Bài giảng Cơ sở công nghệ chế tạo máy
CHƯƠNG 1
NHỮNG KHÁI NIỆM CƠ BẢN
1.1 Khái niệm về quá trình hình thành sản phẩm cơ khí
1.1.1 Khái niệm về sản phẩm cơ khí
Trong quá trình sản xuất kinh doanh và dịch vụ các mặt hàng cơ khí, sản phẩm cơ khí
có thể là những chi tiết kim loại thuần túy hoặc một cụm máy được lắp ghép từ những chi
tiết kim loại và phi kim loại hay một máy hoàn chỉnh để đáp ứng một nhu cầu sử dụng nào
đó.
Ví dụ: Nhà máy sản xuất phụ tùng máy nổ, sản phẩm cơ khí ở đây có thể là Piston,
xéc măng, thanh truyền v.v hay nhà máy sản xuất ổ bi thì sản phẩm cơ khí là ổ bi được
lắp ghép từ các chi tiết kim loại như vòng bi, viên bi v.v Còn bộ phận phi kim loại ở đây
có thể là vòng cách được chế tạo từ nhựa v.v
Bạn đang xem 20 trang mẫu của tài liệu "Bài giảng Cơ sở công nghệ chế tạo máy", để tải tài liệu gốc về máy hãy click vào nút Download ở trên
Tóm tắt nội dung tài liệu: Bài giảng Cơ sở công nghệ chế tạo máy
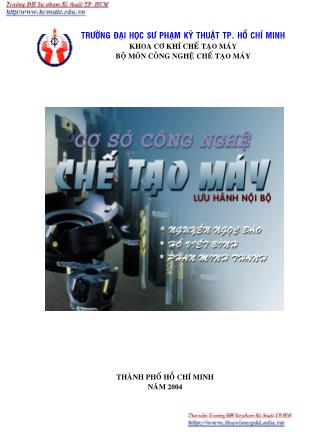
TRƯỜNG ĐẠI HỌC SƯ PHẠM KỸ THUẬT TP. HỒ CHÍ MINH KHOA CƠ KHÍ CHẾ TẠO MÁY BỘ MÔN CÔNG NGHỆ CHẾ TẠO MÁY THÀNH PHỐ HỒ CHÍ MINH NĂM 2004 LỜI NÓI ĐẦU Khối kiến thức thuộc nhóm công nghệ chế tạo máy được phân chia thành hai giáo trình chính, đó là: 1 - CƠ SỞ CÔNG NGHỆ CHẾ TẠO MÁY là môn học cơ sở cho tất cả các ngành cơ khí như: CKM, KCN, TKM, CKT, CKĐ, CTĐ, CĐT Nội dung cung cấp các kiến thức cơ bản như nguyên lý tạo hình bề mặt, các chuyển động cắt gọt, nguyên lý cắt gọt kim loại, dụng cụ cắt cùng với các phương pháp cắt gọt. Để có thể chế tạo ra các chi tiết máy (đối tượng nghiên cứu của Công nghệ chế tạo máy) đạt chất lượng cao cần phải nắm vững các kiến thức cơ bản về nguyên lý cắt gọt, chất lượng bề mặt và độ chính xác gia công chi tiết máy, khái niệm về chuẩn công nghệ và cách chọn chuẩn trong quá trình công nghệ, cũng như những hiểu biết cơ bản về dụng cụ cắt gọt và các phương pháp gia công cắt gọt. 2 – CÔNG NGHỆ CHẾ TẠO MÁY là môn học chuyên ngành cho ngành CKM. Nội dung của giáo trình này gồm các phần chính như: Thiết kế quá trình công nghệ, thiết kế đồ gá, công nghệ gia công các chi tiết điển hình, công nghệ lắp ráp các sản phẩm cơ khí. Phần này giúp cho sinh viên chuyên ngành đi sâu vào lãnh vực thiết kế quI trình công nghệ và các trang thiết bị công nghệ như đồ gá để định vị và kẹp chặt phôi, chi tiết hoặc dao cắt trên các máy công cụ. Ngoài ra, cung cấp một số kiến thức cơ bản về công nghệ lắp ráp các chi tiết máy thành các sản phẩm cơ khí. Để hoàn thành tập giáo trình này ngoài sự cố gắng của các tác giả còn có sự góp ý của đồng nghiệp sao cho phù hợp với mục tiêu đào tạo của trường đại học Sư Phạm Kỹ Thuật. Ngoài giáo trình này ra, trong quá trình học tập sinh viên có thể tham khảo các giáo trình Công nghệ Chế tạo máy của trường Đại học Bách khoa TP HCM và Đại học Bách khoa Hà nội. Các tác giả rất mong sự đóng góp tận tình của các thầy cô đồng nghiệp và sinh viên. TP.Hồ Chí Minh, ngày 30 tháng 8 năm 2003. CÁC TÁC GIẢ CHƯƠNG 1 NHỮNG KHÁI NIỆM CƠ BẢN 1.1 Khái niệm về quá trình hình thành sản phẩm cơ khí 1.1.1 Khái niệm về sản phẩm cơ khí Trong quá trình sản xuất kinh doanh và dịch vụ các mặt hàng cơ khí, sản phẩm cơ khí có thể là những chi tiết kim loại thuần túy hoặc một cụm máy được lắp ghép từ những chi tiết kim loại và phi kim loại hay một máy hoàn chỉnh để đáp ứng một nhu cầu sử dụng nào đó. Ví dụ: Nhà máy sản xuất phụ tùng máy nổ, sản phẩm cơ khí ở đây có thể là Piston, xéc măng, thanh truyền v.v hay nhà máy sản xuất ổ bi thì sản phẩm cơ khí là ổ bi được lắp ghép từ các chi tiết kim loại như vòng bi, viên bi v.v Còn bộ phận phi kim loại ở đây có thể là vòng cách được chế tạo từ nhựa v.v Sản phẩm cơ khí có thể là máy móc thiết bị hoàn chỉnh. Ví dụ: Nhà máy sản xuất máy công cụ (máy tiện, máy phay v.v) Cũng như bất kỳ sản phẩm nào khác, sản phẩm cơ khí được sản xuất nhằm đáp ứng nhu cầu nào đó mà xã hội và thị trường yêu cầu. 1.1.2 Mô hình hình thành sản phẩm cơ khí Quá trình hình thành sản phẩm cơ khí được nhận thức rõ qua việc phân tích mối quan hệ mô tả dưới đây: SX CBSX & TCSX T - THXH - TT SP NC - PT CT Ghi chú: SP: Sản phẩm XH – TT: Xã hội – Thị trường T – TH: Tiếp thị NC – PH: Nghiên cứu – Phát triển CT: Chế thử CBSX và TCSX: Chuẩn bị sản xuất và tổ chức sản xuất. SX: Sản xuất Tiếp thị: là bộ phận rất quan trọng, đầu mối giao tế giữa cung và cầu, có các nhiệm vụ: - Chào và bán hàng. - Nắm bắt thị hiếu của khách hàng đối với sản phẩm công ty, xí nghiệp đang sản xuất. - 3 - - 4 - - Dự báo về nhu cầu phát triển về số lượng, chất lượng và những yêu cầu khác. - Kích thích tạo ra nhu cầu chính đáng mới, qua đó tạo thị trường mới. Ở đây một vấn đề cần quan tâm là nhu cầu không phải có sẳn mà phải qua quảng cáo, dùng thử. Hiện nay để chiếm lĩnh thị truờng rất nhiều công ty đã không ngừng phát triển mạnh về quảng cáo – tiếp thị, đặc biệt là các công ty liên doanh, sản phẩm có thể là mới hoặc truyền thống. Nghiên cứu – Phát triển: là một khâu rất quan trọng có sức mạnh khoa học – công nghệ đủ hoàn thành các công việc: - Nghiên cứu cải tiến sản phẩm đang sản xuất. - Nghiên cứu sản xuất những sản phẩm mới do thị trường yêu cầu. - Nghiên cứu các công nghệ mới đang ứng dụng vào lĩnh vực sản xuất của các xí nghiệp. Bộ phận nghiên cứu – phát triển luôn gắn liền với khâu tiếp thị và chế thử để từ đó cải tiến không ngừng sản phẩm của mình về mọi mặt: chất lượng và mẫu mã để ngày càng chiếm lĩnh được thị trường trong nước và xuất khẩu . Ở những hãng hoặc công ty lớùn, tỷ lệ đầu tư cho bộ phận nghiên cứu – phát triển rất lớn, nhất là đầu tư về lực lượng kỹ thuật, trang thiết bị v.v Chính từ bộ phận này, những thành tựu mới về công nghệ đã được nghiên cứu và ứng dụng, góp phần phát triển hãng và góp phần phát triển khoa học – công nghệ cho từng giai đoạn phát triển của xã hội. Chế thử: Bất cứ công ty, xí nghiệp sản xuất nào muốn phát triển và cải tiến mặt hàng của mình đều phải có bộ phận chế thử. Bộ phận này mục đích kiểm nghiệm về mặt nguyên lý, kết cấu và chất lượng làm việc của thiết bị. Từ thực tế làm việc của thiết bị chế thử chúng ta sẽ tiến hành những thay đổi về các mặt như nguyên lý, kết cấu, vật liệu v.v để thỏa mãn điều kiện tối ưu. Bộ phận chế thử cần thiết được trang bị đầy đủ máy móc cũng như các phương tiện kiểm tra, đánh giá chất lượng. Cán bộ kỹ thuật cũng như công nhân phải có kiến thức thực tế và tay nghề cao. Có đủ năng lực để thực hiện nhanh chóng những sản phẩm mới do bộ phận nghiên cứu phát triển yêu cầu. Chuẩn bị sản xuất và tổ chức sản xuất: Đây là công đoạn quan trọng nhất của quá trình sản xuất sản phẩm. Chuẩn bị sản xuất bao gồm: chuẩn bị về thiết kế và chuẩn bị về công nghệ. - Chuẩn bị về thiết kế: Công việc này thường thuộc bộ phận NC – PT. Căn cứ vào yêu cầu sử dụng, thiết kế ra nguyên lý của thiết bị, từ nguyên lý thiết kế ra kế cấu thực sau đó đưa ra bộ phận chế thử kiểm nghiệm kết cấu và sửa đổi hoàn chỉnh rồi mới đưa sang chuẩn bị sản xuất. - Chuẩn bị về công nghệ:Nhà công nghệ chế tạo căn cứ vào kết cấu đã được thiết kế để chuẩn bị những tài liệu công nghệ hướng dẫn quá trình sản xuất và tổ chức sản xuất. Giai đoạn chuẩn bị công nghệ cần phải tiến hành nhanh chóng, ngày nay nhờ trang bị kỹ thuật hiện đại như sử dụng các thiết bị vi tính với phần mềm mạnh đã giúp cho các nhà - 5 - công nghệ hoàn thành nhanh chóng công việc này với thời gian cần thiết để nhanh chóng đưa vào sản xuất hàng loạt. Có như vậy sản phẩm mới không bị lạc hậu và chiếm lỉnh thị trường nhờ khả năng độc quyền của mặt hàng. Từ bản vẽ thiết kế kết cấu đến lúc ra sản phẩm cụ thể là một quá trình phức tạp, chịu tác động của nhiều yếu tố khách quan và chủ quan làm cho sản phẩn cơ khí sau khi chế tạo có sai lệch so với bản thiết kế kết cấu. Như vậy khi chuẩn bị công nghệ chế tạo cần chú ý khống chế sai lệch đó trong phạm vi cho phép. Công nghệ chế tạo máy là một lĩnh vực khoa học kỹ thuật có nhiệm vụ nghiên cứu, thiết kế và tổ chức thực hiện quá trình chế tạo sản phẩm cơ khí đạt các chi tiêu kinh tế kỹ thuật nhất định trong điều kiện quy mô sản xuất cụ thể. Một mặt công nghệ chế tạo máy lý thuyết phục vụ cho công việc chuẩn bị về công nghệ có hiệu quả nhất. Mặt khác nó nghiên cứu các quá trình hình thành các bề mặt chi tiết và lắp ráp chúng thành sản phẩm. 1.2 Quá trình sản xuất và quá trình công nghệ 1.2.1 Quá trình sản xuất Quá trình sản xuất là quá trình con người tác động vào tài nguyên thiên nhiên để biến nó thành sản phẩm phục vụ cho lợi ích của con người. Quá trình sản xuất trong nhà máy cơ khí là tập hợp các hoạt động có ích để biến nguyên vật liệu hay bán thành phẩm thành sản phẩm. Ví dụ, sản phẩm cơ khí thì phải qua khai thác quặng, luyện kim, chế tạo phôi, gia công cơ khí, gia công nhiệt hóa, kiểm tra, lắp ráp và hành loạt các quá trình phụ như: vận chuyển, chế tạo dụng cụ, bảo quản, sửa chữa thiết bị, chạy thử, điều chỉnh, sơn, bao bì đóng gói .v.v 1.2.2 Quá trình công nghệ Quá trình công nghệ là một phần của quá trình sản xuất trực tiếp làm thay đổi hình dáng kích thước, tính chất lý hóa của bản thân chi tiết và vị trí tương quan giữa các chi tiết trong sản phẩm. Quá trình công nghệ gia công cơ là quá trình cắt gọt phôi để làm thay đổi hình dáng và kích thước của nó. Quá trình công nghệ nhiệt luyện là quá trình làm thay đổi tính chất lý hóa của vật liệu chi tiết. Quá trình công nghệ lắp ráp là quá trình tạo thành những quan hệ tương quan giữa các chi tiết thông qua các loại liên kết mối lắp ghép. Xác định quá trình công nghệ hợp lý rồi ghi thành văn kiện công nghệ thì các văn kiện công nghệ đó gọi là quy trình công nghệ. 1.2.3 Các thành phần của qui trình công nghệ a) Nguyên công Là một phần của quá trình công nghệ, được hoàn thành liên tục, tại một chỗ làm việc và do một hay một nhóm công nhân cùng thực hiện. Nếu thay đổi một trong các điều kiện: tính liên tục, hoặc chỗ làm việc thì ta đã chuyển sang một nguyên công khác. Ví dụ: Tiện một trục bậc như hình 1.1, có thể có 3 phương án gia công như sau: - 6 - - Phương án 1: Tiện đầu B xong rồi trở đầu tiện C ngay, đó là một nguyên công. - Phương án 2: Tiện đầu B cho cả loạt, xong mới tiện đầu C cũng cho cả loạt trên máy đó, như vậy ta đã chia thành 2 nguyên công vì tính liên tục không bảo đảm. l1 l2 l3 AB C Hình 1-1 Tiện trụïc bậc D - Phương án 3: Tiện đầu B trên máy số 1; tiện đầu C trên máy số 2; Như vậy cũng là 2 nguyên công vì chỗ làm việc đã thay đổi mặc dù tính liên tục vẫn bảo đảm. Còn thực hiện nguyên công tiện xong, phay rãnh then A, D ở một máy khác, đó cũng là 2 nguyên công. Nguyên công là đơn vị cơ bản của quá trình công nghệ để hoạch toán kinh tế và tổ chức sản xuất. Phân chia quá trình công nghệ ra thành các nguyên công có ý nghĩa kỹ thuật và kinh tế. * Ý nghĩa kỹ thuật là ở chỗ không thể vừa tiện vừa phay hay vừa tiện vừa mài một chi tiết trên cùng một máy, nên phải chia thành 2 nguyên công (khái niệm này đúng khi không có máy vạn năng tổ hợp). * Ý nghĩa kinh tế là ở chỗ việc phân chia thành ít hay nhiều nguyên công còn tùy thuộc điều kiện thiết bị và sản lượng hàng năm. Hoặc trên một máy chính xác không nên làm cả công việc thô lẫn công việc tinh mà phải chia thành hai nguyên công thô và tinh cho hai máy, máy gia công thô và máy gia công chính xác (vì máy gia công chính xác đắt tiền hơn máy gia công thô). b) Gá Là một phần của nguyên công được hoàn thành trong một lần gá đặt chi tiết (một lần kẹp chặt). Một nguyên công có thể có một hay nhiều lần gá. Ví dụ: Tiện một đầu rồi trở đầu kia (hình 1.1) để tiện là hai lần gá. c) Vị trí Là một phần của nguyên công, được xác định bởi một vị trí tương quan giữa chi tiết gia công với máy hoặc dụng cụ cắt. Cùng ở hình 1.1 nếu dùng ụ phân độ để gá đặt chi tiết khi phay rãnh then, thì sẽ có hai có vị trí khi phay hai rãnh A, D. Như vậy một lần gá có thể có một hoặc nhiều vị trí. - 7 - d) Bước Là một phần của nguyên công được đặc trưng bởi : - Gia công một bề mặt hoặc nhiều bề mặt cùng lúc; - Sử dụng một dao hoặc một nhóm dao ghép; - Cùng một chế độ cắt. Thay đổi một trong ba yếu tố trên là ta đã chuyển qua bước khác. Ví dụ : Trên hình 1.1, khi ta sử dụng phương án một để gia công thì nguyên công tiện có hai bước khác nhau vì đã thay đổi bề mặt gia công, nghĩa là tiện đầu B là bước một, tiện đầu C là bước hai. e) Đường chuyển dao Là một phần của bước để hớt đi một lớp kim loại, sử dụng cùng một dao và một chế độ cắt. Ví dụ: Khi tiện đầu B của trục, do lượng dư quá lớn ta phải cắt hai lần với n, s, t như nhau, đó là hai đường chuyển dao trong cùng một bước. Nếu lần cắt thứ hai ta sử dụng chế độ cắt khác thì đó là hai bước chứ không phải hai đường chuyển dao. f) Động tác Là một hành động của công nhân để điều khiển máy thực hiện việc gia công hay lắp ráp. Ví dụ: nhấn nút, quay ụ dao, xiết mâm cặp 1.3 Hình thức tổ chức sản xuất và dạng sản xuất 1.3.1 Các hình thức tổ chức sản xuất Tổ chức sản xuất theo dây chuyền: mỗi nguyên công hoàn thành tại một địa điểm nhất định nhưng có quan hệ với nhau về mặt thời gian và không gian. Ta còn gọi là tuân thủ nhịp gia công T (phút) và bước vận chuyển L (mét). Số lượng nguyên công phải được tính toán thông qua nhịp sản xuất và độ tin cậy của từng nguyên công. Phương pháp tổ chức sản xuất theo dây chuyền luôn luôn mang lại hiệu quả kinh tế cao. Tổ chức sản xuất không theo dây chuyền: Mỗi nguyên công được thực hiện một cách độc lập, không có liên quan về không gian và thời gian với các nguyên công khác. Hiệu quả kinh tế ở phương pháp này thấp. Việc bố trí thiết bị thường theo nhóm máy: Tiện, phay, bào, mài Phương pháp này phù hợp với sản xuất nhỏ, sửa chữa, chế tạo phụ tùng thay thế v.v 1.3.2 Dạng sản xuất Dạng sản xuất là một kh ... ân chọn bề mặt không gia công nào có yêu cầu chính xác về vị trí tương quan cao nhất đối với các bề mặt gia công làm chuẩn thô. -165- Ví dụ : Khi gia công lỗ biên, nên lấy mặt A và B làm chuẩn thô để có để đảm bảo lỗ có bề dày đều đặn vì yêu cầu độ đồng tâm giữa lỗ với mặt A và B quan trọng hơn giữa lỗ với mặt C cũng không gia công (hình 6.26b). 3. Nếu tất cả bề mặt của chi tiết đều phải gia công thì chọn một mặt nào đó có lượng dư yêu cầu đều, nhỏ nhất làm chuẩn thô. 4. Bề mặt chọn làm chuẩn thô nên tương đối bằng phẳng, không có mép rèn dập (bavia), đậu rót, đậu ngót hoặc quá ghồ ghề. 5. Chuẩn thô chỉ nên dùng một lần trong quá trình công nghệ gia công. Ví dụ ở hình 6.27, dùng mặt 2 để làm chuẩn gia công mặt 3, rồi lại dùng mặt 2 làm chuẩn để gia công mặt 1 thì khó đảm bảo độ đồng tâm giữa hai bề mặt 1 và 3. 6.4.2 Chọn chuẩn tinh Khi chọn chuẩn tinh nên tuân thủ 5 điểm sau đây: 1. Cố gắng chọn chuẩn tinh là chuẩn tinh chính, như vậy sẽ làm cho chi tiết gia công có vị trí tương tự lúc làm việc. Vấn đề này rất quan trọng khi gia công. Ví dụ khi gia công bánh răng nên chọn chuẩn tinh là lỗ bánh răng vì lỗ dùng để lắp với trục truyền động của bánh răng sau này. 2. Cố gắng chọn chuẩn tinh trùng gốc kích thước để sai số chuẩn bằng 0. 3. Chọn chuẩn tinh sao cho khi gia công không vì lực cắt, lực kẹp mà chi tiết bị biến dạng quá nhiều. Lực kẹp phải gần bề mặt gia công, đồng thời mặt định vị cần có đủ diện tích. Ví dụ gia công lỗ tay biên, cần kẹp gần lỗ, không nên kẹp vào giữa (mặt C) để tránh biến dạng (hình 6.26b) 1 3 2 Hình 6.27 Ví dụ chuẩn thô nên dùng một lần 4. Chọn chuẩn tinh sao cho kết cấu đồ gá đơn giản và sử dụng tiện lợi. 5. Cố gắng chọn chuẩn tinh thống nhất. Chọn chuẩn thống nhất nghĩa là trong nhiều lần gá đặt cũng chỉ dùng một chuẩn để thực hiện các nguyên công của qui trình công nghệ, vì khi thay đổi chuẩn sẽ có sai số tích lũy ở những lần gá sau. W W1W1 (Hình 16) b) a) Hình 6.26 A C Hình 6.26 - Sơ đồ định vị khi gia công mặt ngoài Piston (a) và gia công lỗ biên. •• B • 6.6 Kích thước công nghệ 6.6.1 Khái niệm. Để hình thành một kích thước của chi tiết gia công cho trên bản vẽ thiết kế, người công nghệ cần phải xác định phương pháp, trình tự, công cụ (máy, dao, đồ gá) gia công... cũng như phải chọn chọn được chuẩn công nghệ gia công chi tiết (chuẩn định vị, chuẩn điều chỉnh). Như vậy những kích thước có liên quan đến chuẩn định vị, chuẩn điều chỉnh và máy, dao, đồ gá trong quá trình hình thành kích thước của chi tiết cho trên bản vẽ đuợc gọi là kích thước công nghệ. Dưới đây là sơ đồ hình thành kích thước yêu cầu trên bản vẽ thiết kế (hay còn gọi là kích thước thiết kế): Máy-dao- đồ gá [hình thành kích thước thiết kế Bản vẽ chi tiết [kích thước thiết kế] Qui trình công nghệ [kích thước công nghệ] ] Xưởng chế tạo Chuẩn bị sản xuất Kích thước công nghệ do cán bộ công nghệ ở khâu chuẩn bị sản xuất lập ra trong quá trình thiết kế qui trình công nghệ dựa trên cơ sở bản vẽ thiết kế (cũng ở khâu chuẩn bị sản xuất nhưng do cán bộ thiết kế đề ra). Qui trình công nghệ được đưa xuống xưởng chế tạo, các cán bộ kỹ thuật phải điều chỉnh dụng cụ cắt so với chuẩn định vị gia công hoặc chuẩn điều chỉnh trên đồ gá hoặc máy để hình thành kích thước thiết kế. Như vậy kích thước công nghệ có liên quan đến máy, dao, đồ gá. Vì thực tế có những đồ định vị đi liền với máy (mâm cặp, êtô, bàn máy) nên kích thước công nghệ được chia ra làm 3 loại như sau: 1. Kích thước có liên quan đến máy: ký hiệu Cm. Là kích thước điều chỉnnh vị trí tương đối của dao so với những cơ cấu định vị trên máy công cụ như mâm cặp, êtô, bàn máy. Ví dụ hình 6.28a, chi tiết được định vị trên bàn máy hoặc êtô hạn chế 5 bậc tự do để phay mặt bậc và hình 6.28b, chi tiết được -166- Hình 6.28 – Ví dụ kích thước có liên quan đến máy định vị trên mâm cặp hạn chế 5 bậc tự do để tiện trục bậc. 2. Kích thước có liên quan đến dao: ký hiệu Cd Đấy là những kích thước do dao định ra như đường kính mũi khoan, mũi khoét, mũi doa, dao tiện định hình, dao phay định hình hoặc các kích thước điều chỉnh nhiều dao gia công cùng lúc. Hình 6.29 – Ví dụ kích thước có liên quan đến dao 3. Kích thước có liên quan đến đồ gá: ký hiệu Cdg Là những kích thước của đồ gá có ảnh hưởng đến kích thước điều chỉnh vị trí tương đối của dao so với chuẩn định vị và điều chỉnh. Hình 6.30 Sơ đồ định vị gia công rãnh then H1 Cđg DδD Ví dụ hình 6.30, định vị chi tiết bằng khối V dài để gia công rãnh then. Kích thước góc khối V chính là kích thước công nghệ Cđg. 6.6.2 Tính toán kích thước công nghệ Chuẩn thiết kế và chuẩn công nghệ có thể trùng nhau hoặc không trùng nhau. Trường hợp không trùng nhau người cán bộ công nghệ phải biết chuyển đổi từ kích thước thiết kế sang kích thước công nghệ. Có hai cách chuyển đổi từ kích thước thiết kế sang kích thước công nghệ là trực tiếp và gián tiếp theo như mô hình sau: Kích thước thiết kế Kích thước công nghệ Tính toán kích thước Trực tiếp Gián tiếp -167- Dưới đây là một số ví dụ cụ thể chuyển đổi từ kích thước thiết kế sang kích thước công nghệ. 1. Điều kiện chuyển đổi kích thước Điều kiện để chuyển đổi kích thước là dung sai khâu khép kín của chuỗi kích thước công nghệ bằng tổng dung sai các khâu thành phần trong chuỗi: (trong đó n là số khâu thành phần trong chuỗi). ∑ = = n i iKKK 1 δδ Như vậy muốn chuyển đổi từ kích thước thiết kế sang kích thước công nghệ, ta phải hình thành chuỗi kích thước công nghệ. Trong đó kích thước công nghệ sẽ là các khâu thành phần của chuỗi. Việc chọn chuẩn định vị trong quá trình gia công quyết định chuỗi kích thước công nghệ, vì vậy phải chọn thật hợp lý. Nếu điều kiện chuyển đổi hợp lý, ta sẽ tính toán kích thước công nghệ. Còn nếu điều kiện chuyển đổi không hợp lý người công nghệ phải thay đổi lại chuẩn định vị. Trường hợp không thay đổi được chuẩn định vị, phải thương lượng với người thiết kế thay đổi dung sai của một kích thước thiết kế. Nhưng dung sai của một kích thước thiết kế đó không được là khâu khép kín của chuỗi kích thước công nghệ. 2. Ví dụ tính toán kích thước công nghệ Ví dụ 1: Kích thước R là khâu khép kín của chuỗi kích thước Cm1 và Cm2. Như vậy: R = Cm2 - Cm1 Rmax = Cm2 max - Cm1 min Rmin = Cm2 min - Cm1 max Kích thước Cm1 và kích thước R đã biết (chuyển trực tiếp từ kích thước thiết kế qua), kích thước Cm2 chưa biết. Để xác định Cm2, cần phải kiểm tra điều kiện chuyển đổi có thực hiện được không: δR = δCm2 + δCm1 0,4 = δCm2 + 0,2 ⇒ δCm2 = 0,2 -168- Như vậy điều kiện chuyển đổi hợp lý . Vậy kết quả tính như sau: Cm2 max = Rmax + Cm1min = 80,2 + 39,9 = 120,1 Cm2 min = Rmin + Cm1max = 79,8 + 40,1 = 199,9 Kết quả : Cm2 = 120± 0,1 Ví dụ 2 : Kích thước R là khâu khép kín của chuỗi kích thước Cm1 và Cm2. Như vậy: R = Cm2 - Cm1 Rmax = Cm2 max - Cm1 min Rmin = Cm2 min - Cm1 max Kích thước Cm2 và kích thước R đã biết (chuyển trực tiếp từ kích thước thiết kế qua), kích thước Cm1 chưa biết. Để xác định Cm1, cần phải kiểm tra điều kiện chuyển đổi có thực hiện được không: δR = δCm1 + δCm2 0,2 = δCm1 + 0,1 ⇒ δCm1 = 0,1 Như vậy điều kiện chuyển đổi hợp lý . Vậy kết quả tính như sau: Rmax = Cm2 max - Cm1 min Rmin = Cm2 min - Cm1 max Cm1 min = Cm2 max - Rmax = 40,05 – 15,3 = 24,75 Cm1 max = Cm2 min - Rmin = 39,95 − 15,1 =24,85 Kết quả: Cm1 = 25 -0,15 -0,25 -169- TÀI LIỆU THAM KHẢO 1. Phùng Rân – Trương Ngọc Thục – Nguyễn Ngọc Đào Giáo trình CÔNG NGHỆ CHẾ TẠO MÁY; phần 1 và 2 – trường Đại học Sư phạm kỹ thuật, tp. Hồ Chí Minh – 1996. 2. Đặng Văn Nghìn – Lê Minh Ngọc – Lê Đăng Nguyên – Lê Trung Thực CƠ SỞ CÔNG NGHỆ CHẾ TẠO MÁY; trường Đại học Bách khoa tp. Hồ Chí Minh – 1992. 3. Trần Doãn Sơn – Hồ Đắc Thọ – Lê Đức Quý - ... CƠ SỞ CÔNG NGHỆ CHẾ TẠO MÁY; trường Đại học Bách khoa tp. Hồ Chí Minh – 1995. 4. Lê Văn Tiến – Nguyễn Đắc Lộc - ... CÔNG NGHỆ CHẾ TẠO MÁY; tập 1 và 2; Nhà xuất bản giáo dục - 1994 5. Constantin Picos TEHNOLOGIA CONSTRUCTIEI DE MACHINI; Bucuresti - 1974 6. Barơbasôp KỸ THUẬT TIỆN; Nhà xuất bản “MIR” Moscow - 1984 7. Barơbasôp KỸ THUẬT PHAY; Nhà xuất bản “MIR” Moscow - 1984 8. Dương Văn Linh – Trần Thế San – Nguyễn Ngọc Đào HƯỚNG DẪN THỰC HÀNH KỸ THUẬT TIỆN; nhà xuất bản Đà Nẵng - 2000 9. Hoàng Trí – Nguyễn Thế Hùng - Trần Thế San THỰC HÀNH CƠ KHÍ; nhà xuất bản Đà Nẵng - 2000 MỤC LỤC Lời nói đầu Chương 1: NHỮNG KHÁI NIỆM CƠ BẢN 3 1.1 Khái niệm về quá trình hình thành sản phẩm cơ khí 3 1.1.1 Khái niệm về sản phẩm cơ khí 1.1.2 Mô hình hình thành sản phẩm cơ khí 1.2 Quá trình sản xuất và quá trình công nghệ 5 1.2.1 Quá trình sản xuất 1.2.2 Quá trình công nghệ 1.3 Dạng sản xuất và hình thức tổ chức sản xuất 7 1.3.1 Các hình thức tổ chức sản xuất 1.3.2 Dạng sản xuất Chương 2: CƠ SỞ LÝ THUYẾT CẮT GỌT KIM LOẠI 10 2.1 Khái niệm chung 11 2.1.1 Các bề mặt chi tiết máy thường gặp 11 2.1.2 Các chuyển động tạo hình bề mặt 11 2.1.3 Các phương pháp cắt gọt kim loại 14 2.1.4 Khái niệm về các bề mặt hình thành khi gia công chi tiết 15 2.1.5 Khái niệm cơ bản về dụng cụ cắt 16 2.1.6 Các bề mặt tọa độ để nghiên cứu dụng cụ cắt 17 2.1.7 Thông số hình học phần cắt của dao tiện khi thiết kế 18 2.1.8 Aûnh hưởng gá đặt dao và các chuyển động cắt đến góc độ dao 20 2.1.9 Thông số hình học lớp cắt khi cắt gọt 23 2.2 Vật liệu chế tạo dụng cụ cắt 25 2.2.1 Những yêu cầu đối với vật liệu làm dụng cụ cắt 25 2.2.2 Các loại vật liệu chế tạo dụng cụ cắt 26 2.3 Cơ sở vật lý quá trình cắt kim loại 31 2.3.1 Quá trình tạo phoi và hiện tượng co rút phoi 31 2.3.2 Quá trình hình thành bề mặt gia công và hiện tượng cứng nguội 36 2.3.3 Hiện tượng lẹo dao 38 2.3.4 Hiện tượng nhiệt 40 2.3.5 Hiện tượng rung động 42 2.3.6 Hiện tượng mài mòn dao và vấn đề tuổi bền dao 43 3.3.7 Hiện tượng lực cắt 47 2.4 Lựa chọn hình dáng mặt trước và thông số hình học hợp lý của dao 51 2.5 Xác định chế độ cắt hợp lý khi gia công 53 Chương 3: CÁC PHƯƠNG PHÁP GIA CÔNG 60 3.1 Các phương pháp gia công chuẩn bị phôi 60 3.2 Các phương pháp gia công cắt gọt 67 3.2.1 Phương pháp tiện 67 3.2.2 Phương pháp bào, xọc 71 3.2.3 Phương pháp phay 74 3.2.4 Phương pháp khoan, khoét, doa 83 3.2.5 Phương pháp chuốt 93 3.2.6 Phương pháp mài 96 3.2.7 Phương pháp mài nghiền 100 3.2.8 Phương pháp mài khôn 101 3.2.9 Phương pháp mài siêu tinh xác 101 3.2.10 Phương pháp đánh bóng 102 3.2.11 Phương pháp cạo 103 3.3 Các phương pháp gia công điện vật lý và điện hóa 104 3.3.1 Phương pháp gia công bằng tia lửa điện 105 3.3.2 Phương pháp gia công bằng chùm tia lade 106 3.3.3 Phương pháp gia công bằng siên âm 107 3.3.4 Phương pháp gia công điện hoá 109 3.3.5 Mài điện hóa 110 Chương 4: CHẤT LƯỢNG BỀ MẶT CHI TIẾT MÁY 112 4.1 Yếu tố đặc trưng của chất lượng bề mặt 112 4.1.1 Tính chất hình học bề mặt gia công 112 4.1.2 Tính chất cơ lý của lớp bề mặt chi tiết gia công 113 4.2 Aûnh hưởng của chất lượng bề mặt tới khả năng làm việc của chi tiết máy 114 4.2.1 Aûnh hưởng của độ nhấp nhô bề mặt 115 4.2.2 Aûnh hưởng của độ biến cứng 116 4.2.3 Aûnh hưởng của ứng suất dư 117 4.3 Aûnh hưởng của các yếu tố công nghệ tới chất lượng bề mặt chi tiết máy 118 4.3.1 Aûnh hưởng đến nhấp nhô bề mặt 118 4.3.2 Aûnh hưởng đến biến cứng bề mặt 120 4.4 Các phương pháp nâng cao chất lượng bề mặt 122 4.4.1 Phương pháp đạt độ bóng bề mặt 122 4.4.2 Các phương pháp tạo lớp cứng nguội bề mặt 123 Chương 5: ĐỘ CHÍNH XÁC GIA CÔNG 125 5.1 Khái niệm và định nghĩa 125 5.2 Các phương pháp đạt độ chính xác gia công trên máy công cụ 127 5.2.1 Phương pháp cắt thử từng kích thước riêng biệt 127 5.2.2 Phương pháp tự động đạt kích thước trên máy công cụ đã điều chỉnh 128 5.3 Các nguyên nhân gây ra sai số gia công 129 5.3.1 Aûnh hưởng do biến dạng đàn hồi của hệ thống công nghệ 129 5.3.2 Aûnh hưởng do độ chính xác và tình trạng mòn của hệ thống công nghệ 135 5.3.3 Aûnh hưởng do biến dạng nhiệt của hệ thống công nghệ 136 5.3.4 Aûnh hưởng do sai số gá đặt 138 5.3.5 Aûnh hưởng do rung động của hệ thống công nghệ 138 5.3.6 Aûnh hưởng do phương pháp và dụng cụ đo 139 5.4 Phương pháp xác định độ chính xác gia công 139 5.4.1 Phương pháp thống kê kinh nghiệm 139 5.4.2 Phương pháp thống kê xác xuất 140 5.4.3 Phương pháp thống kê theo đồ thị điểm 141 5.4.4 Phương pháp tính toán phân tích 142 5.5 Các phương pháp điều chỉnh máy 143 5.5.1 Điều chỉnh tĩnh 5.5.2 Điều chỉnh theo chi tiết cắt thử bằng calíp làm việc của người thợ 145 5.5.3 Điều chỉnh theo chi tiết cắt thử bằng dụng cụ đo vạn năng 146 Chương 6: CHUẨN VÀ KÍCH THƯỚC CÔNG NGHỆ 149 6.1 Định nghĩa và phân loại chuẩn 149 6.2 Quá trình gá đặt chi tiết 152 6.2.1 Khái niện về quá trình gá đặt chi tiết khi gia công 6.2.2 Các phương pháp gá đặt chi tiết trước gia công 153 6.3 Nguyên tắc 6 điểm khi định vị chi tiết 154 6.4 Sai số gá đặt 158 6.4.1 Sai số đồ gá 6.4.2 Sai số kẹp chặt 6.4.3 Sai số chuẩn 159 6.5 Hướng dẫn cách chọn chuẩn 164 6.5.1 Cách chọn chuẩn thô 6.5.2 Cách chọn chuẩn tinh 165 6.6 Kích thước công nghệ 166 6.6.1 Khái niệm 6.6.2 Tính toán kích thước công nghệ Tài liệu tham khảo
File đính kèm:
bai_giang_co_so_cong_nghe_che_tao_may.pdf