Bài giảng Máy cắt kim loại (Phần 2)
CHƯƠNG VII
MÁY CHUYỂN ĐỘNG THẲNG
I. MÁY BÀO
I.1. Công dụng và phân loại
I.1.1. Công dụng
Máy bào dùng để gia công chi tiết cĩ dạnh mặt phẳng, cĩ đường chuẩn l
đường thẳng đường sinh l đường thẳng, cong, gy khc. Từ đĩ, hình thành cc
bề mặt gia cơng cĩ hình dng mặt phẳng ngang, đứng và nghiêng, các rãnh chữ
T, rãnh đuôi én, rãnh vuông Ngồi ra đơi khi người ta cịn dng my bo để gia
cơng những bề mặt định hình
Bạn đang xem 20 trang mẫu của tài liệu "Bài giảng Máy cắt kim loại (Phần 2)", để tải tài liệu gốc về máy hãy click vào nút Download ở trên
Tóm tắt nội dung tài liệu: Bài giảng Máy cắt kim loại (Phần 2)
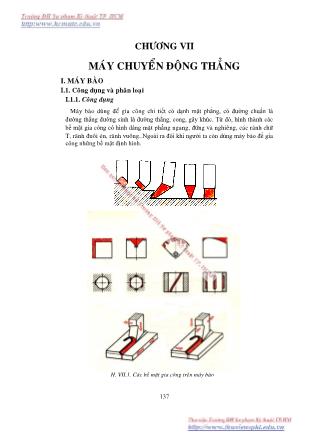
137 CHƯƠNG VII MÁY CHUYỂN ĐỘNG THẲNG I. MÁY BÀO I.1. Công dụng và phân loại I.1.1. Công dụng Máy bào dùng để gia công chi tiết cĩ dạnh mặt phẳng, cĩ đường chuẩn là đường thẳng đường sinh là đường thẳng, cong, gãy khúc. Từ đĩ, hình thành các bề mặt gia cơng cĩ hình dáng mặt phẳng ngang, đứng và nghiêng, các rãnh chữ T, rãnh đuôi én, rãnh vuôngNgồi ra đơi khi người ta cịn dùng máy bào để gia cơng những bề mặt định hình. H. VII.1. Các bề mặt gia công trên máy bào 138 Rãnh chữ T R·ãnh vuông Rãnh đuơi én I.1.2. Phân loại Máy bào có hai loại : - Máy bào ngang. - Máy bào giường. H. VII.2. Máy bào ngang Các dạng bề mặt gia cơng trên máy bào 139 H. VII.3. Máy bào giường 140 I.2.MÁY BÀO NGANG 7A35 I.2.1.Tính năng kỹ thuật Chiều dài lớn nhất của bàn trượt 200-2400 mm. Chuyển động chính là chuyển động thẳng đi về do dao thực. Chuyển động chạy dao là chuyển động tịnh tiến khơng liên tục do phơi thực hiện. Các bộ phận cơ bản của máy bào: Du xích Trục vít dẫn hướng Đầu gắn dao Đai ốc xoay đầu dao Chốt xoay Bàn máy Gá đỡ bàn máy Cử đặt hành trình Chọn tốc độ Du xích ngang Trục quay tay Sống trượt Khâu chia H. VII.4. Các bộ phận cơ bản máy bào ngang 141 I.2.2. Sơ đồ động I.2.3.Các cơ cấu truyền dẫn + Cơ cấu culit lắc Cơ cấu này biến chuyển động quay một chiều thành chuyển động tịnh tiến đi về hai chiều với tốc độ khác nhau. H. VII.5. Sơ đồ động máy bào ngang 142 Khi đĩa biên (1) quay tròn ⇒ cần lắc (4) lắc lư với một góc 2δ ⇒ bàn trượt chuyển động đi và về. + Cơ cấu bánh răng - thanh răng hoặc vítme – êcu : H. VII.7. Cơ cấu culit lắc H. VII.8. Giản đồ thời làm việc cơ cấu cu lit lắc H. VII.9. Giản đồ làm việc cơ cấu bánh răng thanh răng 143 Chỉ dùng cho hành trình lớn từ 1000- 1200 mm. Cĩ ưu điểm là tốc đơ ổn định, nhưng phải dùng thêm cơ cấu đảo chiều chuyển động thẳng bằng cơ khí hoặc bằng điện, nênhiện nay ít dùng. + Cơ cấu dầu ép Dầu từ bơm dầu theo đường ống truyền vào cơ cấu cơng tác.Vị trí 1-đầu bào lùi về,vị trí 2- đầu bào tiến cơng tác. Trên bàn trượt đầu bào cĩ gắn vấu khống chế chiều dài hành trình.Vấu này gạt tay tự động ở vị trí 1 và 2 dùng đảo chiều nhanh,vị trí số V ct và V ck V ct = S Q ; V ck = sS Q − Q: Lưu lượng dầu từ bơm vào trong cơ cấu cơng tác S: Diện tích piston Nhược điểm: khĩ chế tạo, nhiệt độ cĩ ảnh hưởng đến sự làm việc ổn định của máyv.v. + Cơ cấu chạy dao Cơ cấu chạy dao ngang tự động: Cơ cấu cơng tác Vct Vck Bơm Q Van đảo chiều H. VII.10. Sơ đồ máy bào thủy lực 144 Bánh Z1 (21) lắp then với trục đĩa biên (của cơ cấu culít), bánh Z2 (22) lồng khơng trên trục thanh 6. Quá trình làm việc như sau: Yêu cầu sau mổi hành trình kép của đầu bào, bàn máy chạy ngang một lượng S. Đầu tiên đĩa biên quay qua Z1-Z2 tới chốt lệch tâm 7 quay xung quanh Z2 kéo địn 5 làm cho thanh 4 quay lắc. - Khi địn 5 kéo sang phải,con cĩc 4 vào khớp bánh cĩc, truyền chuyển động quay tới trục vítme ngang di động nhờ bàn máy. - Khi địn 5 bị đẩy sang trái, mặt vát nghiên của con cĩc trượt trên răng bánh cĩc và nắp chắn 1, bàn máy đứng yên.Khi bàn máy 9 lên xuống kéo địn 8 và thanh lắc 6 giữ cho cả hệ thống làm việc như cũ. Nguyên tắc làm việc cũng giống như trên, muốn điều chỉnh độ lớn của lượng chạy dao chỉ cần điều chỉnh độ lệch tâm của chốt 7 bằng vít điều chỉnh. + Cơ cấu chạy dao thẳng đứng Khi vấu di động tới chạm vào vấu cố định, làm quay bánh cĩc truyền tới gá dao thẳng đứng qua vítme đứng. H. VII.11. Cơ cấu chạy dao tự động máy bào ngang H. VII.12. Sơ đồ nguyên lý chiều chuyển động bàn máy 145 Vít điều chỉnh Vấu cố định Vấu di động Thân máy H. VII.14. Cơ cấu đầu dao bào H. VII.13. Cơ cấu chạy dao thẳng đứng 146 II. MÁY XỌC: II.1. Cơng dụng : Máy xọc là máy có chuyển động chính là chuyển động thẳng đứng do dao thực hiện theo phương thẳng đứng. Máy xọc dùng để gia cơng các rãnh bên trong lỗ, bánh răng trong,then hoa v.v Các dạng bề mặt máy xọc có thể gia công - . Các dạng mặt định hình. Các dạng mặt phẳng Các dạng rãnh trong và ngoài T T H. VII.15. Chuyển động tạo hình máy xọc H. VII.16.Các dạng chi tiết gia công trên máy xọc 147 II.2.MÁY XỌC 743 III.2.1.Tính năng kỹ thuật -Hành trình lớn nhất của bàn trượt L =300 mm -Đường kính của bàn máy Ф=610 mm -Phạm vi điều chỉnh số hành trình kép 20 ÷ 80 htk/f -Phạm vi điều chỉnh lượng chạy dao 0.05 ÷ 2 mm/hkt Hình dáng bên ngoài Tay quay dọc Tay quay ngang Sống trượt Đế máy Hộp chạy dao Đồ gá Chi tiết Dao Đầu trượt H. VII.17. Các bộ phân cơ bản trên máy xọc 148 II.2.2.Sơ đồ động máy xọc 743 Sơ đồ động máy xọc 743 149 hành trình công tác hành trình chạy không 1 2 6 5 4 02 10 II.2.3. Cơ cấu truyền dẫn: Cơ cấu culit quay Cơ cấu culit – quay gồm đĩa biên (1) nhận truyền động từ hộp tốc độ, trên đĩa biên có lắp con trượt (2). Khi đĩa biên quay quanh tâm O1 ⇒ tay đòn (3) quay quanh tâm O2 với vận tốc góc không đều. Đầu kia của tay đòn (3) lắp khớp động với thanh kéo (4) để di động bàn trượt của dao xọc. Muốn thay đổi hành trình của bàn trượt dao xọc, ta dùng vitme (5) để di động đai ốc (6) trong rãnh của tay đòn (3) H. VII.18. Sơ đồ chuyển động cơ cấu culit quay 150 III. MÁY CHUỐT III.1. Cơng dụng và phân loại III.1.1.Cơng dụng Máy chuốt được sử dụng trong sản xuất hang loạt lớn và hàng khối, Máy dùng để gia cơng chính xác lỗ cĩ dạng prơphin bất kỳ, chuốt rãnh trong, bánh răng trong, lỗ then hoaNgồi ra đang phát triển chuốt mặt phẳng, mặt định hình và rãnh bên ngồi. Chuốt cĩ năng suất và độ chính xác cao. Máy chuốt là máy có chuyển động chính là chuyển động thẳng do dao thực hiện. Dao chuốt có dạng như một thanh kim loại có các lưỡi cắt phân bố đều trên một mặt hoặc trên toàn bộ chu vi của thanh. Hình dáng của dao chuốt: Phần dẫn hướng Phần cắt thơ Phần hiệu chỉnh Chuốt lỗ trụ Chuốt rãnh Phần kéo H. VII.19. Nguyên lý và chuyển độn dao chuốt 151 - Gia công lỗ. - Cắt rãnh. - Gia công bánh răng và thanh răng có modul nhỏ. - Gia công các mặt phẳng. H. VII.20. Các dạnh chi tiết chuốt 152 III.1.2. Phân loại : gồm hai loại Máy chuốt đứng. Máy chuốt ngang. Dao chuốt Chi tiết Chi tiết Dao chuốt Bệ máy H. VII.21. Các dạng chi tiết chuốt H. VII.22. Máy chuốt ngang 153 III.2.MÁY CHUỐT III.2.1.Tính năng kỹ thuật - Lực chuốt lớn nhất : 300 ÷ 400 kN (máy trung bình), 1200 kN (cỡ máy nặng). - Chiều dài lớn nhất của hành trình dao chuốt : 350 ÷ 2000 mm. Ở máy chuốt không có cơ cấu chạy dao. Các lưỡi dao kế tiếp nhau có kích thước lớn dần đã thực hiện lượng chạy dao. Hệ thống thủy lực Bệ máy Dao Chi tiết α βγ Vùng chứa phoi Bước h H. VII.23. Sơ đồ máy chuốt đứng H. VII.24. Lượng chạy dao trên dao chuốt 154 III.2.2..Máy chuốt đứng +Máy chuốt đứng gia cơng mặt ngồi Chuyển động của dao được xác định nhờ các vấu điều chỉnh lắp trên thân máy. Nguyên lý làm việc : Chi tiết gia công cùng bàn máy tiến đến gần dao, và trong chu kỳ làm việc dao chuốt di động từ trên xuống. Khi kết thúc quá trình gia công phôi cùng bàn máy rời khỏi dao và dao di động lên phía trên. 1 H. VII.25. Máy chuốt đứng 155 1 – Thân máy; 2 – Động cơ; 3 – Ống dẫn nước; 4 – Chân máy ; 5 – Bệ máy; 6 – Bàn trượt; 7 – Bàn máy lắp phôi; 8 – Bộ phận làm mát; 9 – Trục chính; 10 – Bộ phận trượt Máy chuốt gia công mặt trong có cấu trúc : bàn máy có lỗ để dao chuốt đi qua, đầu kẹp dao ở dưới bàn máy. Nguyên lý làm việc : Khi bắt đầu gia công, dao chuốt ở vị trí trên cùng. Sau khi lắp phôi vào đồ gá trên bàn máy, cán dao được đưa qua lỗ của chi tiết gia công và được tự động kẹp chặt. Dao chuốt sẽ di động xuống phía dưới thực hiện quá trình cắt gọt III.2.3.Máy chuốt ngang: Hình dáng bên ngoài 1 – Trục chính 2 – Bộ phận làm mát dao chuốt 3 – Bệ đỡ dao 4 – Vỏ máy 5 – Má kẹp phụ 6 – Thân máy H. VII.26. Máy chuốt ngang 156 Máy chuốt ngang làm việc với dao chuốt dài hoặc ngắn với phương pháp nén hoặc kéo. Chủ yếu gia công mặt trong, vì vậy chi tiết gia công phải có lỗ xuyên suốt để dao chuốt đi qua. Nguyên lý làm việc của máy chuốt ngang tương tự như máy chuốt đứng gia công mặt trong. 156 MÁY TỰ ĐỘNG - 2006 - 157 ĐẠI CƯƠNG VỀ MÁY TỰ ĐỘNG 158 CHƯƠNG VIII ĐẠI CƯƠNG VỀ MÁY TỰ ĐỘNG I. Khái Niệm I.1. Vai trò: Công cụ sản xuất luôn được cải tiến, thay đổi dần từ thô sơ đơn giản lên công cụ cơ khí hóa, công cụ tự động hóa. Cách mạng về công cụ sản xuất gắn liền với các cuộc cách mạng khoa học kỹ thuật, cuộc cách mạng khoa học kỹ thuật lần I với nội dung chủ yếu là cơ khí hóa, bắt đầu vào thế kỷ 18. Cuộc cách mạng khoa học kỹ thuật lần II bắt đầu vào đầu thế kỷ-21 với nội dung là tự động hóa và linh hoạt hoá các quá trình sản xuất, khoa học kỹ thuật đã đạt đến trình độ cao. H. VIII.1. Máy tiện tự động điều khiển bằng cam 159 I.2. Tự động hóa là gì: ? Cơ khí hóa là thay thế sức lực của con người bằng máy móc để thực hiện nhanh, những công việc tinh vi, phức tạp, nặng nhọc. Tự động hóa là khả năng cơ khí hóa ở trình độ cao máy móc thực hiện nhanh chóng các quá trình sản xuất mà không cần sự điều khiển trực tiếp của con người. - Hiệu quả lao động của máy tự động hóa: - Công suất lớn, làm việc liên tục 24/ 24. - Tốc độ cao, giảm được thời gian gia công. - Thay thế con người làm những công việc nặng nhọc, độc hại . - Người công nhân có thể theo dõi nhiều máy cùng một lúc. - Máy móc tự động đã thay thế con người để điều khiển các quá trình sản xuất, phức tạp tinh vi, với năng suất cao và chất lượng tốt như: NC, CNC, FMS ( flexible manufacturing system), - Thay thế con người ở những điều kiện làm việc nặng nhọc, độc hại nguy hiểm, giảm thời gian lao động và có thể làm việc liên tục. II . Lý thuyết về năng suất của máy tự động: Nội dung chủ yếu: là giảm thời gian chạy không để tăng năng suất lao động. - Thời gian gia công một sản phẩm, hay thời gian 1 chu kỳ gia công - Kí hiệu: T, tính theo công thức sau: (Phút) Ở đây: lvt - thời gian làm việc Tck- thời gian chạy không, gồm thời gian tiến vào, lùi ra đóng mở các cơ cấu máy. Năng suất của máy tự động Q: là số sản phẩm máy làm ra trong một đơn vị thời gian. (Chiếc / Phút) Nếu t ck = 0, thì năng suất bằng: (1.2) - K: gọi là năng suất công nghệ của máy, nó tượng trưng cho năng suất của một chiếc máy “ lí tưởng “ tự động cắt gọt liên tục, không có hành trình chạy không. Thay trị số: K Tlv 1= , từ công thức (1.2) vào công thức (1.1), ta có: (1.3) cklv ttT += cklv ttT Q +== 11 K T Q lv == 1 η. .1 1. .1 1 K tK K tK Q ckck =+=+= 160 Trong đó; η: gọi là hệ số năng suất của máy, , nó xác định mức độ sử dụng máy có hiệu quả. - Chú ý: từ (1.3) ta có: : Đôi khi còn gọi là “ mức độ gia công liên tục của quá trình công nghệ” giá trị của nó trùng với hệ số năng suất η của máy tự động. Ví dụ: Trong một chu kì gia công tlv = 0.4 phút; tck = 0.8 phút, như vậy năng suất công nghệ K= 4.0 1 = 2.5 (chiếc / phút) và hệ số năng suất: -Tức thời gian có ích của máy chỉ chiếm 33% của chu kì gia công. -Theo công thức (1.3) thì năng suất của máy Q phụ thuộc vào năng suất công nghệ K và hệ số năng suất η. Muốn tăng Q liên tục thi phải đồng thời tăng K và η, tức giảm đồng thời, thơiø gian làm việc(tlv) và thời gian chạy không (tck). Nếu chỉ có một trong hai thành phần này giảm thì gia trị Q sẽ tiến đến một gia trị giới hạn nhất định. Có hai trường hợp năng suất tiến đến một giá trị giới hạn: ( chiếc/ phút) ( chiếc/ phút) + Đường 1 ( hình 1.3) chỉ rằng Q = K ( năng suất lí tưởng), nếu Tck = 0. + Nhưng vì Tck ≠ 0 nên có đường công năng suất thực tế 2. trong trường hợp này dù có tăng K tới đâu thì năng suất Q vẫn tiến đến giới hạn ckT 1 ,chứ không tăng tỉ lệ với K, vì khi K tăng thì trị số: cktK.1 1 +=η lại giảm. cktK .1 1 +=η T t tTT Q lv lv === 1:1η T tlv 33.0 8,0.5,21 1 =+=η K tK KQ ckt Lim ck =+= → .10max ckck t K llK KQ Lim lv 1 .1 0 max =+= → ∞→ H. VIII.2. Dồ thị năng suất 161 Các đường cong trên (hình 1.4) cho thấy mối quan hệ giữa K và η. Ví dụ: Gia công chi tiết có: L =100 mm, S = 0,1 ( mm/ vòng), Tck = 1 ( phút), ( đưa dụng cụ vào và ra, đo, kiểm tra,) Số vòng quay trục chính: ntc = 1000 (vòng / phút). Vậy số vòng quay cần thiết để gia công phôi: 1000 1.0 100 === S Ln (vòng) Năng suất của máy: Q = k. η (chiếc / phút) Năng suất công nghệ K: 11 === n n T K tc lv (chiếc/ phút) Hệ số năng suất η: 5.0 1.11 1 .1 1 =+=+= cktK η Năng suất của máy: Q = k. η =1.0,5 = 0,5 (chiếc /phút) Giả sử có thể nâng k = 50 ( chiếc / phút) lúc đó hệ số năng suất và năng suất của máy Q = K. η = 50.0,02 = 1 (chiếc /phút) Để tăng năng suất lên 50 lần cần những phí tổn về kỹ thuật rất lớn, nhưng năng suất thực tế chỉ tăng 2 lần. Kết luận: muốn tăng năng suất Q của máy đồng thời với việc giảm thời gian làm việc, để tăng năng suất công nghệ K, phải giảm thời gian chạy không (Tck). Lịch sử phát triển của mát tự động có thể biểu diển bằng đồ thị dưới đây, Sau khi chế tạo loại máy đầu tiên người sản xuất cố tận dụng khả năng của chúng bằng cách tăng cường độ gia công ( tăng K), - Nhưng đến một lúc nào đó K tăng mà Q sẽ không tăng, để có năng suất cao hơn nữa cần có một loại máy mới với thời gian chạy không bé hơn hoặc với qui trình công nghệ mới tốt hơn và như thế các máy mới dần dần xuất hiện, các đường cong năng suất cao dần 02.0 1.501 1 ≈+=η H. VIII.3. Đồ thị hệ số năng suất ù H. VIII.4. Giản đồ phát triển năng suất máy tự ... lệ: 1:2 Cách vẽ tương tự như vẽ cam ụ trục phôi: Các đường chạy không là cung tròn Đường cong gia công tiện là cung tròn Đường cong cắt đứt là đường arsimet 0 0 350 340 330 320 310 300 290 280 270 260 250 240 230 220 210 200 190 180 170 160 150 140 130 120 110 100 90 80 70 60 50 40 30 20 10 1 2 3 4 5 6 7 Dmax= 180 Dmin= 40 R=120 10 31 81 26 6 275 288 A130 H. X.11. Hình vẽ cam ụ trục phôi: 0 350340330 320 310 300 290 280 270 260 250 240 230 220 210 200 190 180 170 160 150 140 130 120 11 0 100 90 80 70 60 50 40 30 20 10 1 2 3 4 5 5 6 7 8 0 46 55 77 81 275 288 291 266 R125 Dmax130 Dmin70 A=135 H. X.12. Hình vẽ cam bàn dao đòn cân: 259 9.3) Cam bàn dao đứng: Điều kiện kỹ thuật: - Vật liệu: thép Cm10 - Độ thấm than: 0.8 – 1.2mm - Tôi: 54 – 58 HRc - Tỉ lệ: 1:2 Cam này điều khiển dao vạt góc: Ta lấy; rmax = 60 mm, r = 125 mm, a = 135 mm, h2 = 14.1 Rmin = 45,9 mm từ 0o ÷46o; cam chạy không 46o ÷52o; cam nâng đưa dao gạt vào 52o ÷55o; cam chạy không 55o ÷74o; cam làm việc 74o ÷81o; cam hạ để lùi dao 81o ÷360o; cam chạy không Cam nâng hạ đều là những đoạn thẳng, cam chạy không là những cung tròn, để cam ít mòn ta hạ bán kính cam, hoặc thay bằng đường cong arsimet. Đễ dể lắp cam vào trục phân phối, ta xẻ rãnh cho cam bàn dao đứng. H. X.13.Hình vẽ: cam bàn dao đứng 1 0 3 53 43 3 3 2 3 1 3 0 2 9 2 8 2 7 6 5 2 4 2 3 2 2 2 1 2 0 1 9 1 8 1 7 1 6 1 5 1 4 1 3 1 2 1 1 1 0 9 0 8 0 7 0 6 0 5 0 4 0 3 0 2 1 2 3 4 5 6 4 6 5 5 7 4 8 1 R 1 D m a x D m i A 1 259 II.2. Điều chỉnh máy tiện loại 3:( Máy tiện tự động rêvolve) * Nội dung công việc điều chỉnh : II.2. 1. Lập bản vẽ II.2. 2. Chuẩn bị máy, dụng cụ cắt, phôi, đồ gá II.2. 3. Sơ đồ bố trí bàn dao II.2. 4. Lập sơ đồ gia công II.2. 5. Xác định chế độ cắt II.2. 6. Xác định các thông số công nghệ II.2. 7. Lập phiếu điều chỉnh II.2. 8. Lập chu trình làm việc II.2. 9. Thiết kế cam II.2. 1. Lập bản vẽ: - Xét hình dáng và độ phức tạp gia công của chi tiết, ta chọn máy nhóm 3, Kích thước lớn nhất của chi tiết Þ24. II.2. 2. Chuẩn bị máy, dụng cụ cắt, phôi, đồ gá: Chọn máy 1b140 để gia công chi tiết thép tự động A12, đường kính Þ24, Vật liệu dao cắt thép hơp kim cứng II.2. 3. Sơ đồ bố trí bàn dao: Máy có 3 bàn dao chạy thẳng góc trục phôi. * Các vấn đề cần lưu ý : Các dụng cụ cắt lắp trên đầu rêvolve, các loại dao định hình, cắt đứt lắp trên các bàn dao Để cho đầu dao rêvolve cân bằng, các dụng cụ cắt nên đặt ở những góc độ bằng nhau,( chia đều trên ổ dao 360o ). - Chỉ gia công ren những bề mặt đã gia công để giữ tuổi thọ bàn ren - Phải hiệu chỉnh dao nằm đúng ở vị trí công tác khi đầu rêvolve quay. II.2. 4. Lập sơ đồ gia công: +Sơ đồ gia công H. X.14. chi tiết gia công 260 STT Sơ Đồ Nguyên Công Tên Nguyên Công Bàn Dao 1. 2. 3. 4. 5. 6. 7. Phóng phôi Tiện ngoài phần ren M16 x 2. Tiện thô đoạn Þ20 đến Þ20.5. Tiện rãnh h = 3 mm, vạt góc:1 x 45o. Tiện tinh Þ20. Cắt ren M16 x 2 Cắt đứt Đầu rêvolve Đầu rêvolve Đầu rêvolve Bàn dao trước, bàn dao sau Đầu rêvolve Đầu rêvolve Bàn dao đứng 261 II.2. 5. Xác định chế độ cắt : Dựa vào bảng số liệu điều chỉnh máy tự động ta xác định V(vận tốc cắt ), S( lượng chạy dao ), n( số vòng quay trục chính ) a)Nguyên công tiện : Tiện ngoài Þ25, tra bảng ta được : S2 = 0.12 mm/ vòng, ta chọn V2 = 65(mét/ phút) Số vòng quay trục chính khi tiện : (v/f) Chọn số vòng quay gần với số vòng quay có trên máy: chọn n2 = 800(v/f) Vận tốc thực tế là: (m/f) Tra theo lý lịch của máy ta chọn bánh răng thay thế :A = 25 răng, B = 70 răng Để tiện các nguyên công : 3,4,5,7, ta chọn số vòng quay trục chính : - Nguyên công tiện và cắt đứt :n2 = n3 = n4 = n5 = n7 = 800 (v/f) Lượng chạy dao: s2 = s3 = s5 = 0.12(mm/v ) Lượng chạy dao khi tiện rãnh và vạt góc : s4 = 0.05 (mm/v) Lượng chạy dao khi cắt đứt : s7 = 0.04(mm/v) b) Nguyên công cắt ren : Cắt ren M16 x 2, s6 = t = 2 mm/v, chọn vận tốc cắt :v6 = 8 (mm/f) (v/f) Số vòng quay thực tế trên máy: n6 = 160( v/f) Vận tốc cắt ren thự c tế : 05.8 1000 160.16. 6 == πV ( m/f) II.2. 6. Xác định các thông số công nghệ : a) Xác định chiều dài hành trình : - Ở máy tiện rêvolve tỉ số truyền từ cam đến cơ cấu chấp hành i = 1, nên L và h đều bằng nhau, ∆ = 0.5 ÷ 1 mm. Stt Tên Nguyên Công Chiều Dài Hành Trình 1 Phóng phôi Độ dài chi tiết gia công : l = 48mm Chiều rộng dao cắt đứt : b = 3mm Chi tiết nhô ra khỏi mặt đấu ống kẹp : b = 5mm Lo = 48 +3+5 = 56 mm 863 24.14,3 65.10 . .10 32 3 2 === D vn π 5.60 1000 800.24. 1000 .. 2 2 === ππ nDV 159 16. 8.1000 6 == πn 262 2 Tiện ngòai phần ren M16 x 2 L2 = ∆+b2 = 0.5 + 24 = 24.5 mm 3 Tiện thô đọan φ20 đến đường kính φ20.5 B3 = 14 L3 = ∆+b3 = 0.5 + 14 = 14.5 mm 4 Tiện rãnh : Vạt góc : L4 = ∆ +1/2(d2- d1 ) = 0.5 + 1/2(20.5- 18)=1.75mm L'4 = 3 mm 5 Tiện tinh đọan b5 B5 = b3-b = 14-3 =11 mm. L5 = ∆+b5 +∆1= 0.5 + 11+0.5 = 12 mm ∆1= 0.5 (độ vượt quá của mủi dao ) 6 Cắt Ren Và Lùi Trên Đọan B = 25mm L6 = 2t+B6 = 20 + 2.2 = 24 Mm ( T: Bước Ren) 7 Cắt đứt chi tiết Đường kính cắt đứt : d. = 24- 2x 1 = 22 mm, B = 3mm( chiều rộng dao cắt đứt ), c = 0.3b( hành trình phụ ) L7 = ∆+0.5d +∆1+c = 0.5 + 11 + 1+0.5 = 13 mm b) Xác định số lượng vòng quay và thời gian chính : Số lượng 'vòng quay cần thiết cho mỗi nguyên công, được tính toán với hệ số qui dẫn. -Ta lấy số vòng quay cơ bản là số vòng quay lớn nhất, cho hầu hết các nguyên công: Nto = 800(v/f), hầu hết các nguyên công tiện có c =1, trừ nguyên công cắt ren c6 = nto/n6 = 800/160 = 5 -Số vòng quay cần thiết cho nguyên công 2: (vòng ) Stt Tên Nguyên Công Số Lượng Vòng Quay 3 Tiện thô phần cắt ren M14 K3 = 14,5/ 0,12 = 129(vòng ) 4 Tiện rãnh 3mm K4 = 1.75/ 0,05 = 35(vòng ) K'4 = 3/ 0,05 = 60(vòng ) 5 Tiện tinh φ20 K3 = 12 / 0,12 = 100(vòng) 6 Cắt ren Khi lùi bàn ren K6 =(L6 x C6) / t = (24/2)* 4.5 = 60(vòng ) K'6 = L6/ t = 24/2 = 12(vòng) 7 Cắt đứt chi tiết K7 = 13 / 0.04 = 325( vòng ) - Thời gian chính để gia công chi tiết là: 2041. 12,0 5.24. 2 2 2 2 === CS lK 263 )(66882. 800 6060 1 sn k T to i === ∑ - Thời gian gia công chi tiết : T = 4.85 + 1.1 * 66 = 77.45(s) - Năng suất sơ bộ của máy : )/.(5.46)/.(775.0 45.77 6060 gictfct T Q ==== c) Xác định sự phối hợp giữa các nguyên công : - Xác định phần trăm góc β cho các hành trình chạy không: - Phóng phôi và kẹp phôi β1 = 3% - Quay đầu rêvolve lần thứ nhất : β’1 = 2% - Quay đầu rêvolve sau mỗi lần kế tiếp : β = 3% - Đảo chiều và thay. Đổi số vòng quay trục chính : β5,6 = 1% - Lùi dao cắt đứt : β7 = 1% * Tổng số chạy không của cam :( trừ đi các nguyên công trùng ) Σβ = 16 % * Tổng số góc của hành trình làm việc : Σα = 100- 16 = 84 % (lấy chẳn :19%) • Góc quay làm việc tương ứng với các nguyên công : , * Số lượng vòng quay cần thiết cho toàn bộ hành trình làm việc(1 chu kì gia công ): o o i K K 4.19204. 882 84. 22 === ∑ ∑αα %115.11121. 882 84. 33 ≈=== ∑ ∑ o o i K K αα %33.335. 882 84. 44 ≈=== ∑ ∑ o o i K K αα %67.560. 882 84. 4 ' 4 ≈=== ∑ ∑ o o i K K αα %105.9100. 882 84. 55 ≈=== ∑ ∑ o o i K K αα %67.560. 882 84. 66 ≈=== ∑ ∑ o o i K K αα 0 0 6 ' 6 114,112.882 84. ≈=== ∑ ∑ o o i K K αα %319.30325. 882 84. 77 ≈=== ∑ ∑ o o i K K αα 1050100. 84 882100. === ∑ ∑ α i c K n ( vòng ) 264 ss n n T to c 7975,78 800 1050.6060 ≈=== )/..(7,45)/..(76.0 1050 80060 gtchftch n n T Q c to ===== 45 1.80 36003600 === T Qt * Thời gian cần thiết để gia công chi tiết : * Năng suất chính xác của máy : • Công suất thực tế của máy: T = 79 giây, thời gian có trên máy : T = 80.1 giây (chi tiết/ phút) Trị số này gần bằng với trị số chọn sơ bộ,Ta điền tất cả các thông số trên vào phiếu điều chỉnh. II.2. 7. Lập phiếu điều chỉnh : Phần quay của cam Bán kính cam NC Các bước gia công L= h (mm) S (mm/ v) K (vòng) α [%] β [%] Từ % Đến % Đầu h.tr Cuối h.tr Bàn dao 1 -phóng phôi -quay đầu rêvolve 56 3 2 0 3 3 5 95 95 rêvol ve 2 Tiện ngoài phần Ren M14 x 2 và vạt góc Quay đầu rêvolve 24.5 0.12 204 19 3 5 27 24 27 96.5 121 rêvol ve 3 Tiện thô đoạn Þ20 – Þ20,5 mm Quayđầu rêvolve 14.5 0.12 121 11 3 38 (43) 38 41 120. 5 135 rêvol ve 4 Tiện rãnh b = 3 mm Vạt góc 1 x 45o 1,75 3 0.05 0.05 (35) 60 (3) 6 41 (46) 47 78.2 5 77 80 80 Trướ c sau rêvol ve 5 Tiện tinh Þ 20 Quayđầu rêvolve Đổi vận tốc và chiều quay trục chính 12 0.12 100 10 3 47 57 57 60 20.5 132.5 rêvol ve 265 6 Cắt ren M14 x 2 Đổi vận tốc và chiều quay trục chính Lùi bàn ren Quay đầu rêvolve 2 lần. 24 24 2 2 60 12 6 1 1 60 66 67 (68) 66 67 68 (74) 92 116 116 92 Rêvo lve rêvol ve 7 Cắt đứt chi tiết Lùi dao cắt đứt 13 0.04 325 31 1 68 99 99 100 67 80 Đứng II.2. 8. Lập chu trình làm việc : Góc quay của trục phân phối dược chia ra 100 phần, và chu trình làm việc như sau: Stt Cơ cấu chấp hành Chu trình làm việc 1 Cơ cấu phóng phôi 2 Đầu rêvolve 3 Bàn dao trước 4 Bàn dao sau 5 Bàn dao đứng II.2. 9. Thiết kế cam : Dựa vào thuyết minh của máy ta có các thông số của cam như sau : Cơ cấu chấp hành D (mm) Rmin rmax R A(mm) Cam đầu rêvolve 18 40 140 150 171 Cam bàn dao trước và sau 18 35 80 90 116 Cam bàn dao đứng 18 35 80 90 113 Khoảng cách giữa đầu rêvolve và mặt đầu vấu kẹp : Lmin = 75(mm) a) Cam Đầu Rêvlve : Sơ đồ quan hệ giữa cam và khoảng cách gia công : 3 415 24 27 47 66 74 68 99 38 57 266 - Muốn vẽ cam đầu rêvolve trước tiên phải điều chỉnh vị trí đầu rêvolve, và xác định được khoảng cách L của các nguyên công. Tính các số liệu cần thiết để thiết kế cam : l = lo –b + h lo = l+B+0.5 mm ; Lo : độ nhô ra của phôi l: chiều dài chi tiết gia công B: chiều rộng dao cắt đứt. b: khoảng cách từ mặt đầu phôi đến lưỡi cắt của dao. h: khoảng cách từ lưởi cắt của dao đến đầu rêvolve. Nếu Lmin < Li thì bán kính của cam sẽ giảm đi ∆L, và ngược lại ∆L = Li- Lmin = rmax – ri ri = rmax – ∆L(ri :bán kính đặt con lăn ) Stt bước Bước gia công Số liệu cần thiết (mm) 0 Độ dài nhô ra của phôi Lo = L+B+ 5 = 48+3+5= 56 1 Phóng phôi L1 = lo –b + h = 56- 0 +64 = 120 ∆L = Li- Lmin = 120 – 75 = 45 2 Tiện ngoài L2 = lo –b2 + h = 56-24 +62 = 94 ∆L = Li- Lmin = 94– 75 = 19 3 Tiện thô đoạn Þ20mm L3 = lo –b3 + h = 56- 45 + 62 = 80 ∆L = Li- Lmin = 80 – 75 = 5 5 Cắt ren M14 L5 = lo –b5 + h = 56- 42,5 +62 = 82,5 ∆L = Li- Lmin = 82,5– 75 = 7,5 6 Cắt đứt chi tiết L6 = lo –b6 + h = 56- 24 +67= 99 ∆L = Li- Lmin = 99 – 75 = 24 Bán kính cam đầu rêvolve : rmax = 140 mm, rmin = 40 mm Bán kính cam ở đầu và cuối hành trình : ri = rmax – ∆L r’I = r1 – L 1,( bán kính cam ở đầu hành trình ) r1 = 140 – 45 = 95 mm, r’1 = r1 – L 1 = 95-0 = 95 mm, r2 = 140 – 19 = 121 mm, r’2 = r2 – L 2 = 121-24,5 = 96.5 mm, r3 = 140 – 5= 135 mm, r’3 = r3 – L 3 = 135-15,5 = 119,5 mm, r5 = 140 – 7,5 = 132,5 mm, r’5 = r5 – L 5 = 132.5-13 = 119,5 mm, r6 = 140 – 24= 116 mm, r’6 = r6 – L 6 = 116-24 = 92 mm, Độ nâng cắt ren, cần hạ bán kính 10% ở cuối hành trình cắt ren : (116 – 92).10% = 2.4(mm) ,nên:r6 = 116- 2.4 = 113,6(mm) Các bước vẽ cam đầu rêvolve : - Vẽ các vòng tròn có bán kính rmax rmin, A,(rmax +d/2) H. X.15 Sơ đồ cam Revolve. 267 Chiavòng tròn có bán kính(rmax +d/2), ra 100 phần, điểm khởi đầu vẽ đường tròn này là tại các đường tâm vuông góc nối liền tâm của cam và lỗ tâm định vị Þ10 mm của cam. -Xác định các cung tròn có bán kính R, trên vòng tròn có bán kính A tương ứng với góc α và β ở phiếu điều chỉnh vẽ các cung R qua các phần đã xác định. -Vẽ các bán kính cần thiết cho từng đoạn quay của cam. -Vẽ các đường cong công tác của cam. Cam bàn dao ngang : Ơû cuối hành trình của cam bàn dao ngang con lăn nằm ở bán kính rmax của cam, nên ta chỉ xác định bán kính ở đầu hành trình : Theo thuyết minh :rmax = 80 mm Nguyên công 4: bàn dao trước, R4t = 80, r’4 = 80-1,75 = 78,25 mm Bàn dao sau: r4s = 80, r’4s = 80-3 = 77 mm - Ơû nguyên công 7: nguyên công cắt đứt chi tiết : r7= 80, r’7 = 80 –13.5 = 66.5 mm Điều kiện kỹ thuật: - Vật liệu : thép Cm10 - Độ thấm than: 0.8 – 1.2mm - Tôi: 54 – 58 HRc - Tỉ lệ: 1:2 H. X.14. Cam đầu rêvolve máy tiện tự động 1b140 268 - Biên dạng cam không làm việc thường có bán kính bằng với bán kính rmin của cam. - Cam có tải trọng nhỏ thường được chế tạo bằng gang Gx15-32, Gx 28-48 - Cam có tải trọng lớn thường được chế tạo bằng thép 20x – 40x. [ ] Điều kiện kỹ thuật: - Vật liệu : thép Cm10 - Độ thấm than: 0.8 – 1.2mm - Tôi: 54 – 58 HRc - Tỉ lệ: 1:2 H. X.15. Cam các bàn dao ngang 269 TÀI LIỆU THAM KHẢO 1. Máy Tự Động Và Đường Dây Tự Động, Nguyễn Văn Hùng, Nhà Xuất Bản Đại Học Và Trung Học Chuyên Nghiệp, Hà Nội 1978. 2. Máy Cắt Kim Loại, Gs – Ts,Nguyễn Ngọc Cẩn, Trường Đại Học Sư Phạm Kỹ Thuật,1991. 3. Sách 100 Kiểu Dao Cắt( 100 Kiễu Dao Cắt Được Cấp Bằng Sáng Chế), Kỹ Sư Võ Trần Khúc Nhã, Nhà Xuất Bản Hải Phòng . 4. Chế Độ Cắt Gia Công Cơ Khí, Nguyễn Ngọc Đào – Trần Thế San – Hồ Viết Bình, Trường Đại Học Sư Phạm Kỹ Thuật. 7. Giáo Trình Tự Động Hóa Quá Trình Sản Xuất, Hồ Viết Bình, Trường Đại Học Sư Phạm Kỹ Thuật . X W
File đính kèm:
bai_giang_may_cat_kim_loai_phan_2.pdf