Bài giảng Chế biến lâm sản - Phạm Thị Thủy
Bài mở đầu: (1 tiết)
Mục đích: Học xong sinh viên có thể biết được tầm quan trọng của gỗ đối với nền kinh tế quốc dân, đặc điểm của gỗ, ưu nhược điểm của gỗ cũng như biện pháp khắc phục.
Yêu cầu: Sinh viên có tài liệu, nghe giảng và ghi chép bài đầy đủ, có thái độ học tập cao.
1. Vị trí của gỗ trong nền kinh tế quốc dân
2. Đặc điểm của gỗ và các phương pháp khắc phục các nhược điểm
3. Tình hình cung cấp và sử dụng gỗ ở Việt Nam
Chương I: Bảo quản gỗ (7 tiết)
Mục đích: Học xong sinh viên có thể biết được thuốc bảo quản về công dụng cũng như cách sử dụng, đối tượng, các phương pháp bảo quản
Yêu cầu: Sinh viên có tài liệu, nghe giảng và ghi chép bài đầy đủ
Bạn đang xem 20 trang mẫu của tài liệu "Bài giảng Chế biến lâm sản - Phạm Thị Thủy", để tải tài liệu gốc về máy hãy click vào nút Download ở trên
Tóm tắt nội dung tài liệu: Bài giảng Chế biến lâm sản - Phạm Thị Thủy
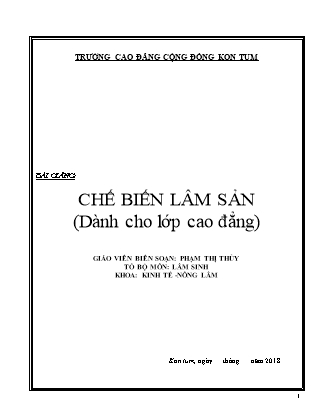
TRƯỜNG CAO ĐẲNG CỘNG ĐỒNG KON TUM BÀI GIẢNG: CHẾ BIẾN LÂM SẢN (Dành cho lớp cao đẳng) GIÁO VIÊN BIÊN SOẠN: PHẠM THỊ THỦY TỔ BỘ MÔN: LÂM SINH KHOA: KINH TẾ -NÔNG LÂM Kon tum, ngày tháng năm 2018 UBND TỈNH KON TUM CỘNG HÒA XÃ HỘI CHỦ NGHĨA VIỆT NAM TRƯỜNG CĐ CỘNG ĐỒNG Độc lập- Tự do- Hạnh phúc CHƯƠNG TRÌNH TRÌNH ĐỘ CAO ĐẲNG NGÀNH ĐÀO TẠO: LÂM SINH ĐỀ CƯƠNG CHI TIẾT HỌC PHẦN 1. Tên học phần: Chế biến lâm sản 2. Số đơn vị học phần: 02 3. Trình độ: Dành cho sinh viên năm thứ 03 (học kỳ 1) 4. Phân bổ thời gian: Lên lớp 30 tiết 5. Điều kiện tiên quyết: - Sinh viên phải nắm vững môn: Sinh lý thực vật, Thực vật học, Cơ giới lâm nghiệp, khai thác lâm sản. 6. Mục tiêu của môn học: Học xong môn học này sinh viên có thể: + Kiến thức: Nhằm trang bị những kiến thức cần thiết về cấu tạo, tính chất, phân loại, bảo quản gỗ và lâm sản, cấu tạo sử dụng các công cụ và máy móc thiết bị, quy trình công nghệ trong sơ chế và chế biến lâm sản. + Kỹ năng: Học xong sinh viên có thể tự sơ chế và chế biến gỗ bằng các dụng cụ thủ công và máy móc. 7. Mô tả vắn tắt nội dung học phần: Học phần gồm bài mở đầu và 4 chương: Bài mở đầu Chương I: Bảo quản gỗ Chương II: Công nghệ xẻ gỗ Chương III: Công nghệ sản xuất hàng mộc Chương IV: Keo dán gỗ và ván nhân tạo 8. Nhiệm vụ của học sinh: Dự lớp đầy đủ và làm đủ các bài kiểm tra (bài 15 phút và bài 1 tiết) 9. Tài liệu học tập: 1- Giáo trình Lâm sản và công nghệ chế biến lâm sản – Đại học nông lâm huế - 2000. 2- Giáo trình khai thác và vận chuyển lâm sản - Đại học Nông lâm Huế- 2000 3- Giáo trình Khai thác sơ chế lâm sản - Trung cấp lâm sinh Gia Lai-1992 10. Tiêu chuẩn đánh giá học sinh: - Dự lớp đúng số tiết theo quy định 80% số tết tiêu chuẩn - Đạt số điểm theo yêu cầu lấy 30% - Kiểm tra kết thúc môn lấy 70% 11. Thang điểm: Thang điểm 10 (từ 0 đến 10) 12. Nội dung chi tiết học phần: Bài mở đầu: (1 tiết) Mục đích: Học xong sinh viên có thể biết được tầm quan trọng của gỗ đối với nền kinh tế quốc dân, đặc điểm của gỗ, ưu nhược điểm của gỗ cũng như biện pháp khắc phục. Yêu cầu: Sinh viên có tài liệu, nghe giảng và ghi chép bài đầy đủ, có thái độ học tập cao. 1. Vị trí của gỗ trong nền kinh tế quốc dân 2. Đặc điểm của gỗ và các phương pháp khắc phục các nhược điểm 3. Tình hình cung cấp và sử dụng gỗ ở Việt Nam Chương I: Bảo quản gỗ (7 tiết) Mục đích: Học xong sinh viên có thể biết được thuốc bảo quản về công dụng cũng như cách sử dụng, đối tượng, các phương pháp bảo quản Yêu cầu: Sinh viên có tài liệu, nghe giảng và ghi chép bài đầy đủ Bài 1: Thuốc bảo quản I. Yêu cầu chung và cơ chế tác dụng 1. Yêu cầu chung của thuốc bảo quản 2. Cơ chế tác dụng II. Phân loại thuốc và căn cứ chọn thuốc 1. Phân loại 1.1. Phân loại theo hiệu lực bảo quản 1.2. Phân theo nguồn gốc nguyên liệu 2. Căn cứ chọn thuốc III. Một số thuốc bảo quản thông dụng 1. Thuốc dầu 1.1. Creosode 1.2. Clonaptanlin 2. Thuốc muối 2.1. Floruanatri (NaF) 2.2. Sufat đồng và các hỗ hợp của nó 2.3. Clorua kẽm (ZnCl2) 2.4. Pentaclofenol 3. Các loại thuốc khác Bài 2: Các phương pháp bảo quản I. Các phương pháp kỹ thuật 1. Bóc vỏ 2. Hong phơi 3. Ngâm nước, phun nước II. Các biện pháp bảo quản bằng hóa chất 1. Nguyên tắc chung khi bảo quản bằng hóa chất 2. Các phương pháp bảo quản bằng hóa chất 2.1. Phương pháp quýet 2.2. Phương pháp phun 2.3. Phương pháp ngâm thường 2.4. Phương pháp đun nóng, ngâm lạnh 2.5. Phương pháp tẩm áp lực Chương II: Công nghệ xẻ gỗ (7 tiết) Mục đích: Học xong sinh viên có thể biết được quy trình của công nghệ xẻ gỗ, phương pháp xẻ, lưu trình xẻ và thiết bị dùng trong xưởng xẻ.. Yêu cầu: Sinh viên có tài liệu, nghe giảng và ghi chép bài đầy đủ. Bài 1: Nguyên liệu và sản phẩm I. Nguyên liệu 1. Các kích thước đặc trưng của gỗ tròn 1.1. Chiều dài và đường kính 1.2. Thể tích gỗ tròn 2. Cắt khúc gỗ tròn 2.1. Nguyên tắc cắt khúc 2.2. Phương pháp cắt khúc II. Sản phẩm 1. Phân loại sản phẩm 1.1. Căn cứ vào kích thước tiết diện ngang 1.2. Căn cứ vào vị trí tâm gỗ trong tiết diện ngang 1.3. Căn cứ vào phương pháp xẻ 2. Kích thước danh nghĩa, kích thước thực tế, lượng dư sấy khô của gỗ xẻ 2.1. Kích thước danh nghĩa 2.2. Kích thước thực tế 2.3. Lượng dư sấy khô Bài 2: Phương pháp xẻ I. Tỷ lệ lợi dụng và tỷ lệ thành khí 1. Tỷ lệ lợi dụng 2. Tỷ lệ thành khí II. Phương pháp xẻ 1. Phân loại phương pháp xẻ 2. Sơ đồ xẻ và tỷ lệ lớn nhất 3. Phương pháp xẻ gỗ bệnh khuyết tật Bài 3: Lưu trình công nghệ và thiết bị dùng trong xưởng xẻ I. Lưu trình công nghệ xẻ gỗ 1. Khái niệm 2. Các phương án bố trí công nghệ xẻ gỗ II. Phân loại thiết bị trong xưởng xẻ và nguyên tắc lựa chọn 1. Phân loại 2. Nguyên tắc lựa chọn thiết bị III. Tính năng kỹ thuật của một số loại thiét bị chính 1. Cưa vòng 2. Cưa sọc 3. Cưa đĩa Chương III: Công nghệ sản xuất hàng mộc (5 tiết) Mục đích: Học xong sinh viên có thể biết được cách gia công phôi và chi tiết cũng như cách lắp ráp sản phẩm. Yêu cầu: Sinh viên có tài liệu, nghe giảng và ghi chép bài đầy đủ, có thái độ học tập cao. Bài 1: Gia công phôi và chi tiết I. Pha phôi 1. Các phương pháp pha phôi từ gỗ xẻ 2. Công nghệ trên khâu cắt ngắn 3. Công nghệ trên khâu xẻ dọc II. Công nghệ gia công sơ chế 1. Công nghệ trên khâu bào thẩm 2. Công nghệ trên khâu bào thẩm III. Gia công tinh 1. Gia công mộng Bài 2: Lắp ráp và trang sức sản phẩm I. Lắp ráp II. Trang sức sản phẩm 1. Mục đích của trang sức bề mặt 2. Các phương pháp trang sức 3. Qúa trình công nghệ trang súc Chương IV: Keo dán gỗ và ván nhân tạo (10 tiết) Mục đích: Học xong sinh viên có thể biết được về keo dán gỗ, keo tổng hợp cũng như công nghệ sản xuất hàng mộc. Yêu cầu: Sinh viên pho to tài liệu, nghe giảng và ghi chép bài đầy đủ, cần có thái độ học tập cao. Bài 1: Những cơ sở lý thuyết về keo dán gỗ I. Khái niệm về chất kết dính, nhựa hóa học và keo hóa học 1. Chất kết dính 2. Nhựa hóa học 3. Kéo hóa học II. Điều kiện cần có của chất kết dính 1. Độ nhớt 2. Độ axit. Bazơ của chất kết kính III. Nguyên lý dán dính IV. Phân loại keo dán 1. Căn cú vào nguồn gốc hóa học của keo 2. Căn cứ vào sự biến đổi của keo khi đun nống 3. Căn cứ vào tính chịu nước V. Phản ứng hóa học tạo nhựa tổng hợp 1. Phản ứng trùng hợp 2. Phản ứng trùng ngưng VI. Kết cấu phân tử của nhựa tổng hợp 1. Kết cấu mạch thẳng 2. Kết cấu mạch không gian 3. Kết cấu mạch rẽ VII. Các yếu tố ảnh hưởng đến quá trình tạo nhựa 1. Cấu tạo hóa học của nhiên liệu 2. Tỷ lệ phân tử gam 3. Độ PH của môi trường phản ứng 4. Nhiệt độ phản ứng 5. Thời gian phản ứng 6. Tốc độ khuấy Bài 2: Keo tổng hợp I.Keo Phenol- Formaldehyd 1.Đặc tính chung của PF 2. Nguyên liệu dùng cho sản xuất keo PF 2.1. Phenol 2.2. Formaldehyd 2.3. Chất xúc tác 3. Phản ứng tạo nhựa PF 4. Sản xuất keo PF trong công nghiệp 4.1. Yêu cầu của xưởng sản xuất 4.2. Chuẩn bị nguyên liệu 4.3. Quy trình điều chế 4.4. Pha chế keo PF II. Keo ure- F 1. Đặc tính của keo UF 2. Nguyên liệu để sản xuất keo UF 3. Phản ứng tạo nhựa Ure- F 4. Sản xuất nhựa U-F Trong công nghệp Bài 3: Công nghệ sản xuất hàng mộc I.Công dụng và tính chất của dán ván, lưu trình công nghệ sản xuất ván dán 1. Công dụng của dán ván 2. Một số tính chất cơ lý của ván dán 3. Lưu trình công nghệ sản xuất cảu ván dán II. Công đoạn sản xuất ván mỏng 1. Nguyên liệu 2. Bóc vỏ 3. Hấp gỗ 4. Cắt khúc 5. Bóc gỗ 6. Cắt ván mỏng 7. Sấy ván mỏng 8. Phân loại và gia công ván mỏng III. Công đoạn dán ván ép 1. Các yếu tố của chất lượng ván mỏng 2. Tráng keo 3. Xếp ván 4. Ép sơ bộ 5. Ép nhiệt IV. Công đoạn gia công sản phẩm của quá trình ép 1. Rọc cạnh 2. Làm nhẵn 3. Bảo quản ván dán trong kho 4. Sản xuất bao bì Kon tum, ngày..tháng.năm 2018 Giảng viên biên soạn Trưởng khoa/ Bộ môn Hiệu trưởng BÀI MỞ ĐẦU (1t) 1. Vị trí của gỗ trong nền kinh tế quốc dân Gỗ là loại nguyên liệu được mọi người dân ưa chuộng, được sử dụng rộng rãi và lâu đời nhất, là một trong những vật tư chủ yếu của nền kinh tế quốc dân. Gỗ được sử dụng trong công nghiệp, nông nghiệp, giao thông vận tải, xây dựng, khai thác mỏ, giáo dục, quốc phòng... Ví dụ: Muốn sản xuất 1 tấn giấy cần 5-6 m3 gỗ, để làm 1 km dường sắt cần 1800 thanh tà vẹt tương đương với 360 m3, . Ngoài ra gỗ còn được sử dụng làm văn phòng phẩm, nhạc cụ, dụng cụ thể dục thể thao, làm bao bì... Sơ bộ thống kê hiện nay có tới 100 ngành công nghiệp dùng gỗ làm nguyên liệu và sản xuất ra trên một triệu sản phẩm khác nhau. Gỗ có thể thay thế bông vải, tơ tằm, lông cừu: với phương pháp chế biến khoa học 1m3 gỗ có thể sản xuất ra 160 kg tơ nhân tạo, đem may được 300 bộ quần áo tương đương với sản lượng 0,5 ha bông lấy trong 1 năm; hoặc tương đương với số lông lấy được của 25-30 con cừu trong một năm. Với công nghệ thủy phân, từ gỗ có thể chế tạo ra đường, rượu thức ăn gia súc, áo đi mưa, đĩa hát. Công nghệ nhiệt phân gỗ có thể cho ta các sản phẩm khác nhau như: than, axit axetic, axeton. Trong một số công dụng gỗ có thể tốt hơn gang, thép: từ gỗ có thể sản xuất ra ván ép lớp có khối lượng lớn, không co giãn, chịu được lực va đập lớn, chịu mài mòn, được dùng để chế tạo thoi dệt tốt hơn hẳn gang thép; hoặc sử dụng để làm bánh răng, đinh ốc cho các tàu thủy, các dụng cụ trong các xưởng hóa chất. 2. Đặc điểm của gỗ và các phương pháp khắc phục a. Ưu điểm của gỗ - Nhẹ, khối lượng thể tích trung bình từ 0.5 - 0.7 g/cm3 nên rất thuận lợi cho việc vận chuyển nhất là vận chuyển thủy. - So với săt, thép, xi măng và một số vật liệu xây dựng khác, gỗ là một loại vật liệu có hệ số phẩm chất cao (nó là tỷ số giữa cường độ gỗ với khối lượng thể tích của bản thân nó). - Cách điện, cách nhiệt và ngăn âm tốt, nhiệt giãn nở bé. - Dễ ghép nối bằng keo, đinh ốc, mộng. - Có hoa văn đẹp tự nhiên, dễ sơn, dễ nhuộm màu và đánh vecni. - Dễ phân ly bằng hóa chất. - Là nguồn tài nguyên có trong thiên nhiên và có thể tái tạo được, có thể trồng, chăm sóc và chế biến bằng các thiết bị đơn giản. b. Nhược điểm - Sinh trưởng chậm, đường kính có hạn, có nhiều khuyết tật tự nhiên. - So với kim loại gỗ là vật liệu mềm, đàn hồi kém. - Trong quá trình phơi sấy thường nứt nẻ, cong vênh, biến hình thay đổi cường độ. - Tính chất biến động tùy thuộc vào điều kiện sinh trưởng, vào vị trí gỗ trong thân cây; ngoài ra còn phụ thuộc vào điều kiện sử dụng, vào chiều thớ, loại gỗ... c. Biện pháp khắc phục Gỗ tuy có nhiều nhược điểm nhưng với trình độ khoa học hiện nay, có thể khắc phục những hạn chế bằng các biện pháp kỹ thuật sau: + Áp dụng các biện pháp kỹ thuật lâm sinh có thể giảm bớt các khuyết tật tự nhiên, tăng tốc độ sinh trưởng. + Bảo quản gỗ bằng các biện pháp kỹ thuật và hóa chất có thể phòng trừ sâu nấm phá hoại gỗ, kéo dài thời gian sử dụng. + Tẩm thước phòng chống cháy để khó khó cháy hay cháy chậm. + Sấy gỗ bằng các phương pháp hiện đại làm cho gỗ khô nhanh, ít cong vênh, nứt nẻ. + Với kỹ thuật dán ép có thể khắc phục được tính chất bất đẳng hướng của gỗ theo chiều thớ. 3. Tình hình cung cấp và sử dụng gỗ ở Việt Nam. a. Tỷ lệ lợi dụng gỗ Tỷ lệ lợi dụng gỗ khâu khai thác khoảng 30-35% Tỷ lệ thành khí khâu cưa xẻ đạt trung bình 60% Tỷ lệ lợi dụng chung 18-21% b. Mức độ tiêu thụ gỗ Nước Anh: 0,43m3/người/năm Nước Pháp: 0,59m3/người/năm Nước Thụy Điển: 3,16m3/người/năm Bình quân thế giới: 0,57m3/người/năm Nước ta mặc dù thiên nhiên ưu đãi có nguồn tài nguyên phong phú và đa dạng nhưng do vấn đề về quản lý sử dụng, hiện tại mức tiêu thụ gỗ bình quân 0,5m3/người/năm vẫn là con số phải phấn đấu lâu dài mới đạt được. Hiện tại Việt Nam phải nhập gỗ sơ chế từ các nước Châu Âu và Châu Mỹ. Trong năm 2015, Việt Nam xuất khẩu chủ yếu qua Trung quốc, Mỹ và Nhật Bản và Thị trường nhập khẩu chủ yếu là Lào, Malaisya, Trung Quốc, Đức.. CHƯƠNG I: BẢO QUẢN GỖ (7t) Mục đích: + Kiến thức: Học xong học sinh có thể nắm bắt được những kiến thức về thuốc bảo quản. + Kỹ năng: Học sinh có thể tự pha thuốc và sử dụng thuốc bảo quản. + Thái độ: Học sinh sẽ sử dụng gỗ tiết kiệm hơn, yêu nghề hơn. Yêu cầu: Học sinh có tài liệu, đi học đầy đủ và ghi chép bài. Bài 1: Thuốc bảo quản I. Yêu cầu chung và cơ chế tác dụng 1. Yêu cầu chung của thuốc bảo quản Có độ đốc cao đối với sinh vật hại gỗ. Không hoặc ít độc đối với người và gia súc. Không gây ô nhiễm môi trường. Dễ thấm vào gỗ và lâm sản, dễ sử dụng. Có tính ổn định trong gỗ, không ăn mòn kim loại. Không làm giảm tính chất cơ học của gỗ. Không làm tăng khẳ năng cháy của gỗ. Không ảnh hưởng đến trang sức bề mặt và giá trị thẩm mỹ của gỗ. Rẻ, sẵn có. 2. Cơ chế tác dụng Đối với côn trùng và hà: Thuốc có thể tiêu diệt côn trùng và hà bằng cách làm tê liệt hệ thống thần kinh hoặc phá hủy men tiêu hóa hay tiêu diệt các vi khuẩn có tác dụng tiêu hóa thức ăn của côn trùng và hà. Đối với nấm: Thuốc có thể phá hủy các bào tử nấm hoặc làm mất khẳ năng trao đổi chất của tế bào nấm hoặc ức chế sự phân chia tế bào. II. Phân loại thuốc và căn cứ chọn thuốc 1. Phân loại a. Phân theo hiệu lực bảo quản Thuốc chỉ có tác dụng với côn trùng, không có tác dụng với nấm mục. Thuốc có khẳ năng phòng trừ nấm nhưng ít hoặc không có tác dụng với côn trùng như: NaF, ZnCl2, FN.... b. Phân theo nguồn gốc nguyên liệu Thuốc có nguồn gốc từ các chất hữu cơ: Creosode, Pentaclofenol... Thuốc có nguồn gốc từ các chất vô cơ: Nà, ZnCl2, CuSO4... 2. Căn cứ chọn thuốc Đối tượng sinh vật hại chủ yếu Điều kiện sử dụng Tính năng tác dụng của thuốc Ví dụ: Bảo quản lâm sản dưới mái che thì đối tượng sinh vật hại chủ yếu là côn trùng. Do điều kiện sử dụng, thuốc bảo quản không cần tính chống rửa trôi nhưng phải không có mùi khó chịu, không bắt lửa, không có màu bẩn, ít độc.... III. Một số loại thuốc bảo quản gỗ chủ yếu 1. Thuốc dầu Là những loại thuốc chỉ tan trong dầu hoặc các dung môi hữu cơ, rất ít tan trong nước, thích hợp cho việc bảo quản ngoài trời. a. Creosode Là loại thuốc dầu được sử dụng rộng rãi trong bảo quản gỗ. Có tỷ trọng: 1,05 -1,12. Đặc tính: Không bị rửa trôi Không ăn mòn kim loại Có màu đen nâu và có màu khó chịu Dễ bắt lửa Có hiệu lực với cả nấm và côn trùng. Sau khi tẩm, gỗ bị biến màu và không trang sức bề mặt được. Công dụng: Thường dùng để tẩm gỗ ngoài trời, gỗ tiếp xúc với đất. Có thể tẩm bằng nhiều phương pháp: quyét, ngâm, tẩm... Độ ẩm khi tẩm phải dưới điểm bão hòa. Creosode được dùng ở dạng nguyên không pha chế. Với liều lượng trung bình: 60kg/m3. Gần đây hiệu lực của thuốc đã giảm nên khi người ta dùng thường trộn thêm thuốc khác vào. b. Clonaptalin Thường dùng là Xylamon, loại này có hiệu lực tốt với mối mọt, có mùi hôi khó chịu, không dùng tẩm gỗ sinh hoạt. Liều lượng 120g/m2 hoặc 6-12kg/m3. 2. Thuốc muối Là những loại thuốc dễ tan trong nước, có thể tẩm cả gỗ tươi hoặc khô, dễ bị rửa trôi. a. NaF Là loại thuốc muối trung tính có màu trắng, không mùi, ít tan trong nước, ít ăn mòn kim loại, dễ bị rửa trôi. Là loại thuốc không độc đối với người và súc vật. Gỗ sau khi tẩm vẫn gia công bình thường. NaF dễ thấm, có hiệu lực với nấm, ít có hiệu lực với côn trùng. Nó được sử dụng sớm và khá phổ biến để tẩm gỗ làm nhà, làm đồ mộc, ... nh kẹp này chuyển độngt ịnh tiến tiếp xúc vào khúc gỗ. Tâm của khúc gỗ được xác định bởi giao điểm của 2 đường thằng nối từng cặp điểm tiếp xúc đối diện nhau. Phương pháp này có độ chính xác không cao song thường áp dụng cho tất cả các khúc gỗ có tiết diện ngang hình bất kỳ. (a) (b) (c) c. Một số khuyết tật của sản phẩm khi bóc và nguyên nhân. Chiều dài ván mỏng không đều do đường đỉnh thước nén và dao bóc không thẳng. Ván mỏng bị rách nhiều do xử lý nhiệt chưa đủ hoặc do mức độ nén nhỏ, hoặc do gỗ khô. Ván mỏng bị xơ bề mặt do xử lý nhiệt quá lâu hoặc do mức độ nén quá cao, hoặc gỗ bị khô. Ván mỏng có đường lồi lõm do thước nén hoặc dao bóc bị mẻ. 6. Cắt ván mỏng Mục đích của cắt ván mỏng là tạo ra tấm ván mỏng có chiều rộng phù hợp với kích thước của sản phẩm. Hiện nay ở các nước, hầu hết dùng máy cắt ván có lưỡi dao cắt chuyển động tịnh tiến theo phương thẳng đứng. Các dao này đều hoạt động theo nguyên lý tự động hoặc bán tự động. Để chất lượng ván khi cắt tốt, khi lắp dao cắt và dao đáy cần chú ý: + Khe hở giữa dao cắt và dao đáy theo phương ngang phải nhỏ hơn 0,3mm. + Độ lệch và khoảng cách dao cắt và dao đáy theo phương dứng phía trước là 150mm và phía sau là 100mm. 7. Sấy ván mỏng. Mục đích của sấy ván mỏng nhằm giảm độ ẩm ván tới độ ẩm phù hợp với yêu cầu với yêu cầu công nghệ. * Yêu cầu của công nghệ sấy ván mỏng: + Phù hợp với năng suất của của máy ép nhiệt. + Hạn chế tới mức thấp hiện tượng rách ván trong quá trình sấy. * Đặc điểm của quá trình sấy ván mỏng: + Sấy ở nhiệt độ cao, vận tốc sấy lớn. * Phương pháp sấy: có 2 phương pháp + Sấy trực tiếp: cho ván mỏng tiếp xúc trực tiếp với nguồn nhiệt. + Sấy đối lưu: môi trường truyền nhiệt trung gian là không khí, đây là phương pháp thông dụng nhất hiện nay. * Nguồn nhiệt để cấp nhiệt cho môi trường: + Hơi nước quá nhiệt + Hơi đốt + Dòng điện * Nhiệt độ sấy: + Nếu dùng hơi nước quá nhiệt: = 120-1300 + Nếu dùng hơi đốt: = 250-2600 * Độ ẩm ván mỏng cần đạt sau khi sấy: + Nếu sử dụng keo UF: = 10-12% + Nếu sử dụng keo PF: . Nếu không sấy ván sau khi tráng keo:= 6-8% . Nếu có sấy ván sau khi tráng keo: =12-14% * Thời gian sấy: Phụ thuộc vào độ ẩm ban đầu và độ ẩm cuối cùng của ván mỏng, vào chiều dày ván mỏng, nguồn nhiệt sấy, vào loại gỗ, độ ẩm của môi trường sấy.... Khi độ ẩm ban đầu của ván mỏng lớn và độ ẩm cuối cùng nhỏ thì gian sấy dài và ngược lại. Với cùng độ ẩm ban đầu và độ ẩm cuối cùng, ván mỏng có chiều dày càng lớn thì thời gian sấy càng dài. 8. Phân loại và gia công ván mỏng a. Phân loại Ván mỏng sau khi sấy được phân loại theo chất lượng và mục đích sử dụng. Chất lượng ván mỏng khi phân loại được xét trên khía cạnh: loại gỗ, số lượng mắt gỗ trên một đơn vị diện tích ván dán, màu sắc, độ nhẵn bề mặt.... Thông thường ván mỏng được chia làm 2 loại: + Ván áo: chất lượng tốt hơn, dùng làm lớp ngoài cùng của ván dán. + Ván giữa: chất lượng kém hơn, dùng độn bên trong của ván dán. Ở Việt Nam phân chia ván mỏng thành 3 loại: ván mặt, ván ruột, ván đáy. b. Gia công ván mỏng Các tấm ván mỏng bị khuyết tật: mắt gỗ bị rời ra, ván bị rách, không đủ kích thước...được đưa vào gia công trên các thiết bị chuyên dùng hoặc bằng thủ công. * Đục và vá ván Đây là phương pháp dùng để gia công các tấm ván mỏng có các mắt gỗ. Quá trình này được tiến hành bằng cách: cắt bỏ các mắt gỗ và ghép vào đó một tấm ván mỏng khác có cùng chiều dày, cùng màu sắc, cùng loại gỗ. * Ghép ván: Ghép ván nhằm mục đích tận dụng các tấm ván mỏng không đủ kích thước đẻ ghép lại thành các tấm ván mỏng có kích thước phù hợp với kích thước sản phẩm nhằm nâng cao tỷ lệ lợi dụng gỗ. Hiện nay có 3 phương pháp ghép ván: + Phương pháp dùng chỉ keo: thực hiện trên máy ghép, cho năng suất cao, chất lượng mối ghép tốt nhưng thiết bị phức tạp (hình a). + Phương pháp dùng băng keo: có thể sử dụng máy ghép hoặc ghép bằng thủ công. Nhược điểm là khi đưa ván vào máy ép, phải bóc băng keo đi vì chúng ảnh hưởng đến chất lượng ván dán (hình b). + Phương pháp tiếp xúc: được sử dụng rộng rãi ở các nước phát triển. Trước khi đưa ván mỏng vào máy ép người ta đưa lên bề mặt phần ván ghép một lớp keo rồi cho đi qua máy ghép. Hai phần của tấm ván mỏng kết nhau lại nhờ keo dán. Phương pháp này cho năng suất cao, chất lượng tốt nhưng đòi hỏi kỹ thuật ghép cao, thiết bị phức tạp (hình c). Các phương pháp ghép ván mỏng (a) (b) (c) III. Công đoạn dán ép ván dán 1. Các yếu tố ảnh hưởng đến chất lượng sản phẩm a. Ảnh hưởng của chất lượng ván mỏng * Độ nhẵn bề mặt Độ nhẵn bề mặt được đặc trưng bởi chiều cao của các nhấp nhô tế vi trên bề mặt ván dán (Hmax). (Hmax) nhỏ sẽ làm cho màng keo tráng lên bề mặt mỏng nhưng liên tục làm tăng chất lượng mối dán. (Hmax) nhỏ còn tạo sự tiếp xúc tốt trong quá trình ép làm tăng khẳ năng hút dẫn giữa keo và vật dán làm tăng cường độ mối dán. (Hmax) quá lớn làm cho màng keo không liên tục hoặc làm cho màng keo quá dày, làm tăng lực chùng co của màng keo, gây cản trở lực hút tương hỗ giữa gỗ và keo làm giảm chất lượng mối dán. Như vậy: Độ nhẵn bề mặt ván mỏng ảnh hưởng đến sự tráng keo lên bề mặt dán và ảnh hưởng đến sự tiếp xúc trong quá trình ép làm ảnh hưởng đến chất lượng mối dán. Nhưng đến một giới hạn nhất định: (Hmax) quá nhỏ cũng làm cho cường độ mối dán không cao do màng keo tráng khó liên tục. Theo thực nghiệm: Hmax tốt nhất đối với gỗ lá kim: = 300-350mr, gỗ lá rộng = 160-200micromet. * Chênh lệch độ dày ván mỏng: Chênh lệch lớn làm giảm khẳ năng trải đều của keo, làm chất lượng mối dán giảm nhất là phương pháp tiếp xúc. Độ chênh pệch lớn còn làm giảm sự đồng đều của áp suất trong quá trình ép làm giảm chất lượng dán dính. * Nhiệt độ ván mỏng Nhiệt độ ván mỏng ảnh hưởng đến trạng thái keo khi tráng lên bề mặt ván, làm thay đổi độ nhớt keo, ảnh hưởng đến khẳ năng tẩm ướt và trải đều của keo ảnh hưởng đến chất lượng mối dán. Ảnh hưởng xấu khi nhiệt độ ván mỏng cao làm keo bị hút quá nhiều vào gỗ gây hiện tượng màng keo đói trên bề mặt dán làm giảm chất lượng mối dán. * Độ ẩm ván mỏng Nếu độ ẩm ván mỏng lớn làm tăng lượng dung môi của keo, do đó làm tăng thời gian ép và làm giảm năng suát ép. Nếu độ ẩm quá lớn trong quá trình ép nước không kịp thoát ra ngoài. Dưới tác dụng của nhiệt độ cao, lượng nước này sẽ hóa hơi tạo ra một áp suất hơi trong lòng tấm ván gây ra hiện tượng nổ vào cuối quá trình ép làm tấm ván bị nứt bề mặt hoặc không kết dính ở những vùng có áp suất hơi lớn làm giảm giá trị của sản phẩm hoặc phải gia công lại làm giảm chất lượng và tăng giá thành sản phẩm. Với ép nguội: độ ẩm gỗ lớn làm cho độ ẩm sản phẩm lớn buộc phải sấy sản phẩm dẫn đến sự chênh lệch độ ẩm sinh ra nội ứng suất làm cho sản phẩm dễ bị cong vênh. Ngược lại: độ ẩm ván mỏng quá nhỏ làm khẳ năng tẩm ướt của keo lên bề mặt ván không tráng keo làm giảm cường độ mối dán (độ ẩm nhỏ còn làm giảm chất lượng mối dán, tạo ra sự cong vênh). b. Ảnh hưởng của chất lượng và số lượng keo. * Nồng độ dung dịch keo Nồng độ dung dịch keo hay đặc trưng lượng nước đưa vào mối dán, nó ảnh hưởng lớn đến chất lượng mối dán. Nồng độ keo thấp nghĩa là lượng nước đưa vào mối dán nhiều sẽ gây ra tác hại trong trường hợp độ ẩm ván mỏng lớn. Nếu nồng độ keo quá cao sẽ làm giảm khẳ năng tẩm ướt và trải đều của keo lên bề mặt ván, làm cho màng keo không liên tục làm giảm chất lượng mối dán. + Với keo UF dùng cho sản xuất ván dán, nồng độ thích hợp là: 55-60%. + Với keo PF dùng cho sản xuất ván dán, nồng độ thích hợp là: 35-45%. * Độ nhớt keo Đặc trưng cho nội lực của bản thân keo, nó quyết định khẳ năng tẩm ướt và trải đều của keo lên bề mặt ván mỏng, làm ảnh hưởng lớn đến chất lượng mối dán. * Lượng keo tráng Lượng keo tráng ngoài việc ảnh hưởng đến chất lượng mối dán nó còn ảnh hưởng đến giá thành sản phẩm vì chi phí keo chiếm 20% giá thành sản phẩm. Lượng keo tráng quá ít làm cho màng keo không liên tục làm giảm chất lượng mối dán. Nếu lượng keo tráng quá nhiều làm cho màng keo dày, lực chùng co của màng keo lớn làm giảm cường độ mối dán (tăng giá thành, giảm hiệu quả kinh tế). Thực nghiệm cho thấy: Một màng keo mỏng liên tục sẽ cho chất lượng mối dán tốt nhất. c. Ảnh hưởng của chế độ dán ép * Nhiệt độ ép Về nguyên lý có thể dán ép ở nhiệt độ cao hoặc nhiệt độ thường song thực tế cho thấy: Sản phẩm ép ở nhiệt độ cao tốt hơn hẳn ở nhiệt độ thường. Nguyên nhân là khi dán ép ở nhiệt độ cao gỗ được hóa mềm tạo khẳ năng tiếp xúc tốt giữa các tấm ván mỏng làm tăng chất lượng sản phẩm, tăng năng suất ép và tăng hiệu quả kinh tế. Tuy nhiên nếu nhiệt độ dán ép quá cao sẽ làm cho độ nhớt của keo giảm nhanh làm cho màng keo dễ bị gián đoạn làm giảm độ bền mối dán.....Vì vậy cần phải có một nhiệt độ dán ép thích hợp tùy theo loại keo và số lượng lớp ván mỏng, tùy theo phương pháp sản xuất. Với keo PF, ván dán 3 lớp: Ván có sấy sau khi tráng keo: Tép=1500c Ván không sấy sau khi tráng keo: Tép=120-1250c Với keo UF Ván có trên 5 lớp: Tép=110-1200c Ván dán có ít hơn hoặc bằng 5 lớp: Tép=140-1500c * Áp suất dán ép Áp suất ép có tác dụng tạo khẳ năng tiếp xúc tốt giữa keo và tấm ván mỏng không được tráng keo nhằm tăng khẳ năng hình thành mối dán, tăng chất lượng sản phẩm khi ép... Áp suất phụ thuộc vào phương pháp ép: Với ép nguội: Pmax = 80 - 120N/cm2, thời gian ép dài. Với ép nhiệt: Pmax = 200 - 220N/cm2, thời gian ép ngắn, nhiệt độ cao. Trị số áp suất này không nhất thiết phải duy trì trong toàn bộ thời gian ép vì sẽ dẫn đến sự co rút không cần thiết. Thực tế chỉ cần duy trì Pmax khoảng 0,6-0,65 thời gian ép (t2), nghĩa là chỉ cần đủ để liên kết được định hình. Giai đoạn giảm áp có ý nghĩa hết sức quan trọng. Sự toàn vẹn của liên kết có thể bị phá hủy nếu giảm áp đột ngột. Quá trình giảm áp thường được tiến hành một cách từ từ hoặc giảm áp thành 2 giai đoạn như hình vẽ. Pmax T T1 T3 T3 T2 * Thời gian ép Thời gian ép là thời gian đủ để tạo mối dán với cường độ dán dính tốt nhất. Thời gian ép có ý nghĩa quan trọng quyết định năng suất ép và chất lượng sản phẩm. Thời gian ép phụ thuộc vào loại keo và phương pháp ép. Việc xác định chính xác thời gian ép rất khó khăn vì nhiệt độ màng keo thay đổi trong quá trình ép. Vì vậy hiện tại người ta dùng phương phương ép thử, thời gian nào cho cường độ mối dán tốt nhất sẽ được chọn nhưng phương pháp này có nhược điểm là lãng phí. Tuy nhiên hiện nay nó vẫn được sử dụng rộng rãi. 2. Tráng keo Chức năng của khâu tráng keo là đưa lên bề mặt ván mỏng sao cho cho màng keo mỏng, đều và liên tục. Sau đây xin giới thiệu 2 phương pháp: a. Phương pháp tiếp xúc Ưu điểm: Keo được đưa lên đồng thời cả 2 bề mặt tráng nên tiết kiệm được diện tích nhà xưởng. Thiết bị đơn giản, dễ sử dụng và bảo dưỡng. Nhược điểm: Chiều dày màng keo khó ổn định. 5 3 3 2 4 1 Tiêu hao keo lớn: 150-200g/m2 Năng suất thấp Sơ đồ tráng keo bằng phương pháp tiếp xúc 1. Ván mỏng 2. Cặp rulo tráng 3. Cặp rulo điều chỉnh 4. Máng chứa keo 5. Ống dẫn keo b. Phương pháp rót không áp lực Phương pháp này chỉ đưa keo lên được một bề mặt của ván mỏng. Keo được rót nhờ hệ thống rãnh của bộ phận rót kéo dài theo chiều rộng ván. Ván mỏng được đẩy nhờ hệ thống băng tải có vận tốc = 2,5-3,5m/s. Ưu điểm: Năng suất cao Lượng keo mất mát ít. Nhược điểm: Rãnh rót bà bơm keo hay bị tắc. Khó bảo dưỡng. Tốt diện tích nhà xưởng. 3 4 5 1 3 2 Sơ đồ tráng keo bằng phương pháp rót không áp lực 1. Bộ phận rót 2. Ván mỏng 3. Băng tải 4. Phễu hứng keo 5. Bơm keo 3. Xếp ván Mục đích của xếp ván là xếp các tấm ván mỏng đã tráng keo và không tráng keo thành các chồng ván phù hợp với kết cấu sản phẩm. a. Yêu cầu đối với công đoạn xếp ván Xếp đủ số lớp ván mỏng. Đúng quy cách sản phẩm. Các bề mặt ván mỏng tiếp xúc nhau phải có ít nhất một bề mặt được tráng keo. Hạn chế tối đa sự xê dịch của các tấm ván mỏng trước khi ép. Xếp ván phải đảm bảo cho năng suất máy ép, tiết kiệm nhà xưởng và nhân lực. b. Các phương pháp xếp ván Xếp theo vị trí cố định Xếp trên băng chuyền 4. Ép sơ bộ Mục đích của ép sơ bộ là tăng chất lượng sản phẩm và tăng năng suất máy ép nhiệt. Ép sơ bộ có tác dụng tạo ra liên kết tạm thời để tránh sự xê dịch ván mỏng khi đưa vào ép nhiệt. Đồng thời ép sơ bộ còn có tác dụng giảm chiều cao của chồng ván. Chế độ ép sơ bộ Áp suất ép: 100-120N/cm2. Thời gian từ khi tráng keo đến khi ép sơ bộ: 10-15 phút. Thời gian ép sơ bộ: 6-7 phút 5. Ép nhiệt a. Phương pháp ép nhiệt: có 2 phương pháp chủ yếu Phương pháp khô nhiệt: chất lượng ván dán không cao. Phương phương ẩm nhiệt: là phương pháp dán ép dựa vào quá trình ẩm dẫn nhiệt ở giai đoạn đầu của quá trình dán ép. Phương pháp này cho năng suất cao, chất lượng sản phẩm tốt. Tuy nhiên nó đòi hỏi thiết bị phức tạp, khống chế quá trình phức tạp, khó khăn. b. Thiết bị ép Máy ép thủy lực một tầng: Loại này cho năng suất thấp, thường sử dụng cho xưởng quy mô nhỏ. Máy ép liên tục kiểu băng chuyền: Áp lực được tạo ra nhờ hệ thống rulo nén và lực căng của băng chuyền. Loại máy này cho năng suất rất cao nhưng đòi hỏi hệ thống gia nhiệt rất phức tạp và chiếm nhiều diện tích nhà xưởng. Máy ép thủy lực nhiều tầng: Đây là lợi máy đang được sử dụng rộng rãi ở nước ta và trân thế giới. Loại máy này có hệ thống piston nằm phía trên hoặc phía dưới bàn ép. Tuỳ theo kích thước của máy mà có từ 1- 8 xilanh. Những xilanh chính được bố trí đối xứng nằm phân bố lực ép đồng đều trên mọi địa điểm của bàn ép. Đường kính của xilanh chính từ 200mm đến 600mm. Ngoài ra có thể có thêm hệ thống piston phụ có áp lực bé, tốc độ hành trình lớn có thể đóng mở các khoang ép. Đường kính xilanh phụ từ 100- 160mm. Bàn ép là một trong những bộ phận có ảnh hưởng lớn đến chất lượng sản phẩm. Bàn ép thông thường được chế tạo bằng thép các bon hoặc được bọc bề mặt bằng các tấm thép. Chiều dày của bàn ép từ 38- 50mm. Kích thước bề mặt phụ thuộc vào đặc điểm của máy ép. Yêu cầu của bàn ép: Đồng phẳng và đồng đều về nhiệt độ. Độ nhấp nhô bề mặt tối đa là 0.05-0.1mm, chênh lệch về nhiệt độ tại các vị trí trên bàn ép nhở hơn 20c. Thời gian làm nóng mặt bàn ép đến nhiệt độ yêu cầu phải nhở hơn 30 phút. * Chế độ ép: Đã giới thiệu ở phần các nhân tố ảnh hưởng đến chất lượng sản phẩm. c. Khuyết tật và nguyên nhân Những nguyên nhân như sau: Độ ẩm ván mỏng nhỏ, Độ ẩm ván mỏng lớn. Độ nhấp nhô bề mặt ván mỏng lớn. Chiều dày ván mỏng không đều. Sử dụng quá ít hoặc không có chất đóng rắn. Độ nhớt keo thấp, Độ nhớt keo cao. Lượng keo tráng quá ít, quá nhiều. ......................... Khuyết tật sản phẩm: Không tạo thành mối dán. Độ bền mối dán Chiều dày sản phẩm nhỏ IV. Giai đoạn gia công sản phẩm của quá trình ép 1. Rọc cạnh Ván sau khi ép phải để sau 24h mới được rọc cạnh, tạo ra kích thước phù hợp và giátrị thẩm mỹ cao. Thiết bị là cưa đĩa 2 lưỡi hoặc 4 lưỡi. 2. Làm nhẵn Nâng cao độ nhẵn bề mặt nhằm tăng chất lượng và giá trị sản phẩm. 3. Bảo quản ván trong kho Được xếp trên đà kê, kho phải thoáng gió...
File đính kèm:
bai_giang_che_bien_lam_san_pham_thi_thuy.doc