Bài giảng Nguyên lý và dụng cụ cắt - Trương Quang Dũng
Gia công kim loại bằng cắt gọt là một phương pháp gia công kim loại rất
phổ biến trong ngành cơ khí.
Quá trình cắt kim loại là quá trình con ngưӡi sử dụng dụng cụ cắt để hớt bỏ
lớp kim loại thừa khỏi chi tiết, nhằm đạt được những yêu cầu cho trước về hình
dáng, kích thước, vị trí tương quan giữa các bề mặt và chất lượng bề mặt của chi tiết
gia công.
- Lớp kim loại thừa trên chi tiết cần hớt bỏ đi gọi là lượng dư gia công.
- Lớp kim loại bị cắt bỏ khỏi chi tiết gọi là phoi cắt.
Kinh nghiệm cho thấy rằng: nếu không hiểu biết và vận dụng tốt những kết
quả nghiên cứu về cắt gọt thì không có thể tạo ra nền cơ khí chế tạo hiện đại. Mặt
khác, nếu không có những thành tựu về nghiên cứu cắt gọt thì cũng không thể có
việc tính toán thiết kế máy, dao, đồ gá và công nghệ một cách kinh tế.
Tóm tắt nội dung tài liệu: Bài giảng Nguyên lý và dụng cụ cắt - Trương Quang Dũng
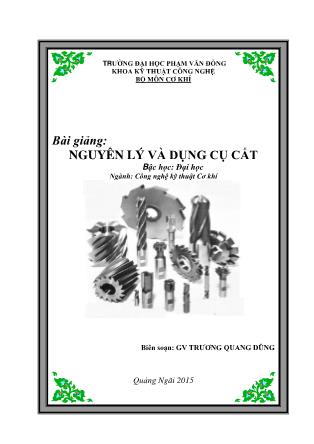
TRƯỜNG ĐҤI HỌC PHҤM VĂN ĐỒNG KHOA KỸ THUẬT CÔNG NGHỆ BỘ MÔN CƠ KHÍ Bài giảng: NGUYÊN LÝ VÀ DỤNG CỤ CẮT Bậc học: Đại học Ngành: Công nghệ kỹ thuật Cơ khí Biên soҥn: GV TRƯƠNG QUANG DŨNG Quảng Ngãi 2015 LỜI NÓI ĐẦU Quá trình sản xuất cơ khí là quá trình biến đổi phôi liệu (kim loại, phi kim: gỗ, chất dẻo ) thành những tiết máy có hình dạng và độ chính xác yêu cầu. Để đạt được hình dáng yêu cầu của tiết máy nhất định thì trong sản xuất cơ khí có những phương pháp khác nhau được thực hiện như: Đúc, rèn, hàn, cán định hình, dập nguội hoặc nóng Nhưng những chi tiết máy có yêu cầu cao về độ chính xác kích thước, lắp lẫn thì cho đến nay chưa có phương pháp gia công tạo hình nào thay thế được phương pháp cắt gọt, thậm chí cả những phương pháp gia công mới như gia công bằng tia lửa điện, điện hóa, siêu âm, laser Có nhiều phương pháp khác nhau gia công bằng cắt: tiện, phay, bào, khoan, khoét, doa, chuốt, cắt ren, cắt rĕng, mài, nghiền Tất cả những phương pháp này đều nhằm thực hiện quá trình lấy đi khỏi bề mặt phôi liệu một lớp “lượng dư” kim loại ở dưới dạng “phoi” để đạt được hình dạng chi tiết. Trong sản xuất cơ khí nói chung và gia công cắt gọt nói riêng, ngoài vấn đề chất lượng sản phẩm thì vấn đề nĕng suất gia công cũng quan trọng. Nó góp phần tác động vào hạ giá thành sản phẩm cũng như giá thành toàn thiết bị. Vậy nĕng suất gia công cắt gọt cũng như chất lượng sản phẩm lại bị điều khiển bởi sự hiểu biết về quá trình gia công vật liệu và những hiện tượng xảy ra trong đó cũng như khả nĕng áp dụng những tiến bộ khoa học kỹ thuật vào quá trình sản xuất cơ khí. Bài giảng “Nguyên lý và Dụng cụ cắt” là tài liệu giúp cho GV và SV thuộc lĩnh cơ khí có được những hiểu biết cơ bản về lĩnh vực tạo hình chi tiết bằng cắt gọt và nắm bắt được những quy luật chung và các hiện tượng “Cơ – Lý – Hóa” xảy ra trong quá trình gia công bằng cắt gọt. Do xuất bản lần đầu nên bài giảng không tránh khỏi những thiếu sót. Tôi mong nhận được những ý kiến đóng góp của bạn đọc và đồng nghiệp. Các ý kiến đóng góp xin gởi về truongquangdungb@gmail.Com, Bộ môn Cơ khí – Khoa Kỹ thuật Công nghệ, trường đại học Phạm Vĕn Đồng. Tác giả GV: Trưѫng Quang Dũng Nguyên lý vƠ dөng cө cҳt MӨC LӨC Nӝi dung Trang Chưѫng 1. NHỮNG KHÁI NIỆM CѪ BẢN CÓ LIÊN QUAN ĐẾN QUÁ TRÌNH CҲT KIM LOẠI 1 1.1. Hệ thống kim loại cần thiết cho gia công cắt 1 1.2. Các phương pháp cắt kim loại 2 1.3. Sự hình thành các bề mặt trên chi tiết trong quá trình cắt 3 1.4. Các chuyển động cắt gọt và chế độ cắt gọt khi gia công cơ 4 1.5. Lớp cắt và tiết diện lớp cắt 6 Chưѫng 2. VẬT LIỆU LÀM DAO 11 2.1. Đặc điểm làm việc và yêu cầu đối với vật liệu làm dao 11 2.2. Các loại vật liệu dùng để chế tạo dao 12 Chưѫng 3. TIỆN VÀ DAO TIỆN 23 3.1. Khái niệm về gia công tiện 23 3.2. Phân loại dao tiện 24 3.3. Thành phần kết cấu của dao tiện 27 3.4. Các định nghĩa cơ bản về các mặt tọa độ 29 3.5. Thông số hình học phần cắt của dao tiện ở trạng thái tĩnh 31 3.6. Thông số hình học phần cắt của dao ở trạng thái động 35 Chưѫng 4. QUÁ TRÌNH CҲT KIM LOẠI 41 4.1. Qúa trình hình thành phoi khi cắt kim loại 41 4.2. Biến dạng kim loại trong quá trình cắt 45 4.3. Quá trình hình thành bề mặt đã gia công trên chi tiết 46 4.4. Các thông số đặc trưng mức độ biến dạng và ma sát khi cắt 50 4.5. Dung dịch trơn nguội 69 75 GV: Trưѫng Quang Dũng Nguyên lý vƠ dөng cө cҳt Chưѫng 5. LỰC CҲT KHI TIỆN 5.1. Hệ thống lực tác dụng lên dụng cụ cắt 75 5.2. Lực cắt và các thành phần lực cắt khi tiện 76 5.3. Các nhân tố ảnh hưởng đến lực cắt 77 5.4. Công thức tổng quát tính lực cắt khi tiện 82 Chưѫng 6. MÀI MÒN VÀ TUỔI BỀN CӪA DӨNG CӨ CҲT 84 6.1. Sự mài mòn của dao 84 6.2. Tuổi bền và tuổi thọ dao 88 Chưѫng 7. TỐC ĐӜ CҲT VÀ CHỌN THÔNG SỐ CҲT 95 7.1. Tốc độ cắt cho phép 95 7.2. Các nhân tố ảnh hưởng đến tốc độ cắt 95 7.3. Cơ sở và trình tự chọn chế độ cắt hợp lý khi gia công cơ 104 7.4. Chọn hình dáng hình học của dao tiện 114 Chưѫng 8. BÀO VÀ XỌC 119 8.1. Đặc điểm và công dụng 119 8.2. Cấu tạo và thông số hình học của dao bào và dao xọc 119 8.3. Các yếu tố chế độ cắt và lớp cắt khi bào và xọc 120 8.4. Xác định chế độ cắt hợp lý khi bào và xọc 122 Chưѫng 9. KHOAN – KHOÉT – DOA 125 9.1. Khái niệm chung 125 9.2. Khoan 125 9.3. Khoét 131 9.4. Doa 133 Chưѫng 10. PHAY 136 10.1. Khái niệm 136 GV: Trưѫng Quang Dũng Nguyên lý vƠ dөng cө cҳt 10.2. Đặc trưng các phương pháp phay 136 10.3. Các loại dao phay 136 10.4. Các thông số hình học dao phay 138 10.5. Các yếu tố của chế độ cắt và lớp cắt khi phay 142 10.6. Phay thuận và phay nghịch 147 10.7. Lực cắt và công suất cắt khi phay 149 Chưѫng 11. CHUỐT 153 11.1. Khái niệm 153 11.2. Kết cấu dao chuốt 154 11.3. Các yếu tố cắt khi chuốt 155 11.4. Các phương pháp chuốt và chọn chế độ cắt 156 Chưѫng 12. MÀI 157 12.1. Đặc điểm 157 12.2. Cấu tạo đá mài 157 12.3. Cách chọn đá 158 . GV: Trѭѫng Quang Dũng Trang: 1 Nguyên lý vƠ dụng cụ cҳt CHѬѪNG 1 NHỮNG KHÁI NIӊM CѪ BҦN CÓ LIÊN QUAN ĐӂN QUÁ TRÌNH CҲT KIM LOҤI Gia công kim loại bằng cắt gọt là một phương pháp gia công kim loại rất phổ biến trong ngành cơ khí. Quá trình cắt kim loại là quá trình con ngưӡi sử dụng dụng cụ cắt để hớt bỏ lớp kim loại thừa khỏi chi tiết, nhằm đạt được những yêu cầu cho trước về hình dáng, kích thước, vị trí tương quan giữa các bề mặt và chất lượng bề mặt của chi tiết gia công. - Lớp kim loại thừa trên chi tiết cần hớt bỏ đi gọi là lượng dư gia công. - Lớp kim loại bị cắt bỏ khỏi chi tiết gọi là phoi cắt. Kinh nghiệm cho thấy rằng: nếu không hiểu biết và vận dụng tốt những kết quả nghiên cứu về cắt gọt thì không có thể tạo ra nền cơ khí chế tạo hiện đại. Mặt khác, nếu không có những thành tựu về nghiên cứu cắt gọt thì cũng không thể có việc tính toán thiết kế máy, dao, đồ gá và công nghệ một cách kinh tế. 1.1. HӋ thống công nghӋ cần thiӃt cho gia công cҳt Muốn hoàn thành nhiệm vụ cắt gọt, con ngưӡi phải sử dụng hệ thống thiết bị nhằm tách được lớp kim loại thừa khỏi chi tiết, đồng thӡi phải đảm bảo các yêu cầu kỹ thuật đã cho trên bản vẽ. Hệ thống thiết bị dùng để hoàn thành nhiệm vụ cắt gọt được gọi là hệ thống công nghệ. Hệ thống công nghệ bao gồm: máy, dao, đồ gá và chi tiết gia công, thưӡng được viết tắt là hệ thống M - D - G - C. Trong đó: - Máy có nhiệm vụ cung cấp nĕng lượng cần thiết cho quá trình cắt gọt. - Dao trong hệ thống công nghệ có nhiệm vụ trực tiếp cắt bỏ lớp lượng dư gia công ra khỏi chi tiết nhӡ nĕng lượng của máy cung cấp thông qua các chuyển động tương đối. - Đồ gá là một bộ phận của hệ thống công nghệ có nhiệm vụ xác định và giữ vị trí tương quan chính xác giữa dao và chi tiết gia công trong suốt quá trình gia công chi tiết. GV: Trѭѫng Quang Dũng Trang: 2 Nguyên lý vƠ dụng cụ cҳt - Chi tiӃt gia công là một thành phần của hệ thống công nghệ - là đối tượng của quá trình cắt gọt. Mọi kết quả của quá trình cắt đều được phản ánh lên chi tiết gia công. Tất nhiên để hoàn thành nhiệm vụ cắt gọt, mỗi bộ phận của hệ thống công nghệ có nhiệm vụ riêng, đồng thӡi phải có mối quan hệ hữu cơ với nhau. 1.2. Các phѭѫng pháp cҳt kim loҥi Yêu cầu bề mặt gia công rất đa dạng, vì vậy phải có nhiều phương pháp cắt gọt để thoả mãn những yêu cầu đa dạng đó. Xuất phát từ mục đích nghiên cứu sử dụng khác nhau, cách phân loại các phương pháp gia công cũng không giống nhau. - Xuất phát từ nguyên lý tạo hình bề mặt phân ra gia công chép hình, gia công định hình, gia công bao hình. a. b. c. d. Hình 1.1. Một số phѭѫng pháp gia công a. Tiện chép hình theo dưỡng b. Tiện định hình bằng dao định hình c. Phay lĕn rĕng bằng phương pháp bao hình d. Phay định hình - Xuất phát từ yêu cầu chi tiết gia công ta có gia công thô, gia công bán tinh, gia công tinh, và gia công bóng. GV: Trѭѫng Quang Dũng Trang: 3 Nguyên lý vƠ dụng cụ cҳt Phổ biến hơn cả là phân loại theo máy gia công. Theo cách phân loại này ta có: gia công trên máy tiện, gia công trên máy phay, gia công trên máy bào, gia công trên máy khoan, gia công trên máy mài,... a.Tiện b. Khoét c. Phay d. Mài Hình 1.2. Phơn loҥi theo máy gia công Ngoài ra, còn cĕn cứ vào bề mặt gia công. Ta phân ra: gia công mặt phẳng, gia công mặt trụ ngoài, gia công lỗ, gia công rãnh,... 1.3. Sự hình thành các bề mặt trên chi tiӃt trong quá trình cҳt Bất kỳ phương pháp gia công nào, quá trình hớt bỏ dần lớp lượng dư gia công cơ (quá trình cắt ) đều hình thành trên chi tiết ba bề mặt có đặc điểm khác nhau. Xét tại một thӡi điểm nào đó trong quá trình gia công (ví dụ khi tiện) , ba bề mặt trên chi tiết được phân biệt như hình 1.1 n t s Mặt đã gia công Mặt đang gia công Mặt sẽ gia công Vùng cắt Hình 1.3. GV: Trѭѫng Quang Dũng Trang: 4 Nguyên lý vƠ dụng cụ cҳt Mặt sӁ gia công là bề mặt của phôi mà dao sẽ cắt đến theo qui luật chuyển động của quá trình cắt. Tính chất của bề mặt này là tính chất bề mặt phôi. Mặt đang gia công là mặt trên chi tiết mà lưỡi dao đang trực tiếp thực hiện tách phoi. Trên bề mặt này đang diễn ra các hiện tượng cơ - lý phức tạp. Mặt đư gia công là bề mặt trên chi tiết mà dao đã cắt qua. Tính chất của bề mặt này là phản ánh những kết quả của các hiện tượng cơ - lý trong quá trình cắt. Vùng cҳt là phần kim loại của chi tiết vừa được tách ra sát mũi dao và lưỡi cắt của dao nhưng chưa thoát ra ngoài. Đây là vùng đang xảy ra các quá trình cơ - lý phức tạp. 1.4. Các chuyển động cҳt gӑt và chӃ độ cҳt khi gia công cѫ Tuỳ thuộc vào phương pháp gia công, tuỳ thuộc vào yêu cầu tạo hình bề mặt, hệ thống công nghệ cần tạo ra những chuyển động tương đối nhằm hình thành nên bề mặt cần gia công. Những chuyển động tương đối nhằm hình thành bề mặt gia công gọi là chuyển động cắt. Những chuyển động cắt gọt được phân làm hai loại chuyển động: - Chuyển động chính . - Chuyển động phụ. 1.4.1. Chuyển động chính và tốc độ cҳt v - Chuyển động chính là chuyển động tạo phoi, nó tiêu hao nĕng lượng cắt lớn nhất. - Chuyển động chính có thể là chuyển động quay tròn như tiện, phay, mài,... hoặc cũng có thể là chuyển động tịnh tiến như bào, xọc, chuốt,... - Chuyển động chính có thể là do các cơ cấu chấp hành khác nhau thực hiện. Ví dụ: do chi tiết thực hiện như trong tiện; do dao thực hiện như trong bào, xọc, khoan, phay, ... Để đặc trưng cho chuyển động chính, ta sử dụng hai đại lượng: - Số vòng quay n (hoặc số hành trình kép) trong đơn vị thӡi gian. Đơn vị đo tương ứng là vg/ph (hoặc htk/ ph) GV: Trѭѫng Quang Dũng Trang: 5 Nguyên lý vƠ dụng cụ cҳt - Tốc độ chuyển động chính hay còn gọi là vận tốc cắt (tốc độ cắt ) ký hiệu là v. đơn vị là m/ ph. Riêng trong mài được lấy đơn vị là m/s. Tốc độ cҳt v là lượng dịch chuyển tương đối giữa dao và chi tiết theo phương vận tốc cắt ứng với một đơn vị thӡi gian (ph) - Nếu chuyển động chính là chuyển động quay tròn thì giữa vận tốc cắt (v), số vòng quay n (vg/ph) và đưӡng kính chi tiết D (mm) có quan hệ sau: v = ( .D.n)/1000 (m/ph) (1.1) - Nếu chuyển động chính là chuyển động tịnh tiến, thì giữa vận tốc cắt v (m/ph), số hành trình kép n (htk/ph) và chiều dài hành trình L (mm) có quan hệ sau: v = (2.L.n)/1000 (m/ph) (1.2) Hình 1.4. Các chuyển động trong quá trình cҳt a. quá trình tiện; b. quá trình phay 1.4.2. Các chuyển động phụ Chuyển động phụ là những chuyển động tiếp tục tạo phoi. Như ta đã biết: lớp lượng dư là một khối không gian, do vậy để tách hết lớp không gian đó thì số chuyển động tối thiểu phải được thực hiện theo 3 phương của hệ toạ độ không gian vuông góc. Như vậy, ngoài chuyển động chính cần phải có hai chuyển động nữa vuông góc với nhau và vuông góc với phương chuyển động chính. Hai chuyển động này trong cắt gọt kim loại gọi là chuyển động chạy dao và chuyển động theo phương chiều sâu cắt. 1. Chuyển động chạy dao và lượng chạy dao s: Chuyển động chạy dao là chuyển động phụ nhằm cắt hết lượng dư trên bề mặt chi tiết. Phương chuyển động chạy dao được ký hiệu là s Để đặc trưng cho chuyển động chạy dao, ta thưӡng dùng các đại lượng sau: a b . b. GV: Trѭѫng Quang Dũng Trang: 6 Nguyên lý vƠ dụng cụ cҳt - Lѭợng chҥy dao ký hiệu là s, đơn vị đo là mm/vg hoặc mm/htk - Tốc độ chҥy dao ký hiệu Vs, đơn vị đo là mm/ph - Lѭợng chҥy dao rĕng ký hiệu là Sz, đơn vị đo là mm/rĕng. a. Lượng chạy dao s: là lượng dịch chuyển tương đối giữa dao và chi tiết theo phương chạy dao tương ứng với một vòng quay (hoặc 1 hành trình kép) của chuyển động chính. Đơn vị đo là mm/vg hoặc mm/htk. b. Tốc độ chạy dao Vs: là lượng dịch chuyển tương đối giữa dao và chi tiết theo phương chạy dao tương ứng với một đơn vị thӡi gian, đơn vị đo là mm/ph. c. Lượng chạy dao rĕng Sz: là lượng dịch chuyển tương đối giữa dao và chi tiết theo phương chạy dao tương ứng với một lưỡi cắt. Đơn vị đo là mm/ rĕng (đại lượng này thưӡng được dùng khi dao có nhiều lưỡi cắt ví dụ như dao phay,...) Như vậy ta có mối quan hệ giữa các đại lượng Vs, s và Sz như sau: Vs = s.n = Sz.z.n (mm/ph) (1-3) z là số rĕng hoặc số lưỡi cắt trên dao. 2. Chuyển động theo phương chiều sâu cắt và chiều sâu cắt t: Chuyển động theo phương chiều sâu cắt là chuyển động phụ nhằm cắt hết lớp chiều dày lớp lượng dư gia công cơ. Chuyển động chiều sâu cắt là chuyển động gián đoạn được điều chỉnh sau mỗi lần chạy dao. Đại lượng đo chiều sâu cắt là chiều sâu cắt t, là lượng dịch chuyển tương đối giữa dao và chi tiết theo phương chiều sâu cắt ứng với mỗi lần chạy dao, đơn vị đo là mm. Trong cắt gọt kim loại ngưӡi ta gọi các đại lượng đo chuyển động chính và các chuyển động phụ (v, s, t) là chế độ cắt khi gia công cơ. 1.5. Lớp cҳt và tiӃt diӋn lớp cҳt Lớp cắt là lớp kim loại cần hớt bỏ đi ứng với một lần chạy dao. Nếu cắt lớp cắt bằng một mặt phẳng chứa lưỡi cắt và vuông góc với vectơ vận tốc cắt v ta sẽ nhận được những tiết diện lớp cắt (hình 1.5) Tiết diện lớp cắt có ý nghĩa quan trọng trong công tác nghiên cứu cắt gọt kim loại. GV: Trѭѫng Quang Dũng Trang: 7 Nguyên lý vƠ dụng cụ cҳt Từ hình 1.5 ta nhận thấy rằng: độ lớn của tiết diện lớp cắt (diện tích) được đặc trưng bӣi hai cặp kích thước: (a, b) và (s, t). Trong đó: - a là chiều dày lớp cҳt, là một kích thước của tiết diện lớp cắt được đo theo phương vuông góc với lưỡi cắt chính - tính bằng mm. - b là chiều rộng lớp cҳt, là một kích thước khác của tiết diện lớp cắt, b chính là chiều dài cắt thực tế của lưỡi cắt, tính bằng mm. - s và t là hai thông số do các chuyển động phụ. ӣ hình a ta có: a s, t b và ta có mối quan hệ: a = s. sin , b = t /sin . ӣ hình b ta có : a = s và t =b Chiều dày cắt a và bề rộng cắt b phụ thuộc vào góc nghiêng chính , nếu giữa nguyên t và s. Khi càng nhỏ phoi cắt ra càng dài, mỏng và ngược lại. - Chiều cao nhấp nhô, là chiều cao của lớp kim loại còn lại sau khi dao cắt đi qua với bước tiến s sau một vòng quay của chi tiết. Kí hiệu: H, đơn vị: mm Chiều cao ảnh hưӣng đến bán kính r của mũi dao + Khi mũi dao ... mặt sau của dao đã mòn đến giới hạn cho phép. Tuổi bền của dao phay thay đổi rất rộng phụ thuộc vào vận tốc cắt, kiểu dao, đưӡng kính dao phay và dạng gia công (thô hay tinh) Ví dụ: Tuổi bền của dao phay mặt đầu hợp kim cứng T = 180 – 420 phút khi gia công thép và của dao phay trụ thép gió T = 120 – 180 phút. Khi tính toán thực tế ta có thể tra tuổi bền của dao trong sổ tay kỹ thuật. 10.7. Lực cắt khi phay Lực cắt tổng R tác dụng lên một rĕng dao phay cũng như lực cắt khi tiện, có thể được phân thành các lực thành phần theo những phương nhất định. Hình 10.14. Lực cắt khi phay bằng dao phay trụ rĕng thẳng * Khi phay bằng dao phay trụ rĕng thẳng, ta có: R = Pr + Pz hoặc R = Pđ + Pn Trong đó: - Pz là lực vòng hay lực tiếp tuyến. nó là lực cắt chính để tạo ra phoi. - Pr là lực hướng kính tác dụng vuông góc với phương trục chính của máy. - Pđ là lực thẳng đứng, tuỳ theo phay thuận hay phay nghịch mà lực này có thể hướng lên hay hướng xuống Từ hình vẽ ta có quan hệ: i R n s Pz Pđ Pr Pn n s R Pz Pđ Pr Pn a. Phay thuận b. Phay nghịch GV: Trương Quang Dũng Trang: 150 Nguyên lý và dụng cụ cắt Pđ = Pz. sini Pr . cosi Dấu (+) ứng với trưӡng hợp phay thuận, dấu (-) ứng với trưӡng hợp phay nghịch. - Pn là lực nằm ngang hay lực chạy dao, vì nó có phương trùng với phương chạy dao. Từ hình vẽ ta có quan hệ: Pn = Pz. cosi Pr . sini Dấu (+) ứng với trưӡng hợp phay nghịch, dấu (-) ứng với trưӡng hợp phay thuận. * Khi phay bằng dao phay trụ rĕng xoắn, ngoài những lực như khi phay bằng dao phay trụ rĕng thẳng, còn có thêm lực dọc trục P0 và lực dọc theo lưỡi cắt Ps Hình 10.15. Lực cắt khi phay bằng dao phay trụ rĕng xoắn Nếu gọi Q là lực tổng tác dụng lên rĕng xoắn, được xác định như sau: Q = R + P0 Hay: Q = PN + Ps Trong đó: - R là lực thành phần tác dụng trong mặt phẳng vuông góc với trục dao, chính là lực tổng tác dụng lên rĕng dao phay rĕng thẳng R = Pr + Pz - PN là thành phần lực tác dụng vuông góc với lưỡi cắt. - Ps là lực dọc theo lưỡi cắt được tạo ra do ma sát của phoi trên mặt trước dao theo phương xoắn vít, do đó gây ra co rút phoi theo chiều rộng lớp cắt. Ps P0 R Q PN R Pr Pz P0 Ps GV: Trương Quang Dũng Trang: 151 Nguyên lý và dụng cụ cắt - P0 lừ lực chiều trục. Khi dùng dao phay trụ rĕng xoắn phải chú ý đến lực này, trong quá trình gá dao lực P0 phải hướng vào ổ trục chính của máy sẽ đảm bảo được độ cứng vững khi gia công. Nếu góc quá lớn thì ngưӡi t dùng 2 dao để khử lực P0. Giữa các lực Ps , P0 và Pz có quan hệ sau: P0 = 0,28.Pz tg Ps = 0,72.Pz sin Tương quan giữa Pr, Pn, Pđ và Pz đối với dao phay trụ rĕng thẳng và rĕng xoắn Khi phay thuận Pr = (0,6 – 0,8)Pz Pn = (0,8 – 0,9)Pz Pđ = (0,7 – 0,9)Pz Khi phay nghịch Pr = (0,6 – 0,8)Pz Pn = (1,0 – 1,2)Pz Pđ = (0,2 – 0,3)Pz * Khi phay bằng dao phay mặt đầu các lực thành phần cũng tương tự như khi phay bằng dao phay trụ. s B t R Pđ Pn Pz Pr i n P0 s n R Pđ Pn Pz B Pr a. Phay đối xứng b. Phay không đối xứng Hình 10.16. Lực cắt khi phay bằng dao phay mặt đầu GV: Trương Quang Dũng Trang: 152 Nguyên lý và dụng cụ cắt Tương quan giữa các lực khi phay bằng dao phay mặt đầu + Khi phay đối xứng: Pn = (0,3 – 0,4)Pz Pđ = (0,85 – 0,95)Pz P0 = (0,5 – 0,55)Pz + Khi phay không đối xứng phay nghịch: Pn = (0,6 – 0,9)Pz Pđ = (0,45 – 0,7)Pz P0 = (0,5 – 0,55)Pz + Khi phay không đối xứng phay thuận: Pn = (0,15 – 0,3)Pz Pđ = (0,9 – 1,0)Pz P0 = (0,5 – 0,55)Pz * Trong quá trình cắt, lực cắt thay đổi phụ thuộc vào sự thay đổi diện tích cắt, ta có: . . . . . xp yp zp p z qp p C t S Z B P D n (KG) (Các hệ số tra bảng CĐCGC cơ khí) ------------o0o--------------- CÂU HӒI ÔN TҰP 1. ωông dụng, đặc điểm, phân loại cá loại dao phay? 2. Trình bày về các thông số dao phay mặt đầu: các góc dao, các lưỡi cắt? 3. Trình bày về các thông số dao phay trụ: kích thước cơ bản, góc, số rĕng? 4. Thế nào là phay thuận, phay nghịch? Giải thích các trưӡng hợp. 5. Tính và chọn chế độ cắt khi phay. GV: Trương Quang Dũng Trang: 153 Nguyên lý và dụng cụ cắt Chương 11 CHUӔT 11.1. Khái niệm Chuốt là một trong những phương pháp gia công kim loại có nĕng suất cao nhất. Chuốt có thể đạt cấp chính xác 3 – 2, độ bóng bề mặt Ra = 0,63 0,32. Chuốt có thể thay thế cho bào, phay, doa, xọc để gia công bề mặt và cho nĕng suất cao hơn 2 – 3 lần, có khi còn cao hơn nữa, chuốt cho nĕng suất cao vì tổng chiều dài của các lưỡi cắt đồng thӡi tham gia làm việc nhiều hơn so với các dao khác. Hình 11.1. Các dạng bề mặt có thể chuӕt Chuốt được dùng trong sản xuất hàng loạt lớn và hàng khối để gia công các chi tiết có hình dạng khác như: mặt phẳng, lỗ trụ, lỗ vuông, rãnh then, lỗ then hoa, các bề mặt định hình, bề mặt tròn xoay, rãnh xoắn, bánh rĕng Khi chuốt lỗ và các mặt định hình phẳng thì chuyển động cắt chính là chuyển động tịnh tiến của dao chuốt, còn chi tiết đứng yên. Khi chuốt các mặt tròn xoay thì dao chuyển động tịnh tiến còn chi tiết chuyển động quay. Quá trình chuốt không có chuyển động chạy dao. Để cắt hết lượng dư trong một hành trình cắt thì các rĕng của dao chuốt được làm cao dần từ rĕng thứ nhất đến rĕng cuối cùng đúng bằng lượng dư gia công. Máy chuốt có 2 loại: máy chuốt đứng để gia công mặt ngoài và chuốt ép, máy chuốt nằm dùng để gia công lỗ. GV: Trương Quang Dũng Trang: 154 Nguyên lý và dụng cụ cắt 11.2. Kết cấu của dao chuӕt Dao chuốt là loại dao có nhiều lưỡi cắt. Tuỳ theo hình dạng của bề mặt lỗ mà dao chuốt có thể là: dao chuốt tòn, vuông, chữ nhật, then hoa, sáu cạnh Dao chuốt mặt ngoài có thể là dao chuốt phẳng hoặc định hình. Thành phần kết cấu của dao chuốt tròn như sau: - Phần 1 là đầu dao dùng để kẹp dao chuốt trong đồ gá và truyền lực Hình 11.2. Kết cấu dao chuӕt - Phần 2 và 3 là cổ dao và côn chuyển tiếp - Phần 4 là phần định hướng phía trước, dùng định tâm chi tiết trước khi chuốt và bảo vệ rĕng dao chuốt khỏi bị gãy do quá tải khi chuốt những lỗ có lượng dư không đều và lớn. - Phần 5 là phần cắt, làm nhiệm vụ cắt hết lượng dư, các rĕng cắt ӣ phần này có kích thước tĕng dần từ rĕng nọ đến rĕng kia một lượng s (s- lượng nâng của rĕng dao chuốt). Trên rĕng có những rãnh chia phoi để chia phoi thành những đoạn nhỏ, do đó giảm biến dạng của lớp cắt và lực cắt. - Phần 6 là phần sửa đúng, có tác dụng sửa đúng kích thước lỗ và tĕng độ bóng bề mặt gia công. Phần sửa đúng có khoảng 4 – 8 rĕng, kích thước đưӡng kính các rĕng sửa đúng đều bằng nhau và bằng kích thước lỗ cần gia công. Trên rĕng sửa đúng không có rãnh chia phoi. - Phần 7 là phần định hướng phía sau , làm nhiệm vụ định hướng chi tiết khi rĕng cuối cùng của dao chưa ra khỏi lỗ. Mục đích là tránh hư hỏng bề mặt lỗ và gãy rĕng dao do chi tiết bị lệch. Trên toàn bộ dao chuốt phần cắt và phần sửa đúng là quan trọng nhất. Độ chính xác và độ bóng của bề mặt gia công chủ yếu là do kết cấu và hình dạng hình học của rĕng dao quyết định 1 2 4 3 5 6 7 GV: Trương Quang Dũng Trang: 155 Nguyên lý và dụng cụ cắt * Thông số hình học của dao chuốt: - Góc trước: ảnh hưӣng rất lớn đến lực cắt và độ bóng bề mặt gia công, góc trước tĕng thì lực cắt giảm và độ bóng tĕng. Tuy nhiên góc trước tĕng quá 120 thì ảnh hưӣng đến độ bóng không đáng kể. Để dễ chế tạo góc trước = 5 250 tuỳ thuộc vào vật liệu gia công. Nhưng thực tế, vì khi mòn dao chuốt thì chỉ mài lại mặt trước, đo đó đối với những rĕng sửa đúng ngưӡi ta chọn = 0 250 để đưӡng kính dao lâu bị giảm khi mài lại, còn ӣ các rĕng cắt thì góc trước được chọn lớn hơn. - Góc sau: ảnh hưӣng đến tuổi bền và kích thước của dao chuốt. Đối với rĕng cắt = 2 30 Đối với rĕng sửa đúng = 1 20 Hình 11.3. Thông sӕ hình hӑc dao chuӕt Ӣ dao chuốt ngoài = 5 100, vì nó có thể điều chỉnh kích thước gia công. 11.3. Các yếu tӕ cắt khi chuӕt 1. Chiều dày cắt a Chiều dày cắt a được tính bằng lượng nâng rĕng (a = Sz). Thưӡng a = (0,02÷0,2)mm, vật liệu dẻo, kém bền a chọn nhỏ và ngược lại. 2. Chiều rộng cắt Là phần chiều dài lưỡi cắt tham gia cắt. Ví dụ: Chuốt lỗ tròn .b D . 3. Diện tích cắt - Diện tích cắt một rĕng là: f = a.b (mm2); = 2 - 30 = 1 - 20 Rĕng cắt Rĕng sửa đúng GV: Trương Quang Dũng Trang: 156 Nguyên lý và dụng cụ cắt - Tổng diện tích cắt do I rĕng cắt ra đồng thӡi là: F = f.i (mm2), với: i = L/t L- chiều dài bề mặt chuốt (mm) t- bước rĕng dao chuốt 11.4. Các phương pháp chuӕt và chӑn chế độ cắt 1. Các phương pháp chuốt Gồm có các phương pháp sau: Chuốt theo lớp, chuốt ĕn dần và chuốt theo mảnh - Chuốt theo lớp: Lớp kim loại được cắt ra có profin đồng dạng với profin của chi tiết cần gia công. Profin của rĕng dao giống profin cuối cùng của bề mặt chi tiết được cắt. Ví dụ: khi chuốt lỗ vuông, thì profin dao là hình vuông. Khi truốt theo lớp thì chiều dày cắt a rất mỏng, còn chiều rộng cắt b lại lớn, do đó độ bóng và độ chính xác bề mặt cao. Nhưng có nhược điểm là khó chế tạo, lực cắt lớn có thể vượt quá giới hạn bền của dao và lực kéo của máy. Hình 11.4. Các phương pháp chuӕt - Chuốt ĕn dần: Profin của lớp cắt và profin của lưỡi cắt không giống profin của bề mặt gia công. Ví dụ: khi chuốt lỗ vuông thì chu vi của lưỡi cắt là tròn, khi chuốt mặt định hình thì lưỡi cắt thẳng. Chỉ những rĕng cuối cùng của dao mới cần có hình dạng của bề mặt gia công. Độ bóng và độ chính xác của bề mặt gia công thấp hơn phương pháp chuốt theo lớp. Bӣi vì trên bè mặt gia công có vết cắt do các rĕng riêng biệt tạo nên. Tuy nhiên phương pháp này dao dễ chế tạo. - Chuốt theo mảnh: a. Chuốt theo lớp b. Chuốt ĕn dần c. Chuốt theo mảnh GV: Trương Quang Dũng Trang: 157 Nguyên lý và dụng cụ cắt Giống như chuốt ĕn dần, profin rĕng dao khi chuốt không giống của chi tiết gia công. Mỗi lớp cắt có chiều dày cắt a và bề rộng cắt b được thực hiện bӣi một nhóm rĕng (từ 2 – 3 rĕng). Do đó còn gọi là chuốt theo nhóm. Trong cùng một nhóm các rĕng có chiều cao bằng nhau. Để cắt được hình dạng chi tiết sẽ phải có nhiều nhóm rĕng. Phương pháp này có ưu điểm: chiều rộng lớp cắt b nhỏ, chiều dày cắt a tĕng nên biến dạng giảm, do đó lực cắt tác dụng lên rĕng nhỏ. Tuy nhiên a lớn dao dễ bị mòn ӣ mặt trước. Phương pháp này dùng để gia công những chi tiết có lượng dư lớn, chi tiết có võ cứng (phôi đúc, rèn) và những chi tiết có thành mỏng, độ cứng vững kém Nhược điểm dao chế tạo phức tạp. 2. Chế độ cắt và tuổi bền của dao chuốt Tuổi bền của dao phụ thuộc vào vật liệu gia công, vật liệu làm dao, độ chính xác gia công. thưӡng định tuổi bền của dao T = 120 – 180 phút. Giữa tuổi bền của dao và tốc độ cắt có quan hệ: . v m y C v T a (m/f) Trong đó: Cv- hệ số phụ thuộc vật liệu gia công và điều kiện gia công T- tuổi bền của dao (phút) a- Chiều dày cắt hay lượng nâng của rĕng (mm) m và y- các số mũ ảnh hưӣng của tuổi bền và chiều dày cắt đến tốc độ cắt. Công suốt chuốt: . 60.1020 z c P vN (Kw) --------------o0o---------------- CÂU HӒI ÔN TẬP 1. Công dụng và kết cấu của dao chuốt? 2. Các sơ đồ cắt khi chuốt. 3. Trình bày các phương pháp và chế độ cắt khi chuốt. GV: Trương Quang Dũng Trang: 157 Nguyên lý và dụng cụ cắt Chương 12. MÀI 12.1. Đặc điểm và công dụng Mài là phương pháp dùng phổ biến để gia công tinh và sửa đúng chi tiết, mài còn dùng để gia công thô, cắt đứt hoặc làm sạch. Gia công tinh các loại bề mặt (mặt trụ, phẳng, rãnh, lỗ, định hình, rĕng, then, v.v...). - Có thể dùng gia công thô (cắt phôi, mài thô), gia công thép đã tôi, các loại vật liệu rất cứng. - Độ chính xác cao và độ bóng cao (8 10). Trên mặt đá mài có nhiều lưỡi cắt có với những hình dạng khác nhau (có thể xem mỗi hạt đá mài như một lưỡi dao cắt). - Chiều sâu cắt và lượng chạy dao nhỏ. - Tốc độ cắt và lực cắt lớn. - Khi cắt dễ bị trượt do kết cấu lưỡi cắt (hạt đá mài). - Đá mài có khả nĕng tự mài sắc bằng cách bong lớp cũ để tạo ra lớp mới sắc hơn. 12.2. Cấu tạo đá mài Hình 12.1. Cấu tạo đá mài Gồm đá mài , bột mài, tấm mài, ... được chế tạo bởi vật liệu mài (hạt mài), chất dính kết, GV: Trương Quang Dũng Trang: 158 Nguyên lý và dụng cụ cắt Vật liệu mài: phải bền- cứng- chịu nhiệt tốt như: kim cương, ôxyt nhôm, cacbit silic, ... Chất dính kết: để liên kết các vật liệu mài tạo thành đá mài như: cao su, silicat, ... Tính chất và tổ chức của đá mài: Tùy theo độ xốp có loại đá chặt, đá vừa, đá xốp. Tùy theo độ cứng của đá có đá cứng, đá mềm. Hình dạng của đá mài: Đá đĩa, đá định hình, thanh mài, dây mài, v.v... 12.3. Cách chӑn đá Chọn vật liệu hạt mài: - Nên chọn vật liệu hạt mài kôrun điện. Khi mài gang xám, đồng thau nên chọn cacbit silic đen, khi mài hợp kim cứng nên chọn cacbit silic xanh. - Vật liệu cứng chọn đá mềm. - Vật liệu mềm chọn đá cứng. Để đảm bảo an toàn, đá mài khi chọn cần cân bằng và thử đá với tốc độ lớn. Chọn độ hạt của hạt mài: Khi mài thô, mài vật liệu mềm và dẻo nên chọn độ hạt lớn. Độ hạt của các hạt mài 11, 12, 16, 25 và 46 cho phép đạt chất lượng bề mặt cao khi mài các chi tiết máy. Chọn chất kết dính: Chất kết dính là ceramic được sử dụng rộng rãi nhất. Chất kết dính là vuncannhit và bankenlit được sử dụng để mài tinh và để chế tạo đá mài dùng cho nguyên công cắt đứt chi tiết. Chọn độ cứng đá mài: Độ cứng đá mài phụ thuộc vào tốc độ cắt, do đó khi tốc độ cắt cao cần chọn đá mài độ cứng cao.Khi mài thép gió và hợp kim nên chọn độ cứng đá mài M3 – CM2, khi mài thô nên chọn độ cứng đá CT1 - CT3, khi mài tinh nên chọn độ cứng đá mài M2 – C2. Chọn cấu trúc đá: GV: Trương Quang Dũng Trang: 159 Nguyên lý và dụng cụ cắt Vật liệu gia công càng dẻo, chiều sâu cắt càng lớn cần chọn đá mài có độ xốp càng lớn. 12.4. Chuyển động cơ bản của máy mài - Chuyển động chính: là chuyển động quay của đá mài. - Chuyển động chạy dao: + Chạy dao vòng (chuyển động tròn CT): Sv (m/ph) + Chạy dao dọc (chuyển động khứ hồi bàn máy mang CT): Sd (m/ph) + Chạy dao ngang hoặc chạy dao hướng kính: Sn or Sk (mm/htk) 12.5. Các loại đá mài và phương pháp mài - Máy mài tròn ngoài: đá mài phải rộng hơn chi tiết. - Máy mài tròn trong: CT quay. - Máy mài phẳng: bằng đá trụ hoặc đá mặt đầu. - Máy mài định hình: mài mặt côn, mài ren, mài rĕng, mài then, ... - Máy mài dụng cụ: mài sắc, mài phá, ... - Máy mài chính xác: máy mài bóng, máy mài nghiền, ... - Máy mài tròn không tâm: mài mặt trụ ngoài và trong. 12.6. Chế độ mài - Tốc độ cắt: V= 1000.60 dn (m/s) - Lượng chạy dao: Sv, Sd , Sn hoặc Sk. - Chiều sâu cắt: + Mài tròn: t= 1/ 2 (D- d) + Mài phẳng: t= H- h ------------------o0o----------------- GV: Trương Quang Dũng Trang: 160 Nguyên lý và dụng cụ cắt CÂU HӒI ÔN TẬP 1. Nêu đặc điểm, công dụng của mài? 2. Trình bày kết cấu đá mài và một số cách chọn đá mài. 3. Trình bày các chuyển động, các loại đá mài và phương pháp mài thông dụng trong cơ khí.
File đính kèm:
bai_giang_nguyen_ly_va_dung_cu_cat_truong_quang_dung.pdf