Bài giảng Cơ khí đại cương - Phạm Tài Thắng
GiỚI THIỆU
Môn học Cơ khí đại cương dùng để giảng dạy cho
sinh viên hệ đại học ngành Bảo hộ lao động nhằm
cung cấp kiến thức cơ bản về:
Quá trình sản xuất cơ khí
Chi tiết máy và cơ cấu máy điển hình
Chất lượng bề mặt và độ chính xác gia công
Các công nghệ gia công cắt gọt kim loại
Bạn đang xem 20 trang mẫu của tài liệu "Bài giảng Cơ khí đại cương - Phạm Tài Thắng", để tải tài liệu gốc về máy hãy click vào nút Download ở trên
Tóm tắt nội dung tài liệu: Bài giảng Cơ khí đại cương - Phạm Tài Thắng
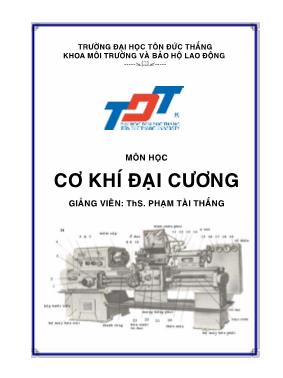
TRÖÔØNG ÑAÏI HOÏC TOÂN ÑÖÙC THAÉNG KHOA MOÂI TRÖÔØNG VAØ BAÛO HOÄ LAO ÑOÄNG -----# "----- MOÂN HOÏC CÔ KHÍ ÑAÏI CÖÔNG GIAÛNG VIEÂN: ThS. PHAÏM TAØI THAÉNG 4/17/2010 1 TRÖÔØNG ÑAÏI HOÏC TOÂN ÑÖÙC THAÉNG KHOA MOÂI TRÖÔØNG BHLÑ Ơ ĐẠ ƢƠ Taøi lieäu tham khaûo Giôùi thieäu Ñaùnh giaù moân hoïc Noäi dung giaûng daïy 2 GiỚI THIỆU Môn học Cơ khí đại cương dùng để giảng dạy cho sinh viên hệ đại học ngành Bảo hộ lao động nhằm cung cấp kiến thức cơ bản về: Quá trình sản xuất cơ khí Chi tiết máy và cơ cấu máy điển hình Chất lượng bề mặt và độ chính xác gia công Các công nghệ gia công cắt gọt kim loại 3 TAØI LIEÄU THAM KHAÛO 1. Cơ khí đại cương. Hoàng Tùng-Nguyễn Tiến Đào, NXB KHKT, 2006 2. Dung sai lắp ghép và kỹ thuật đo lường. Ninh Đức Tốn- Xuân Bảy, NXB GD 3. Máy cắt kim loại. Trường CĐKT Cao Thắng, 2000 4. Cơ khí đại cương. ĐH Đà Nẵng, 2002 4 ÑAÙNH GIAÙ MOÂN HOÏC Ñieåm thöù 1 (10%): Baøi taäp Ñieåm thöù 3 (70%): Kieåm tra cuoái kyø Ñieåm thöù 2 (20%): Kieåm tra giöõa kyø 4/17/2010 2 5 1.1. Khaùi nieäm veà saûn phaåm, chi tieát maùy, phoâi, cô caáu maùy CHÖÔNG 1: MOÄT SOÁ KHAÙI NIEÄM CÔ BAÛN VEÀ SAÛN XUAÁT CÔ KHÍ 1.2. Quaù trình thieát keá, saûn xuaát vaø quaù trình coâng ngheä 1.3. Caùc thaønh phaàn cuûa quaù trình coâng ngheä 1.4. Caùc daïng saûn xuaát vaø hình thöùc toå chöùc saûn xuaát 1.5. Caùc phöông phaùp gia coâng 6 1.1. Khaùi nieäm veà saûn phaåm, chi tieát maùy, phoâi, cô caáu maùy: Saûn phaåm cô khí: vaät phaåm cuoái cuøng cuûa moät quaù trình saûn xuaát. VD: baùnh raêng, maùy khoan, ñai oác, Chi tieát maùy: laø ñôn vò nhoû nhaát vaø hoaøn chænh veà maët kyõ thuaät cuûa maùy. VD: bulong, cam, Phoâi: laø vaät phaåm ban ñaàu cuûa moät coâng ñoaïn saûn xuaát. VD: phoâi ñuùc, phoâi reøn, Boä phaän maùy: goàm nhieàu chi tieát maùy lieân keát vôùi nhau. VD: hoäp toác ñoä, baøn xe dao, Cô caáu maùy: laø moät phaàn cuûa maùy hoaëc boä phaän maùy coù chöùc naêng nhaát ñònh. VD: baùnh vít- truïc vít, baùnh raêng thanh raêng, 7 1.2. Quaù trình thieát keá, saûn xuaát vaø quaù trình coâng ngheä Quaù trình thieát keá: phaùt thaûo, tính toaùn, thieát keá ra moät saûn phaåm. Quaù trình saûn xuaát: taùc ñoäng vaøo taøi nguyeân thieân nhieân bieán thaønh saûn phaåm phuïc vuï con ngöôøi. Quaù trình coâng ngheä: tröïc tieáp laøm thay ñoåi traïng thaùi vaø tính chaát cuûa ñoái töôïng saûn xuaát. Quy trình coâng ngheä: laø vaên kieän coâng ngheä ghi laïi quaù trình coâng ngheä cuï theå. 8 1.3. Caùc thaønh phaàn cuûa quaù trình coâng ngheä 1.3.1. Nguyeân coâng: laø moät phaàn cuûa quaù trình coâng ngheä ñöôïc hoaøn thaønh lieân tuïc, taïi moät choã laøm vieäc vaø do moät hay moät nhoùm coâng nhaân cuøng thöïc hieän 1.3.2. Gaù: laø moät phaàn cuûa nguyeân coâng ñöôïc hoaøn thaønh trong moät laàn gaù ñaët chi tieát 1.3.3. Vò trí: laø moät phaàn cuûa nguyeân coâng, ñöôïc xaùc ñònh bôûi vò trí töông quan giöõa chi tieát vôùi maùy hoaëc giöõa chi tieát vôùi duïng cuï caét 1.3.4. Böôùc: laø moät phaàn cuûa nguyeân coâng ñöôïc ñaëc tröng bôûi beà maët, dao hoaëc cheá ñoä caét 1.3.5. Ñöôøng chuyeån dao: laø moät phaàn cuûa böôùc ñeå hôùt ñi moät lôùp kim loaïi, söû duïng cuøng moät dao vaø moät cheá ñoä caét. 1.3.6. Ñoäng taùc: laø moät haønh ñoäng cuûa ngöôøi coâng nhaân ñeå ñieàu khieån maùy thöïc hieän vieäc gia coâng hay laép raùp. 4/17/2010 3 9 1.4. Caùc daïng saûn xuaát vaø hình thöùc toå chöùc saûn xuaát 1.4.1. Caùc daïng saûn xuaát: tuøy theo saûn löôïng haøng naêm vaø möùc ñoä oån ñònh cuûa saûn phaåm maø ngöôøi ta chia ra 3 daïng saûn xuaát: ñôn chieác, haøng loaït vaø haøng khoái 1.4.2. Caùc hình thöùc toå chöùc saûn xuaát: theo daây chuyeàn vaø khoâng theo daây chuyeàn 10 1.5. Caùc phöông phaùp gia coâng 1.5.1. Phöông phaùp gia coâng caét goït (gia coâng coù phoi): - Laø phöông phaùp gia coâng duøng duïng cuï caét ñeå hôùt ñi 1 lôùp vaät lieäu treân beà maët chi tieát gia coâng 1.5.2. Phöông phaùp gia coâng khoâng caét goït (gia coâng khoâng phoi): - Laø phöông phaùp gia coâng duøng duïng cuï ñeå laøm bieán daïng deûo lôùp beà maët chi tieát gia coâng ôû traïng thaùi nguoäi hoaëc nung noùng 1.5.3. Phöông phaùp gia coâng baèng ñieän lyù vaø ñieän hoùa: - Laø phöông phaùp gia coâng ñaëc bieät ñeå gia coâng caùc loaïi vaät lieäu coù ñoä cöùng cao, beà maët phöùc taïp, kích thöôùc nhoû, 11 2.1. Khaùi nieäm veà chaát löôïng beà maët cuûa saûn phaåm CHÖÔNG 2: CHAÁT LÖÔÏNG BEÀ MAËT VAØ ÑOÄ CHÍNH XAÙC GIA COÂNG CÔ KHÍ 2.2. Độ chính xác gia công cơ khí 2.2.1. Khái niệm về tính lắp lẫn trong ngành cơ khí 2.2.2. Khái niệm về kích thƣớc, dung sai, sai lệch giới hạn 2.2.3. Lắp ghép (khái niệm và phân loại) 2.2.4. Dung sai lắp ghép các bề mặt trơn 2.2.5. Dung sai hình dạng, dung sai vị trí và nhám bề mặt 12 2.1. Khaùi nieäm veà chaát löôïng beà maët cuûa saûn phaåm: 2.1.1.1. Độ nhấp nhô tế vi: 2.1.1. Các yếu tố đặc trƣng: Sai lệch trung bình số học Ra (m): n i i n L a y nn yyy dxxy L R 1 21 0 1... .)( 1 Chiều cao mấp mô trung trình Rz (m): 5 )...()...( 1042931 hhhhhh Rz 4/17/2010 4 13 2.1.1.2. Ñoä soùng beà maët: laø chu kyø khoâng baèng phaúng cuûa beà maët chi tieát maùy ñöôïc quan saùt trong phaïm vi lôùn hôn ñoä nhaùm beà maët. 2.1.1.3. Tính chaát cô lyù cuûa lôùp beà maët: bao goàm lôùp bieán cöùng beà maët vaø öùng suaát dö beà maët. 14 2.1.2.1. Aûnh höôûng ñeán tính choáng moøn: 2.1.2. Aûnh höôûng chaát löôïng beà maët tôùi khaû naêng laøm vieäc cuûa chi tieát maùy: => Aûnh höôûng ñeán ñoä chính xaùc cuûa moái laép - Ñoä nhaùm beà maët caøng lôùn chi tieát moøn caøng nhanh 2.1.2.2. Aûnh höôûng ñeán ñoä beàn moûi cuûa chi tieát : - Ñoä nhaùm beà maët caøng lôùn, chi tieát deã phaù huûy do moûi 2.1.2.3. Aûnh höôûng ñeán tính choáng aên moøn hoùa hoïc cuûa lôùp beà maët chi tieát: - Ñoä nhaùm beà maët caøng lôùn, khaû naêng aên moøn kim loaïi caøng cao 15 2.2. Độ chính xác gia công cơ khí : - Là khả năng các chi tiết có thể thay thế cho nhau mà không cần lựa chọn hay sửa chữa thêm vẫn đảm bảo yêu cầu kĩ thuật của mối ghép. 2.2.1. Khái niệm về tính lắp lẫn trong ngành cơ khí : 2.2.2. Khái niệm về kích thƣớc, dung sai, sai lệch giới hạn: 2.2.2.1. Kích thƣớc danh nghĩa: - Kích thước danh nghĩa là kích thước đã được tính toán. Sau đó, quy tròn theo các giá trị cho trong dãy kích thước tiêu chuẩn - Ký hiệu: Kích thước danh nghĩa của trục là dN Kích thước danh nghĩa của lỗ là DN 16 2.2.2.2. Kích thƣớc thực: - Kích thước thực là kích thước kích đo trực tiếp trên chi tiết gia công bằng những dụng cụ đo - Ký hiệu: Kích thước thực của trục là: dt Kích thước thực của lỗ là: Dt 2.2.2.3. Kích thƣớc giới hạn: - Kích thước giới hạn là kích thước lớn nhất và nhỏ nhất mà kích thước thực của chi tiết đạt yêu cầu nằm trong phạm vi đó - Ký hiệu: + Kích thước giới hạn lớn nhất dmax , Dmax + Kích thước giới hạn nhỏ nhất dmin , Dmin 4/17/2010 5 17 2.2.2.4. Dung sai: - Dung sai là hiệu số giữa kích thước giới hạn lớn nhất và kích thước giới hạn nhỏ nhất. - Ký hiệu: Dung sai chi tiết trục : Td Dung sai chi tiết lỗ : TD 2.2.2.5. Các sai lệch giới hạn: - Sai lệch trên: là hiệu đại số giữa kích thước giới hạn lớn nhất và kích thước danh nghĩa - Ký hiệu: Sai lệch trên es, ES - Sai lệch dưới: là hiệu đại số giữa kích thước giới hạn nhỏ nhất với kích thước danh nghĩa - Ký hiệu: Sai lệch dưới ei, EI 18 2.2.3. Lắp ghép (khái niệm và phân loại): 2.2.3.1. Khái niệm: - Lắp ghép: là sự phối hợp các chi tiết một cách cố định (như bulông gắn vào đai ốc) hoặc phối hợp di động (như trục quay trong ổ, sự chuyển động của vít me, đai ốc trong máy tiện) để tạo thành một mối ghép. 2.2.3.2. Phân loại: a. Lắp ghép có độ hở (lắp lỏng): - Là mối ghép có kích thước của trục luôn luôn nhỏ hơn kích thước của lỗ - Kí hiệu: + Độ hở lớn nhất : S max + Độ hở nhỏ nhất : S min + Dung sai lắp gheùp : T S 19 b. Lắp ghép có độ dôi (lắp chặt): - Là mối ghép có kích thước của lỗ luôn luôn nhỏ hơn kích thước của trục. - Ký hiệu: + Độ dôi lớn nhất : Nmax + Độ dôi nhỏ nhất : Nmin + Dung sai lắp ghép : TN c. Lắp ghép trung gian: - Là mối ghép mà tuỳ theo kích thước của trục và lỗ mà mối ghép có độ hở hoặc độ dôi . - Ký hiệu: + Độ hở lớn nhất : Smax + Độ dôi lớn nhất : Nmax + Dung sai lắp ghép : TS,N 20 2.2.3.3. Biểu diễn sơ đồ phân bố miền dung sai lắp ghép: - Trục tung: biểu thị giá trị các sai lệch giới hạn, tính bằng micromet 1m (10-3 mm) - Trục hoành (đường 0): biểu thị vị trí KTDN, tại đây các sai lệch giới hạn bằng 0 4/17/2010 6 21 2.2.4. Dung sai lắp ghép các bề mặt trơn: 2.2.4.1. Hệ thống dung sai: - Công thức dung sai: T = a.i i - đơn vị dung sai a - hệ số phụ thuộc vào mức độ chính xác của kích thước. 2.2.4.2. Hệ thống lắp ghép: a. Hệ thống lỗ cơ bản: lỗ cơ bản có sai lệch cơ bản là H với: + Sai lệch dưới EI = 0 + Sai lệch trên ES = + TD b. Hệ thống trục cơ bản: trục cơ bản có sai lệch cơ bản là h với : + Sai lệch trên es = 0 + Sai lệch dưới ei = - Td 22 c. Sai lệch cơ bản: xác định vị trí của miền dung sai so với kích thước danh nghĩa. Có 2 trường hợp: + SLCB là sai lệch dưới (ei, EI) + SLCB là sai lệch trên (es, ES) Đối với lỗ : sai lệch cơ bản lần lượt được ký hiệu bằng các mẫu tự viết hoa là A, B, C, CD, E, EF, G, H, J(JS), K, M, N, P, R, T, U, V, X, Y ,Z, ZA, ZB, ZC. Đối với trục : sai lệch cơ bản lần lượt được ký hiệu bằng các mẫu tự viết thường là a, b, c, cd, d, e, ef, f, g, h, j(js), k, m, n, p, r, s, t, u, v, y, z, za, zb, zc. 23 d. Ký hiệu qui ước của kích thước và lắp ghép: - Ký hiệu của kích thước: KTDN + chữ cái sai lệch cơ bản + cấp chính xác - Ký hiệu lắp ghép: KTDN của mối ghép + ký hiệu miền dung sai của lỗ + ký hiệu miền dung sai trục 24 e. Lắp ghép tiêu chuẩn: 3 nhóm + Nhóm lắp lỏng gồm các kiểu lắp: , a H , h A ,... h H , h B + Nhóm lắp trung gian gồm các kiểu lắp: , sj H , m H , k H , h J S , h M , h K , n H h N ,... b H + Nhóm lắp chặt gồm các kiểu lắp: , p H zc H , h P h ZC ,... h R ,... r H 4/17/2010 7 25 2.2.5. Dung sai hình dạng, dung sai vị trí và nhám bề mặt: 2.2.5.1. Sai lệch, dung sai hình dạng của các bề mặt: a. Sai lệch hình dạng: được tính bằng khoảng cách lớn nhất từ các điểm của profin thực tới profin áp theo phương vuông góc với bề mặt áp. Ký hiệu: - Bao gồm: Sai lệch độ troøn, profin mặt cắt dọc, đñộ trụ, độ phẳng, b. Dung sai hình dạng: giá trị cho phép lớn nhất của sai lệch hình dạng. Ký hiệu: T 2.2.5.2. Sai lệch, dung sai vị trí của các bề mặt: a. Sai lệch vị trí: là sai lệch giữa vị trí thực của các bề mặt, các đường trục hoặc các mặt phẳng đối xứng với chuẩn. Kí hiệu: - Bao gồm: Sai lệch độ song song, vuoâng goùc, ñoàng taâm, b. Dung sai vị trí: giá trị cho phép lớn nhất của sai lệch vị trí. Kí hieäu T 26 2.2.5.3. Cách ghi dung sai hình dạng và dung sai vị trí: + Ô thứ nhất : ghi dấu hiệu tượng trưng + Ô thứ hai: ghi trị số dung sai tính bằng mm. + Ô thứ ba: ghi chữ cái ký hiệu chuẩn 27 3.1. Chỉ tiêu kinh tế kỹ thuật CHÖÔNG 3: NAÊNG SUAÁT LAO ÑOÄNG VAØ GIAÙ THAØNH SAÛN PHAÅM 3.2. Giá thành sản phẩm 3.3. Biện pháp tăng năng suất lao động, giảm giá thành sản phẩm 28 3.1. Chỉ tiêu kinh tế kỹ thuật : Tht = Tcbkt + Ttc . n + Tht: thời gian hoàn thành cả loạt sản phẩm + Tcbkt: thời gian chuẩn bị kết thúc cho mỗi loạt + n: số chi tiết gia công (chiếc, cái) + Ttc: thời gian gia công từng chiếc cho mỗi nguyên công Ttc = T0 + Tp + Tpv + Tk Với: T0: thời gian cơ bản Tp: thời gian phụ Tpv: thời gian phục vụ Tk: thời gian nghỉ ngơi và làm những việc sinh lý tự nhiên 3.1.1. Chỉ tiêu về thời gian T: 4/17/2010 8 29 + Ttc: thời gian tạo ra một đơn vị sản phẩm 3.1.2. Chỉ tiêu về năng suất N: tcT N 1 3.2. Giá thành sản phẩm: - Giá thành sản phẩm là năng suất lao động của xã hội, là tất cả các chi phí bằng tiền trong một đơn vị sản phẩm - Giá thành bao gồm tiền vật liệu, tiền công nhân, tiền khấu hao công cụ lao động, thuế, nhà cửa, 30 3.3. Biện pháp tăng năng suất lao động, giảm giá thành sản phẩm: 3.3.1. i gian chuẩn bị kết thúc cho mỗi loạt Tcbkt: 3.3.2. i gian cơ bản T0: 3.3.3. i gian phụ Tp: 3.3.4. i gian phục vụ Tpv: 3.3.5. i gian nghỉ ngơi và nhu cầu sinh Tk: 31 4.1. Một số chi tiết máy điển hình: CHƢƠNG 4: CHI TiẾT MÁY VÀ CƠ CẤU MÁY ĐiỂN HÌNH 4.2. Một số mối ghép điển hình: 4.3. Các hình thức truyền động: 4.4. Các cơ cấu truyền động: 32 4.1. Một số chi tiết máy điển hình: - Là chi tiết máy dùng để đỡ các chi tiết máy quay, truyền động, - Gồm: Trục tâm, trục truyền, trục truyền chung, trục thẳng, trục bậc, 4.1.1. Trục: - Dùng để đỡ các trục quay, truyền tải trọng từ trục đến giá đỡ. - Gồm: ổ đỡ, đỡ chặn, chặn, ổ bi, đũa, kim, 4.1.2. Ổ lăn: 4/17/2010 9 33 - Là một loại ổ trục, dùng để đỡ các trục quay nhằm mục đích giảm ma sát. - Gồm: ổ đỡ, chặn, đỡ chặn, một nữa, hai nữa, 4.1.3. Ổ trƣợt: 34 4.2. Một số mối ghép điển hình: - Là mối ghép được liên kết bởi đinh tán, thường dùng trong các mối ghép chịu tải trọng rung, va đập: đường ray, cầu sắt, 4.2.1. Mối ghép đinh tán: - Có 2 phương pháp: tán nóng và tán nguội 35 4.2.2. Mối ghép ren: Mối ghép bulong – đai ốc - Là mối ghép được liên kết bởi bulong – đai ốc hoặc vít, vít cấy. Thường dùng cho mối ghép tháo lắp nhiều lần - Mối ghép dễ bị tháo lỏng khi chịu tải rung động 36 4.2.3. Mối ghép then và then hoa: - Dùng để cố định các chi tiết máy trên trục theo phương tiếp tuyến, truyền tải trọng từ trục đến chi tiết máy lắp trên trục và ngược lại. - Ví dụ: ghép bánh răng với trục, a. Mối ghép then: - Bao gồm: mối ghép then bằng, then bán nguyệt, then vát Mối ghép then bán nguyệt 4/17/2010 10 37 - Mối ghép then hoa được xem như mối ghép then bằng gồm nhiều then làm liền với trục. Dùng với tải trọng lớn, yêu cầu độ đồng tâm cao hoặc cần di trượt bạc dọc b. Mối ghép then hoa: Mối ghép then hoa 38 4.3. Các hình thức truyền động: - Dùng để truyền chuyển động giữa hai trục song song và xa nhau, làm việc dựa trên lực ma sát giữa dây đai và bánh đai nên có hiện tượng trượt đai 4.3.1. Bộ truyền đai : 1 2 2 1 )1( n n D D i - Tỷ số truyền động: 39 - Dùng để truyền chuyển động giữa hai trục song song hoặc cắt nhau - Gồm: Bộ truyền bánh răng trụ, răng nghiêng, bánh răng côn, 4.3.2. Bộ truyền bánh răng: - Tỷ số truyền động: 1 2 2 1 n n Z Z i Bộ truyền bánh răng trụ 40 - Dùng để truyền chuyển động giữa hai trục vuông góc với nhau trong không gian 4.3.3. Bộ truyền trục vít – bánh vít: Bộ truyền bánh răng trụ - Tỷ số truyền động: 1 2 n n Z K i 4/17/2010 11 41 - Dùng để truyền chuyển động giữa hai trục song song với nhau và cách xa nhau hoặc truyền chuyển động từ một trục dẫn đến nhiều trục bị dẫn 4.3.4. Bộ truyền xích: - Tỷ số truyền động: 1 2 2 1 n n Z Z i 42 - Dùng biến đổi chuyển động quay thành chuyển động tịnh tiến 4.3.4. Bộ truyền vít – đai ốc: - Độ dịch chuyển của đai ốc: KtnS .. 43 4.4. Các cơ cấu truyền động: -Truyền động vô cấp cho ta tốc độ bất kỳ giữa 2 tốc độ giới hạn nmax và nmin. - Gồm: bánh đai côn đai dẹt, bán côn ma sát con lăn , 4.4.1. Truyền động vô cấp : 44 - Cho tốc độ nhất định giữa 2 tốc độ giới hạn nmax và nmin. - Gồm: cơ cấu bánh răng di trượt, nooc-tông, ly hợp vấu, 4.4.2. Truyền động phân cấp : Cơ cấu ly hợp vấuCơ cấu bánh răng di trượt 4/17/2010 12 45 - Biến chuyển động quay từ động cơ thành chuyển động tới – lui của dao cắt, thường sử dụng cơ cấu Culit 4.4.3. Truyền động gián đoạn: 46 5.1. Nguyên lý cắt gọt kim loại CHƢƠNG 5: GIA CÔNG CẮT GỌT KIM LoẠI 5.2. Moät soá phöông phaùp gia coâng caét goït kim loaïi 5.3. Caùc phöông phaùp gia coâng ñaëc bieät 47 5.1. Nguyên lý cắt gọt kim loại: - là quá trình con người sử dụng dụng cụ cắt để hớt bỏ lớp kim loại thừa khỏi chi tiết, nhằm đạt được những yêu cầu cho trước về hình dáng, kích thước, vị trí tương quan giữa các bề mặt và chất lượng bề mặt của chi tiết gia công 5.1.1. Phaân loaïi caùc phöông phaùp caét goït kim loaïi: a. Theo nguyeân lyù taïo hình: gia coâng cheùp hình, theo veát, bao hình b. Theo yeâu caàu kyõ thuaät: gia coâng thoâ, baùn tinh, tinh c. Theo maùy gia coâng: gia coâng tieän, phay, baøo, maøi, d. Theo beà maët gia coâng: gia coâng maët phaúng, truï ngoaøi, truï trong, 48 5.1.2. Heä thoáng coâng ngheä trong gia coâng caét goït: - Bao gồm: máy, dao, đồ gá và chi tiết gia công a. Máy: cung cấp năng lượng và các chuyển động cần thiết b. Dao: trực tiếp cắt bỏ lớp lượng dư ra khỏi chi tiết c. Đồ gá: xác định và giữ vị trí tương quan giữa dao và chi tiết d. Chi tiết gia công: là đối tượng của quá trình cắt gọt 5.1.3. Caùc beà maët hình thaønh trong quaù trình gia coâng cắt gọt : 4/17/2010 13 49 5.1.4. Các chuyển động cắt gọt : a. Chuyển động chính (chuyển động cắt): - Là chuyển động tạo hình giữa dụng cụ cắt với bề mặt gia công để tạo ra phoi và tiêu hao năng lượng cắt lớn nhất - VD: chuyển động thẳng (bào, xọc, ) hay chuyển động quay tròn (tiện, khoan, ) b. Chuyển động bước tiến: - Là những chuyển động tiếp tục tạo phoi, gồm chuyển động chạy dao s và chuyển động theo phương chiều sâu cắt t 50 5.1.5. Quá trình tạo phoi: a. Bản chất của quá trình tạo phoi: - Ñoù laø quaù trình bieán daïng tröôït cuûa caùc phaàn töû kim loaïi theo caùc maët tröôït cuûa chuùng. b. Các dạng phoi: - Gồm các dạng: phoi vụn, phoi xếp, phoi dây. 51 5.1.6. Nhiệt cắt: - Nhieät löôïng sinh ra trong quaù trình caét: Q = Q 1 + Q 2 + Q 3 + Q 4 Trong ñoù: Q: nhieät löôïng sinh ra trong quaù trình caét Q 1 : coâng ma saùt trong giöõa caùc phaàn töû vaät lieäu gia coâng Q 2 : coâng ma saùt ngoaøi giöõa phoi vaø maët tröôùc dao. Q 3 : coâng ma saùt giöõa beà maët chi tieát gia coâng vaø maët sau dao. Q 4 : coâng caét ñöùt phoi. - Söï truyeàn nhieät: + Neáu Q=100% thì Qphoi = 75%; Qdao = 20%; Qct = 4%; Qmt = 1% mtctdaophoi QQQQQ 52 5.1.7. Söï moøn dao: a. Moøn maët sau b. Moøn maët tröôùc d, e. Moøn muõi dao - Nguyeân nhaân: dao moøn do nhieät caét, ma saùt giöõa dao vaø phoâi, ma saùt giöõa dao vaø phoi + Dao moøn seõ laøm cho löïc caét taêng leân, rung ñoäng taêng, ñoä nhaùm beà maët taêng leân, nhieät caét taêng, + Coù theå phuïc hoài baèng caùch maøi laïi caùc goùc ñoä cuûa dao theo yeâu caàu gia coâng 4/17/2010 14 53 - Laø thôøi gian laøm vieäc lieân tuïc giöõa 2 laàn maøi dao, kyù hieäu laø T (phuùt). - Phuï thuoäc vaøo nhieàu yeáu toá: vaät lieäu laøm dao, vaät lieäu gia coâng, thoâng soá hình hoïc cuûa dao, cheá ñoä caét, dung dòch trôn nguoäi, . . . - Ñöôïc qui ñònh trong soå tay: thöôøng laø 30, 60, 90 hay 120 phuùt, Tuoåi beàn dao: Bieän phaùp giaûm moøn dao: - Ñeå giaûm moøn dao, caàn phaûi coù caùc bieän phaùp giaûm nhieät, giaûm löïc ma saùt nhö: + Söû duïng dung dòch trôn nguoäi nhö: xuùt, eâmunxi, nöôùc xaø phoøng, + Choïn cheá ñoä caét (s, t, v) hôïp lyù + Choïn vaät lieäu cheá taïo dao hôïp lyù, goùc ñoä dao maøi ñuùng yeâu caàu + Taêng cöôøng ñoä cöùng vöõng cuûa heä thoáng coâng ngheä (maùy, dao, phoâi, ñoà gaù) 54 5.2. Moät soá phöông phaùp gia coâng caét goït kim loaïi: 5.2.1. Phöông phaùp tieän: -Laø phöông phaùp gia coâng thoâng duïng nhaát ñeå taïo maët truï troøn xoay trong vaø ngoaøi, tieän ren, tieän coân, vaït maët ñaàu, caét ñöùt, . . . + Chuyeån ñoäng caét chính laø chuyeån ñoäng quay troøn cuûa chi tieát. + Chuyeån ñoäng chạy dao laø chuyeån ñoäng tònh tieán cuûa baøn xe dao 55 Maâm caëp: duøng ñeå ñònh vò vaø keïp chaët phoâi khi gia coâng - Caùc duïng cuï khi tieän: Muõi choáng taâm: duøng ñeå ñôõ chi tieát coù chieàu daøi lôùn Giaù ñôõ (luy- neùt): giuùp taêng ñoä cöùng vöõng khi gia coâng chi tieát daøi, keùm cöùng vöõng 56 5.2.2. Phöông phaùp phay: - Phay laø phöông phaùp gia coâng kim loaïi phoå bieán, laø moät trong nhöõng phöông phaùp gia coâng ñaït naêng suaát cao + Chuyeån ñoäng caét chính: chuyeån ñoäng quay troøn cuûa dao. + Chuyeån ñoäng chaïy dao: chuyeån ñoäng tònh tieán cuûa chi tieát + Chuyeån ñoäng chieàu saâu caét t: naâng leân haï xuoáng cuûa baøn maùy 4/17/2010 15 57 + Phay thuaän: laø phöông phaùp phay maø chieàu quay cuûa dao cuøng chieàu vôùi höôùng tònh tieán cuûa phoâi taïi ñieåm tieáp xuùc A - Phöông phaùp phay thuaän vaø phay nghòch: + Phay nghòch: laø phöông phaùp phay maø chieàu quay cuûa dao ngöôïc chieàu vôùi höôùng tònh tieán cuûa phoâi taïi ñieåm tieáp xuùc A 58 5.2.3. Phöông phaùp baøo, xoïc: - Laø phöông phaùp gia coâng caét goït phoâi coù beà maët phaúng. Xoïc ñöôïc xem nhö laø baøo ñöùng + Chuyeån ñoäng caét chính: chuyeån ñoäng tònh tieán Ñi – Veà cuûa dao + Chuyeån ñoäng chaïy dao: chuyeån ñoäng tònh tieán cuûa baøn maùy + Chuyeån ñoäng chieàu saâu caét t: baøn maùy naâng leân hoaëc haï xuoáng 59 Ñaëc ñieåm: - Baøo duøng ñeå gia coâng maët phaúng vaø caùc maët ñònh hình coù ñöôøng sinh thaúng. Ñaëc bieät ñoái vôùi nhöõng raõnh daøi vaø heïp - Xoïc coù theå gia coâng caùc maët trong loã lôùn nhö raõnh then treân baùnh raêng. - Baøo vaø xoïc cho naêng suaát thaáp vì: + Soá löôõi caét tham gia caét goït ít. + Toán nhieàu thôøi gian cho haønh trình chaïy khoâng. + Vaän toác caét thaáp . 60 5.2.4. Phöông phaùp khoan, doa: Khoan: - Laø phöông phaùp gia coâng loã thoâng duïng, vôùi ñöôøng kính ≤ 35mm + Chuyeån ñoäng caét chính laø chuyeån ñoäng quay troøn cuûa dao + Chuyeån ñoäng chaïy dao laø chuyeån ñoäng doïc truïc chi tieát cuûa dao 4/17/2010 16 61 Doa: - Laø phöông phaùp gia coâng tinh loã sau khi khoan, söûa sai kích thöôùc. - Khoâng doa ñöôïc loã bít ñaùy - Muõi doa coù nhieàu löôõi caét hôn muõi khoan 62 5.2.5. Phöông phaùp maøi: - Maøi duøng ñeå gia coâng tinh, naâng cao ñoä chính xaùc vaø ñoä boùng + Chuyeån ñoäng caét chính laø chuyeån ñoäng quay troøn cuûa ñaù maøi + Chuyeån ñoäng chaïy dao s: chuyeån ñoäng tònh tieán cuûa chi tieát + Chuyeån ñoäng ñieàu chænh chieàu saâu caét t: cuûa ñaàu mang ñaù 63 Ñaëc ñieåm: - ÔÛ ñaù maøi, caùc löôõi caét khoâng gioáng nhau. - Toác ñoä caét khi maøi raát cao khoaûng 30 m/s. - Ñoä cöùng cuûa haït maøi cao, caét ñöôïc theùp ñaõ toâi, hôïp kim cöùng. - Nhieät ñoä phaùt sinh trong quaù trình maøi raát lôùn. - Trong quaù trình caét, ñaù maøi coù khaû naêng töï maøi saéc moät phaàn. - Vieäc ñieàu chænh quaù trình maøi raát khoù khaên 64 5.3. Caùc phöông phaùp gia coâng ñaëc bieät: 5.3.1. Ñaëc ñieåm: - Gia coâng ñöôïc beà maët phöùc taïp, kích thöôùc nhoû, vaät lieäu coù ñoä cöùng cao. - Khoâng caàn söû duïng duïng cuï gia coâng coù ñoä cöùng cao hôn vaät lieäu gia coâng. - Tieát kieäm ñöôïc nguyeân lieäu, naâng cao heä soá söû duïng vaät lieäu. - Ñaït naêng suaát, chaát löôïng vaø hieäu quaû kinh teá cao trong tröôøng hôïp raát raát khoù hoaëc khoâng theå gia coâng baèng phöông phaùp khaùc - Thieát bò ñaét tieàn, toán keùm 4/17/2010 17 65 - Laø phöông phaùp gia coâng ñieän vaät lyù baèng caùch phoùng ñieän aên moøn vaät lieäu gia coâng khi truyeàn naêng löôïng qua raõnh daãn ñieän 5.3.2. Caùc phöông phaùp gia coâng ñaëc bieät: a. Gia coâng baèng tia löûa ñieän: 66 - Laø quaù trình hoaø tan ñieän cöïc döông trong moâi tröôøng chaát ñieän phaân khi coù doøng ñieän ñi qua b. Gia coâng ñieän hoùa: 67 - Laø quaù trình laø cung caáp dao ñoäng sieâu aâm cho duïng cuï caét hoaëc chi tieát gia coâng, taïo ra söï dòch chuyeån töông ñoái giöõa beà maët gia coâng vaø löôõi caét vôùi toác ñoä lôùn, taàn soá cao, bieân ñoä dòch chuyeån nhoû, . . . c. Gia coâng sieâu aâm: 68 6.1. Toång quan veà cô khí hoùa – töï ñoäng hoùa: CHÖÔNG 6: CÔ KHÍ HOÙA – TÖÏ ÑOÄNG HOÙA TRONG SAÛN XUAÁT CÔ KHÍ 6.1.1. Khaùi nieäm: a. Cô khí hoùa: - Laø söï thay theá söùc löïc cuûa con ngöôøi baèng maùy moùc ñeå thöïc hieän nhanh choùng nhöõng coâng vieäc naëng nhoïc - Ngöôøi coâng nhaân chæ coù vieäc ñieàu chænh maùy hoaëc vaän haønh maø khoâng phaûi duøng söùc ñeå gaù laép vaät, di chuyeån dao, b. Töï ñoäng hoùa: - Laø söï phaùt trieån hoaøn chænh cuûa cô khí hoùa, trong ñoù thieát bò ñieàu khieån töï ñoäng seõ thay theá vieäc ñieàu khieån baèng tay. - Töï ñoäng hoùa cuõng coù theå tieán haønh toaøn boä hoaëc töøng phaàn 4/17/2010 18 69 6.1.2. YÙ nghóa: - Cô khí hoùa vaø töï ñoäng hoùa khoâng chæ coù yù nghóa veà maët kinh teá, kyõ thuaät maø noù coøn coù yù nghóa raát to lôùn veà maët xaõ hoäi. Noù giuùp cho ngöôøi lao ñoäng giaûm bôùt naëng nhoïc, ruùt ngaén thôøi gian gia coâng, giaûm bôùt tai naïn lao ñoäng, caùc yeáu toá ñoäc haïi, yeáu toá nguy hieåm, - Cô khí hoùa vaø töï ñoäng hoùa laø muïc tieâu, phöông höôùng chính veà tieán boä kyõ thuaät cuûa caùc quoác gia treân theá giôùi. 70 6.2. Nguyeân taéc öùng duïng cô khí hoùa – töï ñoäng hoùa: Muoán öùng duïng cô khí hoùa – töï ñoäng hoùa caàn phaûi ñaùp öùng caùc nhu caàu cô baûn sau: + Coâng suaát lôùn + Toác ñoä cao + Phöông tieän, ñieàu kieän hieän ñaïi, moät ngöôøi coù theå ñieàu khieån nhieàu maùy ñoàng thôøi. + Giaûm thôøi gian lao ñoäng, taêng naêng suaát, giaûm giaù thaønh vaø hieäu quaû kinh teá ñaït cao nhaát 6.3. Cô khí hoùa trong saûn xuaát cô khí: - Trong saûn xuaát cô khí, caùc coâng vieäc caàn thieát phaûi ñöôïc cô khí hoùa thöôøng laø caùc coâng vieäc naëng nhoïc nhö: vaän chuyeån phoâi, laép ñaët maùy, laép raùp caùc chi tieát maùy lôùn, gaù ñaët phoâi, Caùc phöông tieän caàn ñöôïc trang bò laø: caàu truïc, palaêng, xe ruøa, xe naâng, baêng taûi, 71 6.4. Töï ñoäng hoùa trong saûn xuaát cô khí: 6.4.1. Ñieàu khieån thuï ñoäng (passive control): - Laø daïng ñieàu khieån döïa treân moät chöông trình ñaõ ñöôïc ñònh saün tröôùc ñoù nhöng coâng vieäc ñieàu chænh thoâng soá raát haïn cheá. Ví duï: ñieàu khieån baèng cam, baèng bìa ñuïc loã, 6.4.2. Ñieàu khieån chuû ñoäng (active control): - Laø daïng ñieàu khieån döïa treân moät chöông trình ñaõ ñöôïc ñònh saün tröôùc ñoù nhöng coù khaû naêng kieåm soaùt thoâng soá cuûa quaù trình vaø ñieàu chænh döõ lieäu ñaàu vaøo. Ví duï: ñieàu khieån kyõ thuaät soá CNC, 72 6.5. ÖÙng duïng kyõ thuaät CAD – CAM – CNC trong saûn xuaát cô khí: 6.5.1. CAD (Computer Aided Design): thieát keá nhôø söï trôï giuùp cuûa maùy tính - Söû duïng phaàn meàm nhö: Auto Cad, Pro E, Solid Work, Mechanical Desktop, - Raát tieän lôïi khi chænh söõa hay thay ñoåi thoâng soá. 6.5.2. CAM (Computer Aided Manufacturing): gia coâng nhôø söï trôï giuùp cuûa maùy tính - Caùc phaàn meàm CAM chuyeân duøng nhö: Master Cam, - Tieát kieäm chi phí vaø traùnh tình traïng gia coâng chi tieát bò pheá phaåm do chöông trình sai. 6.5.3. CNC (Computer Numerical Control): ñieàu khieån kyõ thuaät soá - CNC giuùp giaûm thôøi gian phuï, thay dao töï ñoäng, hieäu chænh sai soá deã daøng, ñaëc bieät gia coâng CNC raát an toaøn cho ngöôøi lao ñoäng. 4/17/2010 19 73 CHÖÔNG 7: VAÄT LIEÄU DUØNG TRONG CÔ KHÍ 7.1. Caùc tính chaát cô baûn: 7.2. Theùp 7.3. Gang: 74 7.1 Caùc tính chaát cô baûn: - Laø nhöõng ñaëc tröng cô hoïc bieåu thò khaû naêng cuûa kim loaïi hay hôïp kim chòu ñöôïc taùc ñoäng cuûa caùc loaïi taûi troïng. 7.1.1. Cô tính: - Laø tính chaát cuûa kim loaïi theå hieän qua caùc hieän töôïng vaät lyù khi thaønh phaàn hoùa hoïc khoâng thay ñoåi. 7.1.2. Lyù tính: - Laø ñoä beàn cuûa kim loaïi ñoái vôùi nhöõng taùc duïng hoùa hoïc cuûa caùc chaát khaùc nhau nhö O 2 , H 2 O, axit, .. maø khoâng bò phaù huûy. 7.1.3. Hoùa tính: - Laø tính chòu ñöôïc caùc daïng gia coâng khaùc nhau nhö: ñuùc, reøn, 7.14. Tính coâng ngheä: 75 7.2.1. Thép cacbon: 7.2. Thép: Là hợp chất của Fe-C (%C<2.14%; Mn 0.8%; Si 0.4%; P 0.05%, S 0.05%) Ký hiệu thép: + Thép chất lượng thường: CT31, CT33 + Thép chất lượng tốt: C40, C45, + Thép cacbon dụng cụ: CD80, CD50, . 76 7.2.2. Thép hợp kim: Là thép ngoài sắt và cacbon người ta còn đưa thêm vào các nguyên tố hợp kim để tăng tính chất của thép theo ý muốn. - Giới hạn lượng chứa để phân biệt tạp chất và nguyên tố hợp kim: Mn: 0.8-1.0%; Si: 0.5-0.8%; Cr: 0.2-0.8%; Ni: 0.2-0.6%; W: 0.1-0.5%; Mo: 0.05-02%; Ti: 0.1%; Cu: 0.1%; B: 0.002% Ký hiệu thép: + TCVN 1759-75 quy định mác thép như sau: 9Mn2, 12Cr18Ni9TiĐ, 4/17/2010 20 77 7.3. GANG: - Là hợp chất của sắt và cacbon (%C>2.14%) và một ít các nguyên tố Mn, Si, P, S. - Các loại gang thông dụng thường chứa: 2.04.0%C, 0.43.5%Si, 0.201.5%Mn, 0.040.65%P, 0.020.15%S. Gang xám: - Được ký hiệu bằng chữ GX. Ví dụ: GX15-32 có giới hạn bền kéo nhỏ nhất là 150 Mpa và giới hạn bền uốn nhỏ nhất là 320MPa Gang cầu: - Được ký hiệu bằng chữ GC. Ví dụ: GC42-12 có giới hạn bền kéo nhỏ nhất là 420 MPa và độ dãn dài tương đối 12%
File đính kèm:
bai_giang_co_khi_dai_cuong_pham_tai_thang.pdf