớp phủ ceramic. Trong thành phần của dây 37MXC có rất nhiều nguyên tố, trong đó cacbon (C) chiếm khối lượng đến 5%, crôm (Cr) 26%, sắt (Fe) 67%, bo (B) 1% và một số nguyên tố khác với hàm lượng nhỏ. Lớp phủ 37MXC cho độ cứng cao và chịu mài mòn tốt. Khi tạo lớp phủ trên bề mặt bên trong chi tiết trụ tròn bằng thép 40Cr có đường kính trong 130 mm, lớp phủ đạt chất lượng cao nhất tương ứng với điện áp hồ quang (32÷34)V, áp lực khí nén 0,48 MPa (70 psi), khoảng cách phun (120÷125) mm, tốc độ quay chi tiết (45÷50) vòng/phút, tốc độ dịch chuyển súng phun (180÷210) mm/phút. Độ cứng của lớp phủ đạt trên 40HRC, trong khi độ xốp nhỏ nhất là 17,76%. Tổ chức tế vi của lớp phủ 37MXC trên nền thép 40Cr được cho trên hình 6. Lớp phủ có tổ chức gồm những dải kim loại cỡ 100 µm, các lỗ xốp có màu đen hình dạng kéo dài trên nền sáng là dung dịch rắn Fe(Cr). Ngoài ra trên dung dịch rắn Fe(Cr) có sự phân bố không đều của các hạt có thể là hạt cacbit crôm hoặc cacbit sắt làm cho lớp phủ có tính chống mài mòn cao và độ cứng cao. Khả năng chống mài mòn của lớp phủ phụ thuộc vào trạng thái ma sát khô hay ma sát ướt. Trong điều kiện ma sát khô (không có chất bôi trơn) lớp phủ 37MXC có tính chống mài mòn lớn hơn nền Hình 3. Tổ chức tế vi babit thiếc 90Sn-7Sb-3Cu Tạp chí Khoa học Công nghệ Hàng hải Số 47 – 08/2016 22 thép 40Cr khoảng 3 lần. Trong điều kiện ma sát ướt (có chất bôi trơn) thì lớp phủ có k hả năng chống mài mòn tốt hơn rất nhiều do các lỗ xốp có trong lớp phủ ngậm dầu tốt và tạo ra những túi đựng dầu nhỏ dự trữ đảm bảo khả năng bôi trơn tốt hơn. Trên cơ sở đánh giá các đặc tính của lớp phủ 37MXC, có thể ứng dụng lớp phủ này vào chế tạo lớp phủ chống mài mòn cho bề mặt trong các chi tiết dạng trụ tròn, dạng ống trụ tròn có kích thước khác nhau, đặc biệt là với các chi tiết tương đối lớn mà quá trình chế tạo trong nước hiện không đáp ứng được. Để đảm bảo chất lượng lớp phủ, trước khi phun tạo lớp phủ 37MXC cần phun tạo lớp liên kết (lớp bonding) mỏng bằng dây Ni- 5Al làm nhiệm vụ tăng độ bám dính và liên kết giữa lớp phủ với nền. 3.3. Chế tạo lớp phủ thép không gỉ AISI316 chống ăn mòn Thép không gỉ AISI 316 có tính chống ăn mòn tốt. Tuy nhiên trong các điều kiện làm việc khắc nghiệt, chi tiết vẫn bị ăn mòn. Trên cơ sở nghiên cứu thực nghiệm đã xây dựng quy trình chế tạo lớp phủ dây AISI 316 trên mặt trong chi tiết trụ tròn bằng thép không gỉ AISI 316 có đường kính trong 140 mm với điện áp hồ quang (29÷32) V, áp lực khí phun (0,45÷0,48) MPa, khoảng cách phun (120÷130) mm, tốc độ quay của chi tiết 50 vòng/phút, tốc độ dịch chuyển súng phun 180 mm/phút. Độ cứng lớp phủ đạt khoảng (37÷38) HRC, mật độ lỗ xốp nhỏ nhất khoảng 9,7%. Độ bám dính của lớp phủ với nền đạt trên (28,7÷29,4) Mpa. Tốc độ ăn mòn của lớp phủ trong môi trường dung dịch NaCl 3,5% khoảng (0,012÷0,015) mm/năm, tương đối phù hợp với thực tế [6]. Tổ chức tế vi của lớp phủ AISI 316 được cho trên hình 7. Tổ chức lớp phủ khá đồng đều, lỗ xốp và tạp chất ít, phân tán. Ngoài lớp phủ trên nền thép AISI 316 có thể tiến hành phủ lớp vật liệu AISI 316 trên nền thép bất kỳ nhằm tận dụng vật liệu, giảm thiểu giá thành sản phẩm mà vẫn đảm bảo các tính chất chống ăn mòn theo yêu cầu. Việc ứng dụng lớp phủ này có thể được áp dụng trên các chi tiết xilanh, bạc lót của các máy bơm làm việc trong các môi trường axit, nước biển, NH3 Hình 7. Tổ chức tế vi lớp phủ AISI 316 4. Kết luận Trên cơ sở nghiên cứu lý thuyết và thực nghiệm, việc chế tạo thành công lớp phủ lên bề mặt bên trong các chi tiết dạng trụ tròn bằng công nghệ phun phủ hồ quang điện cho phép ứng dụng rộng rãi công nghệ này vào sản xuất thực tiễn ở Việt Nam. Tuy nhiên, do điều kiện công nghệ (súng phun có đường kính 40 mm) nên các chi tiết cần tạo lớp phủ bên trong phải có đường kính trong không nhỏ hơn 100 mm, chiều dài chi tiết cần phun có thể lên tới 500 mm. Khi thay đổi đường kính trong của chi tiết cần phun, các tham số tốc độ quay của chi tiết và tốc độ dịch chuyển súng phun cần hiệu chỉnh tương ứng. Trước đây, việc chế tạo lớp phủ theo yêu cầu đối với các chi tiết trụ tròn có bề mặt làm việc bên trong chưa có công nghệ nào trong nước thực hiện được. Hiện nay với hệ thống thiết bị phun phủ hồ quang điện TAFA Praxair 8830 MHU sẵn có tại học viện Kỹ thuật Quân sự, việc chế tạo các lớp phủ chức năng bất kỳ trên bề mặt trong các chi tiết dạng trụ tròn hoàn toàn có khả năng thực hiện được, đáp ứng nhu cầu thực tế trong sản xuất cơ khí, giúp tăng năng suất lao động và góp phần giảm giá thành sản phẩm, đặc biệt khi chế tạo và phục hồi các chi tiết chịu ăn mòn, chống mài mòn và ma sát làm việc trong các môi trường khắc nghiệt. TÀI LIỆU THAM KHẢO Hình 6. Tổ chức tế vi lớp phủ 37MXC
File đính kèm:
che_tao_lop_phu_chong_an_mon_va_mai_mon_tren_mat_trong_cac_c.pdf