Bài giảng Thực tập cắt gọt kim loại nâng cao (Phay)
BÀI 1 - PHAY RÃNH CHỮ T
1.1. Khái niệm và công dụng
1.1.1. Khái niệm:
- Là rãnh có hình dạng chữ T, tuỳ theo công dụng và điều kiện làm việc mà rãnh chữ T ngược hay xuôi.
1.1.2. Công dụng
- Được dùng nhiều trong nghành chế tạo máy, đặc biệt là trên các bàn máy công cụ để luồn bulông khi lắp ghép hoặc khi kẹp chặt.
Ví dụ: Rãnh thẳng trên các bàn máy phay, máy bào, máy khoan, rãnh vòng trên đầu máy bào, mâm quay, đầu máy phay đứng, êtô để xoay.
Bạn đang xem 20 trang mẫu của tài liệu "Bài giảng Thực tập cắt gọt kim loại nâng cao (Phay)", để tải tài liệu gốc về máy hãy click vào nút Download ở trên
Tóm tắt nội dung tài liệu: Bài giảng Thực tập cắt gọt kim loại nâng cao (Phay)
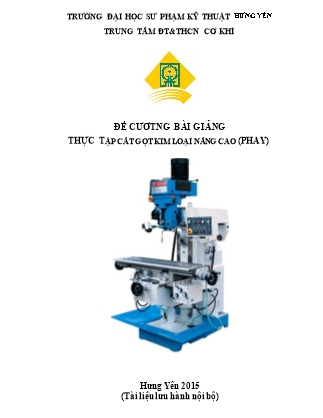
TRƯỜNG ĐẠI HỌC SƯ PHẠM KỸ THUẬT hưng yên TRUNG TÂM ĐT&THCN CƠ KHÍ ĐỀ CƯƠTNG BÀI GIẢNG THỰC Tập cắt gọt kim loại nâng cao (PHAY) Hưng Yên 2015 (Tài liệu lưu hành nội bộ) MỤC LỤC BÀI 1 - PHAY RÃNH CHỮ T Khái niệm và công dụng Khái niệm: Là rãnh có hình dạng chữ T, tuỳ theo công dụng và điều kiện làm việc mà rãnh chữ T ngược hay xuôi. Công dụng Được dùng nhiều trong nghành chế tạo máy, đặc biệt là trên các bàn máy công cụ để luồn bulông khi lắp ghép hoặc khi kẹp chặt. Ví dụ: Rãnh thẳng trên các bàn máy phay, máy bào, máy khoan, rãnh vòng trên đầu máy bào, mâm quay, đầu máy phay đứng, êtô để xoay... Phương pháp phay Phay rãnh vuông Ta có thể sử dụng dao phay trụ đứng (dao ngón) hoặc dao phay đĩa ba mặt cắt để gia công rãnh vuông. Trong khi phay tuỳ theo hướng ăn dao mà ta hãm các chuyển động không cần thiết. Nếu không sẽ xảy ra hiện tượng rung động, giảm chất lượng bề mặt của rãnh gây mẻ hoặc gẫy dao. Quá trình phay được tiến hành bình thường như khi phay rãnh vuông. Phay rãnh chữ T Phay rãnh ngang bằng dao phay đặc biệt (thường gọi là dao phay rãnh chữ T) có kích thước phù hợp. Sau khi phay rãnh vuông xong ta không dịch chuyển bàn máy theo phương ngang mà phải lắp dao vào trục chính của máy và tiến hành điều chỉnh máy để phay rãnh chữ T. Lúc này tâm của rãnh vuông phải trùng với tâm của dao phay. - Chiều cao của rãnh được thực hiện bằng cách: Dịch chuyển bàn máy để cho mặt trên của chi tiết chạm nhẹ vào mặt đầu của dao sau đó dịch cho phôi ra khỏi dao và nâng bàn máy lên một khoảng H bằng chiều cao của rãnh. Khi chiều rộng của rãnh bằng chiều rộng của dao thì phay bình thường. Còn nếu chiều rộng của rãnh chữ T lớn hơn chiều rộng của dao thì ta phải dịch chuyển dao sang hai bên để cắt hết chiều rộng của rãnh. Chú ý: Loại này rất yếu, dễ gẫy cổ dao do đó phải lấy lượng chạy dao nhỏ và phay thật thận trọng, tốc độ cắt lắy nhỏ. Phay vát mép - Đổ phay vát mép c X 45° ta có thể dùng dao phay có góc hoặc dao phay trụ xoay đầu máy đi một góc a. Bài tập ứng dụng Đọc bản vẽ Trình tự gia công * Công việc chuẩn bị: Chọn dao và gá lắp dao: dùng dao trụ 014, dao phay chữ T 022 X 10 Rà gá phôi: phôi được gá trên êtô máy, rà phẳng Điều chỉnh máy để gia công. TT Tên bước Hình vẽ Chế độ cắt n t s (v/p) (mm) (mm/p) Bước 1 Phay rãnh vuông đạt kích thước 14 X 16 840 0.08 Bước 2 Phay rãnh chữ T Sử dụng dao 022 X 10 ,14+0,0^ 22+0.1 470 0.04 Bước 3 Phay vát mép 2x45° 0.06 Sử dụng dao phay trụ xoay nghiêng đầu máy một góc 45° 1.3.3. Các dạng sai hỏng - Nguyên nhân - Biện pháp khắc phục TT Các dạng sai hỏng Nguyên nhân Biện pháp khắc phục 1 - Sai số về kích thước của rãnh - Thao tác đo không chính xác, sai số dụng cụ - Đo kiểm chính xác, kiểm tra lại dụng cụ đo trước khi đo 2 - Sai số về vị trí tương quan, đường tâm của rãnh không đối xứng - Do lấy dấu không đúng, điều chỉnh máy sai - Lấy dấu chính xác, kiểm tra lại trước khi phay tinh 3 - Độ nhẵn bề mặt không đạt: - Chế độ cắt không hợp lý, không tưới dung dịch trơn nguội, dao bị cùn - Lấy chế độ cắt hợp lý, kiểm tra lại dao, tưới dung dịch trơn nguội BÀI 2 - PHAY RÃNH ĐUÔI ÉN Khái niệm chung về rãnh đuôi én Là rãnh hợp bởi 2 mặt phẳng nhỏ hơn 90° thường là các góc: 45°, 50°, 55°, 60°, 65°... Rãnh đuôi én được dùng nhiều trong quá trình tháo lắp nhanh các cơ cấu với các thiết bị đòi hỏi độ chính xác cao như các rãnh trượt, sống trượt mang cá, rãnh để lắp khuôn dập vào đe đầu máy... Ví dụ: Mộng đuôi én của xà ngang (thân ngang) với thân của máy phay nằm, đầu trượt lắp với thân máy bào, băng trượt của các bàn máy... Các thông số cơ bản Trong đó: H: Là chiều sâu của rãnh L: Là chiều rộng của rãnh a: Góc của rãnh 2.3 Phinmg pháp phay rãnh đuôi én Phay rãnh vuông Có thể sử dụng dao phay đĩa hoặc dao phay trụ đứng sao cho rãnh vuông có chiều rộng phải nhỏ hơn chiều rộng của miệng rãnh đuôi én và chiều sâu của rãnh vuông phải nhỏ hơn chiều sâu của rãnh đuôi én khoảng 0,1 -ỉ- 0,2 mm. Chế độ cắt, phương pháp phay, cách điều chỉnh máy tương tự như khi phay rãnh vuông. 2.3.2. Phay rãnh đuôi én Chọn dao: Ta sử dụng dao phay góc đơn có góc độ (a) tương ứng với góc độ yêu cầu của chi tiết gia công và chọn đường kính của dao (D) phù hợp với chiều rộng của rãnh Chế độ cắt: Do điều kiện làm việc của dao khó khăn (dao định hình), dao dễ bị gãy nên chọn vc = 2/3 vc khi phay rãnh vuông. Khi phay phải luôn phay nghịch với lượng dư nhỏ và lượng chạy dao nhỏ s = 0.04 - 0.06 Kiểm tra rãnh đuôi én Việc kiểm tra độ chính xác của rãnh đuôi én được thực hiện bởi các dưỡng chuyên dùng. Các dưỡng này cho phép kiểm tra góc nghiêng của cạnh bên, vị trí đối xứng của chúng và chiều cao của rãnh. Ngoài ra ta có thể kiểm tra bằng phương pháp đo: Nhưng ở đây không đo trực tiếp được mà phải đo gián tiếp thông qua con lăn. Theo hình vẽ ta có: a/2 b = r. cotg- L = Y + 2b + 2r _ a „ = Y + Dcotg^ + D ( a = Y + D cotg^ + 1 Dodó: Y = L-D (cotg^ + 1) Trong đó: D: Là đường kính của con lăn (mm) a: Là góc của rãnh đuôi én (độ) L: Chiều rộng của đáy rãnh cần kiểm tra Y: Là kích thước đo được bằng thước cặp Ví dụ: Cần có kích thước L = 34mm Góc của đuôi én là 60° Sử dụng con lăn có đường kính: Ộ5 Tính Ta có: o. / 60 , Y = 34 - 5 cot g'+l k 2 7 = 34-5(1,732 + 1) = 20,34 Bài tập ứng dụng Đọc bản vẽ (Rz40) 2.4.3. Các dạng sai hỏng - Nguyên nhân - Biện pháp khắc phục TT Các dạng hỏng Nguyên nhân Biện pháp khắc phục 1 Sai số về góc độ - Do chọn dao sai, không đúng góc độ - Kiểm tra góc độ của dao trước khi gia công 2 Sai số về kích thước Do tính toán khoảng Y sai Chọn con lăn không đúng, không đều Thao tác đo kiểm sai Tính toán lại khoảng Y Kiểm tra đường kính con lăn Thao tác đo kiểm chính xác 3 Sai số về vị trí tương quan - Do không điều chỉnh cho đường tâm của rãnh trùng với đường tâm chi tiết - Kiểm tra trước khi phay tinh 4 Độ nhẵn bề mặt không đạt - Do chế độ cắt không hợp lý, dao cùn, không tưới dung dịch trơn nguội - Điều chỉnh lại chế độ cắt, kiểm tra lại dao BÀI 3 - PHAY CHỐT ĐUÔI ÉN Các thông số cơ bản của chốt đuôi én Trong đó: L: Là bề rộng của chốt. a: Là góc nghiêng của chốt h: Là chiều cao Phinmg pháp phay Phay bậc thẳng góc Dùng dao phay trụ hoặc dao phay đĩa 3 mặt cắt để phay bậc thẳng góc sao cho kích thước còn lại của bậc phải lớn hơn kích thước lớn nhất của chốt và chiều cao của bậc phải nhỏ hơn chiều cao của chốt. Chế độ cắt, phương pháp phay tương tự như khi gia công mặt bậc. Phay mặt nghiêng Sử dụng dao phay góc đơn có góc độ tương ứng phù hợp với góc độ yêu cầu của chi tiết gia công. Phương pháp phay tương tự khi phay rãnh đuôi én. Kiểm tra chốt - Cũng như khi kiểm tra rãnh đuôi én khi kiểm tra chốt ta phải kiểm tra thông qua hai con lăn. Ta CÓ: , x a b = r. cot ag — Y = B + 2b + 2r 25-0.1 6- 0.06 60° 3.3. Bài tập ứng dụng 3.3.1. Đọc bản vẽ = B + D cotg^ 3.3.2. Trình tự gia công STT Tên bước Hình vẽ Bước 1 Phay bậc thẳng góc Chế độ căt n (v/p) t ( mm) s (mm/p) 840 0.6-ỉ- 0.8 0.06 Bước 2 Phay chốt đuôi én 470 0.4 0.04 Bước 3 Kiểm tra kích thước rãnh đuôi én Với r = 3mm 3.3.3. Các dạng sai hỏng - Nguyên nhân - Biện pháp khắc phục STT Các dạng hỏng Nguyên nhân Biện pháp khắc phục 1 Sai số về góc độ - Do chọn dao sai, không đúng góc Chọn lại dao Kiểm tra góc độ của dao trước khi phay 2 Sai số về kích thước Do tính toán khoảng Y sai, Chọn con lăn không đúng, không đều Thao tác đo kiểm sai Tính toán cẩn thận Kiểm tra đường kính con lăn Đo kiểm chính xác 3 Sai số về vị trí tương quan - Do không điều chỉnh cho tâm rãnh trùng với đường tâm chi tiết - Kiểm tra trước khi phay tinh 4 - Độ nhẵn bề mặt không đạt - Do chế độ cắt không hợp lý, dao cùn - Điều chỉnh lại chế độ cắt, kiểm tra lạo dao BÀI 4 - SỬ DỤNG ĐẦU CHIA ĐỘ VẠN NẤNG Công dụng và phân loại đầu chia độ Công dụng: Đầu chia độ là một loại đồ gá vạn năng kèm theo máy phay dùng để gá phôi quay được ở nhiều vị trí đồng tâm cách nhau một góc độ hoặc một cung tròn nhất định. Nó mở rộng khả năng công nghệ của máy phay. Phay các rãnh (thẳng hoặc xoắn) trên mặt ngoài của chi tiết dạng trục như: răng dao doa, răng dao phay, rãnh ta rô, rãnh then hoa... Phay các cạnh của chi tiết dạng đa diện: đai ốc, bulông, chuôi ta rô... Phay các rãnh trên mặt đầu của chi tiết dạng trụ: dao phay mặt đầu, răng đĩa ly hợp... Khoan các lỗ trên mặt đĩa: khoan lỗ trên đĩa chia độ, khoan lỗ trên vành bích... Phay các rãnh trên mặt côn: bánh răng côn... Khắc vạch trên vành du xích hoặc khắc vạch trên thước thẳng... Phân loại Có ba loại: Loại có đĩa chia độ: + Chia độ trực tiếp. + Chia độ đơn giản + Đầu chia nửa vạn năng + Đầu chia vạn năng Loại không có đĩa chia độ với cơ cấu bánh răng hành tinh hoặc bộ bánh răng thay đổi. Đầu chia độ quang học: Dùng để phân độ chính xác cho các nguyên công kiểm tra. Ngoài ra còn có các loại: Đầu phân độ nhiều trục dùng để gia công đồng thời hai hoặc nhiều chi tiết. Cấu tạo của đầu chia độ vạn năng Thân (10) gắn trên đế ngang (20) nối liền với hai cánh hình cung (9). Neu nới lỏng các đai ốc, ta có thể quay hộp đi một góc theo thang chia độ và du xích (12). Ở đế có hai rãnh hở ( song song với trục chính) dùng để kẹp chặt đầu chia độ với bàn máy. - Trong thân lăp trục chính có lỗ thông suôt. Hai đầu mút trục chính được gia công thành côn moóc. Ở đầu trước của ổ trục chính có lắp mũi tâm (21), còn ở đầu sau lắp trục gá để chia độ vi sai. Ở đầu trước của trục chính có ren và vành định tâm (7) để kẹp mâm cặp 3 chấu tự định tâm hoặc mâm cặp tốc. Ở vai trục chính người ta gắn vành chia độ (8) có 24 lỗ. Ở phần giữa của trục chính có bánh vít (ở mặt đầu của bánh vít có một rãnh để cắm chốt kẹp (11)). Bánh vít nhận chuyển động quay từ trục vít. Trục vít nằm trong ống lệch tâm và khi quay (bằng tay quay) ống lệch tâm thì trục vít có thể ăn khớp hoặc không ăn khớp với bánh vít. Đĩa chia độ được lắp trên một trục đã lắp sẵn vào ổ bi trượt (ổ bi trượt nằm trong nắp đậy 19). Đĩa chia độ có nhiều hàng lỗ với các số lỗ khác nhau. Nắp đậy được bắt chặt vào thân (10) và được kẹp cố định vào đế. Hình quạt (18) gồm thước (14) và vít kẹp (13) (nhờ vít kẹp (13) có thể định vị các thước theo những góc cần thiết) luôn được ép chặt vào đĩa chia nhờ một lò xo. Vòng đệm lò xo giữ cho hình quạt tránh hiện tượng tự quay. Trục truyền động cơ khí (16) (từ máy phay) lắp trong ổ bi trượt và đặt trong bạc (15). Ở cuối trục này có bánh răng côn luôn luôn ăn khớp với bánh răng côn trên trục của đĩa chia độ. Dùng chốt (17) để định vị đĩa chia độ ở các vị trí cần thiết. Mũi tâm của ụ sau có thể dịch chuyển theo hai phương ngang và đứng. Thân (2) nằm trên đế (24) và được gắn với thanh răng bằng chốt. Bằng cách quay đều của trục răng ta có thể di chuyển thân lên phía trên và quay xung quanh tâm của chốt. Khi quay vô lăng (1) (được kẹp trên trục vít), nòng (3) dịch chuyển cùng với mũi tâm vát (4). Ở mặt dưới đế có hai thanh dẫn hướng được điều chỉnh theo trục của nòng để đảm bảo độ đồng tâm của đầu chia độ và ụ sau. Phương pháp chia độ Phương pháp chia độ trực tiếp Khi số phần chia ít và không đòi hỏi chính xác cao, ta áp dụng phương pháp chia độ trực tiếp. Nguyên tắc chia độ trực tiếp là từ đĩa chia ( với chức năng là mẫu chia) đến phôi có quan hệ truyền động trực tiếp : Đĩa chia quay bao nhiêu thì phôi quay bấy nhiêu. Như vậy độ chính xác của việc chia độ phụ thuộc vào độ chính xác có hạn của bản thân đĩa chia. Tuy nhiên, cách chia độ này có ưu điểm là đầu chia có cấu tạo đơn giản nên rẻ tiền và thao tác dễ dàng, thường được dùng trong khi chia 2,3,... đến 12 phần đều nhau. Cũng có thể mở rộng phạm vi sử dụng bằng cách dùng đĩa chia có 24, 30 lỗ. Nếu đĩa chia có 12 lỗ, ta chia được: 2, 3,4, 6,12 phần đều nhau. Với đĩa chia 24 lỗ, ta chia thêm được 8 và 24 phần đều nhau. Nguyên tắc chia độ trực tiếp thường được áp dụng với các đồ gá chuyên dùng, ví dụ: gá khoan các lỗ trên mặt đầu pittông máy nổ,... Phương pháp chia độ đơn giản. - Dựa trên nguyên tắc là giữa chuyển động của tay quay chia độ với phôi có giảm tốc nhằm thu nhỏ sai số biểu hiện, tức là kết quả chia độ trên phôi khi chịu sai số nhiều như bản thân đĩa chia. Mặt khác, với phương pháp này ta cũng chia được nhiều phần hơn. * Sơ đồ nguyên lý của đầu chia c độ vạn năng - d~ - Khi phân độ đơn giản thì trục vít (8) phải ăn khớp với bánh vít (10). Muốn trục chính (9) quay, người ta quay tay quay (2) cùng với chốt định vị (3) so với đĩa chia độ cố định (1). Chuyển động quay của tay quay được truyền tới trục chính qua cặp bánh răng hình trụ (7) với tỉ số truyền i = 1 và cặp trục vít - bánh vít với tỉ số truyền i = 1/40. Qua cấu tạo của đầu chia, ta thấy tỷ số giảm tốc của đầu chia là N (N thường là 40, hoặc có khi là 60, 30 và 120) Muốn phân độ vòng tròn ra hai hay nhiều phần đều nhau ta làm như sau: Trục chính quay 1 vòng thì tay quay quay N vòng. Mỗi lần phân độ cần l/z vòng thì tay quay quay n vòng Do đó ta có công thức tổng quát là: N =>n = — z Trong đó: n: số vòng tay quay (nt q) z: Số phần cần chia N: Đặc tính của đầu chia độ (N = 40) N, z đều là số nguyên, nghĩa là nếu ta tính trên đĩa hàng lỗ nào trên vòng tròn đồng tâm có số lỗ bằng số z thì mỗi lần phân độ ta chỉ việc quay tay quay đi một cung chứa số lỗ bằng số N trên vòng tròn z lỗ. Ví dụ 1: Khi ta cần phay bánh răng có z = 60. Thì khi phay xong một răng ta cần quay tay quay đi N 40 tq z 60 (Nghĩa là quay đi 40 lô trên hàng lô 60) Thao tác khi chia độ đơn giản như sau: Chọn hàng lỗ có số lỗ cần thiết (trong ví dụ 1 là 60 ). Điều chỉnh cho chốt của tay quay vào hàng lỗ đó. Điều chỉnh hai thanh nan quạt làm chuẩn (trong ví dụ 1 hai thanh nan quạt cách nhau 40 khoảng tức là 41 lỗ ). Thanh thứ nhất chạm vào chốt định vị của tay quay, tức là ở mép lỗ xuất phát, thanh thứ hai ở mép lỗ đã chọn cho lần chia độ sắp tới. Sau khi đã phay xong một vị trí, rút chốt định vị ra khỏi lỗ, vặn tay quay đi một số vòng và số lỗ theo tính toán (trong khi đó hai thanh nan quạt cũng đi theo với cự ly đã điều chỉnh). Tới vị trí đã định, lại cắm chốt định vị vào lỗ mới. Chú ỷ: Trong khi thao tác, cần chú ý luôn vặn tay quay theo một chiều để tránh sai số do độ dơ trong đầu chia độ gây nên. Nếu ta vô ý quay tay quay quá vị trí cần thiết thì quay ngược lại 1 đoạn ( khoảng 1/4 vòng) rồi sau đó mới lại quay theo chiều cũ và khi xắp đến vị trí lỗ đã định nên dùng tay gõ nhẹ tay quay cho từ từ lọt đúng lỗ đổi. Nhiều khi trên đĩa không có hàng nào có z lỗ mà chỉ có hàng B lỗ do đó ta phải biến N__A z~ B Ví dụ: Cần chia vòng tròn ra 9 phần bằng nhau z = 9, N= 40 40 . , 4 n = „ = 4 + -7 tq 9 9 Vì trên đĩa không có hàng 9 lỗ mà chỉ có hàng 54 lỗ chẳng hạn. _ , , 4.6 , , 24 «to=4 + ^y = 4 + ^- (í 9.6 54 Khi đó: Mỗi lần phân độ quay ta quay đi 4 vòng chẵn cộng với 24 khoảng trên hàng lỗ 54. Phương pháp chia độ phức tạp. Phương pháp chia độ đơn giản chỉ chia được vòng tròn ra số phần chẵn với số lỗ có sẵn trong đĩa chia. Gặp trường hợp số phần cần chia không chẵn với số lỗ ở đĩa chia, ta phải áp dụng phương pháp chia độ phức tạp (trên đầu chia đơn giản) Nguyên tắc của phương pháp chia độ phức tạp là phối hợp hai lần chia độ đơ ... bàn máy so với chiều quay của trục chỉnh đầu chia độ. Lắp các bánh răng trung gian phải ăn khớp tổt, không hở quá (va đập ồn ào) và cũng không căng quá (chạy bị kẹt răng), lap then tổt, xiết mũ ốc, bỏ mỡ vào răng và trục trung gian. Xoay nghiêng bàn máy Đổ bề rộng của rãnh đúng bằng bề rộng của dao ta cần phải xoay nghiêng bàn máy đi một góc (to). Theo hình vẽ (hình 1) ta thấy đường khai triển của rãnh xoắn trong đó AC là chu vi của phôi (n D), BC là bước xoắn s. Góc ÁBC là góc xoắn p. jjT) ~ ta có: tg/3 = —— => Tính được p s Thông thường góc xoay bàn máy (co) lấy xấp xỉ bằng góc nghiêng p, nhưng khi bước xoắn lớn thương xảy ra hiện tượng ăn lẹm vào phía trong (nhất là khi dao phay có đường kính lớn hoặc phay bằng dao phay góc kép). Vì vậy góc xoay bàn máy phải có trị số khác p, và được tính theo công thức sau: tgĩữ = tg/3.ũữĩ>(o + /) Trong đó: + co: Là góc xoay bàn máy + (3: Góc xoắn của rãnh cần gia công + 0: Góc của dao phay dùng để gia công + y: Góc trước của răng cần gia công - Khi xoay bàn máy cần chú ý hướng xoắn của phôi. Khi phay rãnh xoắn trái cần xoay bàn máy cùng chiều kim đồng hồ và ngược lại. Vỉ dụ: Phôi hình trụ có đường kính 75mm, cần phay rãnh xoắn có bước xoắn 300mm. Góc xoay bàn máy bình thường (P) như sau: tg/3 = ^- = 3,14-J5 0,785 -> p = 38°10' s 300 Nếu dùng dao phay góc kép cỏ 6= 55°, rãnh cần phay có góc trước ỵ= 5° , thì góc xoay bàn máy (uj) sẽ là: tg(ữ = tg/ỉ.cos(0 + ỵ) = Íg38010'.cos(550 +5°) = 0,85.0,5 = 0,3925 —>ứ)«21°25' Kiểm tra sản phẩm. Sử dụng thước cặp, pan me đo ngoài kiểm tra các kích thước như: Đường kính, chiều dày răng, độ nhám bằng so sánh. Để kiểm tra bước xoắn ta sử dụng dưỡng, thước đo góc và dùng calíp giới hạn, hoặc thước cặp, panme đặc biệt để kiểm tra chiều rộng, chiều dày của rãnh. Vệ sinh công nghiệp. Cắt điện vào máy Tháo chi tiết, dao, đầu phân độ, ụ động, điều chỉnh máy về vị trí ban đầu Lau sạch dụng cụ đo, dao , dụng cụ gá để đúng nơi quy định Điều khiển các cơ cấu chạy dao về vị trí an toàn Tra dầu bảo quản lên băng máy - Vệ sinh máy, thiết bị và nơi làm việc Trình tự các bước phay rãnh xoắn TT Bước công việc Chỉ dẫn thực hiện 1. Nghiên cứu bản vẽ Đọc hiểu chính xác bản vẽ Xác định được: Dạng rãnh xoắn, đường kính đỉnh, biên dạng rãnh, số đầu mối (z), chiều cao rãnh (h), bước xoắn (S), góc nghiêng (P), số vòng lỗ và số lỗ cần quay (với số đầu mối lớn hơn 1), bánh răng thay thế, xác định hướng xoắn. Vật liệu của chi tiết gia công Chuyển hoá các ký hiệu thành các kích thước gia công tương ứng. 2 Lập quy trình công nghệ Nêu rõ thứ tự các bước gia công, gá đặt, dụng cụ cắt, dụng cụ đo, chế độ cắt và tiến trình kiểm tra Tính toán đúng và đủ các thông số hình học cần thiết cho một rãnh xoắn. 3. Chuẩn bị vật tư thiết bị dụng cụ Chuẩn bị đầy đủ: Máy, dụng cụ gá, dụng cụ đo kiểm, dụng cụ cắt, phôi, giẻ lau và bảo hộ lao động Dầu bôi trơn ngang mức quy định Tình trạng máy làm việc tốt, an toàn 4. Chọn dao, gá lắp, hiệu chỉnh dao Chọn dao phù hợp với rãnh xoắn cần gia công. Lau sạch trục gá, ống lót, then, dao Gá dao trên trục ngang, (trục đứng) đúng vị trí và đúng yêu cầu kỹ thuật. 5. Gá phôi và (lấy tâm nếu cần) Xác định đúng chuấn gá Gá phôi trên đầu phân độ và mũi tâm, hoặc sử dụng các dụng cụ gá khác đúng yêu cầu Độ không đồng tâm cho phép < 0,0 Imm Lấy tâm phôi (nếu cần) chính xác. 6. Lắp bánh răng thay thế Xác định đủ bánh răng và lắp đúng vị trí của các bánh răng thay thế trên chạc gá, phù hợp với bước xoắn, chiều xoắn. Các bánh răng ăn khớp sít, đều và êm 7. Phay Xoay bàn máy đối với trục ngang; xoay trục đứng bằng dao trụ đứng có góc tương đương với góc xoắn và hướng xoắn ngược lại. Xác định vị trí tương đối giữa dao và phôi Chọn chế độ cắt hợp lý Đường tâm dao trùng với điểm giữa đường tâm phôi (nếu cần) Thực hiện đúng trình tự và phương pháp phay rãnh xoắn. Đúng số rãnh, đều, đúng hướng nghiêng Kích thước sai lệch ± 0,05 mm. 8. Kiểm tra hoàn thiện Kiểm tra tổng thể chính xác Thực hiện công tác vệ sinh công nghiệp Giao nộp thành phẩm đầy đủ Ghi sổ bàn giao ca 12.9. Bài tập ứng dụng: ĐỌC bản vẽ Rà gá phôi: Rà độ song song, độ tròn đều của phôi Gá lắp dao: Dùng dao phay góc đơn (hoặc dao phay trụ) - Tính toán số vòng tay quay: ntq = 40 z 40 8 _ 200 ltt~~S~p~Ĩ2ữ - Tính toán, chọn và lắp bánh răng thay thế: - Tính toán góc xoay bàn máy: tính góc xoay p Trường hợp dùng dao phay góc kép hoặc dao phay có đường kính lớn thì ta tính góc xoay bàn máy như sau: tg(0 = tgp.cos(0 + y) ► (0 = ? (Khi xoay phải xoay đúng hướng, đúng góc độ, sau đó phải hãm chặt các đai ốc để bàn máy chống xoay) *Điều chỉnh máy để phay: Khi phân độ vít hãm đĩa chia phải hãm lại, khi phay phải nới lỏng để đĩa quay theo. Khi phay hết chiều dài một rãnh cần phải hạ bàn máy một khoảng lớn hơn chiều sâu cắt và lùi dao ra ngoài phôi, sau đó lại nâng bàn máy lên một khoảng (bằng khoảng đã hạ), phân độ sang răng khác. Trước khi phay nên phay thử một lát mỏng để xem hướng xoắn, bước xoắn có đúng không. - Khi phay xoắn phải thì phôi quay ngược chiều kim đồng hồ và ngược lại. 12.9.3. Các dạng sai hỏng - Nguyên nhân - Biện pháp đề phòng Các dạng sai hỏng Nguyên nhân Cách phòng ngừa và khắc phục 1. Hướng xoắn sai. Do tính toán bánh răng lắp ngoài và xác định hướng xoắn sai. Lắp sai vị trí của các bánh răng thay thế hoặc sử dụng bánh răng trưng gian không đúng. Nếu phay xong rồi mới phát hiện được thì không sửa được. Muốn đề phòng, trước tiên là phải nắm vững quy tắc chiều xoắn khi phay. Thận trọng trong việc xác định hướng xoay của bàn máy, và vị trí chính xác. Nên kiểm tra cẩn thận kết quả bằng cách phay thử một vạch mờ trên chiều dài phôi rồi kiểm tra lại, nếu thấy đúng mới phay. 2. Bước xoắn, góc xoắn, không đúng thiết kế. - Do trong quá trình xác định các thông số hình học không đúng, hoặc có thể đọc sai các số liệu liên quan đến các thành phần của một rãnh xoắn. Tính toán tỷ số truyền của bộ bánh răng lắp ngoài không chính xác, hoặc lắp sai vị trí khi xác định chiều xoắn của bánh răng. Xác định góc xoắn không đúng, hoặc xoay nhầm số. Trong quá trình phay bộ bánh răng chuyển động không suốt (bị kẹt vào một thời điểm nào đó) Điều này cũng có thể xảy ra trong quá trình thao tác: Quên hoặc nhầm một công đoạn nào đó. Đọc và xác định chính xác các thành phần, thông số hình học của một rãnh xoắn. Góc xoắn, bước xoắn. Tính toán bộ bánh răng lắp ngoài chính xác kể cả các vị trí lắp bánh răng. Kiểm tra chặt chẽ và theo dõi thường xuyên bộ bánh răng lắp ngoài trong quá trình phay. Luôn thận trọng trong thao tác. Nên phát hiện sớm để có các định hướng khắc phục. 3. Rãnh không đúng kích thước, sai số rãnh Chiều sâu của rãnh không đúng có thể cạn, có thể quá sâu, do thao tác sai khi sử dụng các vạch khắc độ của bàn máy. Số đầu mối (số rãnh) không đúng, Do tính nhầm số vòng lỗ trên các đĩa chia, hoặc thao tác sai trong quá trình phay. Nếu phay sâu rồi mới phát hiện được thì không sửa được. Muốn đề phòng, trước tiên là phải kiểm tra khi phay thử, phay phá. Thận trọng trong việc tính toán số lỗ trên các vòng lỗ của các đĩa chia tương ứng với số rãnh, thao tác thận trọng, chính xác. 4. Rãnh không đứng biên dạng Chọn nhầm dao có thể lớn quá, hoặc không đúng biên dạng rãnh, trong trường hợp này thì không sửa được. Trong trường hợp chọn dao đúng, nhưng chọn góc xoay bàn máy sai vẫn dẫn đến biên dạng rãnh sai vì khi cắt nó sẽ mở rộng về một phía nào đó. Nếu phay đúng chiều sâu rồi mới phát hiện được thì không sửa được. Muốn đề phòng, trước tiên là phải kiểm tra khi phay thử, phay phá. Thận trọng trong việc chọn dao phay rãnh. Thao tác thận trọng, chính xác. 5. Độ nhẵn kém, bề mặt không đạt Do chọn chế độ cắt không hợp lí (chủ yếu là lượng chạy dao quá lớn, mà vận tốc cắt thì thấp). Do lưỡi dao bị cùn (mòn quá mức độ cho phép), hoặc dao bị lệch chỉ vài răng làm việc. Do chế độ bôi trơn bằng dung dịch làm nguội không phù hợp, hệ thống công nghệ kém cững chắc. Không thực hiện các bước tiến hành khoá chặt các phương chuyển động của bàn máy. Chọn chế độ cắt hợp lý giữa V, s, t. Kiểm tra dao cắt trước, trong quá trình gia công. Luôn thực hiện tốt độ cứng vững công nghệ: Dao, đồ gá, thiết bị. Sử dụng đúng chế độ bôi trơn, làm nguội. Khóa chặt các vị trí bàn dao không cần thiết. BÀI 13 - PHAY BÁNH RANG TRỤ RANG XOẮN Bánh trụ răng xoắn dùng để truyền động giữa hai trục song song, cắt nhau hoặc thẳng góc. So với bánh trụ răng thẳng và bánh côn răng thẳng thì loại này truyền động êm hơn, không va đập ồn ào vì răng trước chưa ra khớp thì răng sau đã va vào khớp lúc nào cũng có vài răng đang ăn khớp. + Chiều dày chân răng lớn hơn nên bền hơn, truyền được mômen, công suất và vận tốc lớn hơn bánh răng thẳng cùng modul. + Số răng có thể ít hơn 17 răng mà không xảy ra hiện tượng cắt chân răng. - Nhược điểm: Ma sát nhiều và phát sinh lực chiều trục có khuynh hướng đẩy bánh răng theo chiều dọc trục về phía này hoặc phía kia tuỳ theo chiều xoắn và chiều quay. Các thông số cơ bản. Răng xoắn nếu được trải phẳng sẽ tạo với trục của bánh răng một góc p (gọi là góc xoắn). Do đó hình dạng bước răng và chiều dày răng xét ở mặt đầu bánh răng sẽ khác khi xét ở mặt cắt thẳng góc với từng răng (mặt pháp tuyến). - Xét ở đầu của bánh răng, ta có modul chiếch (modul biểu kiến). ms Dp z m„ n COS0 Trong đó: + ms: Modul chếch (modul biểu kiến) + mn: Modul thật (pháp tuyến) - Xét ở mặt cắt thẳng góc với từng răng, ta có modul thật (còn gọi modul thẳng hoặc modul pháp tuyến) mn = ms . COS0 Mô đun thật mn được coi là căn cứ để tính toán các thông số khác của bánh răng trụ răng xoắn ĩĩ.mn - Bước vòng của răng xét ở mặt đầu bánh răng là bước vòng chếch (bước giả). ĩi.t ts = s COS0 cos/? z - Bước vòng của răng xét ở mặt cắt vông góc vơi từng răng là bước vòng thật. tn - 71.mn - ts. cos p Hai bánh răng xoắn muốn ăn khớp với nhau thì phải có cùng modul thật mn và cùng góc xoắn p. Góc xoắn của răng p có thể từ 10 4- 30° (thường lấy 20°) trong trường hợp truyền động giữa hai trục song song. Khi hai trục thẳng góc có thể lấy p = 45° (phụ với 45°) hoặc 60° (phụ với 30°). cos B = " Dp „ , 4 . W „ ĩĩ-Dp íĩ.mư Bước xoăn của răngS: s = = tg/3 siny? 777 7j Đường kính nguyên bản Dp: Dp = = ms .z cos p - Đường kính ngoài De: + Neu: a = 20°: + Neu: a = 14°30': Ds e D e = Dp + l,5m„ = m„ p ’ n n ' z kcosp ' z ^cosp + 1,5 - Đường kính trong Dj: Di = Dp-2mn = mn ^CQS/ĩ Di = mn ' z ^cos/3 2,314 ’ , nếu a = 20° nếu a = 14°30' - Chiều dày răng T. (đo trên vòng tròn nguyên bản và ở mặt cắt thẳng góc với răng) 7 = = ‘mn 2 2 Chiều cao đầu răng hp h] = mn Chiều cao chân răng h2: h2 = 1,25 mn Chiều cao cả răng h: h = h]+ h2 = 2,25mn - Khoảng cách tâm của hai bánh răng A m„(zl+z2) 2 cos/? mS2-Z2 2 + Khi hai trục song song: Dpi _ ms (Z1 Z2 ) _ 2 _ 2 + Khi hai trục thẳng góc: A Dpi + Pp2 mSỊ ‘Z1 , w Á ” 2 ~ 2 - Sô răng giả Z' (tính theo modul chêch) Z' = = Dp cos3p mn.cos2p Chiều rộng răng B ( chiều dầy bánh răng): B = l.ms 1: chiều dài từng răng Phương pháp phay bánh răng trụ răng xoắn . Phay bánh răng trụ răng xoắn chính là loại phay rãnh xoắn định hình trên mặt trụ kết hợp với việc chia độ. Chọn dao. Chọn modul của dao theo modul pháp tuyến mn. Khi chọn số hiệu dao không chọn theo số răng thực z mà chọn số răng giả Z' tính theo mô đun chếch Z' = = Dp cos3 p mn.cos2p Z': là số răng giả dùng để chọn số hiệu dao trong bảng chọn dao của bánh răng trụ răng thẳng. Ví dụ: Cần gia công bánh răng có z = 40, p = 20° TaCÓ: Z’-- 7 40 40 *48 cos3 p cos3 20 (o,829)3 Ta phả i chọn dao theo Z'« 48 Gá dao: Tương tự như khi phay bánh răng trụ thẳng. Gá lắp và điều chỉnh phôi Phôi được gá lên trục gá, trục gá được gá lên mâm cặp chống tâm một đầu hoặc cặp tốc. Sau đó rà độ song song (so với mặt phẳng của bàn máy và rà độ tròn) bằng đồng hồ lò xo. Điều chỉnh cho mũi dao trùng với đường tâm của phôi bằng phương pháp rà bổ đôi. „ „ , x " , , ,Ẫ , V _ n.D.n 1000.Vc Tỉnh toán chê độ căt *c - IQQQ > n - n D Chọn vận tốc cắt: - Chiều sâu cắt: Căn cứ vào chiều cao của răng h = hi + h2 = mn + l,25mn = 2,25 mn Tỉnh toán và chọn bánh răng thay thế: - Tính toán bước xoắn: s ri.rn.z n.Dp p sinp tgP P.N a c -Trong đó: Sp b d + P: là bước vitme bàn máy (P = 5) + N: Đặc tính của đầu chia độ. + sp: Bước xoắn Ví dụ: Phay bánh răng có z = 32, mn = 1,5, p = 20° Ta có: sp n.mn.z 3,14.1,5.32 ° = ’— » 440 sin p 0,342 P.N _ 5.40 _ 200 _ 5 sp " 440 440 11 55 Bánh răng a lắp vào đầu trục vitme, bánh răng b lắp vào đậu trụ phụ của đầu chia. 25 40 n = — <4 z Tỉnh toán sổ vòng tay quay: Xoay góc chéo bàn máy Phải xoay một góc p, chú ý phải xoay đúng chiều (tương tự như phay rãnh xoắn trên phôi trụ) Kiểm tra răng Dùng thước cặp hoặc panme để đo a = m.(l,476065K + 0,013996Z) Đo theo hướng vuông góc với sườn răng Bài tập ứng dụng Đọc bản vẽ z = 29 mn = 1.5 = 20° a = 20° Trình tự gia công Chọn dao và gá lắp dao: Chọn dao có modul pháp tuyến: mn = 1,5 và chọn số hiệu củ dao theo số răng giảZ’ -TinhZ': Z'= —= 29 « 34 -> 6 cos3 /3 (0,939/ Gá lắp phôi: + Gá phôi lên trục gá, một đầu chống tâm, một đầu cặp tốc. + Điều chỉnh cho mũi dao trùng với tâm chi tiết. Tính chế độ cắt: n = 118 (v/p) + Chiều sâu cắt: h = hi + h2 = 2,25. mn = 2,25. 1,5 = 3,375 113 0,342 »330 Tính toán bánh răng thay thế: o n.m„.z 3,14.1,5.24 s = n = ’ sinp sin 20° ; P.40 200 20 40 25 " 330 330 33 30 55 40 40 n*q~ z~ 29 - Tính ntq và tiến hành phay: Sau khi phay xong một rãnh phân độ sang răng khác, trước khi phân độ phải hạ bàn máy xuống cho dao thoát ra khỏi rãnh vừa phay, nếu không răng sẽ bị nát răng - Kiểm tra độ đều bước răng. a = m(l,476065k + 0,013996z) = 1.5.( 1,476065.7 + 0,013996.29) = 16.1 Các dạng sai hỏng - Nguyên nhân - Biện pháp khắc phục Khi phay bánh răng trụ răng xoắn, có thể xảy ra các trường hợp sai hỏng như khi phay bánh răng trụ răng thẳng và khi phay rãnh xoắn. Số răng không đúng (thiếu hoặc thừa): Do chọn số vòng hoặc số lỗ sai hoặc các thao tác chia bị nhầm. Đổ khắc phục tình trạng đó trước khi phay ta nên chia độ để vạch thử, nếu đủ số răng thì mới tiến hành phay. Răng to, răng nhỏ hoặc chiều dày các răng không đều nhau. Do sai số lỗ hoặc trong quá trình phay không khử độ dơ của đầu chia độ. Răng bị lệch: Do rà dao không đúng với đường tâm của phôi hoặc do bàn máy bị xê dịch trong quá trình phay. Biên dạng của răng không đúng. Do chọn dao không đúng môdul, số hiệu. Ta nên chú ý khi chọn dao. Sườn răng không nhẵn: Do dao cùn, lượng chạy dao quá lớn, trục dao bị đảo, phôi bị rung động. Răng đầu to đầu nhỏ: Do khi gá không rà cho đường tâm của phôi song song với hướng chạy dao dọc Góc xoắn sai Bước xoắn sai: Do lắp nhầm bánh răng thay thế (không sửa được). Chiều xoắn sai: Do lắp nhầm bánh răng, xác định nhầm hướng xoắn, nhầm chiều xoay bàn máy Tài liệu tham khảo Kỹ thuật phay- Phạm Quang Lê-Nhà xuất bản Công nhân Kỹ thuật Kỹ thuật phay: Trần Văn Địch - Nhà xuất bản công nhân Kỹ thuật Hà Nội 2001 Kỹ thuật phay - Nguyễn Tiến Đào -NXB KH & KT 2000 Hỏi và đáp về kỹ thuật phay - Phạm Quang Lê - NXB KH&KT
File đính kèm:
bai_giang_thuc_tap_cat_got_kim_loai_nang_cao_phay.doc
02200038_3798_541035.pdf